- FMA
- The Fabricator
- FABTECH
- Canadian Metalworking
Categories
- Additive Manufacturing
- Aluminum Welding
- Arc Welding
- Assembly and Joining
- Automation and Robotics
- Bending and Forming
- Consumables
- Cutting and Weld Prep
- Electric Vehicles
- En Español
- Finishing
- Hydroforming
- Laser Cutting
- Laser Welding
- Machining
- Manufacturing Software
- Materials Handling
- Metals/Materials
- Oxyfuel Cutting
- Plasma Cutting
- Power Tools
- Punching and Other Holemaking
- Roll Forming
- Safety
- Sawing
- Shearing
- Shop Management
- Testing and Measuring
- Tube and Pipe Fabrication
- Tube and Pipe Production
- Waterjet Cutting
Industry Directory
Webcasts
Podcasts
FAB 40
Advertise
Subscribe
Account Login
Search
FABTECH® 2018 recap—Day 2
I can see clearly now
- By Vicki Bell
- November 7, 2018
The skies were clear and the sun was shining as I took a cab from my hotel to the GWCC for the second day of FABTECH 2018. About that cab ride. I was in a hurry to make an 8 a.m. appointment, and the driver got me there in plenty of time. That’s the good news. The bad is news is that since I was his first fare of the day, he had no change for my $20—or so he said. I’ve taken many cabs in my life and have never heard that one before. He got out of the cab, walked around to the passenger side, pulled his wallet out of a jacket riding shotgun, and took out $2, which is all he said he had. The cab ride was $8, and I walked away with $2 in change from my $20. Needless to say, when I got in the cab tonight to head back to the hotel from the convention center, the first thing I said to the driver was, “Please tell me you can make change.”
Always Impressive
That 8 a.m. appointment was a press conference with TRUMPF Inc. (B6309). Always impressive, this year’s exhibit comprised three separate booths featuring 13 machines and 30,000kW of power. In his opening remarks, Burke Doar, vice president, sales and marketing, spoke about the company’s goal of “helping customers get closer and closer to completely autonomous sheet metal working.”
The first machine on our booth tour was the TruMatic 1000 fiber, demonstrated by Roger Michaud. The combination punch laser machine is achieved by adding a 3kW TruDisk solid-state laser and retrofitting the TruPunch 1000 with a laser cutting system, a laser evacuation unit, and a beam guard system. It is designed to automatically sort finished parts up to 7 by 7 in. Processed parts are sent down a chute and can be sorted into a series of four boxes.
Next, we saw the TruLaser 1030, followed by the TruLaser Cell 5030, which is designed for prototypes and medium-volume manufacturing. FABTECH® marked the North American premier of the 5030.
Also demonstrated were the TruBend 5130, equipped with the ToolMaster for automatic tool changes in seconds, and the new TruLaser Center 7030, dubbed the Dream Machine. The 7030 is a fully automated laser processing machine that takes care of production nearly autonomously by offering efficient, automated, and synchronous processes, from programming to sorted and stacked finished parts.
The company also showcased its Smart Services. In this, its first phase of the project, the system can monitor all machines in the field and proactively reach out to users if problems are detected.
Wrapping up the conference, Peter Hoecklin, president and CEO of the North American operations, announced that the company is opening a new 20,000-sq.ft. center in Costa Mesa, Calif.
Wow!
If I had to pick a “wow” moment from today, it would be when I looked through optrel’s crystal2.0 welding helmet with crystal 2.0 Lens Technology (CLT2.0). I’ve looked through welding helmets before, including that time at FABTECH in Las Vegas many years ago when I suited up to try my hand at welding. I have never before seen what I saw today, which was near-perfect color. According to the company, the helmet delivers 31 percent visible light transmission in its light state for optical clarity. In its dark state, the helmet provides a high-contrast view of the welding pool and best-in-class clearness. Don’t take my word—or optrel’s—for it. If you’re at the show on Thursday, head to booth C12142 and try it for yourself.
Richly Deserved Honor
I had been looking forward to my next appointment since I first learned about it from Josh Welton, a frequent contributor to The Fabricator Blog and a columnist for The WELDER magazine. Josh won the American Welding Society’s 2018 Media Award of Excellence for his work in these publications, and I was excited to be able to attend the awards ceremony. Ten winners were acknowledged in different categories, from education programs to veterans and large and small companies that exemplify a commitment to promoting welding and encouraging the welders of the future. I could not be prouder of Josh. His talent is exceeded only by his enthusiasm for the trade and those who ply it.
Waterjet Beauty
After the ceremony, it was back to booth visits, beginning with a stop at Techni Waterjet (B9667). Jim Fields, the company’s national sales manager, said that the show has been really good and steady—a lot of leads to follow up on. He is excited about things in the works. After 28 years of independent ownership, a majority of Techni Waterjet was purchased by Gmm SPA, a CNC saw manufacturer based in Italy. The two companies will be merging their North American operations into one state-of-the-art facility in Charlotte, N.C. beginning Feb. 1, 2019.
In the company’s booth, I witnessed a demonstration of its Techjet-X3® series waterjet cutting machine that was creating beautiful, intricate, nearly flawless shapes out of 1/4-in. aluminum. A photo of this piece is included in the slideshow that accompanies this post.
Levitating!
Then it was time to levitate. I wish. Some of my best dreams involve levitation. But that’s another story. This one is about a visit with Levitate Technologies Inc. (A2806), a company that makes AIRFRAME™, a wearable exoskeleton engineered to improve upper extremity musculoskeletal health for workers who engage in repetitive motion. Lightweight and customizable to fit any body type, the AIRFRAME™ moves seamlessly with the user – and without intruding into the workspace or limiting motion or dexterity.
I can verify that these claims are true. I donned the device, which involved slipping my arms into straps, much like putting on a backpack, tightening two straps, fastening two buckles, and positioning my upper arms into two supports. It may sound cumbersome, but it was anything but. I raised my arms to mimic grinding or welding at shoulder height, and it was amazing. The exoskeleton is very lightweight yet supporting. I felt like a superhero wearing it.
The strictly mechanical, passive device is well-suited to assembly, equipment maintenance, painting, welding, material handling, and fulfillment center work. Major automakers currently are providing the exoskeletons for their workers. Aerospace and heavy equipment manufacturers also are making the investment.
Joseph Zawaideh, who helped me put on the device and gave me an overview, said that users tell him, “I can retire healthy now. I don’t have to worry about injury.” He also has been told that the exoskeleton “might make it cool to be a welder, again.”
Wrap It Up
My last formal appointment of the day was with Signode Industrial Groups (A2833). I immediately spotted a Yellow Jacket wrapping machine. Yellow Jacket is just one of 40 companies under the Signode brand. The group was acquired by Crown Companies in July and continues to operate as Signode.
Also in the booth were strapping units that wrap, cut, and crimp automatically and a H. Bohl machine that wraps bundles of tubes and bars without trays. Signode also provides the consumables these machines use.
Eye-catching
While on the show floor, I also stopped by a company not previously on my radar. Exor America’s (A2759) hi-tech human-machine interface (HMI) caught my eye. With glass instead of plastic screens, these operated much like digital phone monitors with the same finger motions one would use in operating a phone. The displays were crisp and clear. The company is relatively new in the U.S. and hopes to see its HMIs and other technology adopted by machine manufacturers.
The Editor and The Bandit
I would be remiss if I did not include my brief visit to ASC Machine Tools booth (A2140). While waiting for my contact at another appointment, I learned that the Trans Am from “Smokey and the Bandit” was being featured in the roll forming technology provider’s booth. It was close by, so I decided to check it out. Little did I know that the Bandit (Burt Reynolds’ impersonator Tim Phillips) was also in the booth. It was a photo op that could not be ignored.
The Perfect Ending
The day ended with the annual FMAC Meet the Editors event, at which those of us who work on our many industry publications spend time with people we serve. Good food, good people. It doesn’t get much better. Check back late tomorrow for the day 3 wrap-up.
subscribe now
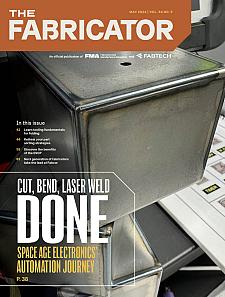
The Fabricator is North America's leading magazine for the metal forming and fabricating industry. The magazine delivers the news, technical articles, and case histories that enable fabricators to do their jobs more efficiently. The Fabricator has served the industry since 1970.
start your free subscriptionAbout the Author
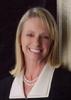
Vicki Bell
2135 Point Blvd
Elgin, IL 60123
815-227-8209
- Stay connected from anywhere
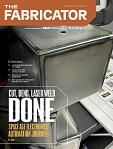
Easily access valuable industry resources now with full access to the digital edition of The Fabricator.
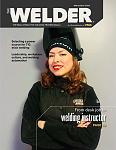
Easily access valuable industry resources now with full access to the digital edition of The Welder.
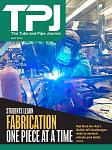
Easily access valuable industry resources now with full access to the digital edition of The Tube and Pipe Journal.
- Podcasting
- Podcast:
- The Fabricator Podcast
- Published:
- 04/30/2024
- Running Time:
- 53:00
Seth Feldman of Iowa-based Wertzbaugher Services joins The Fabricator Podcast to offer his take as a Gen Zer...
- Trending Articles
JM Steel triples capacity for solar energy projects at Pennsylvania facility
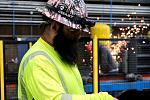
Fabricating favorite childhood memories
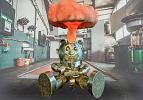
How laser and TIG welding coexist in the modern job shop
Robotic welding sets up small-batch manufacturer for future growth
Ultra Tool and Manufacturing adds 2D laser system
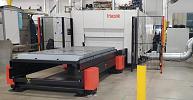
- Industry Events
Pipe and Tube Conference
- May 21 - 22, 2024
- Omaha, NE
World-Class Roll Forming Workshop
- June 5 - 6, 2024
- Louisville, KY
Advanced Laser Application Workshop
- June 25 - 27, 2024
- Novi, MI
Precision Press Brake Certificate Course
- July 31 - August 1, 2024
- Elgin,