Senior Editor
- FMA
- The Fabricator
- FABTECH
- Canadian Metalworking
Categories
- Additive Manufacturing
- Aluminum Welding
- Arc Welding
- Assembly and Joining
- Automation and Robotics
- Bending and Forming
- Consumables
- Cutting and Weld Prep
- Electric Vehicles
- En Español
- Finishing
- Hydroforming
- Laser Cutting
- Laser Welding
- Machining
- Manufacturing Software
- Materials Handling
- Metals/Materials
- Oxyfuel Cutting
- Plasma Cutting
- Power Tools
- Punching and Other Holemaking
- Roll Forming
- Safety
- Sawing
- Shearing
- Shop Management
- Testing and Measuring
- Tube and Pipe Fabrication
- Tube and Pipe Production
- Waterjet Cutting
Industry Directory
Webcasts
Podcasts
FAB 40
Advertise
Subscribe
Account Login
Search
La fina línea de las 5S efectivas en la manufactura esbelta
La gestión no debe ser insuficiente ni excesiva en un taller de fabricación
- By Tim Heston
- December 8, 2019
- Article
- Shop Management
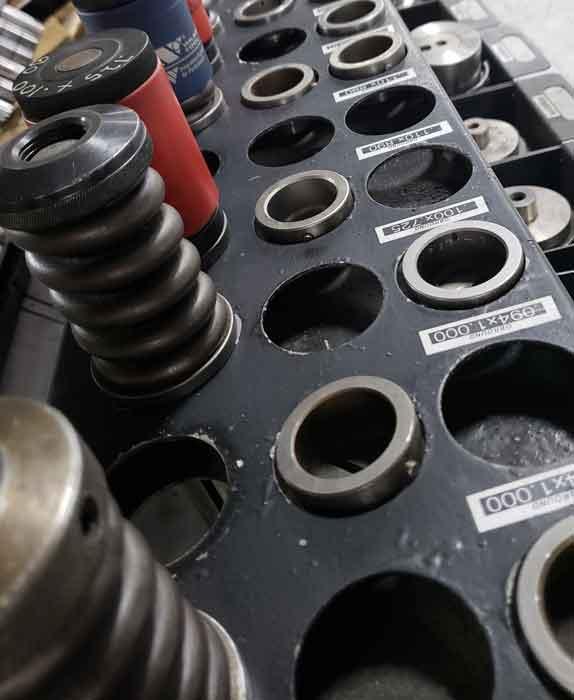
Este rack de punzones, claramente organizado y continuamente mejorado, es de un fabricante que ha mantenido las 5S por más de una década.
Clasificación, orden, limpieza, estandarización y disciplina. Los elementos del método de las 5S suenan tan lógicos, tan sencillos. ¿Por qué algún fa-bricante no trabajaría para mantener un sistema así? Sin embargo, no es tan raro que un programa 5S fracase, especialmente en el mundo altamente variable del taller de fabricación de metal que procesa un trabajo único tras otro.
¿Por qué los talleres trabajan con los primeros cuatro elementos, pero fallan en el quinto? ¿Por qué no pueden mante-nerse las 5S? Para develar una perspectiva, The FABRICATOR habló con Tony Manos, fundador de 5S Supply, Flossmoor, Illinois, cuyo negocio se enfoca en el proceso 5S, y Profero Inc., una consultoría con sede en Frankfort, Illinois.
Por supuesto, cuando le preguntamos por qué fallan las 5S, Manos nos dio la res-puesta esperada: falta de soporte y buena disposición de gestión. “Los líderes de las compañías necesitan involucrarse activamente y darle a la gente el tiempo y las herramientas que necesitan para tener éxito”.
Luego se detuvo brevemente. “Sí, lo sé. Todo mundo dice lo mismo”.
Manos agregó que eso se dice todo el tiempo debido a que es cierto, por supuesto; la clave está en analizar minuciosamente las tuercas y tornillos del “soporte de los líderes” para que mantener las 5S sea una realidad. ¿Cómo hace esto un fabricante? Como lo describió Manos, se requiere encontrar el equilibrio óptimo, una zona tipo “Risitos de Oro” entre nivel de gestión insuficiente y nivel excesivo.
Gestión insuficiente
Cuando Manos entra a una planta, casi inmediatamente ve signos de gestión insuficiente de las 5S. Los signos son bastante obvios: un tablero de siluetas con la mayoría de las herramientas faltantes cerca de un banco de trabajo con varias herramientas desparramadas; un cajón lleno de punzones y llaves Allen por todos lados, y nada con etiquetado claro. Puede que parte de esto tenga que ver con falta de una gestión práctica, especialmente al tratar con empleados que se dicen a sí mismos “desordenados por naturaleza”.
“Esto puede ser difícil, especialmente cuando se tiene un excelente operador”, dijo Manos. “Y la persona puede que sea sumamente productiva, pero pregúntese, ‘cuando contrata a alguien, ¿le gustaría contratar a alguien desordenado o a alguien ordenado?’ Sí, puede tener gente desordenada que sea productiva, pero también tiene gente productiva que es ordenada. Y si tuviera la opción de contratar una de ellas, probablemente elegiría a la persona ordenada”.
Esto tiene que ver con la capacidad de una persona de trabajar en un equipo. Un empleado con una estación de trabajo o escritorio sumamente desordenado puede que sea productivo, pero ¿qué tal si surge una emergencia y no puede acudir al trabajo al día siguiente o toda la semana que sigue? Una estación de trabajo desordenada puede ser algo familiar para el propietario, pero es un misterio caótico para el sustituto que necesita mantener el flujo de trabajo en ausencia de la persona.
Una gestión insuficiente puede involucrar una sencilla falta de supervisión, pero Manos advirtió que las 5S tampoco deberían imponérsele a la gente por la fuerza. Lo más frecuente es que una falta de supervisión en realidad no sea el problema. El asunto realmente surge de una falta de estructura que permita un flujo de trabajo eficiente.
Conociendo cómo fluye el trabajo
Muchos talleres usan las 5S para mojarse las puntas de los pies en la alberca de la manufactura esbelta. Después de todo, no todas las herramientas de la manufactura esbelta funcionan en el taller, pero las 5S es algo bastante universal, entonces, ¿por qué no empezar ahí?
Manos está de acuerdo en que las 5S es un buen inicio, pero el reto es que si el flujo general de partes es altamente variable, rayando en lo caótico, una estación de trabajo a la que se aplica 5S podría ser insuficiente para controlar el caos.
Imagine una estación de ensamble diseñada para manejar cada parte que requiera ensamble en todo el taller de fabricación. El tamaño de la pieza de trabajo, la variedad de herramientas, la ergonomía del ensamble y más, todo eso cambia varias veces en un turno. Debido a que los operadores tienen que manejar tantas herramientas, encuentran difícil mantener las herramientas ordenadas. Diseñar una estación de trabajo así para la máxima eficiencia es un verdadero desafío, si no un evidente imposible, debido a que es demasiado difícil predecir qué herramientas necesitará un operador y en qué momento.
Por lo tanto, durante el turno los operadores corren de aquí para allá alrededor de sus estaciones de trabajo, llegando por una herramienta en un área y otra herramienta en un área lejana en el otro lado del banco de trabajo. Un operador necesita una herramienta inusual que está en un armario central de herramientas. Así que camina hacia allá y encuentra un tablero de siluetas con espacio para la herramienta—sin embargo, no hay herramienta ni registro de quién tomó esa herramienta. Entonces empieza la cacería frenética, el ensamblador se atrasa, y se olvida de regresar las herramientas a donde van. ¿Y por qué molestarse? Tiene que manejar demasiadas herramientas, tratar de mantener las cosas ordenadas sólo lo hace ir más lento.
“Es aquí donde entra en escena el mapeo de flujo de valor, así como la matriz de familias de procesos, los cuales pueden ayudar a los talleres a entender mucho sobre cómo es realmente el flujo de trabajos”, dijo Manos. Muchos dicen que todo lo que hace el taller es absolutamente diferente, pero con frecuencia no es tan diferente como se cree. Usualmente hay una manera de agrupar trabajos similares”.
En la fabricación a la medida, muchas partes fluyen por una ruta similar: punzonado o corte láser, desbarbado de parte plana, soldadura y rectificado, con inserción de tornillería intercalada dependiendo de la geometría de las partes o de los requerimientos del trabajo. Una parte puede requerir prensas dobladoras con diferentes longitudes de cama, herramientas o tonelaje; las partes más gruesas pueden requerir un láser de una potencia mayor. Sin embargo, muchos de los patrones de ruteo son claros, y a partir de ahí pueden surgir nuevas formas de flujo de producto a través de la planta.
Mejor flujo, más oportunidades de 5S
Manos agregó que nuevos patrones de flujo deben crear ruteos dedicados para ciertas familias de productos o trabajos “repetidos”—quizás sólo 30 o 40 por ciento del trabajo total. Sin embargo, desde una perspectiva 5S, dividir el flujo de trabajo ayuda a simplificar el proceso 5S. Ya no ocurre que cierta estación de trabajo requiera todas las herramientas existentes. Si reduce el número de herramientas requerido más fácil será definir las herramientas usadas comúnmente, y más herramientas pueden dedicarse a estaciones de trabajo específicas—sin la pérdida de tiempo que implica caminar a un armario de herramientas.
Menos herramientas también significa que pueden dedicarse más recursos a presentar aquellas herramientas a ensambladores y operadores para hacer sus trabajos más fáciles. Manos describió estaciones de trabajo en una línea de alta mezcla de productos que, entre las herramientas menos usadas, tenía cuatro herramientas comunes que estaban suspendidas en el aire con balanceadores de carga tipo resorte.
“Sí, cada balanceador de carga cuesta unos cuantos cientos de dólares”, dijo Manos, “pero compare eso contra el tiempo que gastaban los operadores antes buscando herramientas. Ahora, cuando necesitan la herramienta, pueden alcanzarla y jalarla. Cuando terminan, las herramientas regresan a su sitio arriba de la estación de trabajo”.
Minimizar la variación del flujo de partes también abre más posibilidades de organización. Manos describió un taller con un trabajo repetitivo que fluía hacia una celda de ensamble dedicada. El trabajo incorporaba cientos de variantes de productos diferentes, tantas que era imposible diseñar una celda de ensamble con todas las herramientas para cada parte. Entonces, en este caso se entregaban kits de piezas de trabajo al lado de una charola llena de herramientas requeridas para el ensamble.
Organizar el flujo reduce la variabilidad en la estación de trabajo, lo cual hace más fácil organizar, limpiar y perfeccionar con el tiempo. Manos habló de usar color y símbolos donde se pudiera. Por ejemplo, las herramientas para un tablero de siluetas específico pueden tener una cinta o banda elástica de un color específico que concuerde con el color del tablero, para que todo mundo sepa qué herramienta exacta—ya sea mazo, martillo, micrómetro, o cualquier otra cosa—va con qué tablero de siluetas.
Los contenedores para tornillería pueden tener un color específico y una imagen de la tornillería que debe ir dentro, acompañada por el nombre real de la tornillería en el contenedor. Siempre tiene que haber ahí texto de apoyo para daltónicos y para diferentes elementos que se ven similares, como tornillería de tamaños similares con roscas diferentes.
Gestión excesiva
Manos recalcó que estas y otras herramientas de comunicación visual pueden funcionar de maravilla, pero que tienen que facilitarles la vida a las personas que las usan.
“Algunas tienden a hacer las cosas mucho más complejas de lo que tendrían que ser”, dijo Manos.
Un buen ejemplo son los códigos de colores complejos. La mayoría de quienes han trabajado en la manufactura sabe el significado de las líneas amarillas en el piso que muestran carriles de tráfico, celdas de trabajo y rutas de salida. “Sin embargo, entré en esta planta y en el piso también vi líneas de color gris claro y gris oscuro. Pregunté qué significaban y me dijeron ‘bueno, el gris claro es por donde se puede caminar y el gris oscuro es donde se está haciendo trabajo’. Luego pregunté, ‘¿no pueden poner simplemente las líneas amarillas ahí?’”.
Éste es un ejemplo que Manos describió para ilustrar un nivel excesivo de gestión 5S. Lo mismo aplica para esquemas, etiquetas y sistemas de rastreo con códigos de colores complicados. De hecho, los esquemas y sistemas de rastreo 5S excesivamente complicados con frecuencia actúan como un “curita” para un problema de consistencia más profundo en preproducción o en producción.
Considere el empuje de la industria hacia una planta de producción libre de papel. Digamos que el taller desea volverse libre de papel debido a que toma años reunir toda la papelería en una hoja de operación. Entonces ocurre lo aparentemente inevitable: el cliente tiene un cambio de último minuto, por lo que personal de la oficina acude a la planta de producción con nuevas instrucciones y revisiones, rogando que el operador aún no haya comenzado el trabajo.
Manos dijo que en muchos casos, volverse libre de papel puede agregar un enorme valor, particularmente si los mercados a los que atiende un taller demandan rastreabilidad, o si las órdenes del cliente cambian a medio proceso. Sin embargo, los gerentes de planta también deben ver el panorama completo. Si los clientes cambian órdenes en el último minuto, ¿podría algún mecanismo en preproducción captar esos cambios antes de que se liberara la orden?
“De manera similar, si los clientes están llamando para verificar órdenes, ¿por qué están llamando? Preguntó Manos. “Y por supuesto, es bueno acceder a un trabajo con unos cuantos clics, pero ¿sabe usted de qué otra manera puede verificar un trabajo? Puede ir a gemba, es decir, puede ir a la planta de producción y verlo usted mismo”. Y si tarda años en encontrar un trabajo en la planta de producción, quizás la planta tenga demasiadas piezas en proceso (WIP), y tenga que atenderse un cuello de botella u otro problema relacionado con el flujo de trabajo.
Manos enfatizó que incluso después de hacer estas preguntas, volverse libre de papel sigue siendo el camino a seguir. Depende de las necesidades de la compañía y de los mercados que ésta atiende, pero también debe depender de lo que haga la vida más sencilla y más fácil para los operadores de primera línea.
Mientras menos complicada y más clara sea la información importante—es decir, la información que le dice a alguien qué hacer después y cómo—más eficiente puede ser un operador y una estación de trabajo, lo cual tiene un impacto directo en cómo se mantienen las 5S. Esto puede que implique un paquete de trabajo sencillo con código de colores, siempre puesto en un área definida en un tablero de siluetas; o puede que incluya el escaneo de un código de barras y el uso de una laptop o tablet para acceder a la información del trabajo.
Sin embargo, ¿qué tal si un operador tiene que escanear varios elementos en diversas etapas de fabricación o ensamble? “En este caso, ¿qué valor agrega esto?” Preguntó Manos, y agregó que podría agregar valor si los clientes requieren rastreabilidad, o si medir ciertos procesos es decisivo para hacer las cosas más eficientes. Sin embargo, para evitar el desperdicio, vale la pena al menos hacer siempre la pregunta.
Manos describió otro ejemplo de un taller donde la información para los paquetes de trabajo para un ensamble específico fue reorganizada por alguien en la oficina frontal. “Esa persona decidió organizar alfabéticamente todas las carpetas en el sistema de cómputo, pero luego les preguntamos a los operadores cómo organizarían la información, y nos dijeron que organizarla por nombre del cliente les funcionaba mejor”.
Esto trae a relucir lo que Manos dijo que era un signo indicador de que un programa 5S tiene exceso de gestión. Nadie se molestó en preguntar al personal de primera línea lo que les funcionaría mejor.
Estrategias de auditoría
Sin embargo, agregó que las 5S debe ser un esfuerzo colaborativo que involucre no sólo a la gente de primera línea en un departamento, sino a la gente de todos los niveles de una organización. Ésa es la razón de que los mejores procedimientos de auditoría 5S regularmente involucran a las personas de otras áreas del negocio que pueden ver un espacio de trabajo con otra perspectiva.
Por ejemplo, alguien en soldadura podría ver la organización de herramientas de punzón en el departamento de corte. Cada herramienta superior e inferior tiene su lugar en un cajón interior completo con cortes en hule espuma, lo que hace imposible para alguien regresar una herramienta de punzón al lugar equivocado. El soldador apreciaría esto, pero también puede que considere que el etiquetado de herramientas es un poco enigmático. ¿Serían comprensibles para alguien nuevo en el departamento de punzonado? ¿Hay una manera fácil de hacer las etiquetas más claras sin hacer las cosas menos eficientes para quienes no necesitan aclaraciones? Quizás sí, quizás no; pero debido a que alguien de otro departamento está dirigiendo la auditoría 5S, al menos se está haciendo la pregunta.
Con relación a esas auditorías, los incentivos equivocados pueden crear problemas y conducir a una eventual desaparición de 5S. Manos visitó una compañía donde las revisiones del desempeño de los supervisores dependían parcialmente del estado de 5S en sus departamentos. “Recuerdo haber visto el resultado de una auditoría que mostraba 85 por ciento, y vi la estación de trabajo”, dijo Manos. “No había manera de que esa estación de trabajo hubiera obtenido ese puntaje de auditoría. Entonces investigamos un poco más, y descubrimos que el supervisor dio esos puntajes debido a que no quería verse mal”.
Como explicó Manos, hacer las 5S parte de las revisiones de desempeño no es malo en sí, pero basarlas en el puntaje solo desvía la atención de lo que realmente importa: la mejora. “Les dije, ‘enfoquémonos en la mejora en lugar de hacerlo sólo en el puntaje’”. De muchas maneras, es el cambio en el puntaje, y no el puntaje en sí, lo que realmente importa.
Por supuesto, los puntajes tampoco deben sacarse del mapa. Si se eliminan, el proceso de auditoría se vuelve menos útil, dándole a las 5S más posibilidad de falla. Ciertamente, algunos elementos de una estación de trabajo pueden contarse y medirse, pero algunos aspectos de las 5S son inherentemente subjetivos.
Es aquí donde entra a escena la “calibración del auditor”. “Para esto, identificamos a los auditores, les damos una hoja, y los dejamos que hagan la auditoría solos, evaluando las mismas estaciones de trabajo, luego regresamos y hablamos sobre los resultados y vemos cuáles son las variaciones. Les preguntamos por qué calificaron como lo hicieron”.
Durante estas reuniones, los auditores desarrollan estándares de calificación. Como cuando se calibra un medidor para usarse por toda la planta de producción, “calibrar” a los auditores minimiza la variación y hace que la auditoría sea más significativa y útil.
Siendo de utilidad
Manos recordó un taller con un empleado bromista en la oficina frontal. Sobre su escritorio había una engrapadora, a la cual le había pegado una pieza plana de madera pintada con un marco negro y una etiqueta que decía “ENGRAPADORA”. Donde quiera que estuviera esa engrapadora, estaría etiquetada y en su “lugar”. El sentido del humor nunca es algo malo.
El doble significado de la broma ilustra la fina línea que tienen que caminar los gerentes al mantener las 5S. Un programa 5S representa cambio y puede ser visto como discordante y algo bobo y excesivo. ¿Por qué tener una etiqueta y un marco en una engrapadora? Eso es ridículo.
Bueno, podría no ser ridículo si la gente pierde mucho tiempo buscando una engrapadora particular. Y si el esfuerzo desperdiciado da como resultado un empleado de oficina apurado que comete un error en la preparación de una orden, podría convertirse en un enorme problema en la planta de producción.
“Las 5S sostenibles tiene que ver con encontrar equilibrio entre un control deficiente y un control excesivo”, dijo Manos.
Si encuentra esa fina línea entre control excesivo y control deficiente, entre gestión insuficiente y micro-gestión, pueden prosperar las cinco S, incluida la “disciplina”.
About the Author
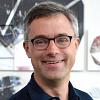
Tim Heston
2135 Point Blvd
Elgin, IL 60123
815-381-1314
Tim Heston, The Fabricator's senior editor, has covered the metal fabrication industry since 1998, starting his career at the American Welding Society's Welding Journal. Since then he has covered the full range of metal fabrication processes, from stamping, bending, and cutting to grinding and polishing. He joined The Fabricator's staff in October 2007.
About the Publication
subscribe now
FMA Communications ha introducido al mercado la edición en Español de la revista The Fabricator. Esta versión consiste del mismo tipo de artículos técnicos y sección de lanzamientos de nuevos productos que actualmente presentan el personal de primera categoría de Fabricator en Inglés.
start your free subscription- Podcasting
- Podcast:
- The Fabricator Podcast
- Published:
- 05/07/2024
- Running Time:
- 67:38
Patrick Brunken, VP of Addison Machine Engineering, joins The Fabricator Podcast to talk about the tube and pipe...
- Trending Articles
Prescripción para la reducción del desperdicio: arreglo esbelto de las instalaciones
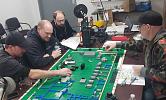
Anidado para la estabilidad del corte láser
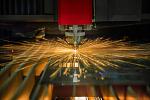
La máquina procesadora de placas crea biseles complejos en un solo corte
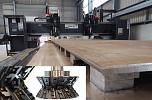
El software guía a los soldadores a través de instrucciones de trabajo
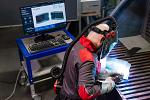
Seguridad en la soldadura desde el inicio
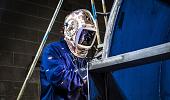
- Industry Events
World-Class Roll Forming Workshop
- June 5 - 6, 2024
- Louisville, KY
Advanced Laser Application Workshop
- June 25 - 27, 2024
- Novi, MI
Precision Press Brake Certificate Course
- July 31 - August 1, 2024
- Elgin,