Contributing Writer
- FMA
- The Fabricator
- FABTECH
- Canadian Metalworking
Categories
- Additive Manufacturing
- Aluminum Welding
- Arc Welding
- Assembly and Joining
- Automation and Robotics
- Bending and Forming
- Consumables
- Cutting and Weld Prep
- Electric Vehicles
- En Español
- Finishing
- Hydroforming
- Laser Cutting
- Laser Welding
- Machining
- Manufacturing Software
- Materials Handling
- Metals/Materials
- Oxyfuel Cutting
- Plasma Cutting
- Power Tools
- Punching and Other Holemaking
- Roll Forming
- Safety
- Sawing
- Shearing
- Shop Management
- Testing and Measuring
- Tube and Pipe Fabrication
- Tube and Pipe Production
- Waterjet Cutting
Industry Directory
Webcasts
Podcasts
FAB 40
Advertise
Subscribe
Account Login
Search
Arc Welding 101: Wire-feed welding, stick welding with the same machine
- By Marty Rice
- November 17, 2014
- Article
- Arc Welding
Q: I would like to know if a wire-feed welding machine can double as a modest-amperage DC shielded metal arc welding (SMAW) machine if I attach an electrode holder to the output.
I have been told that aluminum welding works well and is convenient using SMAW and DC. I have the aluminum roller kit for wire feed but would need to put these in, change the wire, and then get a tank of argon gas.
Putting on an electrode holder and using SMAW would be faster for just occasional use, it seems. Is this sound reasoning?
Randy O.
A: Power sources are designed to provide constant current or constant voltage.
Gas metal arc welding (GMAW) is constant voltage, while SMAW is constant current. All the different amp and voltage curves and droops can get long and complicated to understand and are a bit too technical to go into here.
Here’s how a fellow once explained it to me: The two power sources are like comparing apples to oranges, and when you try to work one off of the other, “it just don’t work.” (That’s a direct quote from a guy I used to work with in the field. He used that reply quite often, on a variety of topics!)
Most of the welding manuals out there explain power sources if you want to look into the technical explanation.
As for aluminum SMAW, I have used it to some extent and can tell you it’s good only for thick aluminum. Aluminum has twice the expansion of mild steel and is a much better conductor of heat. This can cause distortion, and it’s easy to blow a hole in the metal before you realize it’s happening.
Thick aluminum should be preheated to somewhere between 300 and 400 degrees F before you weld it. When I say thick, I mean anywhere from a half inch and up. That’s on my scale of thickness, though, so you should research the actual measurement.
You need to use the direct current electrode positive (DCEP) and keep a really short arc as you drag the electrode without oscillating (weaving). Most specifications on critical joints won’t allow aluminum to be stick-welded.
Be sure to keep the electrodes dry, because moisture in the flux will cause it to dissipate and flake off. Also, it’s important to remove the oxides before welding and postclean the weld because the leftover residue is corrosive.
I know it’s a pain to convert your machine, but that’s probably your best bet unless you want to buy an AC/DC SMAW machine. Then you could always go with an inverter—but that’s a whole other story.
About the Author
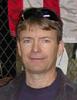
Marty Rice
High School Career Center in Texas
Questions for the author can be e-mailed to vickib@thefabricator.com
About the Publication
subscribe now
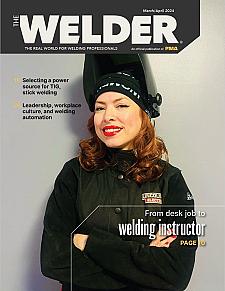
The Welder, formerly known as Practical Welding Today, is a showcase of the real people who make the products we use and work with every day. This magazine has served the welding community in North America well for more than 20 years.
start your free subscription- Stay connected from anywhere
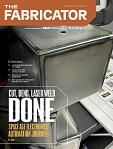
Easily access valuable industry resources now with full access to the digital edition of The Fabricator.
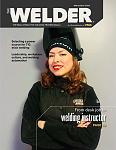
Easily access valuable industry resources now with full access to the digital edition of The Welder.
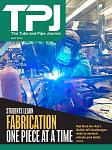
Easily access valuable industry resources now with full access to the digital edition of The Tube and Pipe Journal.
- Podcasting
- Podcast:
- The Fabricator Podcast
- Published:
- 04/30/2024
- Running Time:
- 53:00
Seth Feldman of Iowa-based Wertzbaugher Services joins The Fabricator Podcast to offer his take as a Gen Zer...
- Industry Events
Pipe and Tube Conference
- May 21 - 22, 2024
- Omaha, NE
World-Class Roll Forming Workshop
- June 5 - 6, 2024
- Louisville, KY
Advanced Laser Application Workshop
- June 25 - 27, 2024
- Novi, MI
Precision Press Brake Certificate Course
- July 31 - August 1, 2024
- Elgin,