Senior Editor
- FMA
- The Fabricator
- FABTECH
- Canadian Metalworking
Categories
- Additive Manufacturing
- Aluminum Welding
- Arc Welding
- Assembly and Joining
- Automation and Robotics
- Bending and Forming
- Consumables
- Cutting and Weld Prep
- Electric Vehicles
- En Español
- Finishing
- Hydroforming
- Laser Cutting
- Laser Welding
- Machining
- Manufacturing Software
- Materials Handling
- Metals/Materials
- Oxyfuel Cutting
- Plasma Cutting
- Power Tools
- Punching and Other Holemaking
- Roll Forming
- Safety
- Sawing
- Shearing
- Shop Management
- Testing and Measuring
- Tube and Pipe Fabrication
- Tube and Pipe Production
- Waterjet Cutting
Industry Directory
Webcasts
Podcasts
FAB 40
Advertise
Subscribe
Account Login
Search
If a metal fabricator’s machines aren’t running … then what?
An old manufacturing industry dictum may need some updating
- By Tim Heston
- November 28, 2018
”If the machine’s not running, we’re not making money.”
I kept thinking of that time-honored manufacturing dictum during FABTECH, held in Atlanta earlier this month. It seems true enough, but judging by the technologies being introduced, it seems the industry has moved beyond it. With automated part removal, sorting, stacking, robotics, data tracking interpretation (think of jargon like Industry 4.0), and all the rest, it’s not just about keeping machines running anymore; it’s about allocating resources—both people and machines— in just the right way to keep jobs moving, from raw stock to the customer’s door.
To be sure, the machine power race is still going strong, particularly in laser cutting. We’re now seeing fiber laser cutting machines with 9, 10, 12, even 15 kW of cutting power. They can offer a shop unusual cutting capability, for sure, but it’s not just about piercing and cutting incredibly quickly through incredibly thick stock. They also want to cut thin stock at unprecedented speeds.
But shops aren’t looking at those machines as a way to produce more parts per hour. After all, the industry is awash with laser cutting capacity, and most shop’s constraint processes—the ones that govern a fabricator’s true throughput—lies in bending, deburring, welding, or grinding. Instead, thanks to the tight labor market, shops are looking at these machines to replace older, less productive machines.
One or two high-powered fiber lasers can feed more downstream processes than ever before. Similarly, one or two automatic-tool-change press brakes can replace three or more manual press brakes.
A machine needs to be available to run, of course. The more a single machine can produce, the costlier unplanned downtime becomes. This could be from reactive maintenance, unavailable material or labor, or a combination of all three. Regardless, when a huge, productive, automated system grinds to a halt unexpectedly, a lot of people in the shop suddenly have a lot of free time, as delivery delays pile up and angry customer calls commence.
Running a high-powered machine with parts that aren’t needed immediately just burns cash and builds excess inventory, now more expensive than ever thanks to rising material prices. At the same time, a fabricator never wants to starve a constraint process like bending or welding of needed work. If those processes lack material to produce, the fabricator probably isn’t making as much money as it could be making.
When I walk the exhibit halls of every FABTECH, I think back to a conference session at the show I saw almost a decade ago. The late Dick Kallage, industry consultant and former columnist for this magazine, pointed to a PowerPoint slide with a line. One end of the line read “cash out,” signifying money spent for people, material, machines, purchased components, and outside services. On the other end read “cash in,” signifying a customer’s payment for a job.
The idea, he said, is to make this line shorter using available resources. Shortening that line increases available capacity that can be sold. But if a machine churns away at unneeded work, it increases work-in-process, and the time between “cash out” and “cash in” gets longer.
Maybe that dictum needs an update. “If the machine’s not running ,when we need it to run, we’re not making money.”
subscribe now
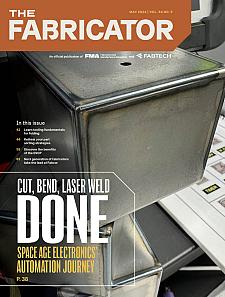
The Fabricator is North America's leading magazine for the metal forming and fabricating industry. The magazine delivers the news, technical articles, and case histories that enable fabricators to do their jobs more efficiently. The Fabricator has served the industry since 1970.
start your free subscriptionAbout the Author
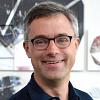
Tim Heston
2135 Point Blvd
Elgin, IL 60123
815-381-1314
Tim Heston, The Fabricator's senior editor, has covered the metal fabrication industry since 1998, starting his career at the American Welding Society's Welding Journal. Since then he has covered the full range of metal fabrication processes, from stamping, bending, and cutting to grinding and polishing. He joined The Fabricator's staff in October 2007.
Related Companies
- Stay connected from anywhere
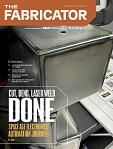
Easily access valuable industry resources now with full access to the digital edition of The Fabricator.
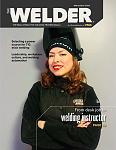
Easily access valuable industry resources now with full access to the digital edition of The Welder.
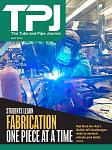
Easily access valuable industry resources now with full access to the digital edition of The Tube and Pipe Journal.
- Podcasting
- Podcast:
- The Fabricator Podcast
- Published:
- 04/16/2024
- Running Time:
- 63:29
In this episode of The Fabricator Podcast, Caleb Chamberlain, co-founder and CEO of OSH Cut, discusses his company’s...
- Trending Articles
Tips for creating sheet metal tubes with perforations
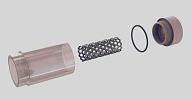
Supporting the metal fabricating industry through FMA
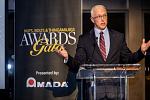
JM Steel triples capacity for solar energy projects at Pennsylvania facility
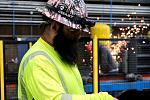
Fabricating favorite childhood memories
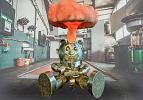
Omco Solar opens second Alabama manufacturing facility
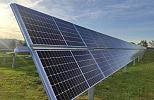
- Industry Events
16th Annual Safety Conference
- April 30 - May 1, 2024
- Elgin,
Pipe and Tube Conference
- May 21 - 22, 2024
- Omaha, NE
World-Class Roll Forming Workshop
- June 5 - 6, 2024
- Louisville, KY
Advanced Laser Application Workshop
- June 25 - 27, 2024
- Novi, MI