Editor-in-Chief
- FMA
- The Fabricator
- FABTECH
- Canadian Metalworking
Categories
- Additive Manufacturing
- Aluminum Welding
- Arc Welding
- Assembly and Joining
- Automation and Robotics
- Bending and Forming
- Consumables
- Cutting and Weld Prep
- Electric Vehicles
- En Español
- Finishing
- Hydroforming
- Laser Cutting
- Laser Welding
- Machining
- Manufacturing Software
- Materials Handling
- Metals/Materials
- Oxyfuel Cutting
- Plasma Cutting
- Power Tools
- Punching and Other Holemaking
- Roll Forming
- Safety
- Sawing
- Shearing
- Shop Management
- Testing and Measuring
- Tube and Pipe Fabrication
- Tube and Pipe Production
- Waterjet Cutting
Industry Directory
Webcasts
Podcasts
FAB 40
Advertise
Subscribe
Account Login
Search
Be aware and be alive
Safety talks can be boring, but they also might save a life
- By Dan Davis
- December 14, 2018
On a chilly day in mid-December, I’m on a 6:30 a.m. flight, and I’m about to fall asleep just after sitting down. The flight attendant starts the safety briefing, and I’m only aware that she has begun. I’m not sure I’m awake by the end of it.
That raises valid questions:
- Do I know where my nearest exit is?
- Where is that floatation device located?
- Do I grab the air mask first and then try to get the air flowing, or does the air need to flow first before I put the mask on?
In theory, my early morning nap has put me and my nearby seatmates in jeopardy if something such as loss in cabin pressure or an emergency landing occurs. In reality, nothing is likely to go wrong, but what if it did?
That’s what safety and shop managers deal with on a regular basis. The routine safety talk eventually runs the risk of falling on deaf ears. Complacency is a real threat to creating a risk-free environment.
Think about it. If a new employee working in front of a press brake has handled sheet metal without gloves for several weeks and experienced no problems, they don’t think they need to change their approach. Gloves aren’t a necessity because no injury has occurred. Until it does, of course.
Greg Anderson, author of Safety 24/7, a book about creating a culture where safety is a core value and where all employees support the effort, not just safety managers, calls this “old-school, bulletproof” thinking.
“The employee has never been hurt in the past, so why should he expect to be hurt in the future?” Anderson said.
In a blog entry on his website, Anderson wrote of his own in-flight safety briefing moment with his then 10-year-old daughter. During the briefing she asked him, “Why does it matter anyway?” She saw what we all notice and, perhaps, contribute to. No one was paying attention. People were chatting, reading newspapers, and even sleeping.
That made him think. What sort of example are these people setting for the younger travelers who probably don’t know the safety briefing by heart?
That exact scenario can happen on a shop floor where more experienced workers half-heartedly pay attention to a safety discussion. New employees can pick up on that and will adopt the same thinking. Sure, attitudes and actions may change if a safety manager is present, but that individual can’t be hovering over every shoulder of every employee during every minute of a shift.
As Anderson wrote in his book and as it’s explained in the article “How to create a culture of safety” in this issue (p. 76), all employees have to make safety a priority if a company wants to create an incident-free workplace. They watch out for each other. Never underestimate the power of peer pressure.
When a company establishes this type of culture, it can be something to behold. I visited an East Coast shop—the reason for the early morning December flight—and saw just what can happen when the shop floor is fully engaged in looking for better and safer ways to do things.
When employees kept getting snagged on an edge of stacked sheet metal protruding from a rack, someone suggested cutting a pool noodle to the correct size and placing it over the sharp edge. Now the pool noodles cover various sharp edges around the floor.
Always on the lookout for a smarter way to move pallets and minimize wasted movements in the shop, someone suggested purchasing a pallet handler that had a scale built into it. Now the pallet handler can be brought to a pallet for weighing, reducing excessive material movement and the increased potential for injury.
“Safety was to be everyone’s responsibility,” Anderson said. “We are in charge of the decisions we are going to make, and those decisions are going to dictate outcomes. We have to choose to work safely, or we can choose to work at risk and put ourselves in danger. That’s the choice.”
In November the Bureau of Labor Statistics (BLS) reported that the incidence rate of total recordable cases in manufacturing decreased in 2017. The median days away from work (DAFW) that resulted from an incident in the manufacturing sector fell to eight, one day fewer than in 2016. Of the four occupation groups that accounted for 67 percent of the DAFW cases in 2017, the BLS stated that “assemblers and fabricators” was the only one with a decrease in cases from 2016 to 2017, from 13,040 to 12,140.
Maybe more people are paying attention when it comes to matters of safety. That’s a good thing. A few minutes of attention potentially can save a lifetime of pain.
subscribe now
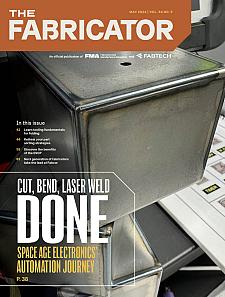
The Fabricator is North America's leading magazine for the metal forming and fabricating industry. The magazine delivers the news, technical articles, and case histories that enable fabricators to do their jobs more efficiently. The Fabricator has served the industry since 1970.
start your free subscriptionAbout the Author
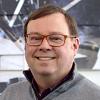
Dan Davis
2135 Point Blvd.
Elgin, IL 60123
815-227-8281
Dan Davis is editor-in-chief of The Fabricator, the industry's most widely circulated metal fabricating magazine, and its sister publications, The Tube & Pipe Journal and The Welder. He has been with the publications since April 2002.
- Stay connected from anywhere
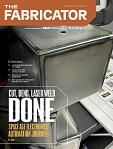
Easily access valuable industry resources now with full access to the digital edition of The Fabricator.
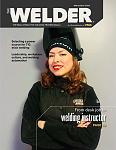
Easily access valuable industry resources now with full access to the digital edition of The Welder.
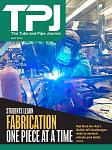
Easily access valuable industry resources now with full access to the digital edition of The Tube and Pipe Journal.
- Podcasting
- Podcast:
- The Fabricator Podcast
- Published:
- 04/30/2024
- Running Time:
- 53:00
Seth Feldman of Iowa-based Wertzbaugher Services joins The Fabricator Podcast to offer his take as a Gen Zer...
- Industry Events
Pipe and Tube Conference
- May 21 - 22, 2024
- Omaha, NE
World-Class Roll Forming Workshop
- June 5 - 6, 2024
- Louisville, KY
Advanced Laser Application Workshop
- June 25 - 27, 2024
- Novi, MI
Precision Press Brake Certificate Course
- July 31 - August 1, 2024
- Elgin,