Editor-in-Chief
- FMA
- The Fabricator
- FABTECH
- Canadian Metalworking
Categories
- Additive Manufacturing
- Aluminum Welding
- Arc Welding
- Assembly and Joining
- Automation and Robotics
- Bending and Forming
- Consumables
- Cutting and Weld Prep
- Electric Vehicles
- En Español
- Finishing
- Hydroforming
- Laser Cutting
- Laser Welding
- Machining
- Manufacturing Software
- Materials Handling
- Metals/Materials
- Oxyfuel Cutting
- Plasma Cutting
- Power Tools
- Punching and Other Holemaking
- Roll Forming
- Safety
- Sawing
- Shearing
- Shop Management
- Testing and Measuring
- Tube and Pipe Fabrication
- Tube and Pipe Production
- Waterjet Cutting
Industry Directory
Webcasts
Podcasts
FAB 40
Advertise
Subscribe
Account Login
Search
Chipping away at fabricating success
- By Dan Davis
- May 14, 2015
One of the best parts of conferences organized by the Fabricators & Manufacturers Association (FMA) is the ability to view some of the leading fabricating operations in North America. Visitors have the opportunity to observe shop floor organization and workflow and ask pointed questions of their counterparts, who may share similar work-related headaches.
During the FMA Safety Conference in April, attendees had the chance to tour Anderson Dahlen, a contract manufacturer of specialty fabrications in Ramsey, Minn. Stainless steel food manufacturing and processing equipment is the company’s forte, which sometimes results in very large and complex fabrications. (Anderson Dahlen also happens to be the longest-running consecutive winner in the FMA Safety Awards program at nine years.)
The tour took a turn into the company’s machining area, where the visitors witnessed almost 20 separate machining centers either at work or being prepared for another job. In fact, the fabricator has two horizontal boring mills with table capacities of 44,000 lbs. Machining is no small sideline activity for Anderson Dahlen.
Yet the company is still a metal fabricator. As the definition suggests, the fabricator is manufacturing something out of different components. In this case, the company happens to be machining as well.
Anderson Dahlen is not alone in that sense. Other fabricators appear to be following a similar path.
In a readership survey sent to almost 10,000 subscribers of The FABRICATOR in March 2015, the editors asked how many survey recipients had some machining activities on their shop floor. Of the 134 respondents, 78 percent indicated their production operations include machining; two years ago, a similar question in the same survey revealed identical results.
In the same survey, fabricators having machining capabilities were asked about the volume of that work at their shops. Forty-nine percent said that machining has increased over the past 12 months, and 34 percent said that it has stayed the same.
The simple reason for this trend is that fabricators recognize if they can offer more capabilities, they have a better chance of enticing a customer to buy from them—and stay with them. That’s what OEMs and other large manufacturing companies want to see. As they look to reduce the number of vendors in their supply chains, they want to sign off on one purchase order for an entire assembly, rather than issue several POs for multiple parts. Fabricators that can do it all in a quality manner and within a tight timeframe have an advantage over other fabricators that can’t deliver in the same manner.
In the May 2015 supplement to The FABRICATOR, “Industry Research Project: Building a competitive advantage,” 42 percent of survey respondents indicated that they have brought in previously outsourced processes within the past year. Of those that followed that path, 25 percent said they brought machining in-house, which topped the list, slightly ahead of cutting.
A fabricating operation with machining capabilities is no longer atypical. It’s much more of a common occurrence. Fabricators have found that adding a machining center is less of a chore than trying to carve out space for a laser cutting machine with an automated material loader/unloader; two or three machining centers might fit in the laser cell’s footprint. Also, certain types of chipping equipment cost far less than some of the staple capital machine tools found on the fabricating floor.
This is not to say that fabricators are competing against established machine shops. In a majority of cases, this is simply not the case. These fabricators are looking at their machine capabilities as an enticement to earn more work from their current fabricating-based customers.
The metal fabricating industry is evolving to the point where the fab shop of today isn’t going to look like one from 25 years ago. The lighting is likely to be better. Certainly, the haze from welding fumes is lessened or eliminated altogether. And in the corner, near the welding cells and assembly area, operators are working at CNC milling centers and maybe even a turning center. Fabricating is the business, and it’s not relegated just to sheet metal anymore.
subscribe now
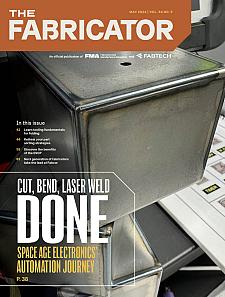
The Fabricator is North America's leading magazine for the metal forming and fabricating industry. The magazine delivers the news, technical articles, and case histories that enable fabricators to do their jobs more efficiently. The Fabricator has served the industry since 1970.
start your free subscriptionAbout the Author
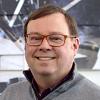
Dan Davis
2135 Point Blvd.
Elgin, IL 60123
815-227-8281
Dan Davis is editor-in-chief of The Fabricator, the industry's most widely circulated metal fabricating magazine, and its sister publications, The Tube & Pipe Journal and The Welder. He has been with the publications since April 2002.
- Stay connected from anywhere
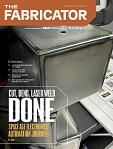
Easily access valuable industry resources now with full access to the digital edition of The Fabricator.
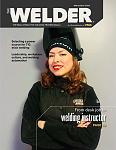
Easily access valuable industry resources now with full access to the digital edition of The Welder.
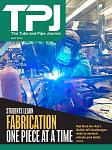
Easily access valuable industry resources now with full access to the digital edition of The Tube and Pipe Journal.
- Podcasting
- Podcast:
- The Fabricator Podcast
- Published:
- 04/16/2024
- Running Time:
- 63:29
In this episode of The Fabricator Podcast, Caleb Chamberlain, co-founder and CEO of OSH Cut, discusses his company’s...
- Trending Articles
Tips for creating sheet metal tubes with perforations
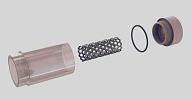
Supporting the metal fabricating industry through FMA
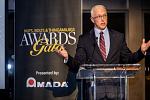
JM Steel triples capacity for solar energy projects at Pennsylvania facility
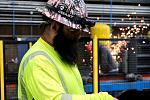
Fabricating favorite childhood memories
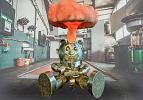
Omco Solar opens second Alabama manufacturing facility
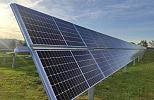
- Industry Events
16th Annual Safety Conference
- April 30 - May 1, 2024
- Elgin,
Pipe and Tube Conference
- May 21 - 22, 2024
- Omaha, NE
World-Class Roll Forming Workshop
- June 5 - 6, 2024
- Louisville, KY
Advanced Laser Application Workshop
- June 25 - 27, 2024
- Novi, MI