- FMA
- The Fabricator
- FABTECH
- Canadian Metalworking
Categories
- Additive Manufacturing
- Aluminum Welding
- Arc Welding
- Assembly and Joining
- Automation and Robotics
- Bending and Forming
- Consumables
- Cutting and Weld Prep
- Electric Vehicles
- En Español
- Finishing
- Hydroforming
- Laser Cutting
- Laser Welding
- Machining
- Manufacturing Software
- Materials Handling
- Metals/Materials
- Oxyfuel Cutting
- Plasma Cutting
- Power Tools
- Punching and Other Holemaking
- Roll Forming
- Safety
- Sawing
- Shearing
- Shop Management
- Testing and Measuring
- Tube and Pipe Fabrication
- Tube and Pipe Production
- Waterjet Cutting
Industry Directory
Webcasts
Podcasts
FAB 40
Advertise
Subscribe
Account Login
Search
DMACC emeritus professor makes face shields for Iowa hospital
- April 17, 2020
- News Release
- Safety
Cory Thompson, an emergency room nurse at St. Anthony Regional Hospital in Carroll, Iowa, and a 2013 graduate of the Des Moines Area Community College (DMACC) Carroll Campus nursing program, knew that he and his fellow health care workers were going to need more personal protective equipment (PPE) during the COVID-19 pandemic. And he also knew who to call—his dad.
Jack Thompson, a DMACC emeritus professor of industrial-electromechanical technology, was in the midst of remodeling his Carroll, Iowa, home when his son called.
“I had several dust masks, but no safety glasses,” said Thompson, reflecting on his immediate thoughts. “After some thinking, I asked my son if [the hospital workers] could use a full-face shield, and he said that would be the preferred type of protection.”
The elder Thompson sprang into action, first taking a closer look at his DMACC welding gear. He noticed that the headgear was in good shape, but the plastic lenses weren’t looking so good.
His next call was to Matheson, Carroll’s local welding supply shop. Matheson didn’t have any replacement lenses for the type of headgear Thompson was calling about, but they did have an older version of the lenses on hand. Thompson set up an appointment to look at the lenses and was excited when he determined he could cut them to fit.
Thompson then called DMACC Carroll Campus Provost Dr. Joel Lundstrom to ask if he could use the DMACC headgear, explaining how it would be used at the hospital.
“I immediately thought it was a good cause and was needed for the safety of the medical community in Carroll,” Lundstrom said.
Thompson returned to the supplier and purchased enough of the older-version lenses to begin his new project—which included carefully modifying the older lenses to fit the new headgear. This meant cutting the lenses from a twist-lock fit to a snap-in fit, with two small bolts to hold the lenses in place.
“Before I could put the lenses into the headgear, I had to disassemble the headgear and clean them, so I ran them through three cycles in my dishwasher,” Thompson said. “I then used a green pad to make sure all of the surfaces were clean of any metal that may have been embedded in the plastic. It also took about an hour of scrubbing to clean my dishwasher after I was done.”
After reassembling the face shields, he called his son, who picked them up and took them to St. Anthony. It proved to be a popular delivery.
“By providing us with face shields, you are not only protecting our staff, you are protecting the patients and community we’re privileged to serve,” said Bailee Schleisman, RN, who works as an infection preventionist at the hospital.
But Thompson was just getting started.
“The next day while watching a video on YouTube, I noticed a simpler version of the [face shields] that I had just rebuilt,” Thompson said. “I asked my son if the hospital could use more shields, and his response was ‘most definitely, yes.’”
Thompson went back to Matheson to see if he could purchase their remaining lenses, but safety equipment sales had been frozen because of priority needs elsewhere.
After returning home, Thompson was sitting in his living room and considering alternative options when he noticed a poster he had framed. He started thinking the plastic might be flexible enough to wrap around his head, and the deconstruction began. He knew he needed some padding for the forehead, so he got some Velcro. He also realized the items needed to be sanitized, so the ability to disassemble it for cleaning was very important. The next step was figuring out how to cut the plastic.
“I tried a scissors first, but the plastic was too brittle, so I turned to a Dremel tool with a cutting wheel,” Thompson said. “It worked, but I figured out later that an oscillating saw works even better.”
Thompson said it takes him about an hour to make each face shield, and he has made 26 to date, including the initial batch of six that went to the hospital. He said he has about $300 invested so far.
“As far as making more, materials are getting hard to find, but I will keep changing and making them,” Thompson said.
“This is part of a larger DMACC effort to support the communities that we serve,” Lundstrom said.
subscribe now
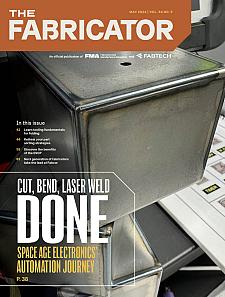
The Fabricator is North America's leading magazine for the metal forming and fabricating industry. The magazine delivers the news, technical articles, and case histories that enable fabricators to do their jobs more efficiently. The Fabricator has served the industry since 1970.
start your free subscription- Stay connected from anywhere
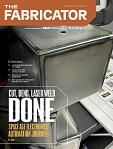
Easily access valuable industry resources now with full access to the digital edition of The Fabricator.
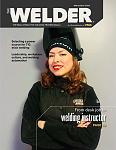
Easily access valuable industry resources now with full access to the digital edition of The Welder.
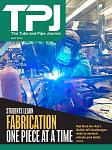
Easily access valuable industry resources now with full access to the digital edition of The Tube and Pipe Journal.
- Podcasting
- Podcast:
- The Fabricator Podcast
- Published:
- 04/30/2024
- Running Time:
- 53:00
Seth Feldman of Iowa-based Wertzbaugher Services joins The Fabricator Podcast to offer his take as a Gen Zer...
- Industry Events
Pipe and Tube Conference
- May 21 - 22, 2024
- Omaha, NE
World-Class Roll Forming Workshop
- June 5 - 6, 2024
- Louisville, KY
Advanced Laser Application Workshop
- June 25 - 27, 2024
- Novi, MI
Precision Press Brake Certificate Course
- July 31 - August 1, 2024
- Elgin,