- FMA
- The Fabricator
- FABTECH
- Canadian Metalworking
Categories
- Additive Manufacturing
- Aluminum Welding
- Arc Welding
- Assembly and Joining
- Automation and Robotics
- Bending and Forming
- Consumables
- Cutting and Weld Prep
- Electric Vehicles
- En Español
- Finishing
- Hydroforming
- Laser Cutting
- Laser Welding
- Machining
- Manufacturing Software
- Materials Handling
- Metals/Materials
- Oxyfuel Cutting
- Plasma Cutting
- Power Tools
- Punching and Other Holemaking
- Roll Forming
- Safety
- Sawing
- Shearing
- Shop Management
- Testing and Measuring
- Tube and Pipe Fabrication
- Tube and Pipe Production
- Waterjet Cutting
Industry Directory
Webcasts
Podcasts
FAB 40
Advertise
Subscribe
Account Login
Search
McNeilus Truck & Manufacturing, Inc. creates program to turn nonwelders into welders
6 questions with Chad Kleist of McNeilus Truck & Mfg.
- By Amanda Carlson
- September 18, 2019
- Article
- Arc Welding
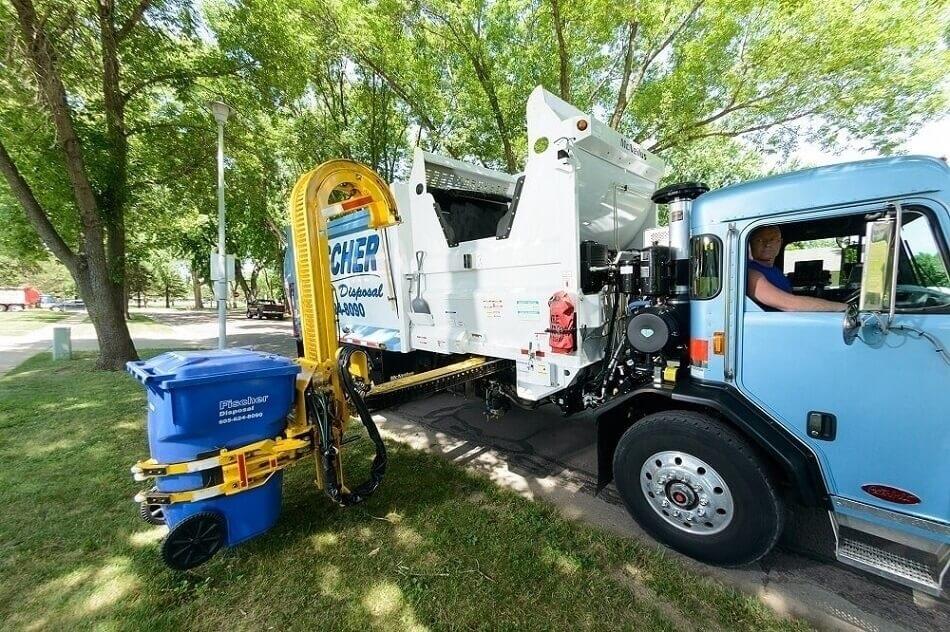
McNeilus, a manufacturer of refuse collection vehicles and concrete mixers, partnered with Riverland Community College to host an in-house weld training program in an effort to address its need for welders.
When Chad Kleist transitioned to his role as senior human resources manager at McNeilus Truck & Manufacturing Inc. (McNeilus), he quickly discovered that the challenges associated with finding skilled workers in a small community required action and a little ingenuity. And that those challenges have existed for a long time.
Located in Dodge Center, Minn., with its population of roughly 3,000 people, McNeilus is a manufacturer of refuse collection vehicles and concrete mixers. The subsidiary of Oshkosh Corp., Oshkosh, Wis., employs about 1,500 employees total both in Dodge
Center and at sales and service centers across the U.S.
But even a major OEM with a well-known parent company is susceptible to workforce issues. Population challenges make filling skilled positions such as production welding difficult. To mitigate this, Kleist leaned on the experience he gained addressing a similar problem elsewhere, with a few differences, of course.
Kleist spoke to The WELDER about the in-house welding program he helped to create at McNeilus, the decisions leading up to starting the program, and the response the company has gotten so far.
TW: What factors were at play at the time when management realized they needed more welders?
Kleist: A co-worker and I uncovered an internal document from almost 20 years ago that said the company needed to find a way to solve our workforce challenges, and that we needed to create a welding program. It’s funny to see that these problems have been around for so long. We’ve always had these challenges.
Before joining McNeilus, I was part of our corporate team at Oshkosh and was trying to solve our workforce challenges across the entire enterprise. For example, at Pierce Manufacturing, a subsidiary of Oshkosh Corp., I wrote a grant to create a program to convert assemblers into electricians.
The challenges at McNeilus are a bit more challenging because the unemployment rate is lower. The people just aren’t here. The ones that are here are employed. The unemployment rate here is low—I think recently it crept up to 2 percent.
`We wanted skilled welders, and I understood that. But when I looked at the numbers back in January 2018, we just didn’t have the people to pull from. We had to make a decision. We could hire contractors to help meet demand, and we do that already from time to time, but that’s not a sustainable model. So, we had to figure out how to find welders without having welders to pull from. I went back and re-examined the assembler-to-electrician program we did at Pierce and I wondered if we could do a similar kind of program in southeast Minnesota for welders.

During the four-week, 160-hour course, trainees earn an OSHA 10 certification and they learn how to set up the machine, how to use small tools, how to make measurements, basic math, and then how to perform pulsed gas metal arc welding (GMAW) on steel.
TW: Can you tell me a little bit about the program?
Kleist: We partnered with Riverland Community College, located in Albert Lea, Minnesota, to provide training at our facility. Bringing training on-site was a big deal to us. We wanted people within the program to weld and then be able to go on the floor and see what it turns into. Also, we wanted people to be there and to feel the energy of the McNeilus family.
The program is a four-week, 160-hour course. The first 16 hours are all about safety training, and with that trainees earn an OSHA 10 certification. After that they learn how to set up the machine, how to use small tools, how to make measurements, basic math, and then welding. They learn how to perform pulsed gas metal arc welding (GMAW) on steel.
After they complete with the 160 hours, they have 30 days to become what I would consider a full-time welder.
Our first class last November comprised current employees who were working as assemblers. We put 11 people through the first class, and maybe eight or a few more through the second class. All of a sudden operations came to me and said, “Hey, you’re taking all of our assemblers.” My thought was I could recruit and hire assemblers easily, but it turned out that wasn’t the case.
Because of that we completely revamped in March and I began recruiting externally for this weld program and left our assemblers alone. We created a new job requisition for someone who has no welding experience at all to come in, take the course, and have an opportunity to weld full-time with us.
TW: Was it difficult to attract external individuals to the program? What kind of response did you get initially?
Kleist: Responses trickled in slowly—at first we had a handful. We’ve had people in the past apply to be a welder, but we had to turn them away at that time because they just didn’t have the skills. Well, those people saw that now we did have an opportunity for them to weld and enrolled in the program.
Once we were up and running, the people who had gone through the program had a lot of success and liked it. So they told other people about it. And from there it went nuts because everyone was talking about it.
We had two brothers from Texas, for example. One brother moved up here, took the program, and loved it. His brother then moved up here to take the program. They used to weld with their dad on the farm growing up, so they had done it before but never had any formal training. After they took our program, they realized that they could have a career in this.
We recently had an executive chef from Minneapolis come through the program. He gave up his career because he always wanted to weld, and it turns out he is a fantastic welder. We went to a hiring event in Chicago and hired a veteran who got his HVAC associate degree at a tech school but always wanted to learn how to weld. We’ve got so many of these interesting stories.We try to find a healthy balance between external and internal people. This last class we had three external and three internal.
TW: How many people have you trained, what’s your retention rate so far?
Kleist: We’ve trained 55 people, and 40 are still with us. We are thrilled by that. We pay good wages here and we have amazing benefits because we are backed by an $8 billion company in Oshkosh. We are happy with our retention rate so far. We lost maybe two people for pay reasons and a few more who got to the line and just couldn’t do it. We offer those who can’t make it another opportunity for a role in the company. It’s been very successful, and it’s gotten a lot better.
We’ve added blueprint reading for our box line and drum line. You go to the drum line for the mixer and to our box line for the refuse vehicles. You can start practicing those prints right in class, which is pretty cool. We’ve also added overhead welding, because that is an area where some people struggle. They try to simulate different positions that they’ll end up with on the floor.
We’ve had the same instructor for six or seven consecutive courses, which helps a ton because he’s developing his teaching technique and gaining a greater understanding of what we do here. Because it’s on-site, he’s getting to know our weld supervisors and our product better. Matt, our instructor, is amazing. He’s giving people a skill that they didn’t have before. When they leave they are just in awe of what they can do.
TW: Do you see the program continuing and/or expanding?
Kleist: We are grateful to receive another grant for next year, so the question now is where are we going with this next year? A person who finishes this course is typically a Class B surface welder. Next year we believe current welders will want to upskill and become Class A surface welders.
“If you’re a welder and want to join a company that has a strong purpose and a great team, we invite you to learn more about McNeilus. If you’ve never welded before and always wanted to, don’t worry, we’ll train you. Being part of the Oshkosh family, we’re focused on helping communities thrive and each person who is part of our team will help with that mission to make a difference. We look forward to growing this program in the future and welcoming talented women and men to our team.”
McNeilus Truck & Mfg. Inc., mcneiluscompanies.com
About the Author
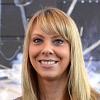
Amanda Carlson
2135 Point Blvd
Elgin, IL 60123
815-227-8260
Amanda Carlson was named as the editor for The WELDER in January 2017. She is responsible for coordinating and writing or editing all of the magazine’s editorial content. Before joining The WELDER, Amanda was a news editor for two years, coordinating and editing all product and industry news items for several publications and thefabricator.com.
About the Publication
subscribe now
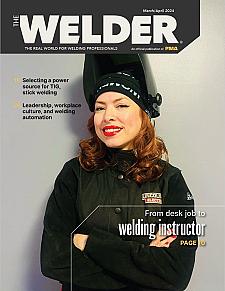
The Welder, formerly known as Practical Welding Today, is a showcase of the real people who make the products we use and work with every day. This magazine has served the welding community in North America well for more than 20 years.
start your free subscription- Stay connected from anywhere
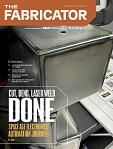
Easily access valuable industry resources now with full access to the digital edition of The Fabricator.
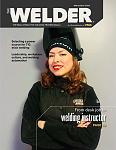
Easily access valuable industry resources now with full access to the digital edition of The Welder.
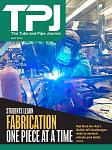
Easily access valuable industry resources now with full access to the digital edition of The Tube and Pipe Journal.
- Podcasting
- Podcast:
- The Fabricator Podcast
- Published:
- 04/30/2024
- Running Time:
- 53:00
Seth Feldman of Iowa-based Wertzbaugher Services joins The Fabricator Podcast to offer his take as a Gen Zer...
- Trending Articles
Aluminum MIG wires offer smooth feeding, reduced tangling
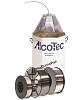
The role of flux in submerged arc welding performance
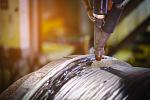
Three ESAB welding machines win Red Dot Awards for product design
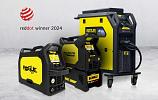
Power source added to cobot welding system for simplified automation
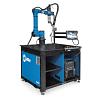
Torch made for welding thin, conductive sheet metal
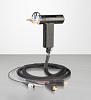
- Industry Events
Pipe and Tube Conference
- May 21 - 22, 2024
- Omaha, NE
World-Class Roll Forming Workshop
- June 5 - 6, 2024
- Louisville, KY
Advanced Laser Application Workshop
- June 25 - 27, 2024
- Novi, MI
Precision Press Brake Certificate Course
- July 31 - August 1, 2024
- Elgin,