Editor-in-Chief
- FMA
- The Fabricator
- FABTECH
- Canadian Metalworking
Categories
- Additive Manufacturing
- Aluminum Welding
- Arc Welding
- Assembly and Joining
- Automation and Robotics
- Bending and Forming
- Consumables
- Cutting and Weld Prep
- Electric Vehicles
- En Español
- Finishing
- Hydroforming
- Laser Cutting
- Laser Welding
- Machining
- Manufacturing Software
- Materials Handling
- Metals/Materials
- Oxyfuel Cutting
- Plasma Cutting
- Power Tools
- Punching and Other Holemaking
- Roll Forming
- Safety
- Sawing
- Shearing
- Shop Management
- Testing and Measuring
- Tube and Pipe Fabrication
- Tube and Pipe Production
- Waterjet Cutting
Industry Directory
Webcasts
Podcasts
FAB 40
Advertise
Subscribe
Account Login
Search
Repensando lo que puede hacer el corte por plasma
Los avances tecnológicos podrían hacerles la vida más fácil a los procesadores de metal grueso
- By Dan Davis
- October 5, 2021
- Article
- Plasma Cutting
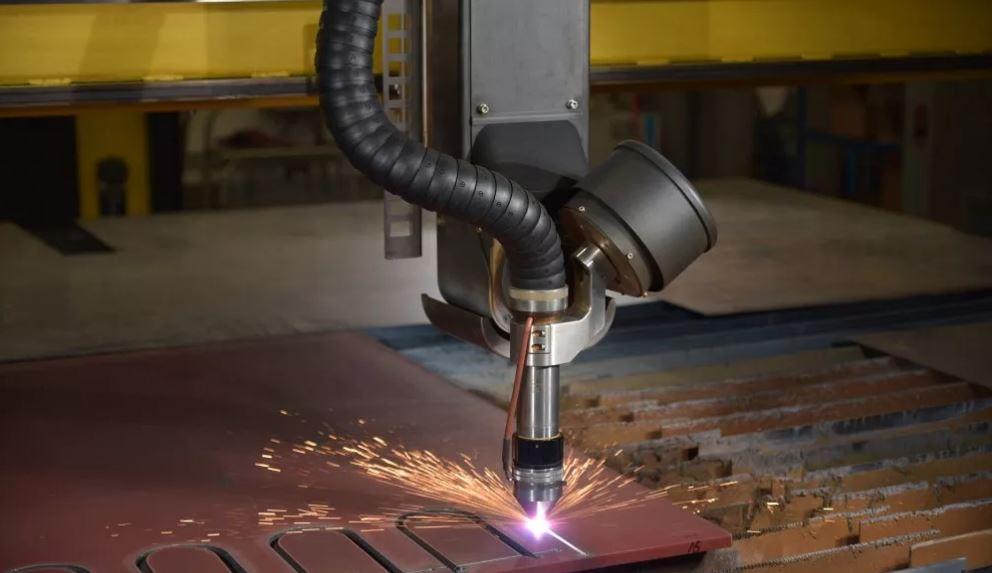
Los avances en la tecnología del corte por plasma les permiten a los fabricantes cortar con plasma materiales a amperajes más altos, al mismo tiempo que minimizan el ángulo de bisel del borde de corte resultante. Debido a que la antorcha se puede inclinar durante el corte, ésta puede compensar el aumento en el ángulo de borde. Esto produce cortes más rápidos al mismo tiempo que mantiene un borde cuadrado y una mejor cilindricidad en agujeros pequeños.
La tecnología del corte por plasma ha avanzado a tal punto que ha forzado a los fabricantes de metal a repensar su uso. El corte por plasma de alta definición brinda un corte con borde más cuadrado que las generaciones previas de la tecnología. En acero suave de 0.25 pulgadas las antorchas de plasma pueden alcanzar velocidades de corte de más de 100 IPM (2.5 metros por minuto). Los sistemas de plasma además pueden producir agujeros listos para tornillo que ayudan a minimizar las actividades secundarias de maquinado una vez que las partes de placa salen de la mesa.
Aun con esos avances, los fabricantes de tecnología de corte por plasma siguen invirtiendo mucho en investigación y desarrollo. Los sistemas de corte láser se están volviendo más potentes y asequibles, por lo que más talleres los están usando para cortar materiales más gruesos de manera más regular. Los chorros de agua siguen siendo una manera adecuada para cortar materiales muy gruesos, y se han emprendido acciones para mejorar la productividad en las máquinas. Eso deja a las compañías de tecnología de corte por plasma tratando de defender sus propuestas como el método de corte preferido para talleres de fabricación y centros de servicio de trabajo pesado.
Estas compañías han usado el tiempo sabiamente. Pensar en una mesa de corte por plasma como una herramienta para procesar sólo acero suave de 0.25 a 2 pulgadas no refleja la realidad actual de la tecnología, especialmente cuando se relaciona con el corte de materiales gruesos no ferrosos. Los fabricantes y los centros de servicio harían bien en preguntarse qué pueden hacer los sistemas de corte por plasma de la actualidad—y quizás de qué podrían ser capaces en el futuro cercano. He aquí algunas preguntas que pueden ayudar a los procesadores de placa a entender lo que la tecnología de corte por plasma tiene para ofrecer.
¿Un procesador de placa tiene que invertir en una fuente de poder de plasma potente sólo para cortar material especial grueso, como metal no ferroso entre 2 y 6 pulgadas?
Los talleres de fabricación y centros de servicio están acostumbrados a procesar materiales gruesos, y usualmente las herramientas de ese trabajo les son familiares. Se usan sistemas de plasma de 200, 300 y 400 amperes para cortar material ferroso y no ferroso de hasta 2 pulgadas. Los sistemas de oxicombustible son los más adecuados para material ferroso con un espesor mayor a 2 pulgadas debido a que el proceso rápido de oxidación, en el cual la superficie del acero es calentada hasta unos 1,800 grados F (982 grados C) y luego golpeada con un chorro de oxígeno para soplar la escoria, produce un corte cuadrado, deja una superficie de corte suave, y crea escoria escasa o nula en el borde inferior. (El oxicombustible solo se las vería difícil cortando metal no ferroso. Por ejemplo, en acero inoxidable, el óxido resultante creado durante el proceso de corte tiene un punto de fusión más alto que el acero inoxidable, lo cual significa que no se está removiendo material. Técnicamente, el oxicombustible podría usarse para cortar material no ferroso, pero esto implica inyectar un polvo rico en fierro a la zona de corte. El polvo de fierro se quema, aumentando la temperatura de reacción, creando una fluidización de la capa oxidada y haciendo posible remover material en la zona de corte. Este corte con polvo se usa de manera muy limitada.) Los chorros de agua son populares debido a que pueden cortar metales muy gruesos, de hasta 1 pie (30.5 cm), pero son relativamente lentos comparados con otros métodos de corte.
¿Qué tal el corte de materiales no ferrosos entre 2 y 6 pulgadas? Dirk Ott, vicepresidente global, sistemas de plasma mecanizado, Thermal Dynamics, dijo que los sistemas de plasma, algunos de los cuales tienen fuentes de poder de 1,000 amperes, cortaban esos espesores de acero inoxidable por allá por la década de 1960. Por supuesto, el problema de la actualidad es que los talleres de fabricación y centros de servicio de trabajo pesado típicamente no cortan materiales no ferrosos de ese espesor con la suficiente frecuencia para garantizar un sistema de plasma tan potente. Es una gran inversión para una compañía que no va a usar la mesa durante todo un turno.
Sin embargo, en meses recientes se introdujo un nuevo nivel de flexibilidad a los sistemas de potencia de plasma para darles a los usuarios la capacidad de alcanzar la salida de corte de 600 a 800 amperes, aun si tienen sólo fuentes de poder de 300 y 400 amperes, respectivamente. Imagínelo como si fuera un taller de fabricación usando dos fuentes de poder de soldadura en paralelo para dar cabida a electrodos de diámetro más grande en busca de una mayor productividad, dijo Ott.
Por ejemplo, un centro de servicio podría tener dos fuentes de poder de 400 amperes alimentando a dos antorchas separadas en una mesa de corte. Ambas antorchas cortan todos los días acero inoxidable de 1.25 pulgadas, y la gerencia de la compañía está satisfecha con la calidad y la producción. Sin embargo, un día llega una orden para cortar algunas partes de acero inoxidable de 4 pulgadas. Mediante el accionamiento de algunos interruptores y el cambio de un cable, el taller puede convertir estos dos sistemas de 400 amperes en un sistema de 800 amperes.
“Usted obtiene flexibilidad con este arreglo. Tiene sus dos sistemas de 400 amperes la mayor parte del tiempo, y sin mucho conocimiento técnico o con la visita de una persona de servicio, puede convertirlos en un sistema grande de 800 amperes”, dijo Ott.
Este tipo de sistema podría ser más atractivo para aquellas compañías que procesan no sólo altos volúmenes de partes de placa en el rango de 0.25 a 2 pulgadas, sino también la orden pequeña ocasional de partes no ferrosas de hasta 6.25 pulgadas. Dichos fabricantes podrían encontrarse en las ramas industriales de generación de energía, contenedores a presión, y procesamiento químico y petroquímico.
Ott agregó que todo operador de alguno de estos tipos de sistemas en los cuales la salida de potencia pueda duplicarse tiene que estar consciente del cambio de consumibles. El lograr una calidad y una velocidad óptimas de corte requiere consumibles diseñados para la aplicación. Cortar a 800 amperes con consumibles diseñados para una salida de 400 amperes dará como resultado cortes de mala calidad y una vida muy corta de los consumibles.
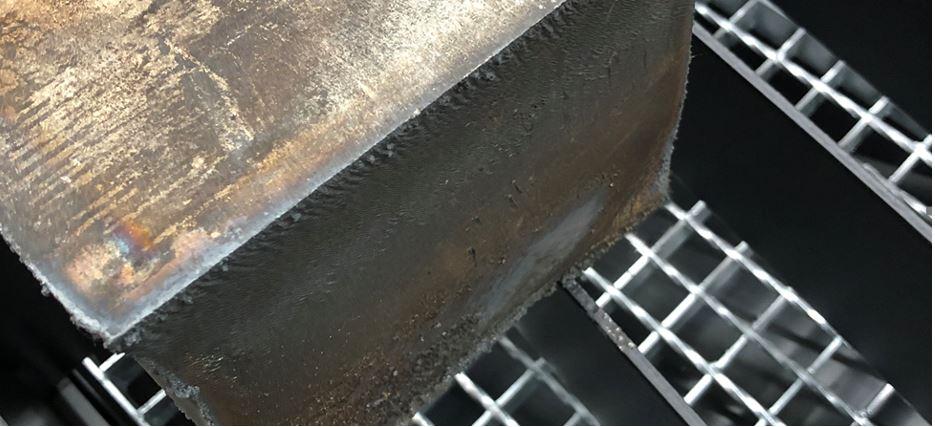
Conectar en paralelo dos fuentes de poder de 400 amperes para crear una salida de 800 amperes permitió el corte de esta sección de 5 pulgadas de espesor de material no ferroso.
Si un procesador de placa está buscando actualizar su capacidad de corte por plasma, ¿tiene que invertir ahora en capacidad futura?
Cuando se trata de invertir en equipo principal, conciliar las necesidades de corte de la actualidad con los posibles requerimientos del futuro es complicado. La mayoría de los talleres de fabricación y centros de servicio tienen un presupuesto, y desean sacarle el máximo provecho sin sacrificar por completo oportunidades futuras.
Ésa es la razón de que los proveedores de tecnología de plasma se hayan cambiado a un enfoque modular en la construcción de sus sistemas de corte. Es muy parecido a los fabricantes de láseres de fibra capaces de aumentar la potencia de sus máquinas mediante la adición de módulos de producción láser. Es una de las razones de que la industria de la fabricación de metal haya visto el reciente aumento en potencias disponibles en máquinas de corte láser.
Steve Zlotnicki, gerente de producto global, sistemas de corte, ESAB Welding & Cutting Products, dijo que una compañía puede comprar un sistema de corte por plasma con una fuente de poder de 200 amperes y tener confianza en que puede actualizar sin cambiar la antorcha, cajas de gas, cables ni mesa. Nuevos módulos de suministro de potencia simplemente se agregan al gabinete con los módulos existentes, y se actualiza la electrónica correspondiente.
“Esto realmente elimina el temor de comprar menos de lo requerido porque obviamente estos sistemas pueden ser caros”, dijo Zlotnicki. “Alguien podría estar bien con el sistema diseñado para cortar 0.5 pulgadas, pero no tiene que preocuparse si llega un proyecto realmente grande para cortar 1.5 pulgadas. La compañía no tiene que pagar otro sistema completo, simplemente actualiza con nuevos módulos”.
Esa actualización podría costar alrededor de la mitad de lo que costaría un nuevo sistema de corte por plasma de mayor amperaje.
¿Qué significa el amperaje avanzado para el corte de material grueso no ferroso?
Más potencia se traduce en velocidades más rápidas de corte en material grueso no ferroso, de acuerdo con Zlotnicki. Una fuente de poder de 800 amperes puede cortar acero inoxidable de 6 pulgadas a alrededor de 8 IPM (20.3 centímetros por minuto), mientras que una fuente de poder de 600 amperes corta el mismo material más o menos a la mitad de esa velocidad.
¿Este aumento en la potencia de plasma hace que el procesador de placa repiense su combinación de gas de plasma/gas de protección?
Tradicionalmente, un taller de fabricación o centro de servicio que corta material no ferroso grueso usa H35—una mezcla de gas de 35% hidrógeno y 65% argón—como el gas de plasma, y nitrógeno como el gas de protección al cortar aluminio y acero inoxidable más grueso que 0.75 pulgadas. Esta combinación ayuda a producir un borde de buena calidad y permite un corte rápido.
Sin embargo, para algunos talleres podría ser momento para una nueva tradición. Ott dijo que un proceso que usa nitrógeno como el gas de plasma y agua común de la llave para protección puede dar como resultado en un proceso de corte 300% más rápido que los sistemas que usan H35 para el gas de plasma, y puede reducir el costo por corte en 20%.
¿Qué significa un sistema de corte por plasma con capacidad de biselado más allá de la función de hacer biseles?
Principalmente, el biselado se asocia con la preparación de soldadura para proyectos de fabricación de uso rudo. Los bordes biselados hacen más espacio para el alambre de soldadura, creando juntas fuertes para soportar peso y cargas considerables. Es por eso que usted ve mucho biselado requerido en aplicaciones asociadas con la rama agrícola, de la construcción, forestal, minera, del petróleo y del gas y naval.
Una de las maneras más eficientes de hacer estos bordes biselados es usar un sistema de corte por plasma con una antorcha de plasma que pueda inclinarse mientras corta la pieza de trabajo. Sin embargo, ¿qué tal si esa capacidad de biselado pudiera usarse fuera de la preparación para soldar?
Zlotnicki dijo que la tecnología de biselado ha avanzado hasta el punto donde puede usarse para minimizar el borde de bisel al cortar con plasma material plano. Por ejemplo, si un fabricante corta acero de 0.5 pulgadas con una fuente de poder de plasma de 200 amperes, ésta va a estar cortando a un poco más de 100 IPM (2.54 metros por minuto). El fabricante además va a ver un ligero bisel de 1 a 3 grados debido a la manera en que el chorro de plasma sigue naturalmente a la antorcha de corte.
Por otro lado, si ese fabricante cortara el mismo material con una fuente de poder de plasma de 400 amperes, podría ir más rápido, pero también aumentaría el ángulo de bisel. Zlotnicki dijo que al ser capaz de inclinar la antorcha de 4 a 6 grados mientras corta con el sistema de 400 amperes, el fabricante puede tener mayores velocidades de corte y algo mucho más cercano a un borde cuadrado.
“Usted realmente consigue aumentar su velocidad y con ello su productividad, al mismo tiempo que corrige el aumento en el ángulo de bisel que normalmente obtendría cuando aplica potencia de más a su material”, dijo Zlotnicki.
La capacidad de biselado también puede usarse para mejorar la calidad de agujeros pequeños. Cuando se aplica un valor de corrección a la cabeza de corte al cortar con plasma un agujero pequeño, se mejora la cilindricidad del agujero. Típicamente, usar una antorcha sin capacidad de biselado en agujeros pequeños podría producir una diferencia de 0.4 a 0.6 mm entre la parte superior y la parte inferior del agujero. Con ajustes hechos por medio de una antorcha de biselado, esa diferencia puede reducirse a 0.1 mm, dijo Zlotnicki.
Hacer más corte de placa es un gran paso para un fabricante o centro de servicio. ¿Qué deben considerar si planean agrandar su negocio de procesamiento de placa?
Un procesador de placa que opera varias mesas de corte por plasma y posiblemente algunas mesas de oxicombustible tiene mucho qué vigilar. La conectividad digital les hace eso más fácil.
Con máquinas capaces de alimentar información de producción en tiempo real a los sistemas de manejo del taller, los dueños y gerentes de compañías saben exactamente lo que está pasando y quién está involucrado. Esta transparencia en el proceso de producción mantiene a todo mundo sin complicaciones y, típicamente, mantiene a todo mundo enfocado en tener partes listas para las fechas de entrega.
Los gerentes de fábrica no tienen que interrumpir noches, fines de semana ni vacaciones debido a que pueden usar sus teléfonos para verificar el estado de la producción de un trabajo específico. El gerente de producción espera los viernes porque pueden reunirse reportes fácilmente con unos cuantos clics. Al agente de compras le complace saber exactamente cuánto material se ha usado y que se han optimizado los nidos de corte en cada placa. El técnico de control de calidad está agradecido de que se recolecte y almacene información en caso de que un cliente tenga una pregunta acerca de una parte y requiera saber sobre el proceso de producción e incluso sobre el lote original del material. Holger Hahn, gerente de productos global, software de aplicaciones, ESAB, dijo que la promesa de la tecnología de Industria 4.0 y la conectividad digital que trae consigo pueden hacer la vida más fácil para todas las partes de un taller de fabricación o centro de servicio de trabajo pesado.
“Primero, si usted puede monitorear algo, puede manejarlo”, dijo Hahn. “Si usted no sabe lo que está pasando, ¿cómo puede mejorar?”.
“Segundo, estos sistemas pueden ayudarlo a evitar tiempo improductivo”, agregó. “Si usted ve el futuro de la tecnología digital, habrá más aprendizaje de máquinas; está creciendo. Habrá más datos que analizar, y será más fácil predecir ciertos eventos que pueden llevar a tiempo improductivo no planeado”.
¿Es una discusión de conectividad digital más para operaciones grandes con múltiples mesas de corte?
Hahn dijo que hasta las operaciones más pequeñas entienden lo que se puede lograr con un panorama más claro de lo que está pasando en la planta de producción y la conectividad con los sistemas de la oficina de atención al público. De hecho, parte de la presión de considerar este tipo de descripción digital de la producción podría venir de compañías de manufactura más grandes que desean que su proveedor de servicios de fabricación y partes sea tan eficiente como ellas. Eso se logra únicamente midiendo las operaciones de producción y emprendiendo acciones para eliminar el desperdicio.
En algunos casos, estos grandes fabricantes de equipo original (OEM, por sus siglas en inglés) envían a sus propios expertos para poner al corriente a los fabricantes de metal en la cadena de suministro sobre las mejores prácticas para convertirse en una empresa digital. Operaciones de fabricación más eficientes les dan a las compañías la oportunidad de ganar más dinero y reinvertir en sus negocios. Los OEM grandes, a su vez, pueden estar seguros de que sus socios en la cadena de suministro no sucumbirán ante las dificultades operacionales que pueden afectar las entregas de partes.
La fabricación de placa de uso rudo podría no ser lo primero en lo que la gente piensa cuando hablan de la manufactura moderna, pero ésta se está volviendo más sofisticada. La tecnología de corte por plasma está evolucionando al mismo ritmo acelerado.
About the Author
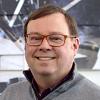
Dan Davis
2135 Point Blvd.
Elgin, IL 60123
815-227-8281
Dan Davis is editor-in-chief of The Fabricator, the industry's most widely circulated metal fabricating magazine, and its sister publications, The Tube & Pipe Journal and The Welder. He has been with the publications since April 2002.
About the Publication
Compañías Relacionadas
subscribe now
FMA Communications ha introducido al mercado la edición en Español de la revista The Fabricator. Esta versión consiste del mismo tipo de artículos técnicos y sección de lanzamientos de nuevos productos que actualmente presentan el personal de primera categoría de Fabricator en Inglés.
start your free subscription- Podcasting
- Podcast:
- The Fabricator Podcast
- Published:
- 04/30/2024
- Running Time:
- 53:00
Seth Feldman of Iowa-based Wertzbaugher Services joins The Fabricator Podcast to offer his take as a Gen Zer...
- Trending Articles
Los operadores de prensa dobladora inexpertos hacen indispensable el repensar la seguridad
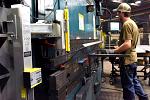
Prescripción para la reducción del desperdicio: arreglo esbelto de las instalaciones
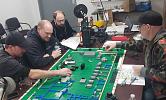
Anidado para la estabilidad del corte láser
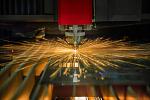
La máquina procesadora de placas crea biseles complejos en un solo corte
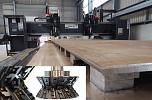
El software guía a los soldadores a través de instrucciones de trabajo
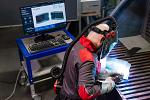
- Industry Events
Pipe and Tube Conference
- May 21 - 22, 2024
- Omaha, NE
World-Class Roll Forming Workshop
- June 5 - 6, 2024
- Louisville, KY
Advanced Laser Application Workshop
- June 25 - 27, 2024
- Novi, MI
Precision Press Brake Certificate Course
- July 31 - August 1, 2024
- Elgin,