Senior Editor
- FMA
- The Fabricator
- FABTECH
- Canadian Metalworking
Categories
- Additive Manufacturing
- Aluminum Welding
- Arc Welding
- Assembly and Joining
- Automation and Robotics
- Bending and Forming
- Consumables
- Cutting and Weld Prep
- Electric Vehicles
- En Español
- Finishing
- Hydroforming
- Laser Cutting
- Laser Welding
- Machining
- Manufacturing Software
- Materials Handling
- Metals/Materials
- Oxyfuel Cutting
- Plasma Cutting
- Power Tools
- Punching and Other Holemaking
- Roll Forming
- Safety
- Sawing
- Shearing
- Shop Management
- Testing and Measuring
- Tube and Pipe Fabrication
- Tube and Pipe Production
- Waterjet Cutting
Industry Directory
Webcasts
Podcasts
FAB 40
Advertise
Subscribe
Account Login
Search
Cuando un robot de soldadura tiene un cerebro
El potencial de la soldadura autónoma en el taller de fabricación
- By Tim Heston
- June 20, 2022
- Article
- Automation and Robotics
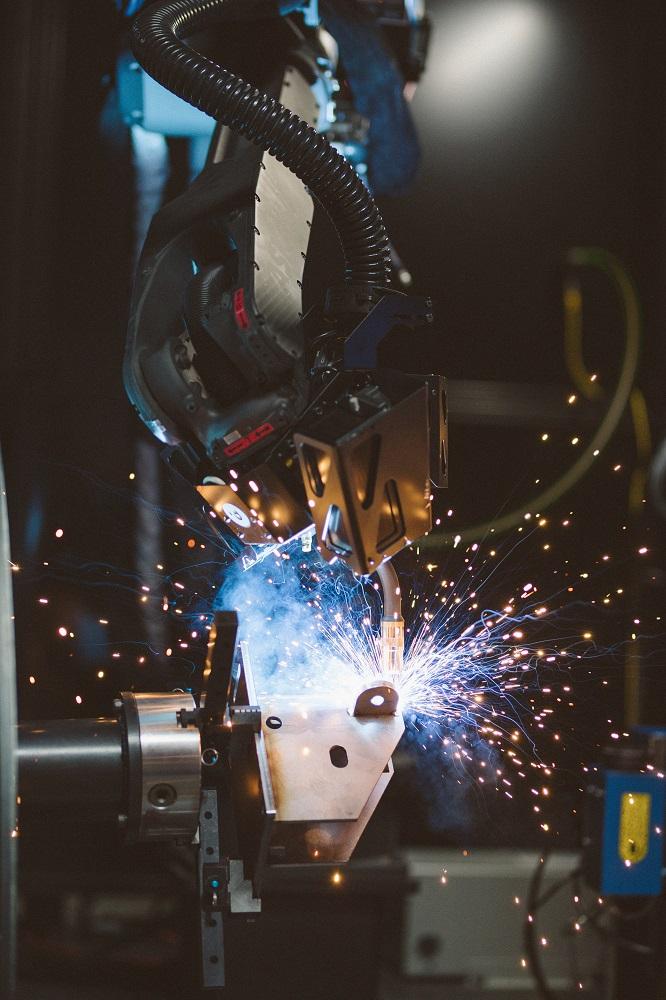
Después de escanear una pieza de trabajo y compararla con el modelo CAD con datos de soldadura embebidos, un robot comienza a soldar—sin requerir dispositivo colgante de enseñanza, ni programación fuera de línea ni enseñanza cinética. Path Robotics
Un soldador capacitado puede ver un dibujo, revisar un procedimiento de soldadura, fijar una parte y empezar a soldar. No ocurre así con un robot, al menos no tradicionalmente.
Históricamente, una combinación de personas, hardware y software le ha enseñado al robot qué hacer, usualmente con un operador usando un dispositivo colgante de enseñanza. Todo esto merma el tiempo productivo de un robot. La enseñanza puede ocurrir de manera cinética, con el operador moviendo el brazo de robot a lo largo de una trayectoria en particular. Esto incluso podría hacerse mediante interfaces de programación simplificada que están proliferando entre las celdas de cobots de soldadura.
Otra opción implica la simulación y la programación fuera de línea. Esto con frecuencia viene con representaciones digitales del robot, de las fijaciones, de la parte en sí, e incluso de componentes secundarios alrededor de la celda, todo esto para evitar colisiones y verificar el proceso.
Todo esto reduce el trabajo en la planta de producción a unos cuantos retoques de la programación (en el peor de los casos). Aun así, alguien tiene que desarrollar la fijación y ejecutar el programa fuera de línea. Los humanos y el software siguen efectuando la enseñanza, ya sea fuera de línea en la oficina o en la planta de producción. Eso ocupa tiempo y recursos de programación. Un robot no puede simplemente “ver” una parte y empezar a soldar—una limitación que ha evitado que la robótica se cuele en el concepto “long tail” (larga cola) de la producción no serial altamente mezclada y en bajos volúmenes.
Eso podría estar por cambiar. Los avances en visión, software y aprendizaje de máquina están construyendo la base para un nuevo tipo de robot de manufactura—uno con cerebro.
Ver, luego hacer
El sector de la fabricación de metal ha visto surgir algunas tecnologías que pueden ayudar a los robots a ver, y luego hacer. Omnirobotic, con sede cerca de Montreal, implementó robots y cobots de auto-aprendizaje para recubrimiento de polvo y aplicaciones similares. En Suecia, OpiFlex desarrolló robots móviles flexibles que pueden ser entrenados para “ver” un trabajo específico en una máquina específica—ya sea una prensa dobladora, una dobladora de panel, un centro de maquinado, una estampadora o cualquier otra cosa—y saber qué hacer después.
Los enfoques específicos difieren, pero en general, dicha automatización recibe una especie de “entrenamiento robótico” que rige la manera en que interactúa el robot con la realidad. Entonces, cuando el robot “ve” una parte colgando en una línea de recubrimiento de polvo, de una manera específica, con una orientación específica y a una velocidad específica, sabe moverse y asperjar de cierta manera.
Algunas compañías han ahondado en la búsqueda de soluciones similares para la soldadura robótica, y en los últimos años varias organizaciones han llevado sus tecnologías al mercado. A juzgar por su éxito inicial, el panorama de la soldadura robótica podría verse bastante diferente en los próximos años.
Aprendizaje acelerado
Andy y Alex Lonsberry crecieron cerca del taller de fabricación de motocicletas personalizadas de sus padres. Los hermanos aprendieron a soldar a temprana edad, pero en lugar de entrar al negocio familiar, los dos acabaron en la academia. Los hermanos originarios de Ohio obtuvieron sus títulos en la Universidad Case-Western Reserve. Alex se enfocó en neurociencias computacionales, Andy en aprendizaje de máquinas para robots andantes bípedos.
“Nos enfocamos en hacer que los sistemas aprendan como lo hacen los humanos”, dijo Andy, y agregó que su trabajo los llevó a que ambos iniciaran una compañía consultora. “El único propósito de esa compañía era ir y encontrar un punto problemático del mercado”.
Dos robots de soldadura trabajan en colaboración para soldar una pieza de trabajo grande. Están extrayendo datos directamente del archivo CAD y de la información embebida en éste. Abagy Robotic Systems Inc.
Con el tiempo los dos nos reunimos con algunos gerentes de ingeniería en una fábrica de mofles para discutir un asunto que nada tenía que ver con la soldadura. Como recordó Andy, “a media reunión, el presidente de la compañía entró al salón y dijo ‘hablemos de soldadura’. Dijo que varios de sus soldadores estaban envejeciendo, y estaban batallando para reclutar nuevos. Esto les impedía agrandar la compañía.
“Eran una fábrica de alta mezcla y bajos volúmenes con alrededor de 3,000 unidades de mantenimiento en almacén (SKU, por sus siglas en inglés), y producían tamaños de lote de 5 y 10. Estaban considerando diversas opciones, que incluían mandar a hacer externamente. Sin embargo, eran una compañía “hecho en América”; no querían perder reconocimiento de marca; y les preocupaba perder calidad. “Además, la compañía no quería mantener millones de dólares en inventario. “Eran un negocio de flujo de efectivo; querían recibir un pedido, hacerlo y embarcarlo”.
El fabricante había intentado la soldadura robótica, pero no era práctico construir fijaciones a la medida para tantas variaciones de partes. Las tolerancias de partes también eran un problema, y debido a que las partes se hacían con acero inoxidable delgado, los parámetros de soldadura eran críticos.
“En resumen”, dijo Andy, “nunca iban a poder hacer que funcionara, entonces la compañía acudió a nosotros con una idea. ‘Apreciamos a los soldadores humanos; queremos más pero al parecer no podemos encontrarlos. Estamos intentando agrandar esta compañía. ¿Hay alguna manera de que tomen este brazo robótico y le den ojos y un cerebro?
Después de diseñar muchas interacciones, los hermanos hicieron justo eso, y en 2018 los dos formaron Path Robotics, con sede en Columbus, Ohio. La compañía ha estado vendiendo sus sistemas bajo un modelo de automatización como un servicio. Path conserva la propiedad del equipo mientras que el fabricante le paga a Path una cuota mensual establecida, todo con base en ciertas garantías de productividad y calidad.
Actualmente, un operador de una celda Path, que usa sujeciones sencillas de palanca y otros elementos comerciales, puede fijar una parte en cualquier sitio y en cualquier orientación en una mesa de soldadura. La ubicación exacta no importa siempre y cuando el robot pueda acceder físicamente a la unión de soldadura.
Los sensores del sistema escanean el área, luego comparan lo que ven con la información embebida en el archivo CAD. El archivo CAD puede incluir infinidad de puntos de datos de soldadura, incluidos aquéllos que siguen instrucciones detalladas por la especificación del procedimiento de soldadura (WPS, por sus siglas en inglés). Sin embargo, la información de soldadura en el archivo CAD puede ser mínima también. Como mínimo, el archivo necesita especificar el tamaño de la soldadura y si la soldadura será por tramos o continua.
La tecnología se deriva de la investigación de los hermanos. “Se trata de máquinas capaces de evaluar los datos que se les dan, y que les permiten explorar al interior de su ambiente, conectando patrones entre lo que es bueno y lo que es malo con base en su propia exploración”.
De manera muy simplificada, su investigación tiene que ver con una manera para que los robots y otra automatización “aprendan” sin requerir un conjunto muy grande de datos. Los enfoques tradicionales en el aprendizaje de máquinas y en la inteligencia artificial mejoran con el tiempo mediante la extracción de enormes cantidades de datos. Es así como su teléfono inteligente parece volverse más inteligente cada año. Los métodos de aprendizaje empleados por Path ciertamente pueden beneficiarse de todos los datos relacionados que puedan obtener, pero no lo requieren.
“En realidad es la única manera de hacer el tipo de aprendizaje de máquina que necesitamos para trabajar en un ambiente de soldadura”, dijo Andy. “Necesitamos poder aportar valor con conjuntos pequeños de datos”.
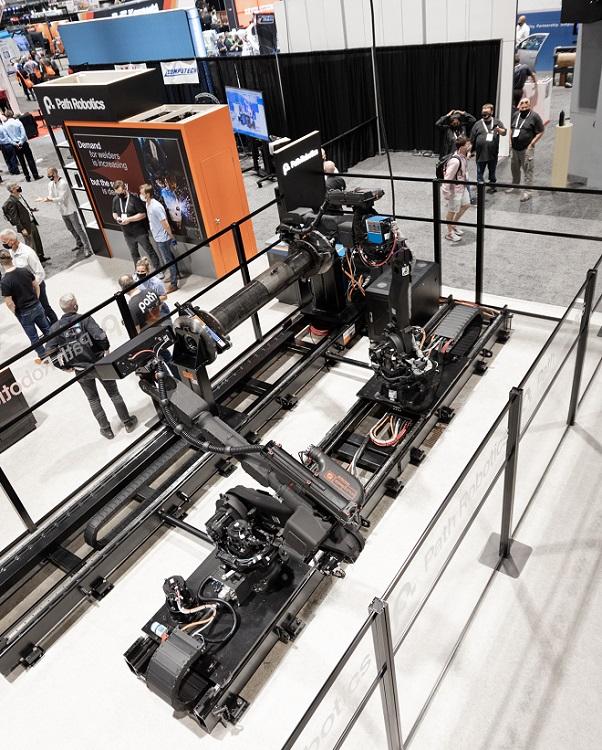
Path Robotics demuestra sus sistemas de visión y soldadura en la FABTECH 2021, realizada en noviembre, en Chicago.
Path usa su propia tecnología de visión, de detección y de software que permite al robot ver y evaluar el reto de soldadura fijo frente a él. Los sensores realimentan datos durante la soldadura y ven la geometría de la pieza de trabajo justo antes del arco, para compensar la variabilidad del empate. Aun cuando los detalles son patentados, de acuerdo con Andy “hemos podido correlacionar lo que está pasando en tiempo real con lo que acaba de pasar unos momentos antes, para determinar la penetración real de soldadura, sin tener que cortar una muestra ni hacer pruebas ultrasónicas”. Agregó que la tecnología no elimina la necesidad de ensayos destructivos y no destructivos para las soldaduras que lo requieran. Sin embargo, la tecnología de inspección agrega un nivel de seguridad cuando se trata de asegurar alta calidad y penetración adecuada de la soldadura.
Path además usa tecnología de relleno adaptiva, la cual puede ayudar en la soldadura de pasadas múltiples. El calor inadecuado en una pasada de raíz puede evitar buenas características de humectación (cómo el metal fundido fluye y se funde con la raíz y paredes laterales de la soldadura), lo cual a su vez perturba los parámetros de soldadura en pasadas posteriores. “Adaptamos sobre la marcha para asegurarnos de que eso no ocurra”, dijo Andy.
La tecnología también compensa el encogimiento de la soldadura, viendo la geometría de la pieza de trabajo justo antes del arco de soldadura, y luego ajustando los parámetros para que concuerden. “Si vemos encogimiento, lo vemos sobre la marcha”, dijo Andy, y agregó que entran en escena los datos de visión así como la información embebida en el modelo CAD”.
Andy explicó que dicha adaptación funciona dentro de las restricciones de la especificación WPS, que son especialmente críticas para el trabajo a nivel código en la soldadura estructural. En muchos casos, la especificación WPS rige la técnica (cordón angosto contra zig-zag, por ejemplo), el viaje y otras características. “Extrayendo información de aquí, el sistema toma decisiones con base en la especificación WPS; y esto puede variar de una aplicación a otra y de una compañía a otra”.
Sujetar y continuar
Alexander Domanitskiy, vicepresidente de desarrollo de estrategias y negocios en Abagy Robotic Systems, con sede en Los Ángeles, mostró un video de un técnico que fijaba una pieza de trabajo en una celda de robot usando palancas y topes sencillos, asegurando la parte en una ubicación arbitraria. Luego el técnico salió de la celda a una estación de trabajo de computadora y vio un modelo 3D CAD. El modelo incluía sólo datos de la parte y de la soldadura—no había modelos de sujeciones, topes ni otras fijaciones.
La celda robótica de soldadura por arco de metal protegido con gas tiene un sistema de visión que hace varios escaneos, después de lo cual aparece una “nube de puntos” rojos en la pantalla de la computadora. El sistema puede hacer coincidir los datos de la nube de puntos con el modelo 3D, entender la diferencia, y ser capaz de planear la trayectoria para la pieza de trabajo real, no para el modelo 3D teórico.
En ese punto, el sistema compensa todo problema de acceso a la soldadura; en el video, el técnico monitorea el sistema mientras éste ajusta la trayectoria del robot para adaptarse a una sujeción. “En épocas pasadas, se desarrollaba una celda para una parte, para un código de artículo SKU o quizás para una familia de productos en particular”, dijo Domanitskiy, “y todo requería herramental complicado. Ahora, estamos cambiando a un concepto diferente que implica analizar el volumen de una zona de trabajo. Cualquier cosa que quepa en ese espacio puede soldarse. Siempre que el robot pueda llegar físicamente, éste puede soldar; no necesita fijaciones especiales ni modelos 3D de esas fijaciones.
Con instalaciones y equipos de soporte en Europa y Estados Unidos (con una oficina a las afueras de Houston), las raíces de Abagy se remontan a un fabricante global de exhibidores con sede en Rusia. “El fundador tenía una planta de producción de alrededor de 200 personas, todas trabajando tanto en metal como en madera, y se sorprendió mucho cuando se dio cuenta de que cuando se necesita producir un lote de una pieza, realmente no había manera de usar un robot”, dijo Domanitskiy. “Se comprometió a resolver ese problema hace cuatro años y medio. Nuestra primera instalación comercial fue en febrero de 2020”.
El enfoque de Abagy incluye software patentado que se implementa usando una combinación de procesamiento local (on-premise) y procesamiento basado en nube. La nube hace los cálculos y la planeación pesada, mientras que el software local maneja la celda robótica. “Sin embargo, si el fabricante lo requiere podemos crear una solución local (on-premise)”, dijo Domanitskiy.
El software trabaja con diversos sistemas existentes robóticos y de visión. “Somos bastante neutrales cuando se trata de hardware”, dijo Domanitskiy. Trabajamos con las principales marcas de robots y diversos fabricantes de fuentes de poder para soldadura, incluidos los principales. Y trabajamos con diversos sistemas de visión, dependiendo de la aplicación”.
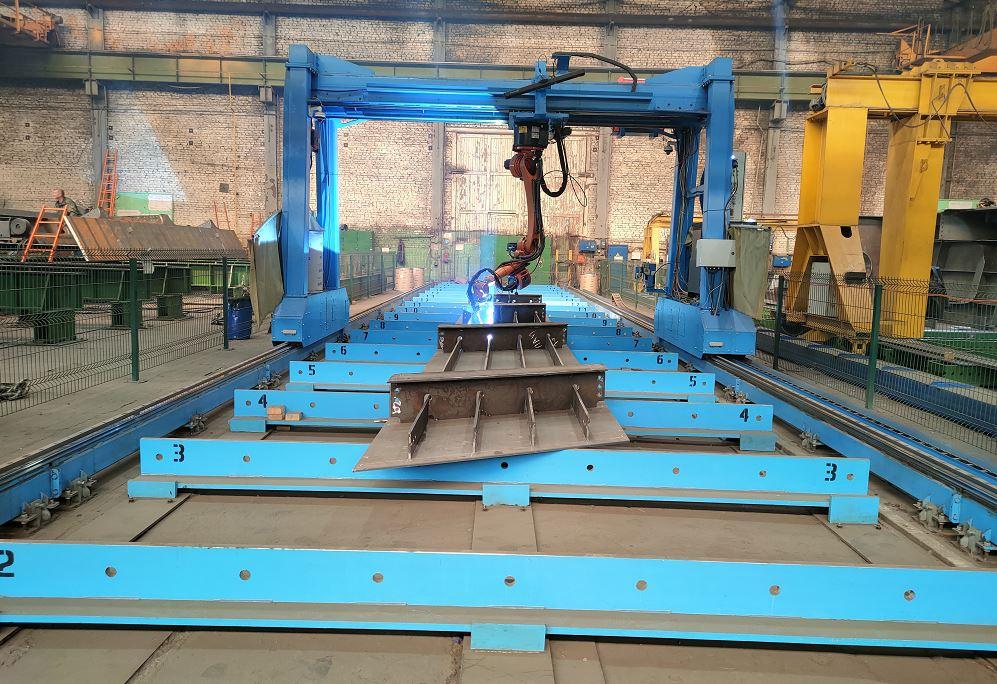
Un robot de soldadura suspendido en una grúa de pórtico móvil suelda una pieza de trabajo grande. Abagy Robotic Systems Inc.
Agregó que los sistemas de la compañía han sido implementados en diversos tamaños de partes, incluidos trabajos que implican placas y vigas estructurales grandes, usando uno o varios robots. La tecnología funciona con configuraciones de varios robots de soldadura en diversos modos. Un modo es configurar dos celdas de soldadura virtuales, con cada robot trabajando en tareas específicas; otra opción implica configurar la celda para que los dos robots puedan trabajar colaborativamente.
“Dos robots pueden trabajar uno al lado del otro, y podemos verificar las conexiones entre éstos para hacer una operación colaborativa”, dijo Domanitskiy. “Imagine que un robot se queda sin alambre. En ese caso, podemos redistribuir automáticamente algunas de las tareas de soldadura al otro robot”.
Agregó que el software puede trabajar con robots que se mueven junto con grúas de pórtico y posicionadores. “Básicamente no tenemos límite en el número de ejes que podemos soportar, y usamos un gemelo digital para hacer toda la planeación de trayectoria, para verificar colisiones y singularidades. Siempre que permitimos al operador presionar el botón para ejecutar el trabajo, ya lo probamos con el gemelo digital”.
Como lo explicó Domanitskiy, el sistema además detecta encogimiento de soldadura y hace ajustes en tiempo real. “Cuando hacemos la soldadura, sabemos exactamente dónde debe estar la punta del alambre. Cuando tenemos calor distribuyéndose a lo largo de la trayectoria, entonces sabemos que vamos a sufrir algunas distorsiones en términos de la geometría de parte. Así que corregimos continuamente la posición de la punta del alambre para ajustar la geometría de la costura.
¿Un futuro autónomo?
La percepción popular es que los robots están en todos lados en la manufactura. Sin embargo, toda persona que trabaje en una planta de producción—especialmente en fabricación de metal—sabe que eso no es verdad.
Los fabricantes trabajan con integradores para desarrollar automatización robótica en torno a productos específicos con demanda previsible. Sin embargo, la mayor parte del trabajo fluye como siempre lo ha hecho, desde el corte al doblado, hasta la soldadura manual.
En 2022 la industria puede mostrar los inicios de un cambio gradual de la marea, donde la automatización autónoma haga práctica a la robótica, no sólo para flujo de valor o familia de un producto, sino para casi cualquier sitio en la planta de producción. Cuando los robots tienen un cerebro, su potencial crece.
About the Author
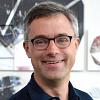
Tim Heston
2135 Point Blvd
Elgin, IL 60123
815-381-1314
Tim Heston, The Fabricator's senior editor, has covered the metal fabrication industry since 1998, starting his career at the American Welding Society's Welding Journal. Since then he has covered the full range of metal fabrication processes, from stamping, bending, and cutting to grinding and polishing. He joined The Fabricator's staff in October 2007.
About the Publication
subscribe now
FMA Communications ha introducido al mercado la edición en Español de la revista The Fabricator. Esta versión consiste del mismo tipo de artículos técnicos y sección de lanzamientos de nuevos productos que actualmente presentan el personal de primera categoría de Fabricator en Inglés.
start your free subscription- Podcasting
- Podcast:
- The Fabricator Podcast
- Published:
- 05/07/2024
- Running Time:
- 67:38
Patrick Brunken, VP of Addison Machine Engineering, joins The Fabricator Podcast to talk about the tube and pipe...
- Trending Articles
Prescripción para la reducción del desperdicio: arreglo esbelto de las instalaciones
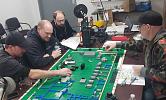
Anidado para la estabilidad del corte láser
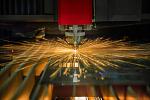
La máquina procesadora de placas crea biseles complejos en un solo corte
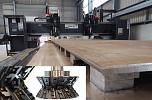
El software guía a los soldadores a través de instrucciones de trabajo
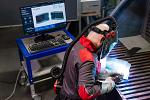
Seguridad en la soldadura desde el inicio
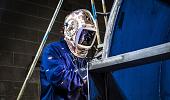
- Industry Events
World-Class Roll Forming Workshop
- June 5 - 6, 2024
- Louisville, KY
Advanced Laser Application Workshop
- June 25 - 27, 2024
- Novi, MI
Precision Press Brake Certificate Course
- July 31 - August 1, 2024
- Elgin,