- FMA
- The Fabricator
- FABTECH
- Canadian Metalworking
Categories
- Additive Manufacturing
- Aluminum Welding
- Arc Welding
- Assembly and Joining
- Automation and Robotics
- Bending and Forming
- Consumables
- Cutting and Weld Prep
- Electric Vehicles
- En Español
- Finishing
- Hydroforming
- Laser Cutting
- Laser Welding
- Machining
- Manufacturing Software
- Materials Handling
- Metals/Materials
- Oxyfuel Cutting
- Plasma Cutting
- Power Tools
- Punching and Other Holemaking
- Roll Forming
- Safety
- Sawing
- Shearing
- Shop Management
- Testing and Measuring
- Tube and Pipe Fabrication
- Tube and Pipe Production
- Waterjet Cutting
Industry Directory
Webcasts
Podcasts
FAB 40
Advertise
Subscribe
Account Login
Search
Steel processor reduces labor requirements with robotic shot blast system
- April 1, 2024
- News Release
- Finishing
Situation
With an inventory of 4,000 tons of different steel grades and qualities, Ottostahl uses flame and plasma cutting to produce custom precision components at its facility in Magdeburg, Germany. In addition to plate and sheet cutting, the company provides postprocessing operations such as shot blasting, drilling, and mechanical chamfering.
In its shot blasting department, the company uses three machines: two continuous-flow roller conveyor machines with an operating width of 3,800 mm and a rotary table blast machine. After 60 years of service, the old rotary table blast machine was due for replacement.
Ottostahl’s key requirements for a new system were specified shot blast results for a variety of components, short cycle times, and high energy efficiency. Since finding qualified workers in Magdeburg is very difficult, the company also required fully automatic mechanical handling of components to relieve personnel from strenuous physical activities.
Resolution
Based on these specifications, Rösler and automation specialist Teqram developed a fully automatic shot blasting system around the Easy Shotblaster RDT 150 rotary table machine. The entire blast system is integrated into a manufacturing cell measuring 8 by 8 m and comprising an intelligent stationary robot and the RDT 150 shot blast machine equipped with suitable accessories.
With its image processing technology, the vision-controlled robot automatically recognizes the components placed into its working section, completely independent from their position on the pallet. This eliminates the need for time-consuming robot teaching or programming. Moreover, with the intuitive interface, the operator requires no special knowledge.
After the automatic selection of a suitable gripper from the gripper magazine, the robot picks up the components and places them on the rotary table in optimum position. Then it provides component data to the machine controls for selecting a suitable processing program. After half of the cycle time is over, the robot automatically turns the components on the rotary table to blast the other side. After the blast process is complete, the robot returns the finished workpieces to the pallet.
With a table diameter of 1,500 mm and a load bearing capacity of 500 kg, the machine handles blast cleaning of workpieces with a wide variety of sizes and shapes. To ensure the required short cycle times, the machine is equipped with two Gamma 300G turbines, each with an installed power of 11 kW. Using curved Y-shaped throwing blades, the turbines deliver improved blast performance while consuming significantly less energy. The bulkheads mounted in front of the turbines also help reduce cycle times and energy consumption.
When the workpieces on the table are turned, the blast media flow is turned off, but the turbines continue running at full speed. This prevents costly energy peaks that occur when the turbines are decelerating and accelerating. Before the robot turns the workpieces, a blow-off system removes residual blast media from the rotary table.
About 90% of all components can be loaded and unloaded by the robot. Components that exceed the robot’s weight capacity can be loaded and unloaded by crane. Likewise, very small components can be loaded this way when automatic loading would require too much time. For safety reasons, in case of manual loading, the turbines are completely turned off before the door to the blast chamber can be opened.
The compact shot blast machine’s sturdy design helps guarantee a high equipment uptime. For example, the blast chamber, made from tough manganese steel, is lined with replaceable wear plates made from highly wear-resistant material. In addition, both sides of the Y-shaped throwing blades in the turbines can be used, nearly doubling their life. A quick-exchange system allows the throwing blades to be replaced without dismounting the turbines.
The highly automated system gives Ottostahl efficient blast cleaning of a broad range of sheet metal components while reducing labor input and improving working conditions for the employees.
subscribe now
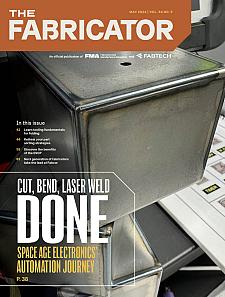
The Fabricator is North America's leading magazine for the metal forming and fabricating industry. The magazine delivers the news, technical articles, and case histories that enable fabricators to do their jobs more efficiently. The Fabricator has served the industry since 1970.
start your free subscription- Stay connected from anywhere
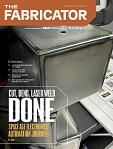
Easily access valuable industry resources now with full access to the digital edition of The Fabricator.
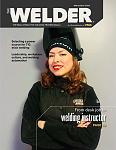
Easily access valuable industry resources now with full access to the digital edition of The Welder.
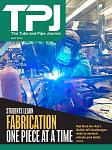
Easily access valuable industry resources now with full access to the digital edition of The Tube and Pipe Journal.
- Podcasting
- Podcast:
- The Fabricator Podcast
- Published:
- 04/16/2024
- Running Time:
- 63:29
In this episode of The Fabricator Podcast, Caleb Chamberlain, co-founder and CEO of OSH Cut, discusses his company’s...
- Trending Articles
Tips for creating sheet metal tubes with perforations
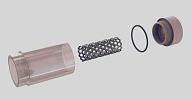
Supporting the metal fabricating industry through FMA
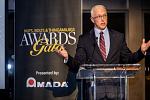
JM Steel triples capacity for solar energy projects at Pennsylvania facility
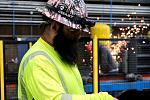
Fabricating favorite childhood memories
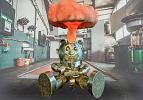
Omco Solar opens second Alabama manufacturing facility
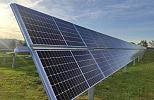
- Industry Events
16th Annual Safety Conference
- April 30 - May 1, 2024
- Elgin,
Pipe and Tube Conference
- May 21 - 22, 2024
- Omaha, NE
World-Class Roll Forming Workshop
- June 5 - 6, 2024
- Louisville, KY
Advanced Laser Application Workshop
- June 25 - 27, 2024
- Novi, MI