Senior Editor
- FMA
- The Fabricator
- FABTECH
- Canadian Metalworking
Categories
- Additive Manufacturing
- Aluminum Welding
- Arc Welding
- Assembly and Joining
- Automation and Robotics
- Bending and Forming
- Consumables
- Cutting and Weld Prep
- Electric Vehicles
- En Español
- Finishing
- Hydroforming
- Laser Cutting
- Laser Welding
- Machining
- Manufacturing Software
- Materials Handling
- Metals/Materials
- Oxyfuel Cutting
- Plasma Cutting
- Power Tools
- Punching and Other Holemaking
- Roll Forming
- Safety
- Sawing
- Shearing
- Shop Management
- Testing and Measuring
- Tube and Pipe Fabrication
- Tube and Pipe Production
- Waterjet Cutting
Industry Directory
Webcasts
Podcasts
FAB 40
Advertise
Subscribe
Account Login
Search
Automatización en movimiento
Cómo podría cambiar el taller de fabricación con la automatización móvil
- By Tim Heston
- March 21, 2022
- Article
- Automation and Robotics
Un vehículo guiado automatizado con horquillas permanece listo para llevar una tarima de partes en Factory Smart de TRUMPF a las afueras de Chicago. MCJ Supply Chain Solutions
Los clientes no pagan para que se muevan partes de un proceso o de una estación a otra. Sin embargo, sin ese movimiento, no puede haber creación de valor (corte, doblado, soldadura, recubrimiento). Si las partes no se mueven, nada ocurre. Peor aún, un manejo inadecuado del material aumenta la variabilidad y la imprevisibilidad, lo cual implica mayor acumulación de piezas en proceso (WIP, por sus siglas en inglés) entre procesos. Mientras mayor sea la acumulación de WIP, mayor será el tiempo de entrega, y menos competitivo se volverá un fabricante. Es un círculo vicioso que vale la pena romper.
La mayoría de los fabricantes a la medida hacen tal variedad de partes que realmente no pueden desviarse mucho de la distribución de taller departamental centrado en los procesos, de ahí la necesidad de montacargas. Sin importar qué tan eficiente sea el flujo de partes, la gente pierde tiempo en apilar, levantar y transportar—todos, procesos sin valor agregado. Sin embargo, en los próximos años muchos talleres podrían liberar a los empleados de todo ese trabajo sin valor optando por alternativas automatizadas en lugar del montacargas: específicamente, el vehículo guiado automatizado (AGV, por sus siglas en inglés) y el robot móvil autónomo (AMR, por sus siglas en inglés).
Los AGV y los AMR
De acuerdo con una investigación de LogisticsIQ, se espera que el mercado global de AGV y AMR alcance 14 mil millones de dólares para 2026, con más de 270 vendedores dando servicio al espacio de la manufactura y la logística. De acuerdo con el estudio, en particular será especialmente robusta la adopción de los AMR, con una tasa de crecimiento anual combinada de aproximadamente 45% entre 2020 y 2026.
Los AGV han recorrido un largo camino desde que usaban alambres o imanes en el piso. Muchos en uso actualmente emplean triangulación combinada con cinta reflejante para lograr lo que la industria denomina localización, o la capacidad para que los AGV sepan dónde están. Tradicionalmente, los AGV recorren una trayectoria fija mientras que los AMR se mueven libremente en un ambiente dinámico, lo cual cambia la manera en que los vehículos evitan obstáculos y afrontan un congestionamiento de tráfico.
“El software para flotas de AMR comparte datos de posición entre los diferentes robots, lo cual los ayuda a evitarse unos a otros antes de que lleguen lo suficientemente cerca entre sí para que sus sensores puedan detectarse”, dijo Andrew Freeney, ingeniero jefe de AMR del integrador de automatización Robex situado en Perrysburg, Ohio. Antes de eso, trabajó más de cuatro años en MiR, proveedor de AMR.
Feeney agregó que las aplicaciones de AMR de la actualidad usualmente ayudan a superar el reto de las áreas con mucho tráfico. Los AMR pueden evitar obstáculos de maneras sofisticadas, y no necesitan seguir rutas con marcadores físicos. Sin embargo, agregó que muchas aplicaciones aprovechan otro rasgo de los AMR: éstos no sólo mueven partes de A a B, sino que además están diseñados para interactuar con otros sistemas automatizados en diversas formas: “hemos tenido aplicaciones donde robots de 6 ejes toman o ponen objetos en un AMR”, dijo Freeney, y agregó que en estos casos las aplicaciones han usado “marcadores de acoplamiento para mejorar la exactitud posicional y ayudar con los diferentes tipos de equipo que quieren tomar y poner objetos en el robot”. Agregó que los AMR además pueden tener módulos superiores que pueden personalizarse para trabajos específicos, más o menos análogos al herramental de extremo de brazo en los robots estacionarios.
Como con buena parte de la automatización, los AGV y los AMR siguen evolucionando. Por ejemplo, los AGV también han mostrado capacidad de interactuar con máquinas. Aparte de la chapa metálica, Jungeinrich tiene una sociedad con DMGMori en un sistema AGV que puede cargar partes, interactuar con tecnología y optimizar el taller de máquinas.
Al final de cuentas, lo más importante no es cómo les dicen sino lo que le pueden ofrecer al fabricante de metal. Cuál es el mejor depende de lo que el fabricante quiera llevar a cabo.
No hay lugar para jardines amurallados
Los vehículos automatizados pueden operar como un nodo bajo el control de producción o el sistema de ejecución de manufactura (MES, por sus siglas en inglés) de una planta. Un vehículo automatizado en sí es adaptivo; si no lo fuera, no sería seguro de usar afuera. Los sensores le permiten evitar obstrucciones y prevenir colisiones. Sin embargo, el verdadero cerebro operacional reside en el software de planta.
Aunque en algunos casos, los vehículos automatizados no están conectados al software general de la planta sino más bien a disparadores entre operaciones específicas. Por ejemplo, una operación corriente abajo puede disparar un vehículo automatizado para que alimente piezas de trabajo en cierto momento.
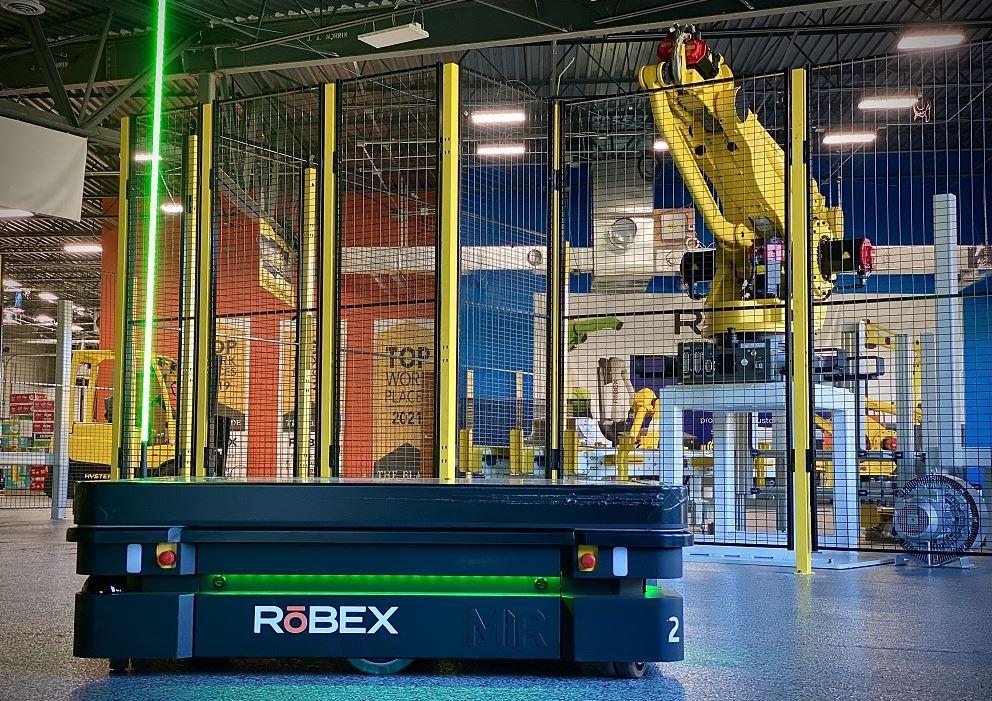
Un robot móvil autónomo no sólo puede transportar piezas de trabajo y herramientas de un punto a otro, sino que además interactúa con otros sistemas automatizados en la planta de producción. Robex
Kai Beckhaus, presidente de MCJ Supply Chain Solutions ubicada en Texas, el consorcio de automatización de Mitsubishi Logisnext Americas y el fabricante de AGV Jungheinrich, describió un escenario Kanban donde los operadores en la operación corriente abajo reducen partes hasta un cierto nivel (el nivel de “inventario de seguridad”). Luego, presionan un botón (o usan una tablet, si la aplicación requiere diferentes tipos de reabastecimiento) para indicarle a un AGV que alimente más partes. Este concepto podría aplicarse también de manera automatizada. Sensores en la ubicación de una tarima detectan cuando la tarima de existencias de reserva es removida, luego mandan una señal para que el AGV traiga más.
La solución conectada a MES ofrece una enorme posibilidad de agrandar la automatización móvil; y para los AMR que interactúan con máquinas a su alrededor, la conectividad y la interoperabilidad se han vuelto especialmente importantes. Los vehículos automatizados se comunican por Wi-Fi, pero el flujo de información digital que se envía a través del aire necesita traducirse; dicha automatización realmente no puede llevarse a cabo en un jardín amurallado.
Los fabricantes de vehículos automatizados buscan acuerdos con los fabricantes de máquinas. El fabricante de AGV Jungheinrich tiene un acuerdo con TRUMPF, por ejemplo, pero también tiene software middleware que puede comunicarse con diversos MES y sistemas de control de producción. “Los vendedores de vehículos automatizados ahora siguen las especificaciones del cliente”, dijo Beckhaus, “y no al revés”. Los gerentes de IT y operaciones de un fabricante no tienen que mover cielo y tierra para adaptarse a los requerimientos de conectividad de los vehículos automatizados.
En septiembre, FABTECH fue anfitrión de un panel de interoperabilidad entre varios fabricantes importantes y usuarios de AMR, incluyendo uno de los clientes más grandes de automatización móvil, FedEx. Aaron Prather, consejero principal, investigación técnica y planeación para FedEx, se enfoca en la integración de nuevas tecnologías en toda la empresa.
“Podría ser cualquier cosa desde robótica hasta etiquetas RFID”, dijo durante la discusión del panel. “Ponemos a prueba la tecnología y vemos si está lista para el uso de la empresa, y la interoperabilidad es clave. Cuando adquirimos nuevas tecnologías, necesitamos que todas funcionen en conjunto”.
“Se puede construir un robot móvil autónomo que puede hacer un tipo de cosa realmente bien”, dijo el panelista JasonWalker, director general/cofundador de Waypoint Robotics, una compañía establecida en Nashua, New Hampshire, que hace una variedad de AMRs para transportar herramientas y materiales, incluso en ambientes impredecibles de tráfico pesado. “Pero sin importar lo geniales que sean nuestros robots, éstos no tienen horquillas; nosotros nunca vamos a levantar una tarima. De manera similar, ese robot de tarimas nunca va a ser capaz de deslizarse hasta una máquina CNC y quitar algo de la misma. La razón de que se tengan todos estos factores de forma es que cada uno de éstos es difícil de hacer a un precio económico; todos éstos están hechos por arranques individuales. Así que si desea resolver todos los problemas en una planta, deseará mezclar y hermanar muchas compañías diferentes; tendrá una flota heterogénea”.
Waypoint Robotics de Walkers es parte de un grupo llamado MassRobotics, una organización sin fines de lucro que en 2021 emitió el estándar MassRobotics AMR Interoperability Standard. “Éste permite que nuestros robots estén en el mismo edificio, entiendan lo que están haciendo otros robots, eviten colisiones potenciales, unifiquen el flujo de tráfico, y esto establece el escenario para muchas otras posibilidades”.
Ochenta-veinte
Aunque el crecimiento de los AGV y AMR es más común en almacenamiento, distribución y ciertos ambientes de manufactura, éstos no han permeado la fabricación de metal en Estados Unidos, pero es probable que esto cambie pronto. Varios fabricantes de equipo original (OEM, por sus siglas en inglés) de corte láser, punzonadoras y prensas dobladoras han presentado sus modelos del taller de fabricación del futuro, mostrando la automatización móvil en las expos y probándola en salas de exhibición.
Actualmente, Smart Factory de TRUMPF en las afueras de Chicago tiene una flota de AGV Jungheinrich entregando y recogiendo piezas cortadas y partes formadas. Como lo explicó Kartik Iyer, director de Smart Factory de TRUMPF, como con la mayor parte de la fabricación de metal, la regla 80-20 es vigente con respecto a usar vehículos automatizados. “Evite emprender un proyecto pensando que va a automatizar todo, necesita usar la regla 80-20. Necesita encontrar las partes con alto volumen, que requieren transporte frecuente, y luego trate de crear un transporte autónomo para esas partes”.
Agregó que una característica importante que se debe considerar es el tamaño de una parte. “Mientras más grande sea la parte, más grande será el AGV que necesitará. Se necesita un pasillo más amplio, y las zonas de seguridad necesitan ser más grandes”.
Un AGV de Jungheinrich AGV transporta una tarima de partes formadas de una celda de doblado en Factory Smart de TRUMPF. MCJ Supply Chain Solutions
Las partes necesitan estar dentro de ciertos límites de longitud y anchura para caber sobre una tarima estándar, y los AGV pueden tener problemas cuando las partes sobresalen y quedan volando, interfiriendo potencialmente con los sensores láser del vehículo.
Por supuesto, los AGV vienen en todas las formas y tamaños, y algunos pueden manipular piezas de trabajo voluminosas, pero si un taller procesa esas piezas de trabajo grandes sólo ocasionalmente, incorporar un AGV así para manejar esos casos raros—e incorporar los pasillos amplios y otros elementos que requiere dicho arreglo—probablemente no tendría sentido.
“Trate de abordar problemas donde la solución tenga el máximo impacto”, dijo Lyer, “en lugar de intentar resolver cada problema en su taller”.
Como lo explicó Beckhaus de MCJ, una vez que un taller determina qué es lo que automatizará, necesita saber qué tipo de manejo de material requiere durante el tiempo de capacidad pico, así como la frecuencia de esos periodos de capacidad pico. La mayoría de los vehículos automatizados son cargados por batería, y éstos regresan automáticamente a sus estaciones de carga cuando no están en uso. Los periodos de demanda pico que ocurren sólo ocasionalmente, como una vez por semana o por turno, podrían requerir una cantidad de vehículos diferente a la de una operación con demanda pico que ocurre varias veces al día.
Otra estrategia general con respecto a los vehículos automatizados es evitar la complejidad reduciendo la variabilidad del proceso. Los AGV pueden tener toda clase de funciones, pero muchas de éstas puede que no se necesiten si el proceso es estable y las partes son exactas.
Por ejemplo, los AGV tienen sensores hidráulicos que podrían dar una estimación para el peso de una carga (para asegurar que la carga es segura de levantar), pero no es una báscula de precisión. Teóricamente, un AGV podría incluir una báscula de ese tipo para pesar la carga sobre la tarima que está transportando, luego reportar al MES diciendo que falta el peso de cierto lote, lo que significa que esas partes podrían faltar.
La cuestión es que toda esta capacidad crea una solución reactiva tipo “curita” que no llega a la raíz del problema. La consistencia del proceso corriente arriba, ya sea mediante apilamiento automatizado de partes u otras medidas de control de proceso, todas manejadas por software de control de producción y la infraestructura IT, podría ser la mejor estrategia. Si entra basura, sale basura; la solución duradera no es agarrar y quitar la basura, sino evitar que se produzca basura en primera instancia.
Un pensamiento similar se aplica para la identificación de tareas en la planta de producción. Como lo describió Beckhaus, algunas aplicaciones de manufactura usan identificación pasiva de tarimas. Aunque las tareas individuales sobre la tarima tienen etiquetas de trabajo con códigos de barras o QR, la tarima en sí no tiene código de identificación de barras. Eso se debe a que en una situación dada, el AGV—que recibe instrucciones del MES—sólo tiene una tarima que traer. “Usted sabe dónde está la tarima, y el AGV recibe la instrucción de llevar la tarima de A a B. Debido a que sólo se produjo una tarima de partes, sólo hay una tarima, por lo que no puede haber mezcla”. Esto ejemplifica la ventaja del flujo de partes de una sola pieza (o en chapa metálica, una sola tarima). Entre menos piezas en proceso (WIP, por sus siglas en inglés) tenga una operación, más fácil será de identificar esa pieza en proceso.
Por supuesto, algunas operaciones podrían requerir un acomodo más completo. En este caso, Beckhaus dijo que los AGV pueden trabajar en conjunto con escáneres de código de barras o RFID. “Pero repito, usted nunca querrá sobrecargar una aplicación así. Si un sistema IT le da suficiente seguridad de éxito, debería seguir con él, debido a que cuando aumenta la complejidad, agrega causas potenciales de falla”.
Primeros pasos
Lo primero es una buena limpieza del lugar. Idealmente, los pasillos deben estar bien definidos, libres de desperdicios y limpios. El piso no necesita ser perfecto ni completamente libre de grietas, pero al menos debe ser suficientemente aceptable, y definitivamente, no debe estar lleno de tarimas vacías. Si los AGV necesitan llevar material de los racks, los racks en sí necesitan estar en una posición consistente; un pandeo excesivo de ciertos travesaños de un rack bajo carga podría causar un problema. “Necesita construir un ambiente confiable para asegurar una automatización de AGV confiable”, dijo Beckhaus.
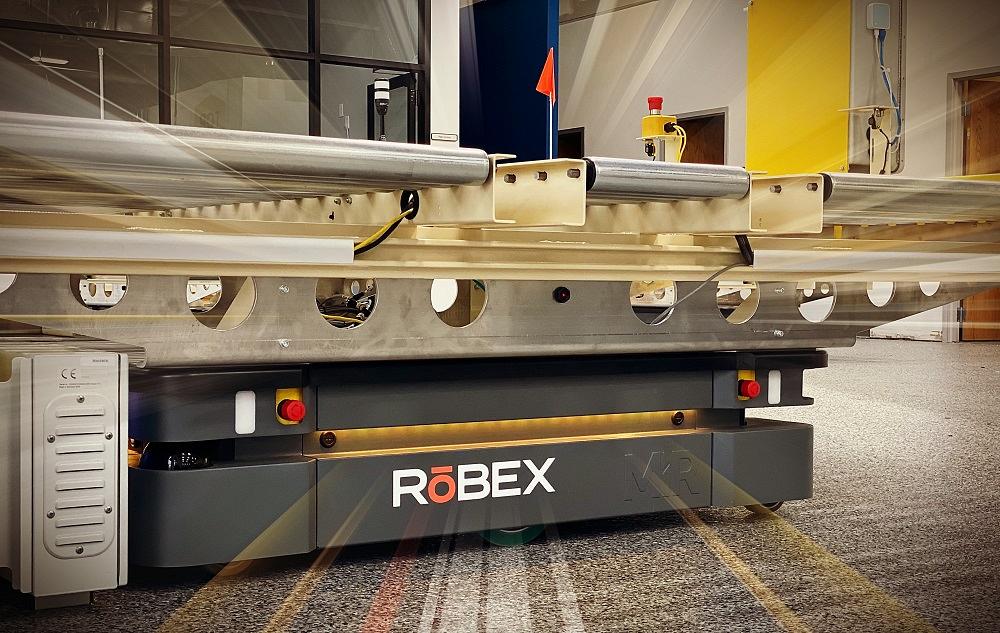
Este módulo superior AMR crea una banda transportadora móvil. El AMR con una parte o caja encima se coloca cerca de un punto de alimentación, y la banda transportadora automáticamente descarga la pieza de trabajo que lleva. Robex
Los AMR también usan sensores y, por lo tanto, necesitan un piso razonablemente liso. “Se necesita un piso más o menos liso”, dijo Cal Bowers, vicepresidente de crecimiento de Robex. “Los sensores pueden estropearse si el AMR pasa por una superficie muy rugosa, por lo que nosotros sí vemos los pisos durante una visita inicial al sitio”.
Beckhaus agregó que algunos ambientes sumamente polvosos podrían no ser adecuados para un AGV, principalmente debido a que el aire sucio puede obstruir los sensores del vehículo. Sin embargo, los ambientes de chapa metálica de precisión con una ventilación y extracción de polvo adecuadas deben de ser perfectamente adecuados para los vehículos automatizados. Cuando el polvo cubre los sensores de un vehículo, éste no puede “ver” y entonces simplemente se detiene. En el peor de los casos, alguien podría tener que limpiar periódicamente los sensores del vehículo con un paño limpio.
Otro paso inicial hacia la automatización móvil es establecer la unidad de carga—en el contexto de un taller de chapa metálica, esto sería la tarima sobre la que están las piezas de trabajo. “Nos interesa la unidad de carga”, dijo Beckhaus, “pero no nos interesa lo que hay sobre ésta. El vehículo toma una unidad de carga y la lleva de A a B, como se le instruyó”.
La carga no puede exceder un peso máximo. Además, la carga no puede estar tan descentrada como para hacer que el vehículo se vuelque en tránsito. La carga no debe tener partes sueltas que pudieran resbalarse en tránsito. Y la pieza de trabajo en sí no puede sobresalir de la tarima de manera imprevista interfiriendo con los sistemas de seguridad del vehículo. Como explicó Beckhaus, los AGV pueden lidiar con ciertas salientes de partes, pero “éstas necesitan estar definidas y hay ciertos límites. Una parte muy larga con una saliente excesiva es probable que no sea factible, pero puede funcionar una saliente menos grande”.
Esa saliente sólo necesita definirse en el sistema de seguridad del vehículo para que los anchos de pasillo sean suficientes para que el vehículo viaje y ejecute vueltas con el radio adecuado. La saliente no debe chocar con objetos, o especialmente con personas. Como lo explicó Beckhaus, la limitación de la saliente con frecuencia es la razón de que el manejo de material inicial—descarga de camión, transporte de materia prima—siga siendo manual. El manejo por vehículos automatizados ocurre corriente abajo.
Beckhaus agregó que todo lo relacionado con la seguridad “tiene que tener redundancia en un ambiente AGV”. Los sensores pueden fallar, por lo que los respaldos deben estar ahí para asegurar que tanto el vehículo automatizado como la carga que lleva no causen daño.
Ésta es la razón de que la consistencia y la simplicidad del proceso sean tan importantes. Entre menos predecible sea un proceso, más sensores puede requerir, y si esos sensores se aplican en situaciones relacionadas con la seguridad, necesitarán redundancias integradas. Siempre es mejor “eliminar” la condición insegura para que el riesgo no ocurra en primera instancia.
Optimización de los procesos indirectos
La automatización móvil abre la puerta a todo tipo de maneras de optimizar el flujo de partes. Los desarrollos emergentes en inteligencia artificial y aprendizaje de máquinas ofrecen nuevas posibilidades en cuanto a cómo interactúa la automatización móvil y cómo aprende del ambiente que la rodea. Sin embargo, en el corto plazo, automatizar el acto de mover tarimas de partes de una estación de trabajo a otra podría dar un respiro a una industria que no puede encontrar suficientes choferes de montacargas y otros manejadores de material.
Como lo dijo Lyer, la meta es optimizar los procesos indirectos. “Éstos son las latencias ocultas que están integradas en la producción, donde hacer máquinas más rápidas no sería la solución”.
En resumen, dijo, sólo alrededor del 20% de la fabricación de metal implica procesamiento directo—corte láser, doblado, soldadura—y alrededor de 80% de los procesos en la fabricación de metal son indirectos. “Y el manejo de material es una buena parte de eso”.
About the Author
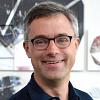
Tim Heston
2135 Point Blvd
Elgin, IL 60123
815-381-1314
Tim Heston, The Fabricator's senior editor, has covered the metal fabrication industry since 1998, starting his career at the American Welding Society's Welding Journal. Since then he has covered the full range of metal fabrication processes, from stamping, bending, and cutting to grinding and polishing. He joined The Fabricator's staff in October 2007.
About the Publication
Compañías Relacionadas
subscribe now
FMA Communications ha introducido al mercado la edición en Español de la revista The Fabricator. Esta versión consiste del mismo tipo de artículos técnicos y sección de lanzamientos de nuevos productos que actualmente presentan el personal de primera categoría de Fabricator en Inglés.
start your free subscription- Podcasting
- Podcast:
- The Fabricator Podcast
- Published:
- 04/30/2024
- Running Time:
- 53:00
Seth Feldman of Iowa-based Wertzbaugher Services joins The Fabricator Podcast to offer his take as a Gen Zer...
- Trending Articles
Los operadores de prensa dobladora inexpertos hacen indispensable el repensar la seguridad
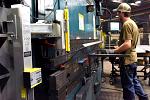
Prescripción para la reducción del desperdicio: arreglo esbelto de las instalaciones
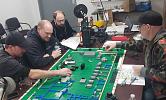
Máquina de corte por láser diseñada para el mercado mexicano
La sierra de doble carro sigue los contornos del tubo perfectamente
La máquina procesadora de placas crea biseles complejos en un solo corte
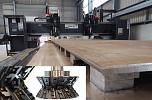
- Industry Events
Pipe and Tube Conference
- May 21 - 22, 2024
- Omaha, NE
World-Class Roll Forming Workshop
- June 5 - 6, 2024
- Louisville, KY
Advanced Laser Application Workshop
- June 25 - 27, 2024
- Novi, MI
Precision Press Brake Certificate Course
- July 31 - August 1, 2024
- Elgin,