- FMA
- The Fabricator
- FABTECH
- Canadian Metalworking
Categories
- Additive Manufacturing
- Aluminum Welding
- Arc Welding
- Assembly and Joining
- Automation and Robotics
- Bending and Forming
- Consumables
- Cutting and Weld Prep
- Electric Vehicles
- En Español
- Finishing
- Hydroforming
- Laser Cutting
- Laser Welding
- Machining
- Manufacturing Software
- Materials Handling
- Metals/Materials
- Oxyfuel Cutting
- Plasma Cutting
- Power Tools
- Punching and Other Holemaking
- Roll Forming
- Safety
- Sawing
- Shearing
- Shop Management
- Testing and Measuring
- Tube and Pipe Fabrication
- Tube and Pipe Production
- Waterjet Cutting
Industry Directory
Webcasts
Podcasts
FAB 40
Advertise
Subscribe
Account Login
Search
Top 5 in 365—Articles about materials handling
- By Vicki Bell
- September 19, 2018
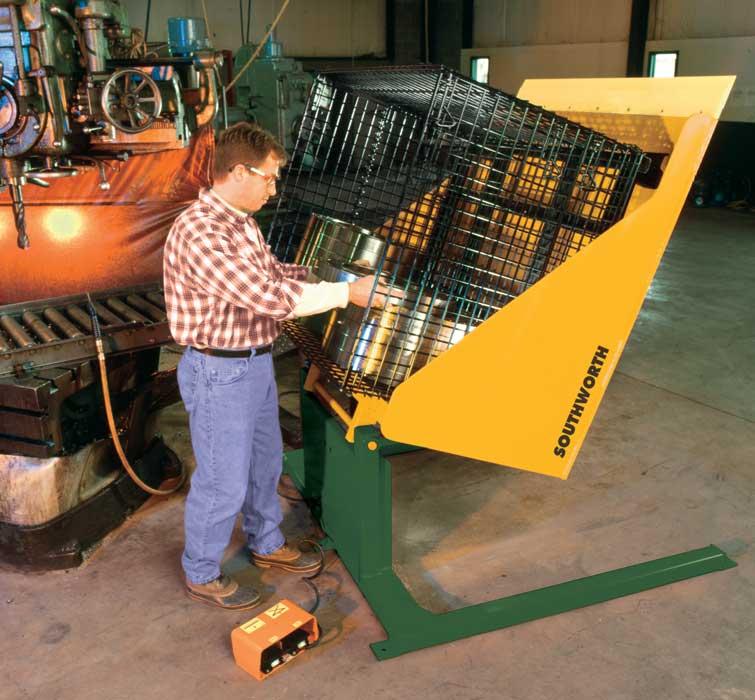
Seconds not spent reaching into a bin are seconds spent moving material, increasing productivity. A tilter can be used to present the container at an optimal height and angle, allowing workers to access items with minimal bending, reaching, and stretching.
The last installment of “Top 5 in 365” showcased the five most-popular articles on thefabricator.com published within the last year about manufacturing software. Previous installments have focused on bending and folding, laser cutting, arc welding, assembly and joining, automation and robotics, consumables, cutting and welding prep, and finishing. This post is about the materials handling category on the website.
The material handling technology area encompasses systems and equipment for handling coil, sheet, plate, profiles, tube and pipe, raw materials, and scrap. It also covers peripheral accessories such as C-hooks, clamps, die storage systems, hoists, lifters, and sheet stackers and destackers.
Here are the top five most-read articles in the past year about manufacturing software.
5. Sawing, storage system specialist Kasto opens Chicago-area facility
Open house provides opportunity to introduce new storage system for tube, pipe, and bar
For modern service centers, running the business successfully requires making in-numerable complex decisions, nearly all of which affect other decisions. Thankfully, some decisions are more straightforward, especially when considering equipment to retrieve material from inventory or equipment to cut it.
It comes down to reducing cost per pick and cost per cut,” said Kasto Inc.’s Vice President Nikolis Wasynczuk, speaking at the company’s grand opening of its new facility, showroom, and demo center in Schaumburg, Ill., near Chicago
4. Gunderson Marine finds a way to keep sheets from falling from cranes
Gunderson Marine, Portland, Ore., has worked to maintain a safe working culture over almost 100 years of manufacturing. It has built more than 2,000 marine vessels over the years and currently has about 800 employees. It also has branched out to railcar manufacturing over the years.
The company and Magswitch Technology, Lafayette, Colo., have collaborated on a new custom lifter system that keeps steel sheets from falling from cranes.
3. Technology Spotlight: The potential of self-driving vehicles in metal fabrication
Oxide coating application proves SDVs’ potential
Self-driving vehicles, combined with robot intelligence, could help drive efficiency on what remains a highly manual process in metal fabrication: moving parts from one process to another.
2. 5 design elements for safe, heavy-duty racking
Poorly designed racking is a safety hazard that shouldn’t be overlookedWhat exactly makes a Ford F-250 cost more than an F-150? From the outside, they look pretty much the same, right? It’s not until you lift the hood and check the undercarriage that you notice what makes the F-250 capable of handling higher payloads. That’s what makes it worth more of your hard-earned cash.
The same idea applies to structural storage racking. When comparing different systems at face value, you see I-beam construction, heavy-duty bolts, and structural bracing. It’s easy to assume they can handle the same weight—especially if the advertised steel sizes and weight capacities are the same.
1. The economics of ergonomic material handling
Ergonomic equipment heads off lost-time injuries, boosts productivity
Good ergonomics is not just a nice thing to do, it is a must-do, based on its economic value. Many claims are for injuries that are the result of accumulated trauma, rather than from a single event, including sprains, strains, tendonitis, and lower back pain. The injuries derive from actions that create excessive or repeated stress on backs, shoulders, elbows, wrists, ankles, and hands. Costs of lost-time injuries vary, but using a conservative average of $25,000 per incident, preventing a single lost-time injury can save more than enough to pay for ergonomic equipment. In addition, ergonomic improvements can eliminate wasted motion – a core lean manufacturing tenet and a precursor to increased productivity.
Next up? Metals and Materials.
subscribe now
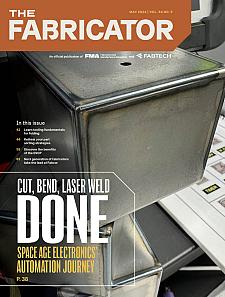
The Fabricator is North America's leading magazine for the metal forming and fabricating industry. The magazine delivers the news, technical articles, and case histories that enable fabricators to do their jobs more efficiently. The Fabricator has served the industry since 1970.
start your free subscriptionAbout the Author
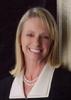
Vicki Bell
2135 Point Blvd
Elgin, IL 60123
815-227-8209
- Stay connected from anywhere
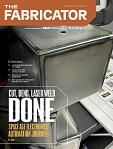
Easily access valuable industry resources now with full access to the digital edition of The Fabricator.
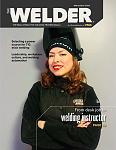
Easily access valuable industry resources now with full access to the digital edition of The Welder.
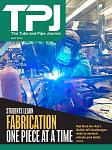
Easily access valuable industry resources now with full access to the digital edition of The Tube and Pipe Journal.
- Podcasting
- Podcast:
- The Fabricator Podcast
- Published:
- 04/30/2024
- Running Time:
- 53:00
Seth Feldman of Iowa-based Wertzbaugher Services joins The Fabricator Podcast to offer his take as a Gen Zer...
- Industry Events
Pipe and Tube Conference
- May 21 - 22, 2024
- Omaha, NE
World-Class Roll Forming Workshop
- June 5 - 6, 2024
- Louisville, KY
Advanced Laser Application Workshop
- June 25 - 27, 2024
- Novi, MI
Precision Press Brake Certificate Course
- July 31 - August 1, 2024
- Elgin,