Senior Editor
- FMA
- The Fabricator
- FABTECH
- Canadian Metalworking
Categories
- Additive Manufacturing
- Aluminum Welding
- Arc Welding
- Assembly and Joining
- Automation and Robotics
- Bending and Forming
- Consumables
- Cutting and Weld Prep
- Electric Vehicles
- En Español
- Finishing
- Hydroforming
- Laser Cutting
- Laser Welding
- Machining
- Manufacturing Software
- Materials Handling
- Metals/Materials
- Oxyfuel Cutting
- Plasma Cutting
- Power Tools
- Punching and Other Holemaking
- Roll Forming
- Safety
- Sawing
- Shearing
- Shop Management
- Testing and Measuring
- Tube and Pipe Fabrication
- Tube and Pipe Production
- Waterjet Cutting
Industry Directory
Webcasts
Podcasts
FAB 40
Advertise
Subscribe
Account Login
Search
El potencial de los robots móviles flexibles en la fabricación de chapa
Cómo los robots en movimiento crean capacidad flexible
- By Tim Heston
- March 16, 2022
- Article
- Automation and Robotics
Los robots móviles flexibles se pueden mover con gatos hidráulicos, montacargas o carros guiados automatizados con horquillas. Después del acoplamiento, el brazo vertical naranja, que tiene un escáner de área de seguridad en el extremo, se dobla y se extiende. Un brazo idéntico está montado detrás del robot. Crédito de la foto: OpiFlex y SICK
En un laboratorio de la Universidad de Skövde, una pequeña ciudad en el centro-sur de Suecia, Anna Syberfeldt habló e hizo un gesto a un robot cerca de ella. El robot hizo lo que ella le dijo transportando un objeto de cierta manera y orientación, transportándolo a una velocidad específica y en un camino específico. La investigación de la profesora de ingeniería de producción se centra en la interacción entre humanos y la automatización.
“Estamos desarrollando soluciones robóticas que pueden interactuar con los humanos de manera eficiente”, dijo, “y también de una manera que los humanos puedan entender. Los humanos nos comunicamos mediante la voz y los gestos y queremos hacer lo mismo con los robots".
A varias horas de viaje hacia el noroeste, más cerca de Estocolmo, Johan Frisk se paró cerca de un robot que operaba una prensa dobladora. En lugar de vallas de seguridad, el sistema utilizó escáneres de área junto con software para brindar la protección.
Frisk estaba monitoreando lo que llamó un robot móvil flexible (FMR). No es un cobot, sino que utiliza un brazo articulado tradicional capaz de transportar cargas útiles completas a toda velocidad. Como dijo Frisk, "son robots coexistentes, no robots colaborativos".
Una vez que se termina el lote, el operador mueve el sistema a otra prensa dobladora, una dobladora de paneles, una prensa estampadora o muchas otras máquinas. Todas pueden operarse manualmente o con un FMR. Una prensa dobladora puede tener a alguien ejecutando manualmente un trabajo, mientras que una dobladora adyacente puede estar trabajando un lote con un FMR.
Frisk es director ejecutivo de OpiFlex, una empresa sueca que fundó en 2013 con el objetivo de asumir los desafíos de automatización en las operaciones de mezcla alta/bajo volumen de las pequeñas y medianas empresas (PYMEs), que en conjunto constituyen la mayor parte de la fabricación mundial. Syberfeldt y Frisk han trabajado juntos en varios entornos industriales y de laboratorio y ambos hablan de un futuro de robótica industrial con límites físicos y comunicativos mucho menos restrictivos. Salvaguardar la innovación ha reducido esas barreras físicas y, en lugar de programar, las personas "entrenarán" a los robots para que trabajen con ciertas máquinas y sistemas. Después del entrenamiento un robot podrá "ver" una máquina, recibir un trabajo del sistema de ejecución de fabricación (MES) o un software similar, programarse y comenzar el trabajo.
Su visión se refleja en un documento presentado en la Conferencia Internacional IEEE/RSJ de 2016 sobre Robots y Sistemas Inteligentes, titulado "Cuarta Revolución Robótica", por los autores Dominik Boesl en la Universidad Técnica de Munich y Bernd Liepert con KUKA y euRobotics. “Durante mucho tiempo la automatización estuvo impulsada por sistemas que estaban programados, línea por línea, para repetir tareas más o menos complejas con la mayor velocidad y exactitud. Desafortunadamente, esta optimización unilateral les impidió convertirse en herramientas flexibles y versátiles. Por lo tanto, el deseo de tener robots perceptivos y cognitivos es obvio. Las máquinas deben entender lo que sus usuarios y operadores quieren hacer, en lugar de estar programadas para repetir tareas básicas. Algún día seremos capaces de idear sistemas que entiendan lo que queremos que hagan y, tal vez hasta aprender como un aprendiz de robot”.
Todavía no estamos allí. Aun así, a juzgar por los FMR que operan actualmente en los talleres de chapa europeos y el trabajo realizado por Syberfeldt y otros investigadores, hemos recorrido un largo camino en los últimos años. Los FMR están fuera del laboratorio y ahora funcionan en la industria. Varias operaciones de chapa en Europa han estado operando con FMR durante varios años. OpiFlex también tiene socios en América del Norte y espera comenzar a mudarse a Estados Unidos en algún momento de 2022.
Según Frisk, todo este progreso en FMR fue posible al comenzar con una de las operaciones más complejas que realiza la robótica: doblar piezas de chapa en la prensa dobladora.
Comience con lo más complicado
Poco después de su lanzamiento en 2013, la organización de Frisk completó un estudio de mercado. Después de pasar años en la industria de la robótica en ABB y en otros lugares, Frisk quería saber por qué tan pocos fabricantes pequeños usaban robots. Fuera de la industria automotriz, la manufactura tiene menos de 10 robots por cada 10,000 empleados, dijo Frisk. Agregó que, en la industria automotriz, que con frecuencia se considera una de las industrias más robotizadas, la proporción es de aproximadamente 1300 robots por cada 10 000 empleados.
El estudio encontró que el desafío se reducía a la flexibilidad y la capacidad de seguir las restricciones de fabricación. Una celda de corte o doblado altamente automatizada puede hacer maravillas en términos de rendimiento, pero solo si los procesos posteriores pueden seguir el ritmo. Y como cualquier persona que trabaje en un taller de fabricación de metales sabe, las restricciones se mueven según la combinación de demanda y productos.
El estudio reveló una lista de deseos de las tiendas de fabricación típicas y otras PYMEs. Primero, querían que la programación de robots fuera más intuitiva y rápida. En segundo lugar, necesitaban protección sin cercas mientras trabajaban con brazos robóticos que pudieran operar a toda velocidad y con cargas útiles. En tercer lugar, querían poder mover el robot donde fuera necesario, "desacoplando" efectivamente el robot de la dobladora, paneladora, estampadora, centro de maquinado o cualquier otra máquina en el piso. Durante un turno, una máquina puede alternar entre operación manual y robótica. Teniendo en cuenta todo esto, el equipo de Frisk comenzó con lo que sigue siendo el área más complicada en la fabricación de metales: el departamento de prensas dobladoras.
“Automatizar la formación de láminas de metal es mucho más difícil que otros procesos, como la atención de máquinas en el mecanizado”, dijo Frisk. "Así que preguntamos, '¿Por qué no comenzar con lo más complicado?' De esa manera todo lo demás será relativamente fácil".
Una prensa dobladora pone a prueba a un robot, exigiendo que manipule las láminas de múltiples maneras, que siga las bridas hacia arriba durante el ciclo de doblado, reposicione su pinza y luego apile el trabajo de manera segura y confiable en una tarima. El equipo de Frisk tuvo como objetivo diseñar un sistema de robot que pudiera trabajar con la cama de la prensa dobladora a la misma altura que lo haría un operador durante la operación manual; esto significaba que la cama no podía levantarse ni unos pocos pies para facilitar el acceso del robot.
También diseñaron el sistema para que fuera móvil. Las primeras iteraciones de diseño tenían un brazo articulado en un carro automatizado (AGV), pero este concepto tenía algunos problemas. Primero, inmovilizó el AGV durante el funcionamiento de la máquina. Después, el robot en sí no estaba asegurado en una ubicación precisa, lo que creaba obstáculos de programación.
El diseño final incorporó una estación de acoplamiento colocada en una ubicación precisa frente a la máquina. El robot se coloca en su lugar, ya sea manualmente (como con un gato hidráulico) o a través de la automatización móvil usando un AGV con horquillas. Una vez que el robot está en posición, el operador se dobla y extiende los brazos que sujetan los escáneres de área SICK montados en la plataforma del robot móvil.
Según las patentes de OpiFlex, estos escáneres funcionan con una unidad de control de seguridad que identifica la celda y la máquina (o máquinas) dentro de ella. Con la celda identificada, la unidad de control de seguridad envía información sobre las configuraciones de la zona de seguridad a los sensores sobre cuándo reducir la velocidad de la operación y dónde detenerse, en caso de que alguien se acerque demasiado al robot.
“La tecnología funciona de modo que, incluso si perdemos aire o energía, no perderemos la pieza de trabajo”, dijo Frisk. “Entonces, si perdemos aire, no perderemos el vacío. En chapa, podemos sujetar una pieza de trabajo durante horas sin perder el agarre. Además, todo es de doble canal, y esto incluye las pinzas”.
Según la compañía, la tecnología cumple con los requisitos de los estándares de seguridad robótica global, incluido ISO 10218. “Estamos siguiendo el estándar ISO”, dijo Frisk, “y por lo tanto, la tecnología también cumpliría con los estándares ANSI y CSA (para los EE. UU. y Canadá)".
Después de extender los brazos que sujetan los escáneres de seguridad, el operador realiza las conexiones necesarias para el aire (para la pinza del robot), la entrada y salida de datos (E/S) y la alimentación.
Un operador mueve el FMR a la estación de acoplamiento frente a un centro de mecanizado. Crédito de la foto: OpiFlex
Entrenando al robot
Luego viene la programación, y aquí la empresa adopta un enfoque que tiene elementos de lo que Syberfeldt y otros investigadores han estado trabajando en el laboratorio durante años. El robot no está programado con un dispositivo de enseñanza ni una simulación de doblado fuera de línea. Un operador podría ajustar el movimiento del robot aquí y allá y determinar la mejor manera de recoger y apilar piezas. De lo contrario, la mayoría de la programación ocurre automáticamente.
El robot puede hacer esto porque durante su instalación y configuración inicial el FMR ha sido “entrenado”, no sobre cómo doblar un trabajo específico, sino sobre cómo operar una máquina completa. La empresa utiliza un asistente de integración que efectivamente "crea una máquina", dijo Frisk, proporcionando una base para la programación simplificada. “El robot conoce la ubicación de la prensa dobladora y otros elementos de la celda del robot”, dijo Frisk. “Configuramos cada robot y celda, y creamos un generador de programas que utiliza el operador. El operador responde algunas preguntas simples y usamos sensores para identificar las piezas y cómo moverlas en la celda”.
La capacitación inicial del robot incorpora los conceptos básicos incluyendo las herramientas disponibles, las posiciones del tope trasero y las mejores formas de configurarlos para ciertas geometrías de piezas y secuencias de doblado. La capacitación también incorpora todas las funciones de la prensa dobladora, como la flexión adaptativa en la que la dobladora se dobla por debajo, mide el ángulo y luego completa los 2 grados finales (teniendo en cuenta el espesor del material y la variación de la propiedad).
El entrenamiento también entra en detalles más sutiles. Por ejemplo, la configuración robótica extrae información de los sensores en el tope trasero y en otros lugares que verifican la alineación de la pieza, incluso en la dirección longitudinal a lo largo de la línea de plegado. En la mayoría de los casos, las ventosas de la pinza mantienen el contacto con la brida mientras se balancea hacia arriba durante la curva. De todos modos, las ventosas pueden moverse muy levemente, lo que podría ser suficiente para hacer que una pieza complicada y con múltiples curvas quede fuera de tolerancia.
Frisk describió una pieza de trabajo reciente con seis curvas. En cada doblez, los sensores verificaron la alineación y la posición de la línea de doblez, especialmente crítica para los dobleces iniciales, considerando los efectos de las tolerancias de apilamiento en los dobleces posteriores. Un pequeño error en la primera curva puede convertirse en un gran error en la última curva. Mostró un video que demuestra cómo, en la cuarta curva, el sistema detectó un ligero movimiento de la pieza de trabajo. “El robot se mueve ligeramente hacia adelante y hacia atrás para alinear perfectamente la pieza de trabajo en la dirección longitudinal”, dijo Frisk.
El entrenamiento del robot involucra no solo el freno, sino todo el sistema de celdas de doblado, incluido la tarima entrante de piezas en bruto planas y una tarima de piezas formadas. Por ejemplo, utilizando una combinación de sensores, software y un sutil movimiento robótico, el sistema está diseñado para eliminar la necesidad de un cuchillo de aire al recoger láminas delgadas.
La formación para el apilamiento de piezas formadas implica opciones de orientación de las piezas. Ciertas piezas se pueden apilar una encima de la otra, mientras que otras deben apilarse en ángulo para garantizar que la pila sea estable y no se vuelque sobre la tarima.
Nuevamente, toda esta capacitación proporciona la base para que el robot se programe solo, con el operador ajustando la ruta, las opciones de apilamiento y otros elementos según sea necesario. Según Frisk, el refinamiento de un programa simple en la prensa dobladora toma alrededor de dos minutos, el más complejo alrededor de 15 minutos.
La búsqueda para lograr un flujo flexible
Por supuesto, no todos los trabajos son adecuados para FMR. Aunque tienen un gran número de pinzas disponibles, pueden tener problemas para doblar piezas extremadamente pequeñas. Además, el robot no está montado en un riel, por lo que es posible que no pueda acceder a todas las herramientas en ciertas configuraciones de doblado con conjuntos de herramientas que se extienden por toda la cama. Frisk agregó que a veces los talleres pueden superar estos desafíos alterando la ubicación de las herramientas.
Aun así, no todas las aplicaciones son adecuadas para la robótica y, en la fabricación con una gran variedad de productos, la idoneidad puede cambiar de un día a otro, de un turno a otro, incluso de una hora a otra; de ahí la necesidad de mover el FMR de una máquina o área a otra en caso de ser necesario. Y con la nueva tecnología de protección (sin vallas), los operadores ahora pueden trabajar en máquinas adyacentes, tal vez doblando piezas que simplemente no son adecuadas para el FMR. Claro, probablemente podrían trabajar para adaptar el FMR a un trabajo desafiante, pero ¿por qué tomarse la molestia cuando un operador de frenos capacitado puede configurar la máquina y simplemente terminar el pedido?
Un operador da los toques finales a un programa para un robot móvil flexible que atiende una paneladora. En comparación con la operación de la prensa dobladora, el cuidado de la máquina pick-and-place requerido para el doblado de paneles es relativamente sencillo de automatizar. Crédito de la foto: OpiFlex y SICK
Al igual que los humanos, no todos los robots serán adecuados para todos los trabajos. Por ejemplo, al momento de escribir este artículo, OpiFlex no está desarrollando FMR para soldadura, un proceso que requiere componentes auxiliares como alimentadores de alambre y gas de protección. Aun así, están surgiendo otras alternativas flexibles en el mercado, incluidos los cobots y los robots a los que se les puede enseñar a soldar cinéticamente (moviendo físicamente la antorcha de soldar) ya través de interfaces simplificadas. Algunas tecnologías están eliminando por completo la necesidad de programar soldaduras; el robot “ve” la soldadura, la compara con el archivo CAD, la ajusta y comienza a soldar. Una tecnología similar está disponible para el recubrimiento en polvo e incluso para la limpieza con chorro. (Para obtener más información sobre esto, consulte la cobertura de The FABRICATOR de FABTECH 2021, archivada en thefabricator.com).
Aun así, la capacidad de mover el FMR entre varias máquinas ayuda a superar los desafíos perennes del taller de la restricción de movimiento. A fines de 2021, los FMR se han utilizado para operar y atender dobladoras de paneles, prensas de estampado, centros de mecanizado, prensas de inserción de hardware y una variedad de operaciones de manejo de materiales. En muchas de estas aplicaciones, dijo Frisk, los fabricantes se están alejando de equipos como transportadores, muchos de los cuales se usaban simplemente para transportar piezas fuera de una celda automatizada y a través de cercas de seguridad para apilarlas. Con los avances en protección sin cercas, ¿para qué tener un transportador?
La flexibilidad potencial de los FMR está empujando a algunas empresas, incluso a algunos OEMs grandes a repensar sus operaciones. Frisk dijo que, en los últimos años, OpiFlex ha recibido más llamadas de fabricantes de equipos originales (OEM) y Tier 1 grandes que de talleres de trabajo pequeños y medianos y fabricantes por contrato.
“Tengo que admitir que no esperábamos eso”, dijo, y agregó que, en estos días, con la demanda de los clientes en constante cambio y los ciclos de desarrollo de nuevos productos cada vez más cortos, la flexibilidad se ha vuelto primordial en casi todos los entornos de fabricación.
Robots como colegas
Considere un taller de chapa metálica con robots en el área de doblado. Tal automatización aumenta la capacidad allí, pero ¿qué pasa si un cuello de botella en el mecanizado retrasa las operaciones de ensamblaje final? En este caso, un operador podría mover el FMR al centro de mecanizado, sujetarlo en su lugar en la estación de acoplamiento montada en el piso, iniciar la operación y aumentar el rendimiento del mecanizado. Debido a que la atención del robot en el mecanizado es relativamente simple en comparación con el doblado en la prensa dobladora, los FMR de OpiFlex (después del entrenamiento inicial) no requieren programación específica del trabajo, una hazaña que hace posible el flujo de piezas de una sola pieza.
Teniendo en cuenta la llegada del cambio automático de herramientas y ahora los FMR, ¿será posible el flujo de piezas de una sola pieza en la prensa dobladora? Frisk hizo una pausa y pensó por un momento. “Sí, el cambio rápido es increíblemente importante”, dijo, pero agregó que doblar en la prensa dobladora es un animal único. “Una prensa dobladora sigue siendo algo bastante complicado. Tenemos que tener un poco de respeto por eso. La chapa en general es complicada (para la robótica) porque las piezas que provienen del corte por láser pueden ser muy diferentes. En el mecanizado, trabajamos con piezas de trabajo redondas o cuadradas. Es mucho más simple”. Lo que sí dijo es que la interacción entre robots y humanos evolucionará significativamente a medida que aumente la capacidad cognitiva de los robots. Al igual que los humanos, podrán mirar, escuchar y aprender.
De vuelta en el laboratorio de Syberfeldt, el profesor tocó un robot adyacente para despertarlo (más o menos análogo a despertar a las computadoras del sueño). El robot, equipado con sensores visuales y auditivos que alimentan un motor de inteligencia artificial, ahora está listo para trabajar. “El hecho de tocarlo le dice al robot: ‘oye, estoy aquí’. Entonces puedo hacer un gesto para mostrarle al robot lo que quiero que haga y cómo. Nuestro objetivo es hacer que el robot sea lo más humano posible”.
Tales interacciones se convertirán en una parte crítica de lo que la comunidad científica llama sistemas ciberfísicos. “Estamos tratando de distribuir inteligencia a unidades específicas en el sistema de producción”, dijo Syberfeldt, “e introducimos muchas dinámicas. Entonces, independientemente de la situación y el entorno, el robot puede ver lo que se necesita, tomar una decisión y luego ir a donde se necesita”.
El hardware, incluidos los sistemas de seguridad y las pinzas, seguirá siendo más avanzado. Syberfeldt prevé que las pinzas en algunas aplicaciones se vuelvan más parecidas a las manos, nuevamente para imitar la flexibilidad del operador humano. Los mayores avances estarán en el software.
“La pregunta que estamos tratando de responder es: '¿Cómo pueden los humanos interactuar con un robot de la manera más eficiente?' Lo hemos visto desde la perspectiva de la robótica. Creo que ahora tenemos que mirar el desafío desde una perspectiva humana. Los humanos necesitan adaptarse, porque lo que estamos descubriendo es que, si bien estamos programados para interactuar entre nosotros y con otros animales, simplemente no es natural que los humanos interactúen con los robots. Necesitamos ver al robot como nuestro nuevo colega en el taller”.
About the Author
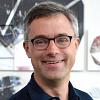
Tim Heston
2135 Point Blvd
Elgin, IL 60123
815-381-1314
Tim Heston, The Fabricator's senior editor, has covered the metal fabrication industry since 1998, starting his career at the American Welding Society's Welding Journal. Since then he has covered the full range of metal fabrication processes, from stamping, bending, and cutting to grinding and polishing. He joined The Fabricator's staff in October 2007.
About the Publication
Compañías Relacionadas
subscribe now
FMA Communications ha introducido al mercado la edición en Español de la revista The Fabricator. Esta versión consiste del mismo tipo de artículos técnicos y sección de lanzamientos de nuevos productos que actualmente presentan el personal de primera categoría de Fabricator en Inglés.
start your free subscription- Podcasting
- Podcast:
- The Fabricator Podcast
- Published:
- 04/30/2024
- Running Time:
- 53:00
Seth Feldman of Iowa-based Wertzbaugher Services joins The Fabricator Podcast to offer his take as a Gen Zer...
- Trending Articles
Los operadores de prensa dobladora inexpertos hacen indispensable el repensar la seguridad
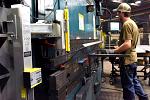
Prescripción para la reducción del desperdicio: arreglo esbelto de las instalaciones
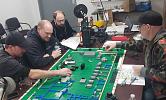
Anidado para la estabilidad del corte láser
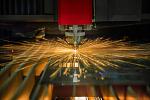
La máquina procesadora de placas crea biseles complejos en un solo corte
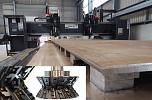
El software guía a los soldadores a través de instrucciones de trabajo
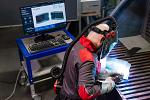
- Industry Events
Pipe and Tube Conference
- May 21 - 22, 2024
- Omaha, NE
World-Class Roll Forming Workshop
- June 5 - 6, 2024
- Louisville, KY
Advanced Laser Application Workshop
- June 25 - 27, 2024
- Novi, MI
Precision Press Brake Certificate Course
- July 31 - August 1, 2024
- Elgin,