- FMA
- The Fabricator
- FABTECH
- Canadian Metalworking
Categories
- Additive Manufacturing
- Aluminum Welding
- Arc Welding
- Assembly and Joining
- Automation and Robotics
- Bending and Forming
- Consumables
- Cutting and Weld Prep
- Electric Vehicles
- En Español
- Finishing
- Hydroforming
- Laser Cutting
- Laser Welding
- Machining
- Manufacturing Software
- Materials Handling
- Metals/Materials
- Oxyfuel Cutting
- Plasma Cutting
- Power Tools
- Punching and Other Holemaking
- Roll Forming
- Safety
- Sawing
- Shearing
- Shop Management
- Testing and Measuring
- Tube and Pipe Fabrication
- Tube and Pipe Production
- Waterjet Cutting
Industry Directory
Webcasts
Podcasts
FAB 40
Advertise
Subscribe
Account Login
Search
Fabricating for the win
Welcome to the fast-paced, competitive, and fun world of NASCAR® welding and fabrication
- By Amanda Carlson
- March 26, 2015
- Article
- Arc Welding
When NASCAR®’s Sprint Cup Series is in full swing, the focus tends to be on drivers like Carl Edwards, Denny Hamlin, Matt Kenseth, and Kyle Busch; the drama surrounding each race; and the week-to-week results and point standings. What gets considerably less attention are the teams of people behind the scenes that make sure drivers are safe and have a car not only capable of winning races, but also of standing up to NASCAR’s stringent rules and regulations.
Joe Gibbs Racing in Huntersville, N.C., is tucked away off a quiet, tree-lined road just outside of Charlotte. Though it may seem quiet on the outside, make no mistake, it is anything but on the inside. Walk through the fabrication and assembly areas on an early morning in mid-January and you’ll find a bustling shop full of guys who have already put in a couple hours’ worth of work with no stop in sight. Banners that display various championships and race wins line the large rectangular room, flanked by offices belonging to the four crew chiefs.
In a state with a deep history in tobacco and legendary college basketball programs, racing is king. Not only is it king, it is a way of life. But there’s more to racing than just driving fast. It takes a team of skilled welders and fabricators to take the idea of a car and make it into reality.
So what does it take to make it in this ultracompetitive world where your work is heavily scrutinized, your time is not your own, and all the while you have a driver’s life in your hands? It requires incredible skill, yes, but there are other qualities you must possess and things you must accomplish. To be successful at one of racing’s top teams requires more than just welding ability. It requires an unparalleled dedication to the sport and to your craft. With that dedication, however, sometimes comes sacrifice.
It Takes a Team to Build a Race Car
What the casual NASCAR fan sees on race day—the driver, the crew chief, and possibly even the pit crew—represents only a few of the individuals responsible for putting together a high-performance race car. Not only must it have the capability to win races, but it also must be able to stand up to stringent requirements for size, weight, and safety. There is very little room for error as mistakes can mean time-consuming rework, disqualification, or compromised safety.
Joe Gibbs Racing is home to a staff of skilled welders and fabricators who build upwards of 100 cars per year. Each department at Joe Gibbs must work together to ensure that cars are moving through the assembly line quickly without sacrificing quality craftsmanship. For each team to work together, they must know how their jobs affect those of others around them. Different teams are responsible for various sections of the car—brakes, engines, chassis, front, midsection, and the rear.
Since Joe Gibbs is now home to four drivers, each team of fabricators has to be well-versed in the needs of each driver and be able to change setups per the crew chief’s instructions quickly and accurately, explained Shane Love, lead welder/motor room fabricator, because each crew chief may have several different setups in mind.
“The crew chief of the No. 18 car may say, ‘I want to change these springs, change these shocks, and put this different spindle on’ while at the track, so they’re practicing that now [in the shop] to get to a point where they can do it as quickly as possible when they’re at the track.”
Cars must meet the appropriate specifications as found on the official NASCAR grid templates (see Figures 1 and 2). The gold line found on the edge of each template indicates a perfectly built race car per NASCAR standards, but cars that come within 1⁄8 inch of the gold standard are considered legal.
Car bodies are measured with these grid templates an average of four to five times from the time they are built until the time they are loaded onto trucks for transport to the race venue. NASCAR also measures the cars at the race track, usually once when the cars arrive to the track, again before qualifying heats, and one final time before the race.
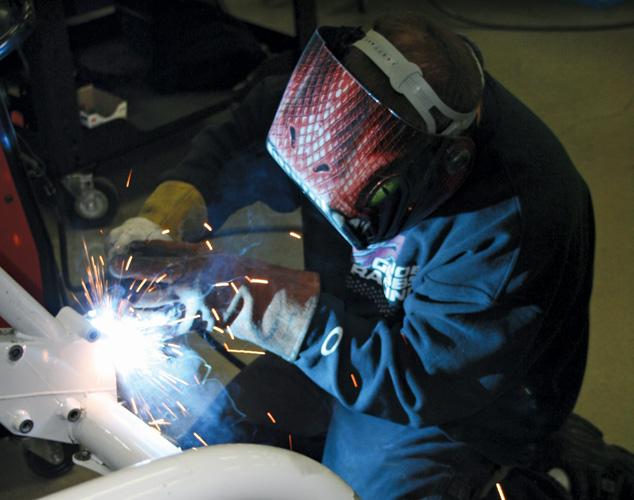
There’s more to being a successful motorsports welder than just welding skill. You’ve got to work hard, make sacrifices, be a team player, and, at the heart of it all, love racing.
Welders assemble the body and chassis using mostly gas metal arc welding (GMAW), although some gas tungsten arc welding (GTAW) is performed to make parts. GMAW provides the fabrication team with the speed it needs to keep up with demand. The team uses Lincoln Electric XP 180, 216, and 350 power sources and is encouraged to attend the company’s Motorsports Welding School in Cleveland.
Pay Your Dues
Welders and fabricators at Joe Gibbs Racing eat, sleep, breathe, and have practically been raised in the art of racing in some fashion. It’s not just a job, and anyone who treats it as such probably won’t last very long. Many welders and fabricators there have grown up along the dirt tracks, raced stock cars or go-karts, or repaired chassis or other components for themselves or other drivers.
Love has been with Joe Gibbs Racing for the last 17 years and, like many of his colleagues, he grew up racing.
“I wanted to be a driver. But it got to the point where money became an issue, so I went into welding instead.”
He began taking welding courses at Central Piedmont Community College in Charlotte and then moved on to Lincoln Electric’s motorsports welding program. He placed an emphasis on metallurgy and welding specialty and exotic metals and brought that unique experience first to Hendrick Motorsports before joining the Joe Gibbs team.
Chris Newmyer is also a lifer in the motorsports world. He has been with Joe Gibbs for 12 years, where he works on suspension components.
“I’ve got an associate’s degree in drawing, but I grew up racing and did a lot of welding out of necessity. I really just learned as I went,” Newmyer said.
Jay Brassard, a 32-year motorsports vet and 10-year employee at Joe Gibbs, learned to stick weld when he was 6 years old and not long after that began a lifelong interest in racing. First it was go-karts, then it was motocross, and finally he transitioned into automobile racing.
“It started at a very young age for me. My grandfather built race cars and raced at a little local dirt track. I remember seeing pictures of my grandfather and the other guys involved, and he was the welder on their race team. That got me interested,” Brassard said.
Love said the welding and fabrication department is full of guys who have paid their dues at their hometown track and advises all motorsports hopefuls to do the same.
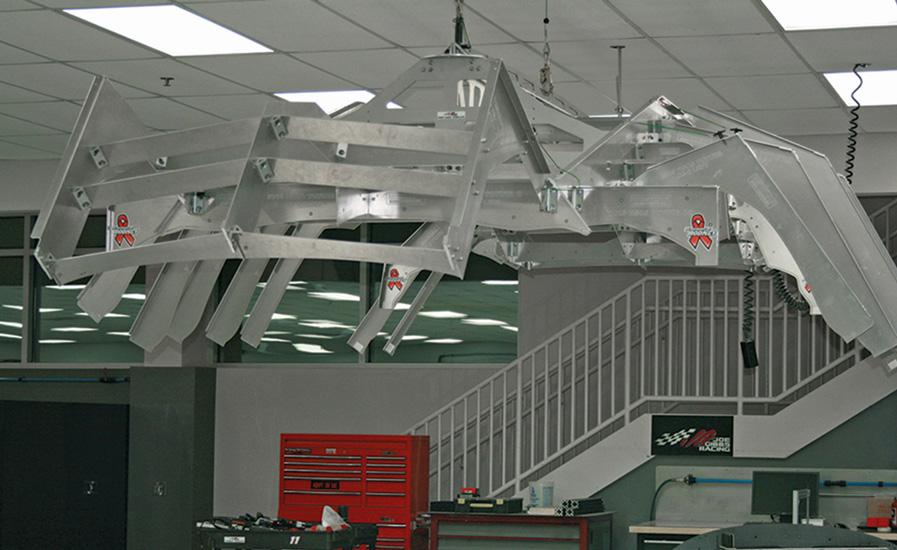
Figure 1
The grid template is placed over the length of the car roughly four to five times before
it is shipped to the race track. A gold line runs along the perimeter of the grid template,
and cars must measure to within 1⁄8 inch of that line to be size-compliant.
“If there’s a race track nearby, then you need to spend some time there before you can even think you’ll make it at this level. It might only be a street stock car, but it still relates. The more you can do on that Saturday night level, the more valuable you’ll be to a company like this later on,” Love said.
The experience that can come only by working the races, making parts, fixing parts, and knowing how each component works with the overall car’s design is a key factor at Joe Gibbs, where Love said welders and fabricators are charged to make as much of the car in-house as is possible.
“We make absolutely everything we can possibly make. We try not to buy or outsource anything because we want control. We try to control parts and our pieces, and if we make them we control them, all the way from the metal that we buy to the finished product,” Love explained.
Another component to paying your dues is moving to where the action is. Sending resumes and making phone calls are great, said Newmyer, but the sure-fire way to get a team’s attention is to show up at their doorstep.
“You’ve got to get here and start knocking on doors. I’m from out west originally, and I’ve had a lot of people call me wanting to get involved in motorsports out here [in North Carolina], but they don’t seem to want to take the initiative to come out here. That doesn’t work. I tried that for years—I sent resumes but nobody pays any attention to that. You have to show up at the door. You have to show that you’re committed to it,” Newmyer explained.
Love has paid his dues, and as a result, the engineering and design teams tend to include him in conversations involving parts they know he’ll be working on. It’s part of the team dynamic that makes working at Joe Gibbs Racing so special—there’s a high level of respect among the various departments.
Embrace Hard Work, Sacrifice
While fans might consider the off-season as a time to celebrate victory or lament defeat, race teams spend that time furiously gearing up for the next season. Love said the months of November through February are the shop’s busiest times.
“We’re talking seven days a week, from 6 a.m. to at least 5 p.m. Saturdays and Sundays I typically work from 8 a.m. until 4 p.m,” Love said.
Along with typical season prep work, Joe Gibbs has had a particularly busy off-season with the addition of a fourth driver, Carl Edwards.
Adding a fourth car has increased the work load by 33 percent.
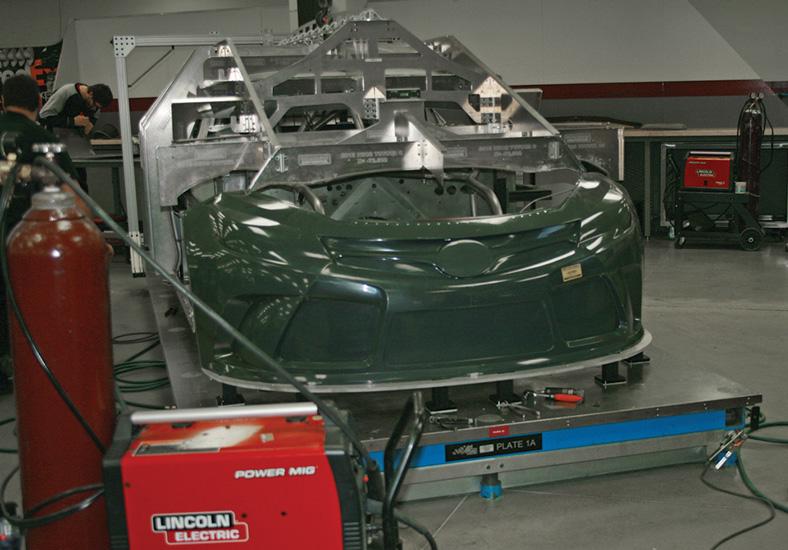
Figure 2
Here’s another look at a grid template as the car sits on a plate. Three men are assigned to a plate—one person works on everything
from the firewall and forward, another works on the side panels and roof, and finally the third person fabricates the entire rear of
the car.
“We’ve got a lot of pieces and parts to make. Even though there are a lot of people to help, it’s still a lot to be done in a very short period of time between the end of one season and the start of another,” Love said.
Newmyer said the best way to deal with the hectic schedule is to dig in and get to work. With experience comes the realization that it’s not always going to be crazy.
“I get a lot of satisfaction when we run well, but there’s also a lot of satisfaction when a driver comes over from another race team and looks at some of your work and says, ‘I can’t believe I’ve been competing against that.’”
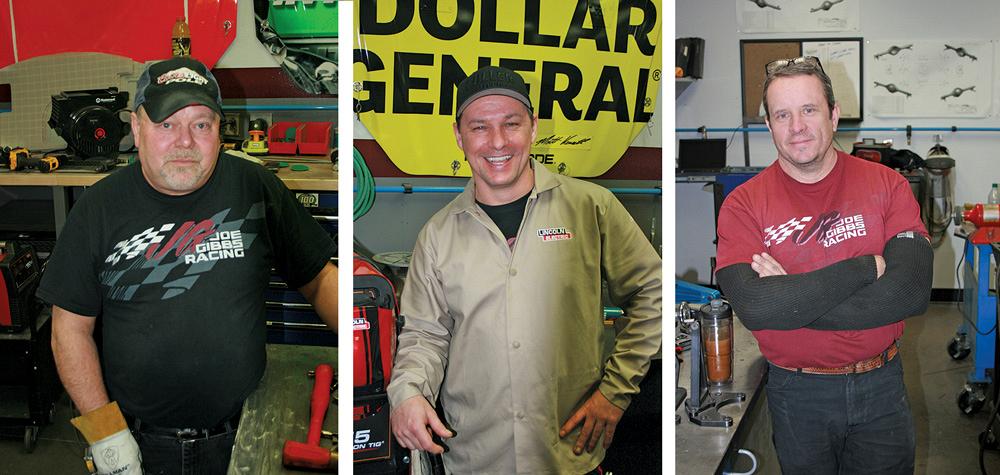
Left: Jay Brassard has spent most of his life welding
and either racing or working on cars,
minibikes, and go-karts.
Center: Shane Love, lead welder/motor room
fabricator, grew up wanting to be a driver.
But learning to weld paired with his love of
racing has helped him realize his dream of
making a living in the racing business.
Right: Chris Newmyer moved to North Carolina
from the West Coast to pursue a career in
motorsports welding. Welders with the
same dream must be willing to knock on
doors, pay their dues, and go to where the
action is.
About the Author
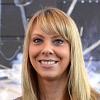
Amanda Carlson
2135 Point Blvd
Elgin, IL 60123
815-227-8260
Amanda Carlson was named as the editor for The WELDER in January 2017. She is responsible for coordinating and writing or editing all of the magazine’s editorial content. Before joining The WELDER, Amanda was a news editor for two years, coordinating and editing all product and industry news items for several publications and thefabricator.com.
About the Publication
subscribe now
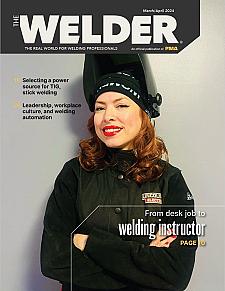
The Welder, formerly known as Practical Welding Today, is a showcase of the real people who make the products we use and work with every day. This magazine has served the welding community in North America well for more than 20 years.
start your free subscription- Stay connected from anywhere
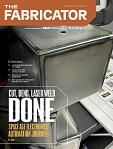
Easily access valuable industry resources now with full access to the digital edition of The Fabricator.
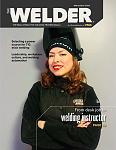
Easily access valuable industry resources now with full access to the digital edition of The Welder.
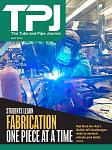
Easily access valuable industry resources now with full access to the digital edition of The Tube and Pipe Journal.
- Podcasting
- Podcast:
- The Fabricator Podcast
- Published:
- 04/30/2024
- Running Time:
- 53:00
Seth Feldman of Iowa-based Wertzbaugher Services joins The Fabricator Podcast to offer his take as a Gen Zer...
- Trending Articles
The role of flux in submerged arc welding performance
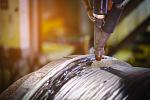
Aluminum MIG wires offer smooth feeding, reduced tangling
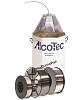
Connecticut students compete in Maritime Welding Competition
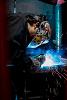
Three ESAB welding machines win Red Dot Awards for product design
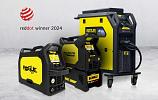
Power source added to cobot welding system for simplified automation
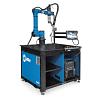
- Industry Events
Pipe and Tube Conference
- May 21 - 22, 2024
- Omaha, NE
World-Class Roll Forming Workshop
- June 5 - 6, 2024
- Louisville, KY
Advanced Laser Application Workshop
- June 25 - 27, 2024
- Novi, MI
Precision Press Brake Certificate Course
- July 31 - August 1, 2024
- Elgin,