- FMA
- The Fabricator
- FABTECH
- Canadian Metalworking
Categories
- Additive Manufacturing
- Aluminum Welding
- Arc Welding
- Assembly and Joining
- Automation and Robotics
- Bending and Forming
- Consumables
- Cutting and Weld Prep
- Electric Vehicles
- En Español
- Finishing
- Hydroforming
- Laser Cutting
- Laser Welding
- Machining
- Manufacturing Software
- Materials Handling
- Metals/Materials
- Oxyfuel Cutting
- Plasma Cutting
- Power Tools
- Punching and Other Holemaking
- Roll Forming
- Safety
- Sawing
- Shearing
- Shop Management
- Testing and Measuring
- Tube and Pipe Fabrication
- Tube and Pipe Production
- Waterjet Cutting
Industry Directory
Webcasts
Podcasts
FAB 40
Advertise
Subscribe
Account Login
Search
Technology Spotlight: Sheet, tube fabricator increases productivity by 40 percent with automated material storage/delivery
- February 6, 2019
- Product Release
- Shop Management
Situation
König Metall, Gaggenau, Germany, is a fourth-generation family-owned business that processes sheet metal, tubes, and pipes for numerous industries, including electronics and automotive. The company, which employs 600 people in Germany and more than 1,200 worldwide with subsidiaries in Italy, Poland, Canada, and Croatia, produces parts to customer requirements using the newest-generation laser cutting, punching, and nibbling machines.
To meet constantly increasing market requirements, the company must remain flexible and productive. This includes transparent stock and fully automatic supply to its production lines. However, König Metall was unable to achieve these conditions to the required extent. This issue became a big challenge when a major customer closed its production without notice and decided to outsource its parts to König Metall.
“Our warehouse was about to burst,” reported Mario Eberle, CNC sheet metal technology production manager. “We stored on about 600 square meters within the production area. Our total load capacity contains only 350 insufficient storage spaces in the existing sheet racks. The rest was stored where there was space on the floor.”
Despite the use of an enterprise resource planning system, this situation repeatedly led to shortages. In addition, the supply of sheet metal for the processing machines became increasingly complex. Operators had to search for the material, relocate it, and then transport it manually by forklift.
“This chaotic warehousing caused long response times,” recalled Eberle. “Furthermore, the frequent movements of the material often resulted in scratches, which, at the end of the day, led to board rejects.”
Resolution
The company contacted Remmert GmbH to implement a new intralogistics concept that directly connects production facilities to the warehouse with a fully automated central supply system.
Remmert redesigned the warehouse to help make the increase in productivity more sustainable for König Metall, placing the existing processing machines closer to the storage to save space and speed up material flow.
The heart of the automation system is the MIDI sheet metal storage unit, offering 595 storage spaces and a maximum storage volume of 1,785 tons. With its compact design, the system offers high storage density, giving the company space savings of 300 sq. m. Two laser cutting machines connected to the system are in operation 24 hours a day, supplied with raw material by Remmert’s Laser Flex 4.0. This unit provides fully automated loading/unloading and enables a material change in 60 seconds.
By implementing these changes, König Metall has increased throughput times in production by 40 percent and nearly eliminated downtime. As soon as a production machine places an order, the automated supply vacuum unit of Laser Flex 4.0 takes the raw material from the sheet metal storage and moves it independently to the connected laser machines. After cutting, the fork unit of the unloading station lifts the finished sheet metals from the shuttle table of the laser. Finished parts are returned to MIDI storage or sent to the next process step.
The connection of the storage unit to the processing machines is managed by Remmert’s warehouse management software PRO WMS Enterprise. “The machines communicate automatically with [the software]. As soon as a production order is loaded, the [software] assigns the relevant movement command to the storage and retrieval unit, and the requested material is delivered,” explained Frank Baudach, Remmert sales manager DACH.
The software also stores all goods movements to help ensure transparent storage management. These automated processes eliminate almost all manual work steps.
Productivity of the laser cutting systems has been significantly increased. The forklift traffic for material transports, which required three to five employees, has been eliminated. Downtime no longer exists, because the material is transported automatically.Remmert GmbH
subscribe now
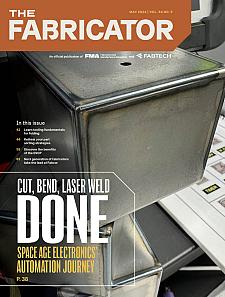
The Fabricator is North America's leading magazine for the metal forming and fabricating industry. The magazine delivers the news, technical articles, and case histories that enable fabricators to do their jobs more efficiently. The Fabricator has served the industry since 1970.
start your free subscription- Stay connected from anywhere
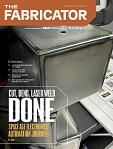
Easily access valuable industry resources now with full access to the digital edition of The Fabricator.
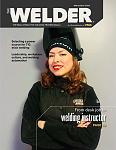
Easily access valuable industry resources now with full access to the digital edition of The Welder.
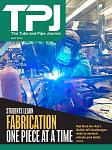
Easily access valuable industry resources now with full access to the digital edition of The Tube and Pipe Journal.
- Podcasting
- Podcast:
- The Fabricator Podcast
- Published:
- 04/30/2024
- Running Time:
- 53:00
Seth Feldman of Iowa-based Wertzbaugher Services joins The Fabricator Podcast to offer his take as a Gen Zer...
- Industry Events
Pipe and Tube Conference
- May 21 - 22, 2024
- Omaha, NE
World-Class Roll Forming Workshop
- June 5 - 6, 2024
- Louisville, KY
Advanced Laser Application Workshop
- June 25 - 27, 2024
- Novi, MI
Precision Press Brake Certificate Course
- July 31 - August 1, 2024
- Elgin,