Senior Editor
- FMA
- The Fabricator
- FABTECH
- Canadian Metalworking
Categories
- Additive Manufacturing
- Aluminum Welding
- Arc Welding
- Assembly and Joining
- Automation and Robotics
- Bending and Forming
- Consumables
- Cutting and Weld Prep
- Electric Vehicles
- En Español
- Finishing
- Hydroforming
- Laser Cutting
- Laser Welding
- Machining
- Manufacturing Software
- Materials Handling
- Metals/Materials
- Oxyfuel Cutting
- Plasma Cutting
- Power Tools
- Punching and Other Holemaking
- Roll Forming
- Safety
- Sawing
- Shearing
- Shop Management
- Testing and Measuring
- Tube and Pipe Fabrication
- Tube and Pipe Production
- Waterjet Cutting
Industry Directory
Webcasts
Podcasts
FAB 40
Advertise
Subscribe
Account Login
Search
¿Por qué no está operando la máquina?
El monitoreo de máquinas ayuda a los talleres a sacarle más provecho a lo que tienen
- By Tim Heston
- August 29, 2022
- Article
- Shop Management
Toda persona que haya trabajado en el taller de fabricación por años probablemente tenga recuerdos del jefe irrumpiendo después de que las punzonadoras se detienen. ¿Por qué está todo tan callado? Para los gerentes el golpeteo de las prensas en el taller de fabricación es equivalente al tintineo de las cajas registradoras. Si las máquinas no están produciendo, se infiere que el taller de fabricación no está ganando dinero.
Contrariamente, si una máquina está operando, todos asumen que todo está bien en el mundo, pero ¿realmente lo está? ¿La máquina está produciendo partes buenas? ¿La máquina está en un estado saludable, bien mantenida, o las cosas saldrán mal más temprano que tarde? ¿La máquina está produciendo las partes correctas para el trabajo correcto en las cantidades correctas, y qué tan bien las está produciendo? ¿La operación está produciendo de la manera más eficiente posible?
En años recientes, los vendedores de máquinas y terceras partes introdujeron sistemas de monitoreo dirigidos a hacer el taller mucho más transparente. Éstos ofrecen, entre otras cosas, tableros que muestran los tiempos productivos y los tiempos sin producir reales. Dichas plataformas se conectan directamente a la máquina y no requieren alimentación manual.
Históricamente, el tiempo productivo de la máquina se ha visto en modo binario—está operando o no está operando—y repito, mucha de esa información se basa en simples suposiciones. Puedo escuchar y ver las máquinas operando, así que todo debe de estar bien. Sin embargo, el taller no es tan sencillo—una realidad que sigue revelándose en el taller cada vez más conectado.
La continuidad del monitoreo
Los vendedores de máquinas y terceras partes de la actualidad ofrecen diversos softwares que pueden rastrear la utilización real de la máquina, un acto que por sí solo puede ayudar a los fabricantes a identificar problemas anteriormente ocultos, lo que aumenta la utilización y la eficiencia de manera inmediata. Dependiendo del producto y del nivel de servicio, el software también puede relacionar esos datos de utilización con trabajos específicos y con otras máquinas en el flujo de valor o en el flujo de trabajo. Luego viene el monitoreo de la condición, el cual indaga en los datos de nivel máquina para determinar la salud de la máquina e identificar problemas antes de que se conviertan en problemas mayores. Estas plataformas usan cierta combinación de estrategias locales (on premise), basadas en la nube y de computación frontera (border computing), siendo la última una especie de búfer de computación de baja latencia entre la recolección de datos en sitio y la nube.
El nivel de integración y la inteligencia de detección dependen del software usado y de la edad y marca de la máquina. En algunas máquinas modernas, un fabricante podría ser capaz de rastrear códigos de alarma específicos o la condición de componentes específicos. Sin embargo, hasta los sensores más sencillos en máquinas antiguas pueden revelar mucho sobre la eficiencia de una operación.
La medición de la utilización de la máquina, el rastreo de trabajos y el monitoreo de la condición de la máquina con frecuencia se ven en entornos acotados (sandboxes) separados. Sin embargo, las líneas entre funciones de software pueden difuminarse en los próximos años. Problemas específicos del taller tienen muchas causas que no pueden encasillarse en una categoría. Por ejemplo, la poca utilización en una prensa dobladora podría tener que ver no sólo con la condición de la máquina (fuga de aceite hidráulico, por ejemplo) sino también con la secuencia y naturaleza de los trabajos que la máquina procesa en todo el turno (rastreo y calendarización de trabajos).
Los fabricantes con pensamiento creativo, que conectan los puntos e identifican patrones de eventos podrían descubrir que obtienen más de las máquinas que operan y de la gente que emplean. Ese logro se volverá más importante con la persistencia de la escasez de mano de obra.
Las sutilezas detrás de la medición de la productividad
Amplias mediciones de datos del tiempo productivo revelan una industria de manufactura de metal llena de activos subutilizados. Por ejemplo, en enero de este año MachineMetrics, Northampton, Massachusetts, publicó un reporte que muestra los tiempos productivos promedio de máquinas en toda su base de clientes, la cual incluye talleres de máquinas así como diversas operaciones de fabricación de chapa y placa metálica. Máquinas como los centros de corte láser automatizados tienen tiempos productivos mucho más altos que sus contrapartes manuales. Sin embargo, el tiempo promedio en 2021 permaneció obstinadamente bajo tan sólo en 28%.
Las tasas de baja utilización “fueron realmente la chispa que nos llevó a iniciar esta compañía”, dijo Eric Fogg, cofundador y director general de atención a clientes de MachineMetrics. “Puede preguntarle a los dueños de muchas compañías, ‘¿Qué tanto están operando sus máquinas? ¿Cuál es la tasa de utilización? Es una pregunta sencilla que no mucha gente puede responder”.
La verdad, según la percepción popular, reside en la planta de producción, y el software de la actualidad puede rastrear varias actividades (no sólo el tiempo productivo) reportadas automáticamente por las propias máquinas. AMADA AMERICA
Fogg agregó que muchos en la manufactura piensan que una máquina con tiempo improductivo no planeado ocurre “debido a las limitaciones de la máquina, problemas de mantenimiento de la máquina, o quizás dificultades con el trabajo. Y sí, esas cosas son algo enorme, y hay mucho trabajo por hacerse en esas áreas. Sin embargo, mucho de eso tiene que ver con planeación y organización. ¿Tenemos la mano de obra y las máquinas para terminar este trabajo? ¿Tenemos los trabajos organizados de una manera que asegure que los trabajos se harán eficientemente en secuencia uno tras otro?”
Las razones para tiempo improductivo no planeado que MachineMetrics recolectó en el 2021 revelan problemas familiares en la manufactura de metal, incluida la escasez de mano de obra. Más del 52% del tiempo, las máquinas estuvieron paradas debido a que simplemente no había operadores disponibles. Más del 22% del tiempo, a las máquinas les faltaron trabajos o material—no es de sorprender en un año de oscilaciones en la demanda y retos de la cadena de suministro extremos.
Dichas razones categorizadas para el tiempo improductivo son sumamente valiosas como puntos de referencia en toda la industria. Por ejemplo, dicha información pormenorizada del tiempo improductivo de máquina en realidad muestra qué tanto está afectando el problema de mano de obra a la manufactura de metal.
Sin embargo, cuando se ve un problema específico en un fabricante, llegar a la causa raíz requiere algunas preguntas más. Si una máquina estuvo parada debido a que no había operador, ¿por qué ese operador no estaba disponible? Sí, el personal probablemente se ha reducido demasiado, pero ¿qué pasó en este ejemplo específico? ¿El operador no se presentó a trabajar? ¿Estaban liberando un cuello de botella en algún otro lado de la planta, y de ser así, qué causó ese cuello de botella? Si a una máquina le faltó un trabajo o material, ¿esto se debió a problemas externos de la cadena de suministro?, ¿o fue un problema interno, es decir, estuvo el operador esperando un conductor de montacargas para entregar el material?, ¿o la máquina simplemente no tuvo nada que procesar debido a una caída en la demanda?
“‘¿Por qué?’ no es una pregunta muy interesante para mí, debido a que todos pueden darle un ‘porque’ diferente y éste con frecuencia no llega al fondo del asunto. Yo quiero saber qué, cómo, cuándo y quién”.
Eso dijo Casey Creer, el consultor principal de servicios profesionales IIoT con sede en Chicago para AMADA AMERICA. Greer trabaja con la plataforma Influent de la compañía, la cual se conecta a varias máquinas y analiza los datos de éstas, incluido equipo tanto de AMADA como de otras marcas.
“Cuando ve una máquina operando por abajo de su capacidad, tendrá algunas preguntas inmediatas” dijo. “¿Qué está produciendo? ¿Quién la está operando, y cuándo?” Tableros que proporciona la plataforma pueden ayudar a un taller a responder inmediatamente esas preguntas. “Veamos ahora la parte. ¿Es una parte difícil de configurar? ¿Qué tiene que hacer el operador para configurarla? Toda esa información le ayudará a tomar mejores decisiones”.
Como lo explicó Greer, los talleres pueden empezar con la medición más objetiva de todas, cuándo. Es difícil evaluar y resolver un problema si los talleres no saben exactamente cuándo están operando sus máquinas. Y realmente saber “cuándo” implica mucho más información pormenorizada que escuchar el golpeteo de la punzonadora desde la oficina.
Greer describió una situación en la cual varios robots de soldadura estaban produciendo como se esperaba. El problema se originó en cómo la operación secuenciaba el trabajo. La situación involucraba a robots de soldadura con mesas duales de soldadura; una parte en una mesa tiene un tiempo de soldadura de 15 segundos mientras que otra parte tenía un tiempo de soldadura de un minuto. Obviamente, el tiempo de soldadura de un minuto establecía el ritmo, el cual desafortunadamente era más lento de lo que desearían los gerentes. Para resolver el problema, la compañía terminó programando partes diferentes con tiempos de producción similares, lo que ayudó de manera efectiva a nivelar la carga (al menos hasta cierto grado) de una familia de productos con tiempos de procesamiento sumamente discrepantes.
“La compañía básicamente combinó y secuenció partes con tiempos de producción similares para mantener la producción de ambas partes, tanto la de un minuto como la de 15 minutos a través de la celda de soldadura”, dijo Greer, y agregó que esta situación ejemplifica la naturaleza del monitoreo moderno de máquinas y la aplicación del Internet Industrial de las Cosas (IIoT, por sus siglas en inglés) en general. “No se trata de tener un producto de software con un conjunto de características. Se trata de aprender sobre un problema desde la perspectiva del fabricante y trabajar juntos para resolverlo”.
¿Cuánto tardó el trabajo en realidad?
Un reto es la desconexión entre el ciclo en que la máquina está operando y las transacciones laborales que registran los operadores. El software de sistema de ejecución de manufactura (MES) y planeación de recursos de la empresa usualmente rastrea el tiempo entre el momento en que un operador marca el inicio y el final de un trabajo, pero con frecuencia carecen de una conexión directa con la máquina en sí. Un operador puede marcar el inicio en un trabajo de prensa dobladora ya configurada a las 10:15 a.m. y luego marcar el final a las 10:30 a.m. Esa información sola muestra que el trabajo le llevó al operador 15 minutos, pero eso es todo. Si mide el tiempo del ciclo de doblado real, la historia se vuelve más completa. Esa nueva información podría revelar que la prensa dobladora pasó sólo cinco minutos moviendo la cortina y doblando partes en realidad.
¿El operador tarda tres veces más de lo que en realidad debería? Probablemente no. Al final de cuentas, el operador necesita manipular el material y hacer inspección y otras tareas durante el proceso. Sin embargo, ahí podría mejorarse la eficiencia, y al tener los datos tanto de tiempo productivo de la máquina como de transacciones laborales, los operadores y supervisores pueden trabajar juntos para la mejora. ¿El acomodo de material ayudaría en cierta manera? ¿Hay un problema con el material, como por ejemplo variación en el espesor o en la dirección del grano, que requiera que el operador ajuste la configuración? ¿El tamaño de la pieza es incorrecto para el herramental que se está usando? ¿Hay problemas de calibración, como por ejemplo una pestaña sin desbarbar moviéndose contra un tope trasero o un tope lateral?
La diferencia entre el tiempo marcado y el tiempo de ciclo real de la máquina podría venir de prácticas heredadas. Trabajando a partir de los datos de transacciones laborales del MES, el operador ve que el taller asignó 15 minutos para el trabajo, y entonces se asegura de marcar el trabajo para 15 minutos. Por supuesto, él podría estar aprovechando la deficiencia operacional, pero también simplemente podría estar siguiendo instrucciones, trabajando de cierta manera porque, pues, ésa es la manera en que siempre se ha hecho.
Repito, para seguir el punto de Greer, el porqué no es muy interesante. La respuesta puede cambiar dependiendo de la perspectiva de una persona, lo cual a su vez da lugar al juego de la culpa. El tiempo usado en señalar culpables es un desperdicio en sí. Trabajar a partir de la información que surge del qué, cómo y cuándo puede darle al personal del taller la información que necesitan para empezar a mejorar.
Volviéndose predictivos con los datos
En un taller de fabricación típico, casi todas las máquinas—sin importar su edad ni su marca—pueden decirle al software de monitoreo de máquina si están encendidas o apagadas. Por supuesto, las máquinas modernas pueden decirle mucho más al software de monitoreo.
“Hay tantos elementos qué monitorear”, explicó Greer, y agregó que el nivel de monitoreo depende de la marca y de la edad de la máquina. “Y cuando se toman los datos, podemos ver todo lo que pasó en una máquina, incluido cuándo arrancaron los programas, qué alarmas ocurrieron y a qué altura de la operación ocurrieron”.
Dichos datos pueden ser sumamente valiosos para los departamentos de mantenimiento que buscan descifrar el estado de una máquina antes de que sea puesta fuera de servicio imprevistamente. Los datos también pueden alimentarse a sistemas de analítica, ya sea fuera de sitio o basados en la nube (dependiendo de la configuración y del vendedor del software), que pueden ayudar a refinar un programa de mantenimiento predictivo. En lugar de simplemente inspeccionar y dar mantenimiento a elementos en un calendario establecido (como con el mantenimiento preventivo), un fabricante puede inspeccionar y dar mantenimiento a los componentes de una máquina con base en el uso real, lo cual a su vez extiende la vida de la máquina y reduce los costos generales de operación. Actualmente, los servicios de monitoreo, ya sea a través de vendedores de máquinas o de terceras partes, pueden notificar a un fabricante sobre un problema antes de que se agrave.
“Con el monitoreo moderno de condiciones, podemos ser mucho más proactivos”, dijo Christine Benz, encargada de TruServices and Smart Services en TRUMPF Inc. “Con un análisis de datos totalmente automatizado, podemos predecir cuándo podrían ocurrir los problemas. Y podemos ayudar a los fabricantes a resolver problemas incluso antes de que estén conscientes de ello”. Por ejemplo, en el pasado un operador podría observar una mala calidad de la rendija, lo cual a su vez provocaría una solución de problemas reactiva. Actualmente, el operador o técnico puede hacer cambios para evitar el problema desde el principio.
Los sensores podrían detectar cambios en los niveles del agua en el sistema de enfriamiento de una máquina de corte láser, o en los niveles de fluido hidráulico en una prensa dobladora, enviando datos que pueden impulsar a un fabricante a actuar “antes de que haya algún efecto en la producción del taller”, dijo Benz. “Nuestra meta con el monitoreo de condiciones es lograr un tiempo improductivo no planeado de cero”.
“En ciertos casos, ahora estamos analizando la calidad del corte de algunas partes y optimizamos las tablas técnicas”, dijo Mathias Staiger, gerente de R&D, conectividad, en TRUMPF. “Y para un tipo de máquina, podemos actualizar automáticamente esas tablas técnicas para que la máquina pueda obtener mejores resultados”. Agregó que en este y en otros casos, la analítica de datos basada en nube trata sólo con datos a nivel máquina, no datos a nivel parte.
En algunos casos, las máquinas pueden leer los resultados de esos análisis y auto-corregirse. Dichos escenarios de aprendizaje de máquina no son algo generalizado en la fabricación de metal, pero sí existen. Un ejemplo importantes es con las tecnologías automatizadas de desanidado y clasificación de partes que justo empiezan a surgir. Las ventosas en el efector de extremo (combinadas con elevadores especializados de pasador de empuje por debajo) pueden intentar levantar una parte de un nido, detectar cuando falla, luego intentar de nuevo usando otra estrategia.
“Si el primer intento no funciona, la máquina automáticamente cambia para conectar un patrón de ventosa diferente en el efector de extremo removiendo las piezas para separar la parte del esqueleto”, dijo Benz, y agregó que la máquina toma en cuenta dónde está la parte en el nido y cómo está orientada. Una parte orientada horizontalmente en la esquina podría levantarse de manera diferente a una pieza en el centro de la chapa. “De esta manera, la máquina aprende”.
Benz agregó que un fabricante puede usar datos deducidos del monitoreo de condiciones en conjunto con otro software, incluido TRUMPF TruTops FAB, el cual puede automatizar la planeación y el movimiento de material. En algunas aplicaciones, por ejemplo, sensores en las máquinas así como en almacenamiento de material y ubicaciones de piezas de trabajo en proceso pueden originar órdenes y movimiento de material. Aclaró que TruTops FAB y el monitoreo de condiciones de TRUMPF son plataformas de software separadas, pero los fabricantes pueden obtener datos de ambas para identificar correlaciones.
“La digitalización y la automatización en la industria de las máquinas herramienta se volverá más importante”, dijo Benz. “Hay una fuerte presión para que la industria de la chapa metálica digitalice todo el proceso, desde el pedido hasta el cobro. Considerando la sorprendente tendencia que vemos con el retorno a la producción doméstica, traer de regreso a Estados Unidos la manufactura, las dos metas principales que tiene la industria son establecer el estándar para partes de alta calidad y ser lo más eficiente posible. Los fabricantes necesitarán hacer realidad ambas”.
Causas raíz del tiempo improductivo no planeado
Cada fabricante es diferente, por lo que es imposible señalar las causas raíz de todos los problemas, pero muchas pueden rastrearse hacia varias áreas generales. Una tiene que ver con instituir una disciplina de diseño de chapa metálica que considere cómo se hacen las cosas. Si los ingenieros diseñan dobleces con factores k, holguras de doblez y deducciones de doblez sin saber qué herramientas usará el operador de la prensa, ahí podría haber un problema. El mismo razonamiento se aplica al anidar y al determinar las entradas, las ubicaciones de micro-pestañas y la posición de la pieza con relación a las tablillas de la mesa y a otras piezas en un nido.
Otra causa raíz tiene que ver con problemas de organización, capacitación y recursos. Podría ser una falta de comunicación, como por ejemplo entre el primer y segundo turno, o el hecho de que a cierto programador nunca se le instruyó acerca de cómo y cuándo llevar las hojas de ruta de trabajo a la planta de producción. Podría derivarse de conocimiento heredado inconsistente del tipo “porque siempre lo hemos hecho de esta manera”. Esto en sí implica un problema con el diseño de chapa metálica (como la asignación de factores k sin saber qué herramental se usará), así como malas prácticas de mantenimiento.
Las consecuencias se agravan cuando la maquinaria se vuelve más rápida y más automatizada. Un sistema de corte automatizado podría estar parado por horas o incluso días—no debido a un asunto sutil del accionamiento eléctrico ni por problemas en la óptica de la cabeza de corte, sino por tablillas sucias. El metal fundido del núcleo se suelda a la escoria acumulada en las tablillas, así que cuando las horquillas automatizadas se deslizan y levantan la hoja cortada, levantan toda la mesa con la hoja.
Sin embargo, no se apresure a sacar conclusiones. ¿Fue sólo la condición de las tablillas, o fue algo malo en las condiciones de corte? ¿Quizás las posiciones de las tablillas con respecto a cómo se anidaron las partes contribuyeron al problema, o quizás tuvo que ver la posición de una micro-pestaña (o la ausencia de la misma)?
Todas las fuentes coinciden en que ésta es la razón de que sea tan valioso iniciar con los datos de la máquina, desde un punto de vista tanto de la producción como del monitoreo de las condiciones. Conforme evolucionen los sensores y el software, este último les dará a los talleres un entendimiento operacional más profundo. Dicha tecnología al final de cuentas ayudará a los fabricantes a identificar lo que está pasando en realidad, dándoles una realidad compartida que sirva como punto de partida para una mejora más inteligente.
About the Author
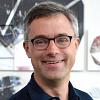
Tim Heston
2135 Point Blvd
Elgin, IL 60123
815-381-1314
Tim Heston, The Fabricator's senior editor, has covered the metal fabrication industry since 1998, starting his career at the American Welding Society's Welding Journal. Since then he has covered the full range of metal fabrication processes, from stamping, bending, and cutting to grinding and polishing. He joined The Fabricator's staff in October 2007.
About the Publication
Compañías Relacionadas
subscribe now
FMA Communications ha introducido al mercado la edición en Español de la revista The Fabricator. Esta versión consiste del mismo tipo de artículos técnicos y sección de lanzamientos de nuevos productos que actualmente presentan el personal de primera categoría de Fabricator en Inglés.
start your free subscription- Podcasting
- Podcast:
- The Fabricator Podcast
- Published:
- 05/07/2024
- Running Time:
- 67:38
Patrick Brunken, owner of Addison Machine Engineering, joins The Fabricator Podcast to talk about the tube and pipe...
- Trending Articles
Prescripción para la reducción del desperdicio: arreglo esbelto de las instalaciones
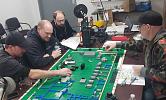
Anidado para la estabilidad del corte láser
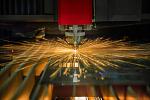
La máquina procesadora de placas crea biseles complejos en un solo corte
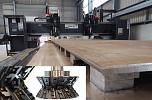
El software guía a los soldadores a través de instrucciones de trabajo
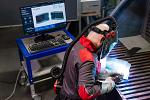
Seguridad en la soldadura desde el inicio
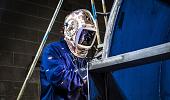
- Industry Events
World-Class Roll Forming Workshop
- June 5 - 6, 2024
- Louisville, KY
Advanced Laser Application Workshop
- June 25 - 27, 2024
- Novi, MI
Precision Press Brake Certificate Course
- July 31 - August 1, 2024
- Elgin,