Contributing Writer
- FMA
- The Fabricator
- FABTECH
- Canadian Metalworking
Categories
- Additive Manufacturing
- Aluminum Welding
- Arc Welding
- Assembly and Joining
- Automation and Robotics
- Bending and Forming
- Consumables
- Cutting and Weld Prep
- Electric Vehicles
- En Español
- Finishing
- Hydroforming
- Laser Cutting
- Laser Welding
- Machining
- Manufacturing Software
- Materials Handling
- Metals/Materials
- Oxyfuel Cutting
- Plasma Cutting
- Power Tools
- Punching and Other Holemaking
- Roll Forming
- Safety
- Sawing
- Shearing
- Shop Management
- Testing and Measuring
- Tube and Pipe Fabrication
- Tube and Pipe Production
- Waterjet Cutting
Industry Directory
Webcasts
Podcasts
FAB 40
Advertise
Subscribe
Account Login
Search
Around DC: Manufacturers won’t have to worry about new emission control rules
Companies applying coatings avoid huge costs associated with new emissions control technology
- By Stephen Barlas
- November 18, 2019
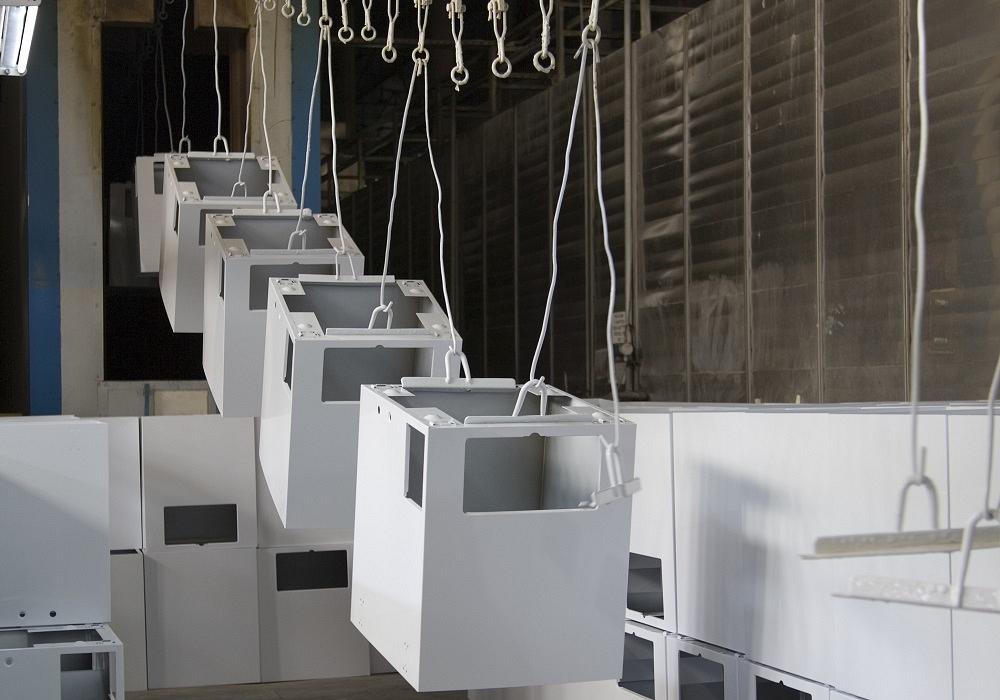
The EPA announced that no new emission controls will be necessary for facilities doing surface coating of miscellaneous metal parts. But the agency is considering a new emissions standard that would come into play when metalworking equipment malfunctions. photo provided
The close to 400 metalworking facilities nationwide subject to the Environmental Protection Agency’s air emission controls for hazardous air pollutants should be breathing a sigh of relief.
The agency announced in the early fall that no new emission controls will be necessary for facilities doing surface coating of miscellaneous metal parts. But the agency is considering a new emissions standard that would come into play when metalworking equipment malfunctions.
Facilities covered by the National Emission Standards for Hazardous Air Pollutants (NESHAP) for fabricators of miscellaneous metal parts and products (MMPP) include job shops and manufacturers of building panels, metal drums, metal pipes, and many more products, even beer kegs. Major sources in that category are broken down into subcategories with differing control requirements: general use, high-performance, magnet wire, rubber-to-metal, and extreme performance fluropolymer coatings. The primary HAPs emitted from MMPP facilities include xylenes, toluene, glycol ethers, ethyl benzene, methyl isobutyl ketone, methanol, ethylene glycol, and dimethyl phthalate. The majority of organic HAP emissions can be attributed to the application, drying, and curing of coatings.
The so-called MMPP NESHAP was established on Jan. 2, 2004. The EPA is required to do a review of NESHAPs periodically to determine whether health and environment risks from a category’s emissions have increased and whether additional controls are available and cost effective. In the review of the category the EPA just completed, it did look at two subcategories: rubber-to-metal bonding and high-performance.
In the former, the agency evaluated the option of reducing the existing source limit to an emission limit of 10 lbs. HAP/gallon solids. Two facilities might have needed to install thermal oxidizers, if alternative low-HAP coatings or other compliance options were not available. The thermal oxidizers would require a total capital investment of $2 million (combined) for the two facilities and total annual costs of $410,000 (combined) to run the untis. Estimated emission reductions from the two facilities would be 43 tons per year of HAP, and the estimated cost effectiveness would $9,500 per ton of HAP reduced. As a result of that analysis, the EPA concluded that the added costs are unreasonable particularly because the risks are already low, and the risks would not be reduced in a meaningful manner by the control of these subcategories.
However, while MMPP emission controls are not being tightened, the EPA is proposing to amend provisions addressing emissions during periods of startup, shutdown, and malfunction; to amend provisions regarding electronic reporting of performance test results; to amend provisions regarding monitoring requirements; and to make miscellaneous clarifying and technical corrections.
Those amendments are not significant in terms of added compliance costs with the MMPP. But the EPA is considering whether it should set new standards for emissions when equipment malfunctions. No such standards exist currently. For example, the EPA established a work practice standard for petroleum refineries for unique types of malfunctions that result in releases from pressure relief devices or emergency flaring events. The EPA is looking into whether it needs to set a malfunction standard for the MMPP sector.
Controversy Over OSHA Changes to Lock Out/Tag Out
Looks like any move by the Occupational Safety and Health Administration (OSHA) to change its lock out/tag out (LO/TO) standard will be controversial. The standard was issued in 1989, and groups such as the Precision Metalforming Association (PMA) want it reformed to comply more closely with an ANSI standard issued in 2016, which allows non-mechanical machine controls on energy distribution when machines are being serviced. The original standard 1989 was based on a much older version of the ANSI standard.
“PMA believes that well-devised alternative methods of energy control using control circuit type devices that are appropriately based on a task-based risk assessment and that meet the requirements for the development and use of alternative methods in ANSI Z244.1-2016 offer significant increases in both safety and productivity for the metal forming industry,” wrote PMA president David Klotz in a letter to the OSHA.
But the AFL-CIO opposes any change to the standard.
“It is important to remember that any claim of saving time and money by switching solely to technological systems puts workers at greater risk of injury and death,” said Rebecca Reindel, AFL-CIO’s safety and health director. “Manual lockout/tagout continues to be the best way to protect workers from hazardous energy sources.”
subscribe now
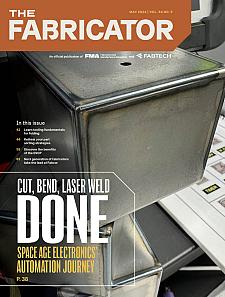
The Fabricator is North America's leading magazine for the metal forming and fabricating industry. The magazine delivers the news, technical articles, and case histories that enable fabricators to do their jobs more efficiently. The Fabricator has served the industry since 1970.
start your free subscriptionAbout the Author
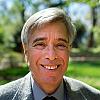
Stephen Barlas
- Stay connected from anywhere
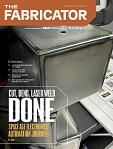
Easily access valuable industry resources now with full access to the digital edition of The Fabricator.
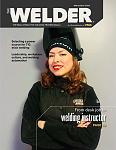
Easily access valuable industry resources now with full access to the digital edition of The Welder.
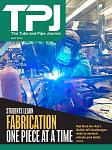
Easily access valuable industry resources now with full access to the digital edition of The Tube and Pipe Journal.
- Podcasting
- Podcast:
- The Fabricator Podcast
- Published:
- 04/16/2024
- Running Time:
- 63:29
In this episode of The Fabricator Podcast, Caleb Chamberlain, co-founder and CEO of OSH Cut, discusses his company’s...
- Trending Articles
Tips for creating sheet metal tubes with perforations
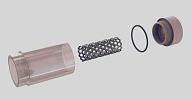
Supporting the metal fabricating industry through FMA
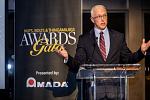
JM Steel triples capacity for solar energy projects at Pennsylvania facility
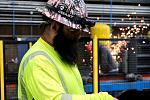
Fabricating favorite childhood memories
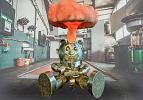
Omco Solar opens second Alabama manufacturing facility
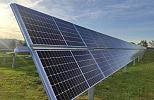
- Industry Events
16th Annual Safety Conference
- April 30 - May 1, 2024
- Elgin,
Pipe and Tube Conference
- May 21 - 22, 2024
- Omaha, NE
World-Class Roll Forming Workshop
- June 5 - 6, 2024
- Louisville, KY
Advanced Laser Application Workshop
- June 25 - 27, 2024
- Novi, MI