Senior Editor
- FMA
- The Fabricator
- FABTECH
- Canadian Metalworking
Categories
- Additive Manufacturing
- Aluminum Welding
- Arc Welding
- Assembly and Joining
- Automation and Robotics
- Bending and Forming
- Consumables
- Cutting and Weld Prep
- Electric Vehicles
- En Español
- Finishing
- Hydroforming
- Laser Cutting
- Laser Welding
- Machining
- Manufacturing Software
- Materials Handling
- Metals/Materials
- Oxyfuel Cutting
- Plasma Cutting
- Power Tools
- Punching and Other Holemaking
- Roll Forming
- Safety
- Sawing
- Shearing
- Shop Management
- Testing and Measuring
- Tube and Pipe Fabrication
- Tube and Pipe Production
- Waterjet Cutting
Industry Directory
Webcasts
Podcasts
FAB 40
Advertise
Subscribe
Account Login
Search
Insertar la tornillería, doblar, y ya está
El potencial de la automatización del doblado y de la inserción de tornillería
- By Tim Heston
- March 31, 2020
- Article
- Assembly and Joining
La inserción de tornillería no es el más glamuroso de los procesos en la fabricación de chapa metálica, pero es algo que tiene que hacerse bien. No hay nada más perjudicial que el retrabajo o el desperdicio causado por problemas de tornillería, ya sea por tornillería perdida o sin complementos, o por el sujetador equivocado.
Los fabricantes afrontan el problema usando una combinación de estrategias. Después de algunas 5S, un departamento de sujeciones podría incluir contenedores con etiquetas que incluyan fotos y establecer un sistema de reordenamiento, ya sea propio o a través de un inventario administrado por el vendedor, para que el departamento nunca se quede sin la tornillería que necesita.
El taller podría aplicar prueba y error al proceso mediante modificaciones pequeñas del diseño de producto (¿la pieza realmente necesita todos estos tipos diferentes de tornillería?), y quizás establecer familias de productos y flujos de valor para limitar la variedad de partes que fluyen a través de ciertas celdas de tornillería. Incluso podría eliminar la inserción de tornillería como un departamento e integrar prensas de inserción cerca de otros procesos, especialmente cuando esto facilite el acceso a los agujeros. Un operador podría insertar sujetadores, hacer algunos dobleces en una prensa dobladora, luego girar de nuevo para insertar la tornillería restante.
La combinación de prensas dobladoras e inserción de tornillería puede ser efectiva, especialmente si una celda se diseña en torno a una familia de partes o a una gama específica de geometrías de partes. En algún punto la automatización se vuelve una opción viable. Sin embargo, ¿cuál es el punto exactamente? Para contestar esta pregunta, The FABRICATOR habló con Ryan Smallfoot, supervisor de integración de Acieta, en Council Bluffs, Iowa.
Smallfoot explicó que una mezcla compleja de partes no es necesariamente una barrera; algunas celdas robóticas pueden producir una parte diferente tras otra. Sin embargo, el proceso sí necesita ser repetible. Un robot típico tiene repetibilidad mucho más exacta de lo que la mayoría de las aplicaciones de chapa metálica requieren, pero las chapas pueden pegarse entre sí. Una chapa puede deslizarse, quizás no quedar exactamente plana sobre el yunque de la prensa de sujeción. También existe la posibilidad de errores de alimentación de tornillería. Algunos problemas pueden eliminarse por completo, otros sólo minimizarse. Sin embargo, entre más variables de proceso pueda sacar de la ecuación un fabricante, mejor.
Mezcla de partes y programación
La construcción de una celda de automatización empieza definiendo exactamente qué va a fluir por la misma. Smallfoot describió una aplicación en la cual una variedad aparentemente infinita de piezas de chapa metálica fluía a través de una celda robótica, que implicaba tanto inserción de tornillería como formado en prensa dobladora. Nadie pasó horas con un control colgante de enseñanza en una celda robótica, y la compañía no puso a un ejército de programadores a correr simulaciones fuera de línea.
En lugar de eso, la programación paramétrica tuvo un papel clave. Las partes tenían muchísimas variaciones, pero sólo en parámetros definidos. Cuando la geometría de una parte cambiaba en cierta dimensión definida, el movimiento del robot se ajustaba automáticamente a ese cambio.
Smallfoot aclaró que las celdas automatizadas pueden manejar diversas partes, incluso sin programación paramétrica. Las únicas restricciones físicas implican la capacidad del herramental de extremo de brazo del robot de asir y manipular las partes en el transcurso de las operaciones: asir la pieza, acomodarla (orientación), inserción de tornillería, doblado y apilamiento.
La simulación fuera de línea hace muy eficiente la programación de nuevas partes; un técnico debe usar el colgante de enseñanza sólo para algunos pequeños ajustes finales. Sin embargo, los talleres necesitan considerar la programación, hecha ya sea fuera de línea o en línea.
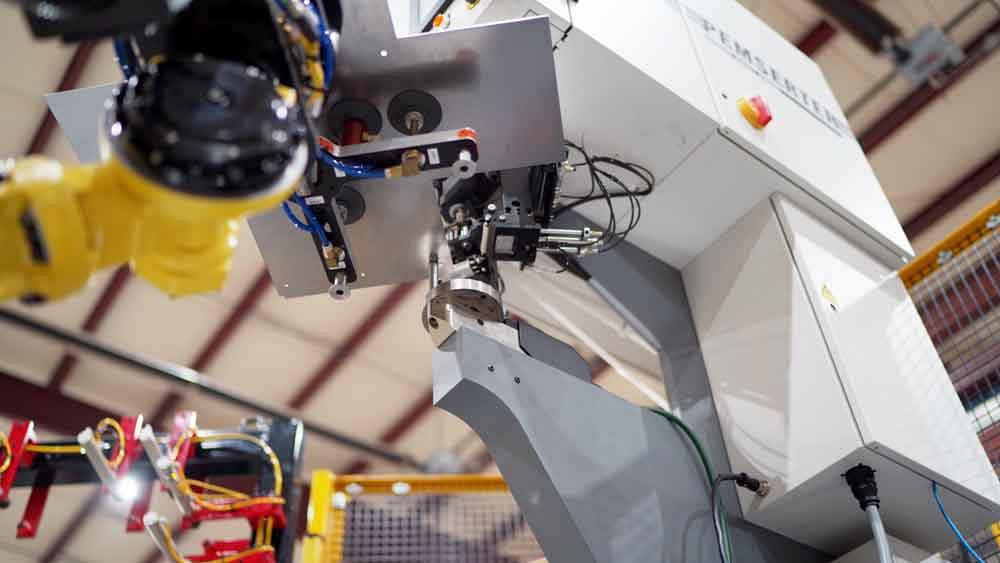
Un robot coloca una pieza de trabajo para la configuración del sistema de inserción de tornillería para alimentar e insertar varios tipos diferentes de tornillería.
El herramental correcto de extremo de brazo
La programación y la simulación fuera de línea de la actualidad son herramientas poderosas, especialmente en cuanto al diseño del herramental de extremo de brazo del robot y en cuanto a evitar colisiones. Por ejemplo, para la inserción de tornillería con frecuencia es necesario que el herramental de extremo de brazo del robot permanezca libre de tubos de alimentación de tornillería y de otros componentes cerca del bastidor trasero de la prensa, detrás del yunque.
Smallfoot agregó que esto depende de la configuración de la máquina de tornillería en la celda. Sin embargo, la trayectoria del robot debe considerar el potencial de colisiones. Entre más despejada sea la trayectoria del robot—lejos de todo punto potencial de colisión—mejor. Esencial para todo esto es el diseño del herramental de extremo de brazo. Mientras mejor sea el diseño del herramental, más trayectorias libres de colisiones puede tomar el robot para llegar al yunque y a la torreta de la máquina de inserción y a sus alrededores.
El herramental de extremo de brazo determinará los límites del tamaño de partes; pero como lo explicó Smallfoot, enfoques alternativos verificados mediante simulación podrían abrir la puerta a ciertas partes que pudieran ser demasiado pequeñas para manejarse de otra manera. Por ejemplo, una pieza podría incluir varias partes pequeñas unidas entre sí por lengüetas. Un robot con la herramienta correcta de extremo de brazo podría transportar esta pieza por la inserción de tornillería e incluso por el formado en la prensa dobladora, doblando varias piezas a la vez. Por supuesto, las piezas tendrían que separarse después del formado, pero hacerlo sería más rápido que tener que insertar tornillería y formar todas esas piezas pequeñas a mano.
Ubicación, ubicación, ubicación
La programación debe asegurar que la operación se mantenga lo más sencilla y eficiente posible para una mezcla dada de partes. Para ilustrarlo, Smallfoot describió los retos de una celda de inserción de tornillería con respecto a los valores de tonelaje de la prensa de inserción.
A veces ocurrían problemas de tonelaje excesivo debido a la geometría de los agujeros en sí—específicamente, una rebaba en el diámetro interior. Para hacer más consistente la inserción de hardware, se programó el láser para cortar una muesca diminuta en el punto de salida del agujero. Esto aseguraba que se pudiera insertar la tornillería sin tonelaje excesivo.
Ocasionalmente la pieza podía no quedar exactamente a nivel en el yunque, lo cual también significaba que la prensa necesitaba ejercer más tonelaje para insertar la tornillería. ¿Qué causaba este error de posicionamiento, exactamente? El robot en sí es sumamente exacto, pero entran en escena otras variables, incluyendo la geometría de parte y los efectos de la inercia y de la gravedad. La inconsistencia casi despreciable causaba a veces que la máquina ejerciera fuerza excesiva y se detuviera.
En operaciones manuales, esto no sería un gran problema. De hecho, es bienvenido debido a que el paro es un punto establecido de seguridad diseñado para evitar que la máquina toque fondo y produzca una parte mala. Si la máquina se detiene, el operador simplemente reorienta la pieza, reinicia el ciclo y continúa.
Un robot convencional no puede hacer esto. Sin embargo, la ventana de tonelaje original de la prensa se diseñó para dar cabida a todas las aplicaciones que la prensa pudiera manejar. Aunque para ciertos requerimientos de inserción de la aplicación, la prensa todavía podría ejercer un poco más de tonelaje, y el sujetador de auto-aseguramiento todavía podría insertarse bien dentro de la especificación.
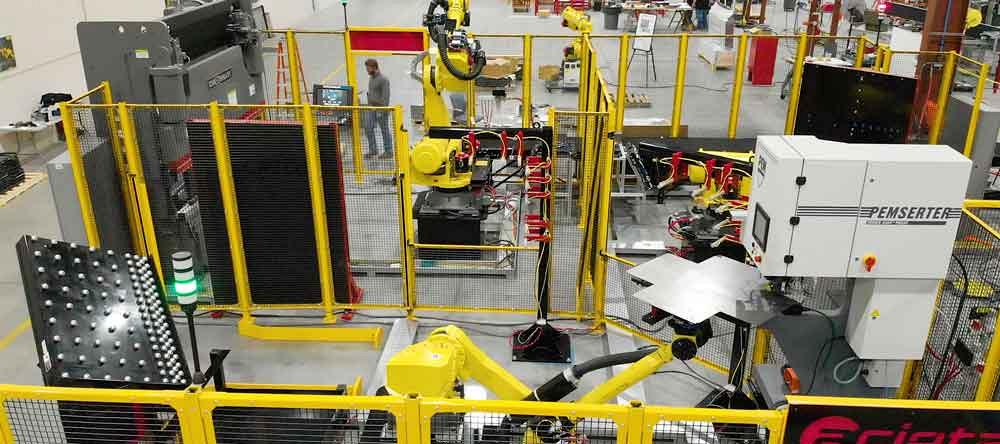
En esta celda, un robot alinea una pieza de trabajo, presenta la pieza para inserción de tornillería, luego transfiere la pieza de trabajo a la celda automatizada adyacente de doblado.
Entonces, para esta aplicación, Smallfoot dijo que el equipo trabajó con el fabricante de equipo original (OEM) de la prensa de tornillería con respecto a actualizaciones de software que ampliaran la ventana de tonelaje muy ligeramente. Agregó que esto podría no aplicarse a todas las celdas automatizadas de tornillería; todo depende de los requerimientos de la aplicación. De todos modos, el ejemplo hace evidentes los retos de ubicación de partes que pueden surgir.
Además, resalta las concesiones que ocurren al diseñar una celda automatizada. Los brazos de robot modernos son muy repetibles, con frecuencia ±0.002 pulgadas, pero el robot en sí es sólo parte de la ecuación. “Los robots son muy exactos”, explicó Smallfoot. “Sin embargo, se necesita realmente una buena mesa de encuadre para poder calificar la pieza, y saber exactamente dónde está la esquina. Y a partir de ese punto, se sabe exactamente en dónde está la herramienta de extremo de brazo en la pieza en sí”.
Considerando la aplicación previa, si la ubicación del agujero es un problema, entonces, ¿por qué el robot no puede simplemente colocar la pieza en un adaptador que asegure la parte sobre el yunque de la prensa de tornillería? Esto podría funcionar, teóricamente, si el adaptador pudiera aceptar todas las piezas en una mezcla dada de partes.
Sin embargo, viene el problema del tiempo de ciclo. Como lo explicó Smallfoot, después de la operación de alineación en la mesa de encuadre, o base de alineación, cuando el herramental de extremo de brazo libera la parte, éste debe volver a asir la parte y a veces, dependiendo de las circunstancias, regresar a la mesa de encuadre y realinear la parte. De lo contrario, el robot está operando efectivamente a ciegas.
Como lo explicó Smallfoot, agregar un adaptador a la inserción de tornillería es una opción. Si el adaptador está hecho a tolerancias exigentes, puede usarse como una base de alineación, por lo que el robot podría no necesitar regresar a la mesa de encuadre cada vez que libera y vuelve a asir una parte. Sin embargo, soltar y volver a asir la pieza de ese adaptador sí agrega tiempo de ciclo, lo cual puede ser problemático.
En la mayoría de los casos, lo más sencillo es lo mejor. Y en la aplicación que describió Smallfoot, un cambio en el software que ampliara ligeramente la ventana de tonelaje era la estrategia más sencilla, sin requerir adaptadores ni otras complicaciones.
La simplicidad también toma en cuenta la secuenciación del trabajo. Por ejemplo, digamos que una parte tiene ciertas ubicaciones de tornillería que crean retos de formado. En una celda manual, un operador podría insertar tornillería, regresar a la prensa dobladora para crear algunos dobleces, insertar más tornillería, luego regresar para crear los dobleces finales. El insertar la tornillería en esta secuencia podría eliminar problemas de formado, especialmente cuando la tornillería se localiza cerca de líneas de doblez.
Sin embargo, como lo explicó Smallfoot, esto puede no ser práctico en una configuración robótica. Sí, un robot teóricamente podría llevar y traer una parte entre el doblado y la inserción de tornillería, pero esto sí aumenta la complejidad. Dependiendo de la parte y de cómo es manipulada, el robot podría necesitar hacer uno o más paros adicionales en la base de alineación, y su herramental de extremo de brazo podría necesitar ser capaz de posicionar la parte parcialmente formada en la prensa de inserción. Esto además podría requerir un cambio de herramienta de extremo de brazo, lo que aumenta aún más la complejidad. El robot teóricamente podría hacerlo todo, pero con toda probabilidad un operador humano podría hacerlo más rápido.
Una mejor estrategia de automatización empezaría con el diseño de la parte. ¿La tornillería necesita estar tan cerca de las líneas de doblez? De ser así, ¿la operación de formado puede usar punzones en la prensa con relieves que puedan aceptar la tornillería insertada? Si éste es el caso, entonces un robot podría llevar la pieza desde la inserción de tornillería y luego directamente al doblado.
Smallfoot agregó que “nunca se puede decir nunca”, cuando se trata de automatización. Sin embargo, en muchos casos mientras menos compleja sea la trayectoria de robot, más rápido puede ser el tiempo de ciclo, y más eficiente la celda de automatización.
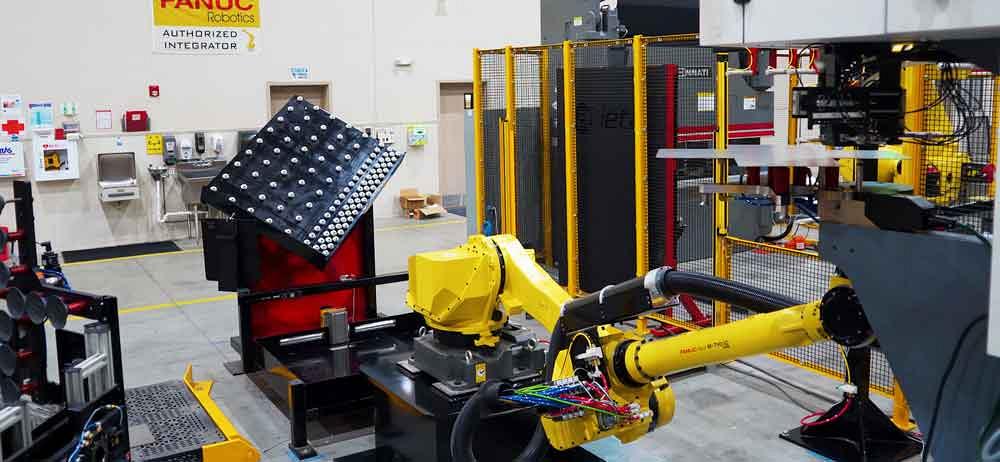
Después de presentar la parte a la estación de alineación (en el fondo), un robot presenta una parte a una prensa de inserción de tornillería. Después de la inserción, la pieza se transfiere directamente a una operación automatizada de doblado.
Adaptar y reintentar
No todo en una operación robótica de inserción de tornillería necesita funcionar absolutamente de manera perfecta. La automatización robótica puede programarse para adaptarse y reintentar. Por ejemplo, Smallfoot describió una operación de inserción de tornillería que ocasionalmente se detenía debido a una falla de vacío. La tornillería era alimentada desde uno de varios alimentadores tipo tazón. La tornillería bajaba por un tubo flexible hacia una lanzadera junto a la cortina de la máquina. Cuando iniciaba el vacío de la cortina, los dedos de la lanzadera que asían la tornillería se abrían, y la tornillería era succionada y asegurada dentro del cuerpo de la cortina. Con el cuerpo de la cortina en el yunque, la máquina operaba e insertaba el sujetador de auto-aseguramiento en la chapa metálica.
Sin embargo, a veces ese vacío podía fallar. “La máquina misma nos diría si fallaba”, explicó Smallfoot, “y dependiendo de la falla, simplemente le diríamos que reintentara”. Agregó que para la gran mayoría de esas fallas (las cuales en sí eran algo raro), simplemente decirle a la prensa que reintentara resolvía el problema.
Propiedades de los sujetadores y proceso de prueba y error
En la mayoría de los casos, las celdas de automatización pueden usar sujetadores convencionales de auto-aseguramiento—es decir, los mismos que se usarían en operaciones manuales. “Aunque sí sé que algunas compañías que hacen sujetadores los fabricarán a las especificaciones del cliente”, dijo Smallfoot, “de forma que se puedan integrar características en el sujetador que pudieran hacer más fácil la inserción robótica”. Agregó que esto podría incluir entradas especiales y otros auxiliares de ubicación. Sin embargo, Smallfoot dijo que la tornillería a la medida no es absolutamente necesaria para la mayoría de las aplicaciones.
Los ajustes del yunque sí necesitan optimizarse para que se adapten al diámetro del sujetador muy bien, pero no demasiado. “Se busca que el yunque esté lo suficientemente apretado para que pueda ubicar e insertar el sujetador”, explicó Smallfoot, “pero no tan apretado que tenga que forzar el sujetador hacia el yunque. Simplemente debe deslizarse sobre la parte superior”.
Se sigue necesitando una persona que alimente la tornillería a los tazones alimentadores y, por supuesto, el sujetador correcto necesita ir dentro del tazón correcto. Muchos fabricantes están demasiado familiarizados con la frustración del retrabajo o (peor aún) con las devoluciones del cliente por errores de tornillería.
He aquí donde entra en escena el proceso de prueba y error. Smallfoot describió una aplicación reciente de inserción de tornillería que usaba dos tipos, uno con roscas internas y el otro con roscas externas. Afuera de la celda, los alimentadores de tazones podían rellenarse sin parar el sistema. Sensores dentro de los alimentadores de tazones disparaban alarmas que notificaban al personal cuando necesitaban rellenarse.
“Y los alimentadores de tazones estaban claramente marcados cuáles eran cuáles”, explicó, y agregó que incluso si un operador agregaba por error la tornillería equivocada al tazón, el sistema se detendría debido a que la tornillería simplemente no quedaba”. “Los agujeros en las partes son de tamaños diferentes”, dijo. “Por lo tanto, si se pone tornillería en el tazón equivocado, la máquina misma se detendrá porque leerá un tonelaje elevado al tratar de insertar un sujetador más grande en un agujero menor, o no leerá tonelaje alguno al tratar de poner un sujetador más pequeño en un agujero más grande”.
Revisiones de calidad y monitoreo del proceso
Para trabajos que requieren revisiones de calidad a intervalos específicos, una celda automatizada puede funcionar. Como lo explicó Smallfoot, una celda puede programarse para producir cierto número de partes y luego, a intervalos específicos, poner las partes en una ubicación donde personal de inspección pueda acceder a las mismas sin detener la automatización.
También abundan las opciones de monitoreo de procesos. “En un robot, se puede rastrear cualquier falla”, dijo Smallfoot, y agregó que ciertas fallas pueden incluso disparar correos electrónicos u otras notificaciones a técnicos cercanos. Dependiendo de la naturaleza y de la gravedad de la falla, esto podría ser cuando ocurre la falla o a ciertos intervalos.
La capacidad de monitoreo de procesos de las máquinas con las que interactúa el robot, incluyendo la prensa dobladora y la prensa de tornillería, dependerá de la máquina en la celda. “Siempre que la máquina dé una descripción de la falla, podemos llevar una bitácora de eso también”, dijo Smallfoot. Agregó que esas bitácoras pueden no incluir la parte específica que la celda estaba fabricando, pero incluirá la hora en que ocurrió la falla.
Recoger y apilar
La mayoría de las celdas de automatización de chapa metálica de calibre delgado no usan robots con herramental de extremo de brazo magnético; el campo magnético es muy profundo, y el robot recoge varias piezas a la vez; las ventosas no tienen este problema. Además, los sistemas de succión modernos pueden diseñarse para manejar algunas geometrías difíciles, incluso aquéllas con varios cortes interiores, relieves y otras formas.
“Las ventosas están diseñadas en torno a las formas de la parte, ya sea rendijas, ventanas o agujeros”, dijo Smallfoot. “La colocación de las ventosas es importante, y puede haber varias zonas de vacío. Incluso si se tienen ventosas a la mitad del sujetador que agarra parte de un agujero, las ventosas que están hacia el exterior siguen haciendo vacío.
Las ventosas pueden sujetar fuertemente, pero no siempre pueden evitar recoger doblemente. La celda debe incluir tecnología para asegurar que el robot levante sólo una pieza a la vez. Como lo explicó Smallfoot, “muchas celdas usan un dispositivo de escaneo láser que puede verificar el espesor del material; es muy rápido”.
La velocidad es crítica. Si se detecta levantamiento doble, un sistema puede usar un cuchillo de aire u otro dispositivo para separar las chapas. Sin embargo, en muchos casos es más fácil y más rápido mover las piezas dobles levantadas a un área de rechazo, y luego levantar una pieza nueva. Esas piezas rechazadas pueden agregarse después al siguiente lote. La velocidad también es crítica al final de la celda, donde las piezas pueden apilarse, ponerse en una banda transportadora o llevarse corriente abajo de alguna otra manera.
Ese paso final—enviar la parte hacia adelante corriente abajo—es realmente de lo que se trata una automatización efectiva, ya sea inserción de tornillería, formado u otra cosa. Después de todo, una parte no está realmente “terminada” con una operación de manufactura hasta que la siguiente operación pueda hacer algo con ella. Con las variables correctas atendidas, eso es justamente lo que una celda robótica bien diseñada debe hacer.
Acieta LLC, www.acieta.com
About the Author
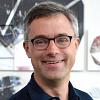
Tim Heston
2135 Point Blvd
Elgin, IL 60123
815-381-1314
Tim Heston, The Fabricator's senior editor, has covered the metal fabrication industry since 1998, starting his career at the American Welding Society's Welding Journal. Since then he has covered the full range of metal fabrication processes, from stamping, bending, and cutting to grinding and polishing. He joined The Fabricator's staff in October 2007.
About the Publication
subscribe now
FMA Communications ha introducido al mercado la edición en Español de la revista The Fabricator. Esta versión consiste del mismo tipo de artículos técnicos y sección de lanzamientos de nuevos productos que actualmente presentan el personal de primera categoría de Fabricator en Inglés.
start your free subscription- Podcasting
- Podcast:
- The Fabricator Podcast
- Published:
- 04/30/2024
- Running Time:
- 53:00
Seth Feldman of Iowa-based Wertzbaugher Services joins The Fabricator Podcast to offer his take as a Gen Zer...
- Trending Articles
Los operadores de prensa dobladora inexpertos hacen indispensable el repensar la seguridad
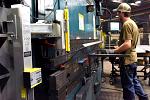
Prescripción para la reducción del desperdicio: arreglo esbelto de las instalaciones
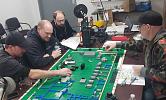
Máquina de corte por láser diseñada para el mercado mexicano
La sierra de doble carro sigue los contornos del tubo perfectamente
La máquina procesadora de placas crea biseles complejos en un solo corte
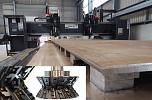
- Industry Events
Pipe and Tube Conference
- May 21 - 22, 2024
- Omaha, NE
World-Class Roll Forming Workshop
- June 5 - 6, 2024
- Louisville, KY
Advanced Laser Application Workshop
- June 25 - 27, 2024
- Novi, MI
Precision Press Brake Certificate Course
- July 31 - August 1, 2024
- Elgin,