Communications Manager
- FMA
- The Fabricator
- FABTECH
- Canadian Metalworking
Categories
- Additive Manufacturing
- Aluminum Welding
- Arc Welding
- Assembly and Joining
- Automation and Robotics
- Bending and Forming
- Consumables
- Cutting and Weld Prep
- Electric Vehicles
- En Español
- Finishing
- Hydroforming
- Laser Cutting
- Laser Welding
- Machining
- Manufacturing Software
- Materials Handling
- Metals/Materials
- Oxyfuel Cutting
- Plasma Cutting
- Power Tools
- Punching and Other Holemaking
- Roll Forming
- Safety
- Sawing
- Shearing
- Shop Management
- Testing and Measuring
- Tube and Pipe Fabrication
- Tube and Pipe Production
- Waterjet Cutting
Industry Directory
Webcasts
Podcasts
FAB 40
Advertise
Subscribe
Account Login
Search
Logre la perfección del borde cortado con plasma
Consejos probados con el tiempo para resultados óptimos en la mesa de plasma
- By Michelle Avila
- December 9, 2020
- Article
- Plasma Cutting
Si combina una fuente de energía de plasma de alta calidad con la mesa o sistema de corte correcto, es posible cortar partes con bordes tersos y poca o ninguna angulosidad. Sin embargo, ocasionalmente los fabricantes se enfrentan a una calidad de corte poco satisfactoria. He aquí un vistazo a los retos de calidad de corte más comunes y los pasos requeridos para retomar el camino.
Escoria
Por mucho, el problema más común de calidad de corte con el que se enfrentan los fabricantes es la escoria. Aunque es relativamente fácil remover el metal en exceso que se solidifica a lo largo del borde superior e inferior de la parte, esto implica más trabajo. Cuando alguien tiene que hacer una operación secundaria como rectificado, cincelado o lijado, con frecuencia es para remover escoria.
La escoria ocurre por varias razones. La velocidad de corte, ya sea demasiado lenta o demasiado rápida, es un culpable común, pero está lejos de ser el único. La distancia entre la antorcha y el material que se está cortando, junto con el amperaje, el voltaje y la condición de los consumibles, todo esto afecta también a la escoria. También está el material que se está cortando—su espesor y tipo, grado, composición química, condición de la superficie, lisura (o falta de la misma), y cambios de temperatura al cortar, todo impacta al proceso. En total, hay más de una docena de factores en escena, aunque afortunadamente, sólo tres son críticos: la velocidad de corte, el amperaje y la distancia de separación.
Cuando la velocidad de corte es demasiado lenta, el arco de plasma buscará más material que cortar. La columna del arco aumenta su diámetro, haciendo más ancha la rendija hasta un punto donde la porción de alta velocidad del chorro de plasma ya no sopla el metal fundido del corte. En lugar de esto, el metal se acumula a lo largo del borde inferior de la placa, formando escoria de baja velocidad. Cortar a un amperaje demasiado alto o a una separación demasiado baja puede causar escoria de baja velocidad, pues ambos cambios hacen que más energía del arco de plasma haga contacto con un área dada del metal.
Entonces, la solución es obvia: cortar más rápido. Desafortunadamente, esto tiene su propio conjunto de retos. Si la velocidad de corte es demasiado rápida, el arco no puede mantenerse. Éste cae o se retrasa, detrás de la antorcha, dejando un pequeño cordón duro de material sin cortar a lo largo de la parte inferior de la placa. De muchas formas, esta escoria de alta velocidad es peor que su contraparte de baja velocidad pues es más dura, y usualmente requiere un maquinado extenso para su remoción.
A velocidades sumamente altas el arco incluso puede volverse inestable. Empezará a vibrar hacia arriba y hacia abajo, causando una cola de gallo de chispas y metal fundido. En estas velocidades el arco puede no cortar el metal y también puede detenerse. Un amperaje demasiado bajo o una separación demasiado alta también puede causar escoria de alta velocidad, pues ambos cambios reducen la cantidad de energía del arco.
Además de la escoria de baja y alta velocidad hay un tercer tipo denominado escoria de salpicadura superior. Esto ocurre cuando el metal resolidificado se rocía a lo largo de la parte superior de la pieza de corte. Usualmente es muy fácil de remover. La causa usualmente es una boquilla gastada, una velocidad de corte excesiva o una separación grande. Esto es causado por el flujo arremolinado del chorro de plasma, el cual en un cierto ángulo arroja material fundido frente a la rendija en lugar de hacerlo hacia abajo a través de la misma.
Entre los dos extremos de la escoria de baja y de alta velocidad hay una ventana “exactamente bien”, oficialmente denominada la zona libre de escoria. Esto es clave para minimizar operaciones secundarias en piezas cortadas con plasma. Su ventana variará; generalmente, al usar nitrógeno o aire como el gas de plasma en acero al carbón, encontrará su ventana libre de escoria bastante pequeña; los fabricantes que cortan con plasma de oxígeno tendrán un poco más de margen. Aunque no siempre es fácil encontrar esta velocidad óptima de corte, hay un par de cosas que se pueden hacer.
Haga varios cortes a diversas velocidades de corte y elija la velocidad que produzca el corte más limpio. Las líneas de retardo (pequeñas rugosidades en la superficie del corte) son una buena manera de determinar su velocidad de corte. Si está cortando demasiado lento, verá líneas de retardo perpendiculares al plano de la placa. Si el corte es demasiado rápido, verá líneas de retardo en forma de S inclinadas que van paralelas a la placa a lo largo del borde inferior.
Además, observe el arco (usando la protección ocular adecuada) durante el corte y cambie dinámicamente la velocidad para producir las características óptimas del arco. Para hacer esto, observe el ángulo del arco conforme éste sale de la parte inferior de la pieza de trabajo. Si está cortando con plasma de aire, el arco debe ser vertical conforme sale de la parte inferior del corte. Con nitrógeno o argón/hidrógeno, un arco ligeramente atrasado es mejor, mientras que un arco ligeramente adelantado es mejor con oxígeno.
FIGURA 1. La distancia entre la antorcha y la pieza de trabajo es crítica. Cuando la antorcha está colocada adecuadamente (izquierda), el arco permanecerá angosto. Si está demasiado cerca (derecha) o lejos de la placa, el arco se ensanchará, creando una parte con un ángulo exagerado.
Un consejo final en cuanto a la escoria: refiérase al manual del usuario que viene con su sistema de corte. Los ingenieros de procesos con plasma invierten meses en un laboratorio experimentando con varios parámetros para crear tablas de corte integrales que enlistan velocidades de corte, alturas de corte y amperajes recomendados para muchos tipos y espesores de material. Empiece siempre con estos puntos y ajuste a partir de ahí en incrementos de 10%, tanto hacia arriba como hacia abajo.
Angulosidad del borde
Cortar partes con una angulosidad del borde lo más pequeña posible es otro reto para los fabricantes. Esto ocurre porque un arco de plasma no es perfectamente recto. Esto significa que todo corte de metal con plasma tendrá cierto grado de angulosidad, pero hay maneras de minimizarlo.
Una manera es adaptar sus consumibles y nivel de potencia al espesor de material que necesita cortar, teniendo en mente que niveles de amperaje más bajos y velocidades de corte más lentas le darán menos angulosidad. Además, inspeccione cuidadosamente que no haya daño en sus consumibles, especialmente la boquilla y el escudo. Hasta una pequeña abolladura o mella puede afectar la calidad del corte. Finalmente, asegúrese de que su antorcha esté a la distancia correcta de la placa, después de la perforación y durante todo el corte (vea la Figura 1).
Material torcido
He aquí unas cuantas cosas que puede hacer para no acabar con material y partes torcidas. Primero, programe su software CAM para crear trayectorias de corte que controlen la entrada de calor mediante el enfriamiento de secciones antes de cortar partes adyacentes. Esto es especialmente útil al cortar material muy delgado.
Luego, use el amperaje más bajo posible y los consumibles correspondientes a la velocidad de corte más rápida posible para el espesor del material. Finalmente, si tiene una mesa de agua, mantenga el agua en contacto con el material. Sólo tenga en mente que en muchos materiales, el agua puede afectar la tersura del borde y, en algunos casos, la dureza del borde.
Metalurgia de bordes
Todo material cortado con un arco de plasma mostrará efectos metalúrgicos en los bordes. Después de todo, está introduciendo una cantidad sumamente grande de calor en el metal. Afortunadamente, puede reducir estos efectos mediante la selección del gas.
Si está cortando acero al carbón, usar oxígeno tanto para su plasma como para su gas de protección le dará la mejor metalurgia de borde. Un proceso de oxígeno/oxígeno es especialmente benéfico al cortar agujeros con diámetro menor a 2.5 pulgadas. De hecho, los efectos metalúrgicos son tan pequeños, que este proceso con frecuencia es adecuado para machuelado de roscas.
Además, las partes cortadas con oxígeno son 100% soldables y maquinables, y rara vez se fracturan durante las operaciones de formado. El plasma de aire o de nitrógeno sí causa cierto endurecimiento y nitruración del borde en la mayoría de los aceros, lo cual puede hacer a los bordes quebradizos y crear porosidad durante algunos procesos de soldadura. Afortunadamente, esta capa de nitruro generalmente es delgada, entre 0.006 y 0.010 pulgadas (0.15 y 0.254 mm) de espesor, y es fácil de remover.
Si necesita cortar acero inoxidable, se recomienda una mezcla de gases. Es posible cortar acero inoxidable de un espesor menor a ¼ de pulgada con un borde muy puro usando una mezcla de 5% hidrógeno/95% nitrógeno para el gas de plasma. Secciones de acero inoxidable más gruesas con frecuencia funcionan mejor cuando se cortan con una mezcla de 35% hidrógeno/65% argón; sin importar el espesor, se recomienda un gas de protección de nitrógeno. Otra opción es cortar el acero inoxidable bajo el agua, usando nitrógeno tanto para el plasma como para el gas protector, lo que elimina la capa de óxido que se forma al cortar en el aire ambiental.
Para resumir: use oxígeno si su sistema lo soporta, para la mejor metalurgia de borde en acero al carbón; para el acero inoxidable use una mezcla de hidrógeno/nitrógeno en material menor a ¼ de pulgada, y una mezcla de hidrógeno/argón en material más grueso; siempre use nitrógeno como su gas de protección, sin importar el espesor.
FIGURA 2. El corte de agujeros puede requerir cierta aplicación de prueba y error, pues algunos operadores batallan para evitar agujeros ovalados o cónicos, así como agujeros con metal en exceso a lo largo del radio interior.
Agujeros
Aunque los consejos anteriores mejorarán la calidad del corte en la mayoría de las partes y formas, el corte de agujeros requerirá un poco más de trabajo. La regla empírica es que el diámetro del agujero no debe ser menor que el espesor de la placa, así que si corta placa de ½ pulgada de espesor, buscará cortar agujeros de ½ pulgada de diámetro o más grandes. Sin embargo, incluso cuando hacen esto, los operadores con frecuencia batallan con agujeros ovalados o cónicos, en los cuales la parte superior del agujero es más grande que la inferior (vea la Figura 2).
El plasma de aire siempre producirá un agujero con cierta conicidad natural, no obstante muy pequeña, debido al ángulo de arco atrasado del chorro de plasma. Los sistemas de plasma de alta definición y de definición X producirán una conicidad casi nula.
Como una buena práctica general al cortar agujeros con plasma, perfore la placa a la altura de corte recomendada y use un tiempo de retardo de perforación. El manual de usuario de su plasma usualmente le dirá lo largo que se requiere un retardo. Esto evitará o al menos reducirá el retorno de metal fundido en su escudo y su boquilla.
Un segundo consejo es jugar con el inicio del agujero. Empiece cerca del centro del agujero y no en el radio. Esto asegurará que la protuberancia que se forma durante la perforación ocurra en el metal que está siendo cortado y no en el borde de su agujero. Empezar en el centro tiene una segunda ventaja, y es que le da al arco más tiempo para estabilizarse y le da al control de altura de la antorcha más tiempo para indexarse a la altura de corte antes de llegar al radio. Aunque la mayoría de las máquinas puede producir excelentes agujeros cuando las formas de inicio son rectas y perpendiculares al agujero, las máquinas más lentas se beneficiarán del uso de un inicio radial o curveado (vea la Figura 3).
Idealmente, se busca que el arco se detenga o se apague en la ranura de entrada de 360 grados o más allá. Algún software puede apagar el arco de plasma en el cruce de la rendija de inicio mientras mantiene el movimiento activo, lo cual es la mejor manera de cortar agujeros pues permite una transición más suave del fin del corte y un terrón muy pequeño cuando el arco se apaga.
La velocidad de corte debe ser alrededor del 60% de la velocidad que se usa para cortar el contorno exterior de la parte. Este ajuste de la velocidad de corte producirá alguna escoria de baja velocidad, pero el inconveniente vale la pena pues minimizará la conicidad de los agujeros. Al cortar agujeros con un diámetro menor a 1 ¼ pulgadas, es mejor deshabilitar el control de voltaje del arco y la corrección de altura del voltaje, y en su lugar habilitar la función de altura de perforación y de altura de indexado al corte. Esto se recomienda debido a que la velocidad más lenta usada para cortar agujeros hará que el control de voltaje del arco mueva la antorcha demasiado cerca de la placa.
Un buen punto de inicio
Estos consejos son un buen punto de inicio. Sin embargo, como se mencionó anteriormente, su sistema específico afectará sus resultados finales en un alto grado. Esto se debe a que la capacidad de procesos entre los fabricantes de plasmas y mesas varía ampliamente. Diferencias en el tipo de control de altura de la antorcha, software CAM, junto con la capacidad de movimiento y aceleración de la mesa pueden realmente impactar su resultado final. Aun así, estos consejos y sugerencias es seguro que mejoran la calidad del corte y la forma de los agujeros para quien use plasma, independientemente del tipo—aire, convencional, alta definición, definición X—o marca.
Michelle Avila es gerente de comunicaciones de Hypertherm, 21 Great Hollow Road, Hanover, NH 03755, 603-643-3441, www.hypertherm.com.
About the Author
Michelle Avila
603-643-3441 ext. 1145
About the Publication
Compañías Relacionadas
subscribe now
FMA Communications ha introducido al mercado la edición en Español de la revista The Fabricator. Esta versión consiste del mismo tipo de artículos técnicos y sección de lanzamientos de nuevos productos que actualmente presentan el personal de primera categoría de Fabricator en Inglés.
start your free subscription- Podcasting
- Podcast:
- The Fabricator Podcast
- Published:
- 04/30/2024
- Running Time:
- 53:00
Seth Feldman of Iowa-based Wertzbaugher Services joins The Fabricator Podcast to offer his take as a Gen Zer...
- Trending Articles
Los operadores de prensa dobladora inexpertos hacen indispensable el repensar la seguridad
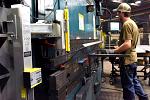
Prescripción para la reducción del desperdicio: arreglo esbelto de las instalaciones
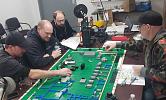
Máquina de corte por láser diseñada para el mercado mexicano
La sierra de doble carro sigue los contornos del tubo perfectamente
La máquina procesadora de placas crea biseles complejos en un solo corte
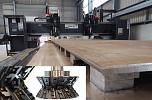
- Industry Events
Pipe and Tube Conference
- May 21 - 22, 2024
- Omaha, NE
World-Class Roll Forming Workshop
- June 5 - 6, 2024
- Louisville, KY
Advanced Laser Application Workshop
- June 25 - 27, 2024
- Novi, MI
Precision Press Brake Certificate Course
- July 31 - August 1, 2024
- Elgin,