Editor-in-Chief
- FMA
- The Fabricator
- FABTECH
- Canadian Metalworking
Categories
- Additive Manufacturing
- Aluminum Welding
- Arc Welding
- Assembly and Joining
- Automation and Robotics
- Bending and Forming
- Consumables
- Cutting and Weld Prep
- Electric Vehicles
- En Español
- Finishing
- Hydroforming
- Laser Cutting
- Laser Welding
- Machining
- Manufacturing Software
- Materials Handling
- Metals/Materials
- Oxyfuel Cutting
- Plasma Cutting
- Power Tools
- Punching and Other Holemaking
- Roll Forming
- Safety
- Sawing
- Shearing
- Shop Management
- Testing and Measuring
- Tube and Pipe Fabrication
- Tube and Pipe Production
- Waterjet Cutting
Industry Directory
Webcasts
Podcasts
FAB 40
Advertise
Subscribe
Account Login
Search
The economics of worker retention
- By Dan Davis
- November 21, 2014
Would you jump from one job to another for an additional 25 cents per hour?
Previous conversations with metal fabrication shop owners and managers suggest that many workers would. In fact, a couple of fabricators shared a melancholy laugh about the situation while chatting at the FABTECH® tradeshow in Atlanta. One shop specializes in heavy-duty weldments and the other is known for its complex precision fabrications, but both offer competitive wages for the area and varied work that should keep shop floor workers engaged. Yet both still struggle to retain workers who take the opportunity for a quick raise—even if it may be a short-term opportunity.
For example, the precision fab shop is located in a very tight labor market in the Southeast. Right now the labor pool is that much shallower because the oil and energy industry is paying top dollar to anyone willing to strike an arc and produce decent work. With the price per barrel for oil hovering around $70, one might wonder what the future for this work will be in the coming months, but only six months ago, it looked like the U.S. was sitting on top of the world, as hydraulic fracturing technology advancements have made this country a leading resource of oil and natural gas. The pay may be excellent, but the long-term play is questionable considering that an organization like OPEC can easily manipulate global markets to make a statement.
Now compare that to the metal fabricating industry. As Senior Editor Tim Heston wrote in his 2015 forecast article in the December 2014 issue of The FABRICATOR, this industry is looking at another year of reasonable growth, which follows two years of similar expansion. The dramatic and almost immediate spike in growth that normally occurs after an economic downturn didn’t occur after the Great Recession; it’s been steady as she goes since 2012. Manufacturing workers aren’t getting rich, but they can sleep at night knowing that demand for metal fabricated products remains fairly high—even in the face of slow economic growth in Asia and Europe.
The metal fabrication worker has a basic choice in these instances: Pursue a bump in wages or make the most of the career path at his or her current place of employment. More often than not, the dollars win out.
Shop owners often argue that these workers typically come back after a layoff or the seasonal work that created the better-paying opportunity dries up. Unfortunately, the fab shop doesn’t have a huge desire to bring this talent back into the fold. The idea is not to create “a revolving door” of workers, as the general manager of the heavy-duty welding operation put it. By allowing these workers to come back when their new opportunities come to an end, the company is unofficially condoning the original departures.
Even the experienced voice of a veteran worker isn’t able to grab the attention of a younger worker looking to maximize his compensation. The general manager of the fab shop said he actually has a welder who made the jump to another shop early in his career only to learn that the new employer lacked a lot of the organization and stability his previous employer had. He was welcomed back, but even the veteran welder’s experience and warnings do little to deter others from jumping to what may seem to be a more lucrative opportunity.
This trend is especially important for metal fabricating companies because they are already struggling to find the right skilled workers for open positions and available wages. As the Fabricators & Manufacturers Association’s economic analyst Chris Kuehl described in the Nov. 20 edition of the “Fabrinomics®” e-newsletter, economists are suggesting that the inability to fill these jobs could shave 1 or 2 percent of GDP growth in the future. If these companies can’t find the right worker, they need to at least hold on to the ones that do the work right.
Metal fabricators have a great story to tell. They just need to share it with everyone, including the workers on the shop floor. They need to know what the long-term plans are for the company and how they might fit into those plans—or even grow in the company. These open lines of communication create an environment where each employee is more engaged in the job and how his or her actions affect overall business performance. They feel like they are part of something larger than themselves and don’t have the wanderlust that often overtakes workers stuck in positions where the highlight of the day is clocking out at the end of a shift.
Metal fabricators also need to step up their training efforts. Obviously, this can prove to be both expensive and time-consuming, but it shows employees that their company is willing to make an investment in them while others may not.
The investment made to create an environment where a worker won’t jump to another job for a small wage increase is money well spent.
subscribe now
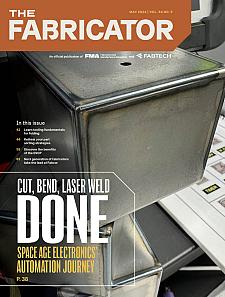
The Fabricator is North America's leading magazine for the metal forming and fabricating industry. The magazine delivers the news, technical articles, and case histories that enable fabricators to do their jobs more efficiently. The Fabricator has served the industry since 1970.
start your free subscriptionAbout the Author
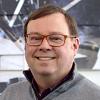
Dan Davis
2135 Point Blvd.
Elgin, IL 60123
815-227-8281
Dan Davis is editor-in-chief of The Fabricator, the industry's most widely circulated metal fabricating magazine, and its sister publications, The Tube & Pipe Journal and The Welder. He has been with the publications since April 2002.
- Stay connected from anywhere
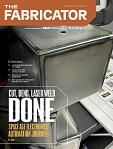
Easily access valuable industry resources now with full access to the digital edition of The Fabricator.
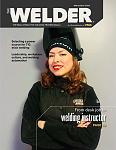
Easily access valuable industry resources now with full access to the digital edition of The Welder.
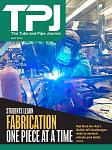
Easily access valuable industry resources now with full access to the digital edition of The Tube and Pipe Journal.
- Podcasting
- Podcast:
- The Fabricator Podcast
- Published:
- 04/30/2024
- Running Time:
- 53:00
Seth Feldman of Iowa-based Wertzbaugher Services joins The Fabricator Podcast to offer his take as a Gen Zer...
- Industry Events
Pipe and Tube Conference
- May 21 - 22, 2024
- Omaha, NE
World-Class Roll Forming Workshop
- June 5 - 6, 2024
- Louisville, KY
Advanced Laser Application Workshop
- June 25 - 27, 2024
- Novi, MI
Precision Press Brake Certificate Course
- July 31 - August 1, 2024
- Elgin,