Senior Editor
- FMA
- The Fabricator
- FABTECH
- Canadian Metalworking
Categories
- Additive Manufacturing
- Aluminum Welding
- Arc Welding
- Assembly and Joining
- Automation and Robotics
- Bending and Forming
- Consumables
- Cutting and Weld Prep
- Electric Vehicles
- En Español
- Finishing
- Hydroforming
- Laser Cutting
- Laser Welding
- Machining
- Manufacturing Software
- Materials Handling
- Metals/Materials
- Oxyfuel Cutting
- Plasma Cutting
- Power Tools
- Punching and Other Holemaking
- Roll Forming
- Safety
- Sawing
- Shearing
- Shop Management
- Testing and Measuring
- Tube and Pipe Fabrication
- Tube and Pipe Production
- Waterjet Cutting
Industry Directory
Webcasts
Podcasts
FAB 40
Advertise
Subscribe
Account Login
Search
6 pasos hacia la Industria 4.0
La manufactura esbelta y la medición estratégica son los cimientos
- By Tim Heston
- May 10, 2021
- Article
- Shop Management
Frases en boga como el internet industrial de las cosas, el aprendizaje de máquina, la inteligencia artificial y la industria 4.0 han circulado por años entre la prensa de negocios y popular; aparentemente, son el futuro. Entonces ¿cómo será ese futuro? Bueno, la automatización se volverá autónoma, de auto-aprendizaje y auto-corrección, mientras que los humanos manejan las excepciones–los problemas del proceso y el retrabajo—luego realimentan esa información al sistema, el cual aprenderá, se volverá aún mejor, y hará que las excepciones se vuelvan más raras aún.
OK, entonces, ¿cómo se ve eso en la fabricación de metal, y qué puede hacer el taller de fabricación progresista hoy para trabajar hacia ese futuro autónomo? Karl Rapp, gerente de ingeniería en aplicaciones, automatización y electrificación, en Bosch Rexroth Corp., tiene una buena manera de explicarlo. Su explicación pasa por seis pasos, cada uno sustentando a los otros. Entre más robustos sean esos pasos de base, más efectivos y hasta revolucionarios podrían ser los pasos finales.
Considere un fabricante de chapa metálica con el paradigma de la automatización del corte láser, un sistema de manufactura flexible (FMS, por sus siglas en inglés) integral con torres de almacenamiento y recuperación y automatización robótica de descarga. Parecería que ese negocio está bien encaminado hacia la Industria 4.0 y la manufactura totalmente autónoma, ¿cierto?
No necesariamente. Como lo explicó Rapp, la respuesta depende de qué tan firme haya sido creada una base por esos primeros pasos hacia la Industria 4.0. Entre más débiles sean esos pasos, es más probable que fallen los esfuerzos de un fabricante. Entonces, ¿qué implica el primer paso? Curiosamente, éste no se enfoca en sensores, maquinaria, ni siquiera en automatización; más bien, tiene que ver con las personas.
Paso 1: manufactura esbelta
Como dicen por ahí, si entra basura sale basura. Un taller con procesos y procedimientos inconsistentes o ilógicos efectivamente produce datos basura, al menos desde la perspectiva de la analítica de alto nivel. Claro, ciertos datos podrían arrojar luz sobre un problema y quizás probar a todos que el statu quo no es suficientemente bueno. Sin embargo, en este punto podrían bastar los datos tomados de simples observaciones, combinados con una saludable dosis de sentido común. Un operador de máquina de corte láser que camina continuamente por toda la planta para conseguir una herramienta no es algo bueno, y nadie necesita analítica sofisticada para probar el punto.
“Es por eso que establecer reglas de manufactura esbelta y calidad es el primer paso”, dijo Rapp. “Necesita limpiar su lugar de trabajo y asegurarse de que tiene bien establecidas las reglas de la manufactura esbelta”.
La manufactura esbelta empieza con las 5S, pero también incluye escrutinio constante del proceso. A los fabricantes no les pagan por el tiempo productivo de la máquina; les pagan por los productos que embarcan. Por ende, entre más rápido fluyan esos productos del rack de materia prima al muelle de embarque, mejor. Los tamaños excesivos de lote podrían hacer que el tiempo productivo de efectividad global del equipo (OEE, por sus siglas en inglés) en una máquina se dispare hasta las nubes gracias a menos configuraciones de máquina, pero es muy probable esos enormes lotes que tarden en llegar al departamento de embarque.
Los procedimientos de manufactura esbelta de un fabricante, escudriñados y pulidos constantemente, evalúan el rendimiento del material, los tiempos de configuración de la máquina, las reservas de piezas en proceso (WIP, por sus siglas en inglés), y más. Los flujos de valor del taller utilizan cuadros kanban para limitar las WIP, y todo mundo presta una atención constante al flujo.
Rapp agregó que los procesos y procedimientos de la manufactura esbelta deben extenderse corriente arriba, incluyendo el manejo de material, la inspección de material e incluso las relaciones con el vendedor. Alguien que no inspecciona o carga material adecuadamente en un sistema automatizado de almacenamiento y recuperación es algo malo—pero repito, nadie necesita analítica de datos para descubrir el hecho. Los errores del operador ocurren, pero detrás de cada error hay un procedimiento que se siguió incorrectamente, inadecuado, mal documentado y comunicado, o una combinación de los tres. Perfeccionar continuamente esos procedimientos construye los cimientos de todo lo demás.
“Cuando un taller no sigue las reglas de la manufactura esbelta y empieza a reunir y analizar datos del proceso, termina con una curva de campana muy ancha que básicamente es no concluyente”, dijo Rapp. “Puede ser distractora e incluso inútil, y no ayuda a resolver esos problemas básicos”.
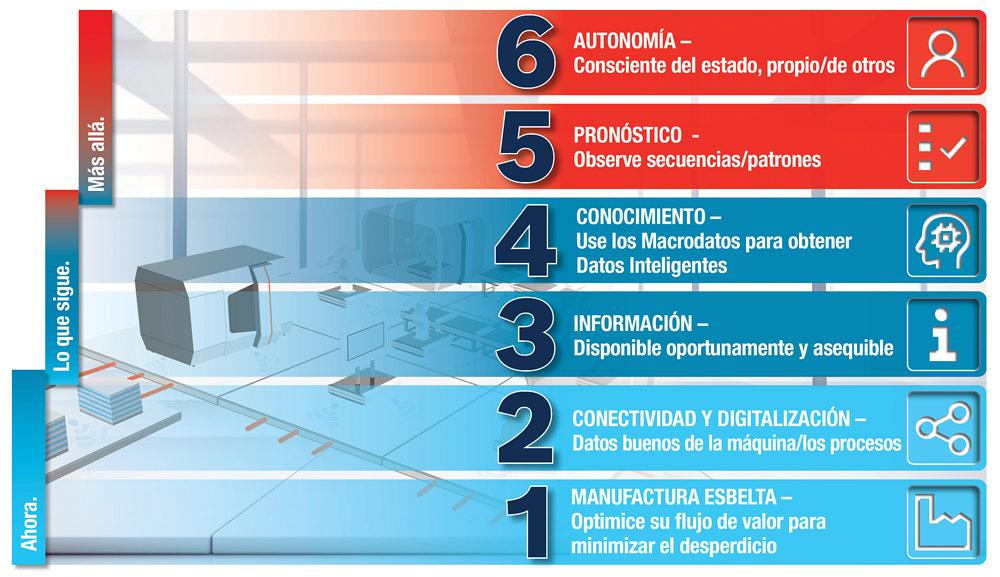
La ruta hacia los ideales detrás de la Industria 4.0 podría seguir seis capas o pasos. Entre más fuertes sean los primeros pasos, más robustos pueden ser los pasos posteriores.
Paso 2: conectividad y digitalización
El paso 2 y los siguientes hurgan en los detalles del monitoreo del proceso y el camino hacia una operación autónoma. Algunas operaciones han llegado al paso 2 y quizás a algunos elementos de los pasos 3, 4 y 5, pero el paso final representa una visión para el futuro.
También sepa que lo que sigue describe a un fabricante hipotético con un sistema FMS de corte láser; los detalles de qué tipo de estrategias de detección funcionarán y cuáles no, por supuesto que depende del diseño de la máquina y de la naturaleza de la operación específica.
Actualmente, muchos talleres de fabricación hacen rastreo del tiempo productivo, con sensores que reportan cuando una máquina se apaga inesperadamente. Sin embargo, como lo explicó Rapp, esto sólo escarba la superficie de la capacidad de la OEE. Es formidable poder detectar automáticamente cuando una máquina que debe estar encendida está apagada, pero ése es solo un primer paso. Las máquinas automatizadas tienen múltiples puntos para medición de la OEE que dividen un proceso largo en sus componentes individuales. Para un sistema FMS láser esto podría incluir carga y descarga de material, así como varios aspectos del comportamiento de la cabeza de corte del láser.
Rapp agregó que lo que son estas mediciones, dónde se toman y cómo ocurren depende del diseño específico de la máquina y de los procesos involucrados. De todas formas, su punto es que los datos de la OEE—el tipo de datos que puede formar el cimiento de los ideales detrás de la Industria 4.0—“necesitan construirse desde cero. Para cada proceso en una máquina o sistema, se necesita un método claro para medir la OEE”.
Otra variable es la frecuencia de los datos, o con qué frecuencia un sensor (o un humano) registra y entrega datos en un formato útil. Cada fábrica reúne una gama de datos a diferentes intervalos. “Piense en los datos que podría recibir sobre la seguridad del trabajador”, dijo Rapp. “Los datos llegan después de concluir un turno, o podría ver datos por la mañana relativos al día anterior. Ésos son datos de frecuencia baja”.
Los sensores que miden el tiempo de ciclo de la máquina podrían registrar puntos de datos con separación de unos cuantos minutos, después de que concluye cada ciclo. “Éstos serían datos de frecuencia media”, dijo Rapp.
Los datos de frecuencia alta —los cuales podrían implicar potencia láser, presión del gas auxiliar, o varios aspectos de la operación del sistema—podrían llegar en unos cuantos milisegundos. Estas frecuencias de datos necesitan estar coordinadas con otras variables del proceso para que el análisis de datos pueda comparar manzanas con manzanas.
Para que los datos se vuelvan útiles, un fabricante necesita contexto. Una máquina de corte láser podría tener infinidad de puntos de datos que colecta, “pero todos esos datos no significan nada a menos que pueda relacionarlos todos con el corte en sí”, dijo Rapp. “¿Qué parte se estaba haciendo en la máquina? ¿Qué información está llegando del sistema de ejecución de manufactura (MES, por sus siglas en inglés? ¿Cuál fue la marca de fecha y hora?”
Piense en cada punto de datos que un sensor colecta como un cuadro congelado en el tiempo. Tiene todas las complejidades del desempeño de la máquina que el sensor está recolectando, pero también tiene lo que la máquina está haciendo—es decir, el trabajo que está cortando.
El paso 2 también incluye la conectividad. Insisto, los clientes compran productos o partes, no tiempo productivo de la máquina, por lo que una máquina o sistema—incluso uno tan grande como un sistema moderno FMS de corte láser—es sólo una pieza del rompecabezas. Los fabricantes tienen muchas formas de conectar sistemas diferentes usando protocolos comunes como el OPC. “Aquí es importante saber”, explicó Rapp, “qué está haciendo el marcado de hora y cómo se está documentando cada punto de datos. ¿La marca de hora ocurre en el controlador de la máquina o en PC, o se está haciendo en una base de datos separada? Habrá diferencias pequeñas de tiempo, y esas diferencias de tiempo se vuelven sumamente importantes pues tienen que ver con cuándo ocurre exactamente una falla y por qué”.
Agregó que el registro no tiene que hacerse necesariamente en tiempo real en el controlador; la frecuencia ideal depende en realidad de qué están detectando exactamente los sensores. “De todas formas, quienes están analizando los datos necesitan saber cómo es el marcado de la hora, para unificar criterios”.
Rapp llamó a la frecuencia de datos “una travesía” que usualmente empieza a intervalos poco frecuentes. “No se empieza colectando datos a una frecuencia alta”, dijo, y agregó que todos esos puntos de datos podrían inundar los esfuerzos con información que no se necesita, al menos no todavía. “Las operaciones típicas empiezan con datos de frecuencia baja, luego aumentan a frecuencias de recolección de datos cada vez más altas”.
Mientras más robusto sea el paso 2, más efectivos se vuelven los niveles superiores. Si las medidas son fallidas o inadecuadas, todo lo demás que venga después se vuelve difícil, incluso inútil. Rapp agregó que los avances en la tecnología de redes harán la recolección de datos aún más robusta y, por consiguiente, se expandirá todo lo que sea posible en pasos posteriores; esto incluye la infraestructura de la red. Las redes alámbricas e inalámbricas de la actualidad, como por ejemplo LAN y WLAN, “con frecuencia tienen límites para lograr la huella digital de datos requerida. Sin embargo, el Ethernet en tiempo real programado y la 5G inalámbrica eliminarán estos obstáculos en la fábrica del futuro”.
Paso 3: información
Los datos por sí solos no pueden incentivar el cambio o la mejora, pero puede haber mejora después de que los datos se analicen, se pongan en contexto y se traduzcan a información aprovechable.
“En este punto se tienen los datos”, dijo Rapp. “Ahora se aplican los principios de la OEE. Se ve la salida potencial total de una máquina. La máquina produjo partes buenas, partes malas y algunas partes que se desconoce si son buenas o malas. La meta es eliminar las partes desconocidas, aumentar las buenas y minimizar las malas”. Ahora bien, el análisis puede relacionar la información de las partes buenas y de las partes malas con otra información del proceso. Parte de esta información al principio viene de una búsqueda manual, ya sea la posición del material sin procesar, la presión del gas u otros elementos que podrían venir directamente de la máquina, del software o, en particular, del operador de la máquina.
“Los operadores de máquina tienen conocimiento”, dijo Rapp. “Ellos observan el proceso, y podrían haber tomado notas del proceso sobre comportamientos específicos del corte o de la formación de pestañas en las partes, u otras estrategias de anidado acerca de las cuales debe saber el programador”.
Si agrega esta información a información relacionada con el marcado de la hora—las condiciones de corte, el flujo de gas, la presencia de humedad (del gas auxiliar, de un ambiente húmedo, etc.) y otros parámetros del proceso—usted empieza a construir una base de datos. Eventualmente, esa base de datos tendrá un registro digital de cada proceso de manufactura y parte producida”, dijo Rapp.
Paso 4: conocimiento
“Una vez que relacionamos la información y la usamos para sacar una conclusión y una solución, eso es conocimiento”, dijo Rapp. “Este conocimiento luego puede documentarse en una base de datos o en otro sistema donde la gente pueda recuperarlo y usar la solución para resolver problemas similares”.
Esta información tampoco puede ser un secreto. “Si usted sólo tiene dos personas en toda una compañía que accedan a la información y la usen para resolver problemas, eso nunca funcionará”. Todos, o al menos la mayor cantidad posible de personas, necesitan poder acceder al conocimiento—ya sea que esté en un sistema de ejecución de manufactura (MES, por sus siglas en inglés) o en otro sistema—y estar suficientemente familiarizados para analizar los datos para resolver problemas o mejorar procesos.
Y como en el paso 3, donde reunir información se vuelve más y más automatizado con el tiempo, el conocimiento obtenido en el paso 4 empieza como un proceso manual y luego, mediante el aprendizaje de máquina, se vuelve más automatizado. Eventualmente, la operación automatizada empieza a adoptar cualidades autónomas.
Es aquí donde la computación de borde y de nube entra en escena. La mayoría de los problemas en los procesos de manufactura son sensibles al tiempo, de ahí la importancia de la marca de hora con cada punto de datos. Esto, dijo Rapp, es la razón de que la naturaleza complementaria de la computación de borde y de nube sea tan crítica. Muy simplificado, la computación de borde (edge computing) usa la potencia de las redes neurales de un servidor de nube, pero en una computadora o sistema de control local.
Considere una alimentación de video desde una cámara inspeccionando partes cortadas conforme éstas salen del sistema FMS, donde (sólo por usar un ejemplo hipotético) hay robots que toman las partes cortadas y las ponen en una banda transportadora. “En este caso, es muy difícil transmitir video en tiempo real en la nube”, dijo Rapp, “por lo que uso un dispositivo de computación de borde que ejecuta el modelo de aprendizaje de máquina de inspección por visión que está conectado directamente a la cámara”.
Los técnicos y operadores trabajan con el sistema de analítica de visión o máquina para enseñar las variables críticas de una operación, como qué es el borde de una parte buena contra el borde de una parte mala, y cuáles son las ventanas de tolerancia aceptables para qué parte. Cada parte podría tener un código QR grabado por láser, el cual le permitiría al sistema correlacionar la observación de la calidad (condición del borde) con la información disponible de la operación del trabajo, que incluye los detalles completos sobre cada proceso corriente arriba, entre ellos el inventario de materia prima de donde vino.
Entre más conocimiento tenga un sistema, mayor será el potencial para más automatización con aprendizaje de máquina. Y el ideal para la base de conocimiento “digital” de la máquina es volverse cada vez más amplia, incorporar tantos datos e información que la analítica lograda con el aprendizaje de máquina pudiera determinar soluciones que la gente no habría considerado de otra manera.
Paso 5: Pronóstico
Una vez que logra el aprendizaje de máquina, “entonces puede ver las curvas de adónde se dirige”, dijo Rapp. “Puede predecir la trayectoria”. ¿Las condiciones están empeorando? Y de ser así, ¿cuándo se volverán tan malas que las partes empezarán a estar fuera de tolerancia? Un buen pronóstico le dirá.
Como con el paso 4, el pronóstico puede ser manual al principio, con técnicos analizando datos actuales e interpolándolos con software para predecir el comportamiento futuro. Sin embargo, conforme evoluciona el aprendizaje de máquina con registro y análisis de datos cada vez más en tiempo real, los sistemas en sí pueden hacer estos pronósticos e implementar la acción correctiva antes de que ocurran los problemas o apagar (o alterar el curso de alguna otra manera) cuando se establece cierto límite (como por ejemplo, la tolerancia de la calidad de un borde para un material específico o para un lote de partes).
Paso 6: autonomía plena
Este paso, dijo Rapp, es una visión de cómo podría verse una planta de fabricación con una implementación completamente madura de la Industria 4.0. Las percepciones populares de una planta de manufactura inteligente con máquinas “conectadas” plantean imágenes de equipo de fabricación que se comunica a lo largo de todos sus flujos de valor, con información fluyendo del corte láser al doblado, inserción de herrajes y ensamble final.
Sin embargo, no es así como lo describe Rapp. “Imagine que tengo una planta de manufactura, y la única conexión que tengo entre una máquina y otra es la pieza de trabajo en sí”. Rapp aclaró que “al usar Ethernet en tiempo real para intercambio programado de información confiable, todas las máquinas están conectadas a un sistema central MES. El MES del futuro usará métodos de aprendizaje de máquina y los datos digitales para decisiones inteligentes de flujo de valor en tiempo real”. Sin embargo, las máquinas ya no tienen que hablar entre sí directamente—sólo el MES, el “cerebro” del taller de fabricación del futuro.
Rapp ve una planta totalmente autónoma que se vuelve mucho más flexible, no limitada a departamentos de procesos específicos o arreglos de flujo de valor rígidos. En la planta conectada, todos los materiales requeridos y piezas de trabajo seguirán la ruta que haga mejor uso de toda la capacidad disponible de la operación. Las rutinas de trabajo podrían cambiar sobre la marcha conforme los vehículos de guiado automático (AGV, por sus siglas en inglés) muevan material, herramientas y partes cortadas a donde esté la capacidad de procesamiento, exactamente cuando se necesiten.
Imagine una pila de piezas cortadas con láser que es llevada en un AGV y que llega a una prensa dobladora automatizada, la cual, después de escanearla, abre una conexión al MES con redes neurales, el “cerebro” de la planta. El cerebro revela la información del producto y del cliente desde el MES, pero también revela datos de las máquinas corriente arriba, previamente compartidos cuando éstas procesaron la parte, así como información de un sistema de visión que detecta la parte actual esperando en el AGV. Sabiendo todo esto, el cerebro ordena a la prensa dobladora que tome la mejor acción posible.
Quizás las variables de proceso de la operación de corte estaban ligeramente fuera de la norma, o tal vez la pieza se anidó con el grano en lugar de contra el grano de la chapa metálica. Tal vez la pieza cortada, debido a la liberación de esfuerzo después de ser cortada del esqueleto, no esté del todo plana. La máquina conectada ajusta el proceso de doblado para que sea adecuado, afinando todo desde la secuencia de doblez y la selección de sujetador del robot, hasta las trayectorias que sigue el robot para orientar y formar la pieza de trabajo. En un mundo autónomo, las máquinas se configuran ellas mismas.
Éstas lo hacen aprovechando el aprendizaje de máquina y la analítica automática, conocimiento construido sobre lo que Rapp denomina una “huella digital continua” conforme la pieza pasa por cada paso de manufactura. Esto, al final de cuentas, es la manera en que una fábrica se vuelve inteligente.
About the Author
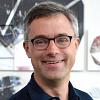
Tim Heston
2135 Point Blvd
Elgin, IL 60123
815-381-1314
Tim Heston, The Fabricator's senior editor, has covered the metal fabrication industry since 1998, starting his career at the American Welding Society's Welding Journal. Since then he has covered the full range of metal fabrication processes, from stamping, bending, and cutting to grinding and polishing. He joined The Fabricator's staff in October 2007.
About the Publication
Compañías Relacionadas
subscribe now
FMA Communications ha introducido al mercado la edición en Español de la revista The Fabricator. Esta versión consiste del mismo tipo de artículos técnicos y sección de lanzamientos de nuevos productos que actualmente presentan el personal de primera categoría de Fabricator en Inglés.
start your free subscription- Podcasting
- Podcast:
- The Fabricator Podcast
- Published:
- 04/30/2024
- Running Time:
- 53:00
Seth Feldman of Iowa-based Wertzbaugher Services joins The Fabricator Podcast to offer his take as a Gen Zer...
- Trending Articles
Los operadores de prensa dobladora inexpertos hacen indispensable el repensar la seguridad
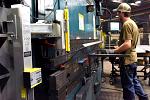
Prescripción para la reducción del desperdicio: arreglo esbelto de las instalaciones
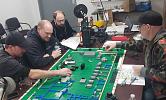
Anidado para la estabilidad del corte láser
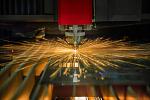
La máquina procesadora de placas crea biseles complejos en un solo corte
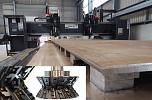
El software guía a los soldadores a través de instrucciones de trabajo
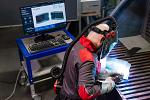
- Industry Events
Pipe and Tube Conference
- May 21 - 22, 2024
- Omaha, NE
World-Class Roll Forming Workshop
- June 5 - 6, 2024
- Louisville, KY
Advanced Laser Application Workshop
- June 25 - 27, 2024
- Novi, MI
Precision Press Brake Certificate Course
- July 31 - August 1, 2024
- Elgin,