- FMA
- The Fabricator
- FABTECH
- Canadian Metalworking
Categories
- Additive Manufacturing
- Aluminum Welding
- Arc Welding
- Assembly and Joining
- Automation and Robotics
- Bending and Forming
- Consumables
- Cutting and Weld Prep
- Electric Vehicles
- En Español
- Finishing
- Hydroforming
- Laser Cutting
- Laser Welding
- Machining
- Manufacturing Software
- Materials Handling
- Metals/Materials
- Oxyfuel Cutting
- Plasma Cutting
- Power Tools
- Punching and Other Holemaking
- Roll Forming
- Safety
- Sawing
- Shearing
- Shop Management
- Testing and Measuring
- Tube and Pipe Fabrication
- Tube and Pipe Production
- Waterjet Cutting
Industry Directory
Webcasts
Podcasts
FAB 40
Advertise
Subscribe
Account Login
Search
Grill or be grilled
Robotic welding cell helps grill fabricator do what it does best
- By Amanda Carlson
- May 23, 2016
- Article
- Arc Welding
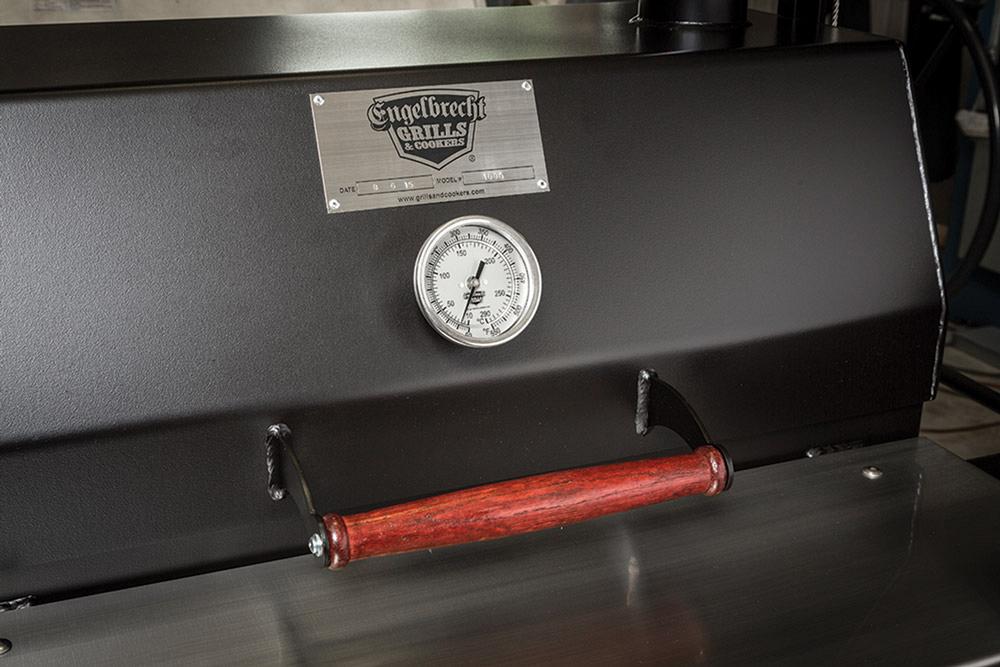
Engelbrecht Grills & Cookers designs and fabricates some of the best wood-fi red grills available today. The 1000 series Braten grill was named Top 10 Best Value by AmazingRibs.com. Celebrity chef Bobby Flay uses the 1000 series, and the White House commissioned the company to fabricate a special 1000 series grill as a gift from President Obama to British Prime Minister David Cameron.
It’s not unusual for welders and fabricators to take on home hobbyist projects. It’s a common way to blow off steam, make extra money, or build something of quality without relying on someone else. The rub about being a fabricator is they can spot good craftsmanship, or the lack thereof, from a mile away.
That, in a nutshell, explains the genesis of Engelbrecht Grills & Cookers, Paxton, Ill. Its namesake Chris Engelbrecht is a lifelong welder and metalworker thanks to his upbringing on his family’s farm. Like most guys, he loved grilling and barbecuing. He didn’t, however, like the way most smokers were built. So he did what any true craftsman does—he built his own. It was nothing fancy, just an old propane tank, pipe, and whatever else he could get his hands on, but it was one that he knew would perform up to his standards. He machined the parts and made sure everything fit up perfectly. In his words, it was just built very well. It didn’t take long for others to notice.
“I had my own unique approach to it. It was something I wanted to do and other people liked it. My friends saw and asked me to make them one, and it just kept rolling from there.”
For the next two years he spent his free time making grills for friends and acquaintances—a full-time paid hobby as he calls it. Finally, it clicked. Why not eliminate the word hobby from that sentence? After all, demand was steady and he barely had enough free time to keep up with all of the orders he was receiving.
He left his job as a pipeline welder in the propane industry, set up a shop space, and took a gamble. He’s never looked back.
“I ended up just taking a risk and throwing in the chips. I built a shop and took a huge gamble on this idea.”
If You Can’t Stand the Heat …
That’s not to say the company didn’t experience its share of hardships. One of its most popular items in the late 2000s was a large trailer-mounted grill used for tailgating. The units built according to strict customer specifications cost around $10,000. They were so popular that Engelbrecht had a couple of guys who worked solely on those units, two sometimes three at a time.
After the recession of 2008-2009, the demand for trailer-mounted grills dropped off to almost nothing. Business was so slow, Engelbrecht recalled, that he and his co-workers had nothing to do during the day but clean the windows.
To add insult to injury, another popular model, the Campfire Grill, hit a snag that many American OEMs are all too familiar with: overseas competition.
“We used to build well over 1,000 [Campfire Grills] a year, and that was before we were automated. It’s really hard to protect your design in the BBQ world because it’s all just such old technology. The whole thing was copied by someone mailing them overseas, and they began selling them over here for $100, which is well below our cost to even build it. So that killed that one too.”
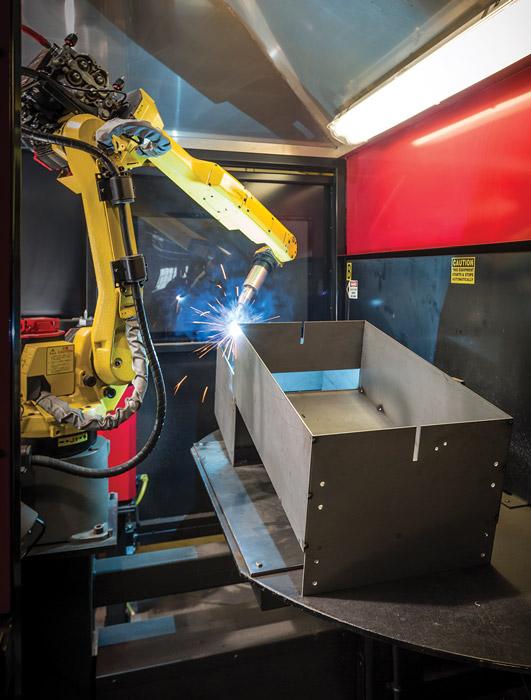
Engelbrecht decided on a System 40 welding robot cell with a FANUC® ARC Mate® iC robotic arm, Power Wave® power source, and AutoDrive® wire feed system. The cell included a 76-in. turntable and servo-driven positioner that allows small to mediumsized parts to be welded without reorientation.
It was indeed a rough patch, but looking back, Engelbrecht said it afforded them the flexibility to review existing products and refocus efforts elsewhere to stay in business. They turned to their 1000 series and changed its design slightly, a move that spawned the idea for the Braten Campfire grill.
Engelbrecht decided to stop making any trailer-mounted grills and instead began producing the 2000 series—the grill meant for the trailer that they mounted to a stand instead.
Their persistence paid off. Today Engelbrecht is one of the premier manufacturers of wood-fired grills. Its 1000 series Braten grill was named Top 10 Best Value by AmazingRibs.com. Celebrity chef Bobby Flay uses the 1000 series.
And the White House commissioned Engelbrecht Grills to fabricate a special 1000 series as a gift from President Obama to British Prime Minister David Cameron in 2012.
When Automation Became Necessary
Even with their strong rebound in mind, the need to automate wasn’t immediate. It started with fabricating the time-consuming, tedious components and grew when customer demand for their products did too. It was a nice rebound after the recession, but things went from busy to overwhelming quickly.
For example, their longest lead time for a 1000 series grill was in 2011-2012, when customers waited six or seven months for delivery. That kind of loyalty, Engelbrecht said, is a testament to the brand and the quality of the product.
“These are 100 percent paid orders. We started that way back in the beginning when the wait was like a week or two—you pay us now and we’ll send you the grill. Then the wait became one month, then two months, but we kept the same policy. People were fine with it, which is amazing.”
It was a far cry from where they had come from, but if they were going to move forward and address the growing lead-time challenges, Engelbrecht knew they needed to automate.
“We just got overwhelmed with work. We would have years where we doubled our orders and the work just became so much that we couldn’t do anything.”
Engelbrecht already had an established rapport with Lincoln Electric Co., Cleveland, so he approached them with what he wanted: a robot that could run Surface Tension Transfer® (STT). Beyond that, Engelbrecht was open to ideas.
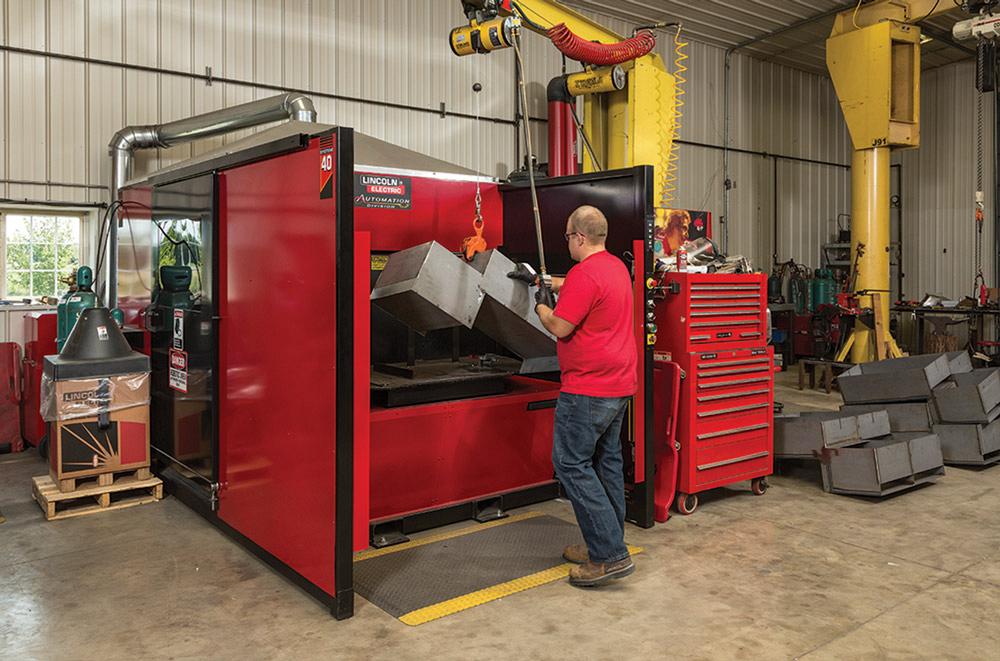
The motivation for automating was never about cost savings through eliminating welders. It was about freeing the company’s five employees to focus on what they do best, not doing the same thing over and over again.
They decided on a System 40 welding robot cell with a FANUC® ARC Mate® iC robotic arm, Power Wave® power source, and AutoDrive® wire feed system. The cell included a 76-in. turntable and servo-driven positioner that allows small to medium-sized parts to be welded without reorientation. The turntable wasn’t on Engelbrecht’s initial wish list, but after talking with Lincoln representatives about what productivity advantages it can have, especially for a shop his size, it made more sense to him.
The motivation behind automating was never about cost savings through eliminating welders. It was about freeing his five guys to focus on what they do best, not doing the same thing over and over again.
Since the robotic cell was implemented, production has doubled and production welding time has decreased by 95 percent. What once took two weeks to hand weld is now done in one day by the robot. Before the robot, it took 28 hours of production time to build a 1000 series Braten grill. With the robot it now takes 15 hours. On Campfire Grills, the automated system has shaved production time from between four and five hours to one hour.
Today lead times are right around two months, depending on the grill.
“I can say that we finally increased productivity, and we’ve increased our efficiency to where we’re almost to the point of having the 1000 series in stock. We’ll see how the week goes. Usually I’ll say that and, boom! they’re gone.
“There’s this one-liner I like in particular, which says, ‘Do what you do best and hire out the rest.’ We’re metal fabricators. It’s what we do best and we love what we do. The mundaneness of some of these parts takes away from that. What the machine provides is the ability to destress and just focus on what we do best.”
Engelbrecht Grills & Cookers, 866-879-3851, www.grillsandcookers.com
Photos courtesy of Lincoln Electric Co., Cleveland.
About the Author
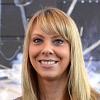
Amanda Carlson
2135 Point Blvd
Elgin, IL 60123
815-227-8260
Amanda Carlson was named as the editor for The WELDER in January 2017. She is responsible for coordinating and writing or editing all of the magazine’s editorial content. Before joining The WELDER, Amanda was a news editor for two years, coordinating and editing all product and industry news items for several publications and thefabricator.com.
About the Publication
Related Companies
subscribe now
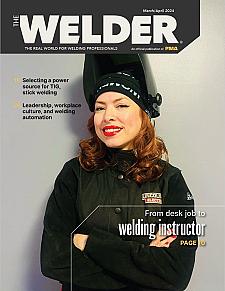
The Welder, formerly known as Practical Welding Today, is a showcase of the real people who make the products we use and work with every day. This magazine has served the welding community in North America well for more than 20 years.
start your free subscription- Stay connected from anywhere
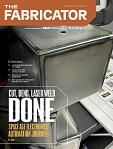
Easily access valuable industry resources now with full access to the digital edition of The Fabricator.
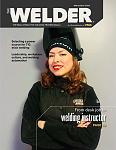
Easily access valuable industry resources now with full access to the digital edition of The Welder.
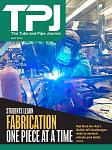
Easily access valuable industry resources now with full access to the digital edition of The Tube and Pipe Journal.
- Podcasting
- Podcast:
- The Fabricator Podcast
- Published:
- 04/30/2024
- Running Time:
- 53:00
Seth Feldman of Iowa-based Wertzbaugher Services joins The Fabricator Podcast to offer his take as a Gen Zer...
- Trending Articles
Aluminum MIG wires offer smooth feeding, reduced tangling
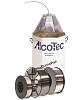
The role of flux in submerged arc welding performance
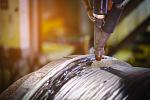
Three ESAB welding machines win Red Dot Awards for product design
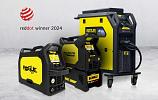
Power source added to cobot welding system for simplified automation
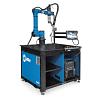
Torch made for welding thin, conductive sheet metal
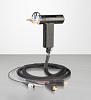
- Industry Events
Pipe and Tube Conference
- May 21 - 22, 2024
- Omaha, NE
World-Class Roll Forming Workshop
- June 5 - 6, 2024
- Louisville, KY
Advanced Laser Application Workshop
- June 25 - 27, 2024
- Novi, MI
Precision Press Brake Certificate Course
- July 31 - August 1, 2024
- Elgin,