Laser Division Product Manager
- FMA
- The Fabricator
- FABTECH
- Canadian Metalworking
Categories
- Additive Manufacturing
- Aluminum Welding
- Arc Welding
- Assembly and Joining
- Automation and Robotics
- Bending and Forming
- Consumables
- Cutting and Weld Prep
- Electric Vehicles
- En Español
- Finishing
- Hydroforming
- Laser Cutting
- Laser Welding
- Machining
- Manufacturing Software
- Materials Handling
- Metals/Materials
- Oxyfuel Cutting
- Plasma Cutting
- Power Tools
- Punching and Other Holemaking
- Roll Forming
- Safety
- Sawing
- Shearing
- Shop Management
- Testing and Measuring
- Tube and Pipe Fabrication
- Tube and Pipe Production
- Waterjet Cutting
Industry Directory
Webcasts
Podcasts
FAB 40
Advertise
Subscribe
Account Login
Search
El orgullo de ser propietario de la programación de máquinas punzonadoras y de corte por láser
La operación de la máquina de corte por láser no es un trabajo para pulsadores de botones
- By Dustin Diehl
- January 6, 2022
- Article
- Laser Cutting
Los programadores de máquinas que piensan en el panorama general, incluido el rendimiento de la chapa y cómo un nido afecta el procesamiento de fabricación posterior, pueden ayudar a impulsar el rendimiento de fabricación y hacer la vida más fácil en el taller. Imágenes: Amada
¿Recibe informes de rendimiento que muestran un tiempo de luz verde abismalmente bajo? Para conocer la cruda realidad diríjase al taller. Es posible que encuentre algunos empleados cansados en la estación de agitar y romper cerca de su láser de fibra independiente.
Es posible que vea un tiempo de inactividad inesperado en su centro de corte láser automatizado, o sea, su automatización de extracción de piezas atascada por una pieza en particular. Su unidad combinada de punzón / láser también podría estar más averiada de lo esperado, ya que los técnicos buscan eliminar los problemas de calidad de las piezas después de reposicionar la abrazadera.
Es posible que vea la configuración de una prensa dobladora que tiene demasiadas piezas de prueba. Probablemente hable con el operador y descubra que no puede calibrar la pieza regularmente. Verá las piezas cortadas apiladas cuidadosamente cerca del freno, mirará más de cerca los bordes y verá los restos de una microtab rota. Luego caminará hacia la soldadura y verá dos chapas en un dispositivo. Los bordes acoplados pronto se fusionarán y cubrirán con metal de soldadura, sin embargo, aún no están desbarbados para lograr un acabado perfecto. ¿Por qué se desbarbaron esas piezas en la soldadura y, sin embargo, las piezas en el doblado no lo fueron?
Todo esto apunta a lo que se ha convertido en la piedra angular de la fabricación moderna de chapa metálica: la programación, incluido el anidamiento y la programación de la operación de corte principal del taller (ver Figura 1). Quienes tienen la propiedad sobre la programación no solo piensan en el rendimiento del material, sino también en lo que le sucede a una pieza durante y después de la perforación o el corte con láser.
Al conocer todos los procesos necesarios para llevar una pieza cortada al formado, la soldadura y demás, los programadores pueden desarrollar estrategias que ayuden a que esas tareas sean lo más fáciles y repetibles posible. Dicho de otra manera, los buenos programadores (personas con un fuerte sentido de propiedad sobre su trabajo que pueden equilibrar la búsqueda del fabricante de un alto rendimiento de material con las necesidades de las operaciones posteriores) pueden ayudar a que un taller con dificultades sea más exitoso.
Implicaciones de un microtabbing deficiente
En un mundo perfecto, cada pieza cortada se colocaría perfectamente en un nido sin una microtab para que los trabajadores o la automatización pudieran levantar fácilmente cada pieza de trabajo de la hoja y enviarla aguas abajo sin necesidad de desbarbar.
Sin embargo, varios factores presionan a los programadores a realizar microtabbing. La primera y más obvia es la geometría de la pieza. En una máquina de corte por láser algunas formas de las piezas (especialmente las pequeñas) simplemente no pueden quedar sueltas en una chapa sin caer a través de los listones.
Sin embargo, sin importar la forma de la pieza, los programadores confían en las microtabs para la estabilidad de la pieza, y los mejores lo hacen pensando no solo en lo que sucede en la mesa de corte, sino también después. Por ejemplo, un taller con personal cansado en la mesa de separación de partes probablemente tenga un problema de rebasamiento.
El perímetro de las piezas de 0.25 pulgadas de espesor y más, en general no necesitan pestañas en absoluto. Piense en el juego “Operando”. Cuando levanta una pieza gruesa a través del agujero y la suelta por error, aterriza en los bordes del agujero, pero no se cae. La misma interacción sucede en chapas y placas de metal más gruesas. El espesor por sí solo ayuda a bloquear la pieza en el esqueleto.
Cuando vea empleados del área de separación con dispositivos de succión o magnéticos levantando piezas de 0.25 pulgadas o piezas más gruesas, están jugando efectivamente Operando. En sus días más productivos, simplemente levantan las partes sin pestañas perfectamente directamente del esqueleto. En materiales de 0.375 pulgadas o más gruesos, incluso una sola pestaña, puede hacer que la pieza sea virtualmente imposible de separar del esqueleto, sin importar cuán estrecha sea.
Figura 1. Aquellos que tienen la propiedad de la programación piensan en todos los detalles, incluido el tamaño y la ubicación de las microtabs, la orientación de las piezas en relación con los listones, la integridad del esqueleto y cómo la colocación de las uniones afecta las operaciones posteriores.
En las circunstancias adecuadas, una pestaña generalmente será suficiente para mantener la mayoría de las piezas de chapa en el esqueleto. Usando un imán u otro dispositivo de elevación usted debería poder tirar hacia arriba y, después de hacer un ligero movimiento hacia adelante y hacia atrás, escuchar el chasquido de la microtab cuando la pieza se libera.
Si las circunstancias requieren que coloque la pestaña en la pieza dos veces, la ranura alrededor de esa pieza debe ser lo suficientemente ancha como para permitirle girarla hacia adelante y hacia atrás para romper ambas pestañas. Tener más de tres microtabs en una parte es una señal de alerta. Dejando a un lado las circunstancias inusuales, lo más probable es que esté usando demasiadas pestañas.
Desarrollar una estrategia de microtabbing
Cuando lo haga, asegúrese de seguir una práctica que sea coherente en todo el taller. Algunas operaciones utilizan anchos de pestaña estándar para diferentes espesores de material; una vez más, el material más grueso requiere pestañas más estrechas, considerando que todo el espesor del material aumenta el volumen (y el poder de retención) de cada pestaña. Algunos usan fórmulas que optimizan las pestañas para mezclas de piezas específicas. Cualquiera que sea esa práctica estándar, debe tener en cuenta no solo la estabilidad del corte, sino también el procesamiento posterior.
Digamos que la pestaña está en el borde que se deslizará contra un tope trasero en una prensa dobladora. La rebaba que queda después de romper la microtab puede hacer que la pieza se mueva ligeramente cuando el operador presiona el borde contra el tope trasero. Tal inconsistencia puede causar muchos dolores de cabeza por el doblado.
Si ha determinado que esa microtab es absolutamente necesaria y no desea recurrir a agregar un proceso de desbarbado secundario, tiene dos alternativas. Puede mover esa pestaña a otra parte del perímetro de la pieza, como a un borde que se va a soldar, o si el diseño de la pieza lo permite (tanto funcional como cosméticamente) puede diseñar la pestaña para que se rompa hacia adentro, dejando una pequeña hendidura en el borde de la pieza y creando una superficie de medición plana para el operador del freno.
Por supuesto, antes de decidir dónde debe ir la pestaña o cómo debe romperse, primero pregunte si necesita la pestaña. ¿Hay alguna manera de adaptar un nido o secuenciar el corte para eliminar la necesidad de esa pestaña? Aquí es donde entra en juego la prevención de colisiones de su software de anidamiento.
Supongamos que tiene una pieza que tiene geometrías internas (cuerpos extraños) propensa a volcarse, o una pieza que tiende a arquearse después de ser cortada. Podría usar microtabs, pero probablemente haya una solución más simple y mucho más efectiva.
Al programar un láser volador puede utilizar la prevención de colisiones para asegurarse de que el cabezal nunca atraviese una determinada coordenada donde ya estaba, y secuenciar ciertas geometrías de corte propensas a inclinarse al final. Por ejemplo, el cabezal láser puede cortar primero las geometrías internas de una pieza y luego tomar un nuevo camino hacia el perímetro de la pieza, no sobre áreas previamente cortadas donde estos cuerpos extraños inclinados hacia arriba podrían causar un choque.
La relación de una pieza con los listones también juega un papel importante. Si tiene una parte larga y delgada, generalmente querrá anidarla en la dirección X para que quede a través de múltiples listones (vea la Figura 2). Esto significa que, incluso si tiene acero de mala calidad que se arquea después del corte, la pieza permanecerá firmemente asentada en la mesa de corte.
Algunos softwares le permiten agregar ubicaciones de listones al diseño del nido para que pueda ver claramente dónde se asientan los listones en relación con las partes que está cortando. Si ve una pieza sobre dos listones, pero necesita que esté sobre tres, puede hacer el cambio.
Figura 2. Para que se encuentren sobre múltiples listones, las partes largas están orientadas en la dirección X.
Factores de automatización de corte por láser
Un programador de primera en la actualidad debe considerar no solo la estabilidad de la pieza durante el corte, sino también cómo se mueve el material a lo largo de todo el proceso de corte. Y la naturaleza de ese movimiento puede variar enormemente, especialmente en operaciones que tienen sistemas de corte tanto autónomos como automatizados.
En láseres voladores independientes, el movimiento del material es mínimo. La hoja se desplaza hacia el área de trabajo, la máquina calibra (estableciendo la coordenada 0,0) y el cabezal láser comienza a cortar. Después de cortar, la máquina lanza la hoja cortada a la estación de descarga.
El programa de corte aún debe garantizar la estabilidad de la pieza, evitando que el cabezal se vuelque y colisione. El flujo de gas auxiliar también puede tener un efecto en algunos entornos, lo que hace que las piezas se vuelquen cuando el cabezal se eleva al final de un corte. Para evitar esto, las máquinas modernas apagan el gas auxiliar abruptamente cuando el cabezal se retrae y se mueve a la siguiente coordenada. Si la máquina no hace esto de manera efectiva, y si el cabezal necesita atravesar la parte previamente cortada, un programador siempre puede poner una pausa breve (como un código M en el programa) antes de atravesar esa parte.
De cualquier modo, con un láser de óptica voladora independiente la mesa de lanzadera se mueve pero la hoja en sí no lo hace, al menos hasta que los empleados en la mesa de separación comiencen a quitar piezas (lo que nuevamente los programadores deben tener en cuenta en su estrategia de anidamiento y tabulación). Debido a que la hoja en sí no se mueve, garantizar la estabilidad de la pieza y la extracción efectiva es relativamente sencillo.
La automatización láser introduce variables adicionales y, para comprenderlas, es útil saber exactamente cómo se mueven las hojas y las piezas hacia y desde el área de trabajo de corte. El primer nivel de automatización mueve las hojas de un sistema de almacenamiento a la mesa de corte, luego retira el nido de corte completo después del corte, ya sea a un casete del sistema de almacenamiento o una mesa de descarga para clasificar las piezas.
Esto generalmente implica una combinación de ventosas para recuperar el material y horquillas que se deslizan entre los listones para levantar y quitar la hoja cortada, tanto el esqueleto como las partes cortadas. Las propias horquillas deben entrar lo suficientemente por debajo de la hoja para evitar chocar con cualquier parte o inclinación de geometría interna (cuerpos extraños) entre los listones. En la mayoría de los casos, las horquillas suben y levantan la hoja sin incidentes, pero las vueltas o distorsiones severas de las piezas (especialmente con piezas grandes) pueden crear problemas cuando las horquillas levantan y transportan el nido de piezas cortadas hasta su destino.
Para evitar esto, un programador podría tener la tentación de agregar más microtabs, pero nuevamente, agregar esos microtabs también podría agregar costos de procesamiento y dolores de cabeza generales en el futuro. Por lo general, es mejor identificar las causas fundamentales de esa inclinación y distorsión. En lugar de agregar microtabs, podría ser mucho más fácil simplemente reposicionar o reorientar una parte en un diseño de nido (o, a veces, cambiar la forma en que se espacian los listones en la mesa) para que las partes permanezcan estables y no se vuelquen en primer lugar.
Cuando la eliminación y clasificación automatizada de piezas entran en escena, las variables aumentan. Las opciones modernas incluyen copas de succión inteligentes en un sistema mecanizado (ver Figura 3) o al final de un brazo robótico. Usando una variedad de tamaños, estas copas pueden agarrar la pieza firmemente y sacarla limpiamente del nido. En lugar de un humano, ahora la automatización juega “Operando”.
Dicho esto, algunas geometrías pueden crear desafíos para la extracción de piezas, especialmente cuando se trata de ángulos agudos. Una parte con un ángulo agudo tiene una mayor probabilidad de engancharse o interferir con el esqueleto. En este caso, el láser puede realizar una secuencia de destrucción del esqueleto (o destrucción de cuerpos extraños), eliminando el metal esquelético cerca del ángulo agudo de la pieza para que cuando las copas quiten la pieza, todo esté despejado.
En otras situaciones donde hay probabilidad de engancharse, el láser puede cortar hendiduras en el esqueleto en ubicaciones estratégicas. Esas hendiduras hacen que la red esquelética sea menos rígida y le permiten alejarse de la pieza cuando las copas levantan la pieza de la hoja.
Figura 3. Con la estrategia correcta de anidación y programación, los sistemas de extracción de piezas deberían poder sacar las piezas limpiamente del nido.
Las secuencias de destrucción del esqueleto pueden llevarse un paso más allá y, en algunos casos, eliminan la necesidad de retirar piezas por succión. Considere un escenario en el que el láser corta un nido de varias partes rectangulares grandes, luego destruye el esqueleto restante, cortando pequeños triángulos que caen a través de los listones y a través de un conducto de desechos. Luego, las horquillas ingresan desde abajo, levantan las piezas de trabajo grandes y luego las transfieren a un transportador que transporta el trabajo hacia abajo.
La practicidad de este enfoque depende de la mezcla de piezas, los volúmenes, el tamaño y la forma de sus piezas (es mucho más común cuando se trata de piezas grandes en grandes volúmenes). Independientemente, el enfoque ejemplifica el pensamiento holístico. Desde una perspectiva de corte puro de pulgadas por minuto, destruir el esqueleto de esa manera puede parecer un desperdicio extraordinario. Pero piense en los beneficios. La chatarra se recoge automáticamente en contenedores fáciles de mover. La tabulación se vuelve innecesaria y elimina la necesidad de mover un esqueleto con partes sueltas.
Tabulación para máquinas punzonadoras y combinadas
Las microtabs juegan varios roles en el punzonado. Al igual que en un láser independiente, las pestañas mantienen las piezas seguras a medida que salen de la máquina, si aún no se han separado y enviado por un conducto. Pero a diferencia del corte por láser, las pestañas y las redes del esqueleto funcionan en conjunto para garantizar la integridad del esqueleto a medida que la hoja se mueve a lo largo del ciclo de corte. Un esqueleto débil puede causar estragos.
La ubicación de las pestañas, cuerpos extraños y los componentes del esqueleto son especialmente importantes para garantizar que las piezas no se enganchen en el esqueleto, sino que caigan constantemente por el conducto. El recorte de línea común es una estrategia habitual aquí; una pequeña parte en un grupo de piezas de trabajo de corte de línea común tiene más posibilidades de caer libremente sin ningún esqueleto que le estorbe. Alternativamente, esto podría requerir secuencias de destrucción de esqueletos o cuerpos extraños y tabulación estratégica. El resultado final: cuando se corta el último microtab nada debe evitar que esa parte se caiga.
Nuevamente, debido a que la hoja se está moviendo no tiene más remedio que asegurarse de que las piezas estén tabuladas en su lugar durante el ciclo de corte. Esto puede parecer una desventaja, pero en el contexto de la automatización en realidad es una gran ventaja. De hecho, hay una buena razón por la que la automatización de la extracción de piezas es mucho más común en el campo de punzonado y punzón / láser.
Las nuevas tecnologías de control de rayo láser están cambiando el juego (más información adelante), pero en el corte por láser tradicional las piezas sin tabular deben viajar "sueltas" dentro del esqueleto a través de varias posiciones después del corte antes de llegar a la automatización de selección de piezas.
No es así con la automatización del sistema de punzonado o de combinación de punzón / láser. La hoja se sujeta y se mueve debajo de la torreta y el cabezal láser. Comienza el corte y las micro articulaciones mantienen el trabajo en su lugar. Luego viene el proceso de eliminación de piezas. En algunas situaciones, una herramienta dedicada a la eliminación de micro articulaciones corta las pestañas justo antes de que entre la pinza para quitar la pieza. En otros casos, las succiones pueden agarrar y asegurar la pieza antes de que el láser elimine las micro articulaciones. El láser corta y la pieza se levanta de forma segura. La pieza jamás flota suelta en una hoja.
Tablas de listones y cepillos
Muchos pasan por alto una variable clave: el estado de la mesa de corte. Esto incluye la mesa de cepillo para combinaciones de punzonado y punzonado / láser, así como los listones de mesa para corte por láser (ver Figura 4). La acumulación de escoria en sus listones hace más que verse mal. De hecho, puede cambiar la posición de la hoja y la pieza.
Imagine que el láser corta una pieza. La mesa de lanzadera se mueve a la estación de descarga de piezas y una agarradera comienza su ciclo. El problema es que no recoge la pieza. ¿Por qué? Se remonta a esos listones sucios. La escoria no se esparce uniformemente, por supuesto. Algunas puntas de los listones tienen más escoria que otras, lo que hace que todo lo que esté encima de ellas sea desigual.
Después de que el láser corta la pieza, simplemente flota en el esqueleto y se asienta de manera desigual sobre esos listones sucios. La automatización "piensa" que la pieza está a cierta altura cuando no lo está. Y debido a que la pieza de trabajo es desigual, es más probable que se enganche contra el esqueleto. Una vez más es el juego “Operando” y con listones sucios la automatización de extracción de piezas tiene una mayor probabilidad de perder. La solución es obvia: limpie sus listones de manera regular.
Figura 4. Un láser comienza a cortar un conjunto de listones de cobre nuevos y limpios. El corte láser confiable requiere una limpieza regular de los listones, especialmente en sistemas automatizados. La acumulación excesiva de escoria puede cambiar la posición de la hoja y la pieza cortada, lo que a su vez puede afectar la fiabilidad de la automatización de extracción de piezas.
En una configuración de punzonado o de combinación punzón / láser, la condición de la mesa de corte puede ser igualmente importante. De hecho, ignorar la condición de la mesa podría evitar que el programador utilice estrategias que resulten en una mayor utilización del material.
Esto incluye el viejo truco de reposicionar las abrazaderas para que el programador pueda colocar las piezas "debajo de las abrazaderas". Para reposicionar una hoja usted reposiciona almohadillas con émbolos, extiende y mantiene la hoja sin moverse mientras las abrazaderas se sueltan y reposicionan. Al final de la operación se recuperan las piezas solo para encontrar un pequeño paso en el borde de una pieza. Parece que hubo un problema con el reposicionamiento de la abrazadera.
Usted comprueba los émbolos en las almohadillas de reposicionamiento; no están gastados. Se activan por aire, por lo que verifica la presión del aire, que parece acertada. Por lo tanto, los émbolos deben tener un agarre firme.
Antes de señalar con el dedo al departamento de programación y convertir en una regla el no incluir el reposicionamiento de la abrazadera, verifique el estado de la mesa de cepillos. Una mesa de cepillo desgastada 3 mm en ciertas áreas puede ser suficiente para causar un problema. Cuando las abrazaderas sueltan la hoja, la hoja se dobla solo un poco, pero lo suficiente como para que cuando las abrazaderas se vuelvan a enganchar en su nueva posición empujen la hoja ligeramente. Eso es suficiente para crear una discrepancia entre el lugar donde está la hoja y el lugar donde el programa cree que está.
Estableciendo las reglas
Todas estas condiciones del taller del mundo real (la naturaleza de la automatización en su taller, la remoción de piezas, el estado de sus máquinas) deberían ayudarlo a construir reglas que den forma a su estrategia de programación. Con el aporte de los operadores, los empleados de remoción de piezas y otros, usted puede crear programas que les ayudarán a hacerles la vida más fácil.
Puede optar por una secuenciación que evite colisiones de cabezales, y puede indicarle al software si es necesario colocar ciertos tipos de piezas en la cantidad de listones de la cama de corte por láser. Si ciertas partes serán difíciles para la automatización de la extracción, puede decirle al software que las anide en grupos que la automatización de la extracción pueda captar.
Por ejemplo, si está cortando un panel con una ventana grande, es posible que pueda colocar una docena de soportes pequeños en esa ventana, y todos se pueden ser tabuladas y asegurar para que una pinza automática los agarre, mueva y apile, incluso en una operación desatendida durante el fin de semana.
Esta automatización desatendida en el corte por láser, completa con el apilado de piezas, seguramente se volverá más común en los próximos años, y esto tiene mucho que ver con la tecnología detrás del rayo láser en sí. Varias técnicas de manipulación y ancho del haz del láser están creando cortes más anchos que ayudan a que la extracción automatizada de piezas sea mucho más robusta y confiable.
Algunas de las últimas tecnologías de control del haz del láser pueden crear anchos de corte dos o tres veces más anchos de lo que era posible antes (consulte la Figura 5). Para la automatización de extracción de piezas (y el personal de extracción manual de piezas, para el caso), esto hace que el juego de la Operación sea más fácil que nunca.
Calidad del material, rendimiento y flujo de piezas
Sus listones están limpios. Su mesa de cepillos está lejos de estar gastada. Su programación estratégica, el uso de prevención de colisiones, orientación de piezas, restricciones de grano para doblar o cosméticos, y más, ha ayudado a agilizar el flujo y hacer que la vida en el taller sea mucho más predecible.
Figura 5. Las nuevas tecnologías de control de rayos de laser ajustan el ancho de corte para la aplicación, como cortes más anchos para la automatización de remoción de piezas.
Como buen programador, usted se enorgullece de lograr altos rendimientos. Al mismo tiempo, ha implementado buenas reglas para que el software se ancle de la manera que mejor se adapte a su operación. Minimiza su tiempo ajustando nidos dinámicos (considerando que, a diferencia de los nidos estáticos, es probable que no vuelva a ver ese grupo de partes), aunque ha establecido preferencias de reglas que le brindan un nido dinámico que no necesita ser modificado de todos modos. Por supuesto, debido a las restricciones de orientación de las piezas u otras restricciones, es posible que sacrifique un poco de rendimiento del material para garantizar la estabilidad del proceso con un alto tiempo de luz verde, pero vale la pena.
Luego, los precios de los materiales se disparan. El mayor gasto en el balance general acaba de aumentar aún más. Como programador, usted está en el centro de un debate en toda la empresa. Los gerentes y compradores quieren el máximo rendimiento en cada chapa y están encantados de cambiar a material más económico. Mientras tanto, el personal del taller solo quiere el material que necesita ahora (por favor, nada de piezas de relleno innecesarias solo para llenar un nido) y quieren una buena chapa plana con láser.
Para mitigar esto, usted como programador se comunica con la gerencia de la tienda y las compras sobre el valor de un buen material. Unos pocos centavos ahorrados por tonelada serán superados con creces por las horas pasadas en el piso lidiando con la distorsión y otras características impredecibles de las hojas deficientes.
Un mejor stock puede impulsar el rendimiento a las nubes de varias maneras. Por ejemplo, supongamos que tiene una chapa llena de partes largas y delgadas. Un programador con buen material probablemente querrá anidarlos en la dirección X a través de los listones y realizar cortes de línea común. Esos cortes comunes tienen un triple beneficio: acortan drásticamente el tiempo de corte (al cortar una línea se obtienen bordes de dos partes), aumentan el rendimiento del material y facilitan el procesamiento posterior. Las partes son fáciles de quitar del nido. Y sin micro juntas no requieren desbarbado, ni abren la puerta a problemas de calibrado en la prensa dobladora. Por supuesto, si tiene un material insatisfactorio y sus piezas se arquean, es posible que deba agregar micro juntas por lo que todos esos beneficios del procesamiento posterior se van por la ventana.
Para satisfacer la demanda de mayor rendimiento y al mismo tiempo equilibrar las necesidades del taller, solicite a su ERP y al personal de programación una estimación de uso anual. Lo usará para gobernar el uso de la pieza de relleno y la estrategia de gestión de remanentes. Claro, 100 de una determinada parte pueden encajar perfectamente en una chapa, pero si eso le da suficiente para dos años, no son buenas piezas de relleno. Por otro lado, si un 50 adicional de una determinada pieza tiene buenas posibilidades de ser utilizado durante las próximas dos semanas, cortar y almacenar esas piezas de relleno puede tener sentido.
Estas decisiones pueden variar mucho y dependen en gran medida de las necesidades y la naturaleza de la operación. Independientemente, los buenos programadores no pueden simplemente enterrar la cabeza frente a la pantalla de una computadora. Cuanto mejor conozcan el taller y lo que les sucede a sus piezas durante y después del corte, más ayudarán a mejorar el flujo y aumentar el rendimiento, desde las piezas en bruto hasta el muelle de envío.
About the Author
About the Publication
Compañías Relacionadas
subscribe now
FMA Communications ha introducido al mercado la edición en Español de la revista The Fabricator. Esta versión consiste del mismo tipo de artículos técnicos y sección de lanzamientos de nuevos productos que actualmente presentan el personal de primera categoría de Fabricator en Inglés.
start your free subscription- Podcasting
- Podcast:
- The Fabricator Podcast
- Published:
- 04/16/2024
- Running Time:
- 63:29
In this episode of The Fabricator Podcast, Caleb Chamberlain, co-founder and CEO of OSH Cut, discusses his company’s...
- Trending Articles
Los operadores de prensa dobladora inexpertos hacen indispensable el repensar la seguridad
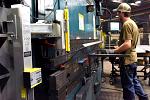
La mezcla de gas auxiliar impulsa la tecnología del láser de fibra
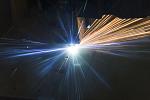
Prescripción para la reducción del desperdicio: arreglo esbelto de las instalaciones
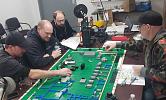
Máquina de corte por láser diseñada para el mercado mexicano
La sierra de doble carro sigue los contornos del tubo perfectamente
- Industry Events
16th Annual Safety Conference
- April 30 - May 1, 2024
- Elgin,
Pipe and Tube Conference
- May 21 - 22, 2024
- Omaha, NE
World-Class Roll Forming Workshop
- June 5 - 6, 2024
- Louisville, KY
Advanced Laser Application Workshop
- June 25 - 27, 2024
- Novi, MI