- FMA
- The Fabricator
- FABTECH
- Canadian Metalworking
Categories
- Additive Manufacturing
- Aluminum Welding
- Arc Welding
- Assembly and Joining
- Automation and Robotics
- Bending and Forming
- Consumables
- Cutting and Weld Prep
- Electric Vehicles
- En Español
- Finishing
- Hydroforming
- Laser Cutting
- Laser Welding
- Machining
- Manufacturing Software
- Materials Handling
- Metals/Materials
- Oxyfuel Cutting
- Plasma Cutting
- Power Tools
- Punching and Other Holemaking
- Roll Forming
- Safety
- Sawing
- Shearing
- Shop Management
- Testing and Measuring
- Tube and Pipe Fabrication
- Tube and Pipe Production
- Waterjet Cutting
Industry Directory
Webcasts
Podcasts
FAB 40
Advertise
Subscribe
Account Login
Search
Stuck on SMAW?
Easy answers to 8 common electrode questions
- By Mike Crawford
- July 10, 2007
- Article
- Arc Welding
Whether you're a do-it-yourself welder who uses shielded metal arc welding (SMAW) only a few times a year or a professional welder who welds every day, one thing is certain: SMAW requires a lot of skill and electrode knowledge. Because variables such as storage techniques, electrode diameter, and flux composition all contribute to SMAW electrode selection and performance, arming yourself with basic knowledge can help you minimize confusion and ensure SMAW success.
- What are the most common SMAW electrodes?
Hundreds, if not thousands, of SMAW electrodes exist, but the most popular are mild steel electrodes that fall into the American Welding Society (AWS) classification A5.1. These include the 6010, 6011, 6012, 6013, 7014, 7024, and 7018 electrodes.
- How do I decipher these AWS electrode classifications?
AWS uses a standardized coding system to identify SMAW electrodes. Codes are printed on the side of each SMAW electrode and represent specific properties. For the mild steel electrodes mentioned previously, here is how the AWS system works:
- The letter E indicates an electrode.
- The first two digits represent the resulting weld's minimum tensile strength, measured in pounds per square inch (PSI). For example, the number 70 in a E7018 electrode indicates that the electrode will produce a weld bead with a minimum tensile strength of 70,000 PSI.
- The third digit represents the welding positions for which the electrode can be used. For example, 1 means the electrode can be used in all positions and 2 means it can be used on flat and horizontal.
- The fourth digit represents the coating type and the type of welding current (AC, DC, or both) that can be used with the electrode.
- How do 6010, 6011, 6012, and 6013 electrodes differ, and when should each be used?
The 6010 electrodes can be used only with DC power sources. They deliver deep penetration and have the ability to dig through rust, oil, paint, and dirt (see Figure 1). Many experienced pipe welders use these all-position electrodes for root welding passes that are located within a pipe. However, 6010 electrodes have an extremely tight arc, which can make them difficult for amateur welders to use.
The 6011 electrodes also can be used for all-position welding, except they require an AC welding power source. Like 6010 electrodes, 6011 electrodes produce a deep, penetrating arc that cuts through corroded or unclean metals. Many welders choose 6011 electrodes for maintenance and repair work when a DC power source is unavailable.
The 6012 electrodes work well in applications that require gap bridging between two joints. Many professional welders also choose 6012 electrodes for high-speed, high-current fillet welds in the horizontal position. These electrodes tend to produce a shallower penetration profile and dense slag that requires additional post welding cleaning.
The 6013 electrodes produce a soft arc with minimal spatter, offer moderate penetration, and have a easily removable slag. They should be used only to weld clean, new sheet metal.
- How do 7014, 7018, and 7024 electrodes differ, and when should each be used?
The 7014 electrodes produce about the same joint penetration as 6012 electrodes and are designed for use on carbon and low-alloy steels. 7014 electrodes contain a higher amount of iron powder, which increases deposition rate. They also can be used at higher amperages than 6012 electrodes.
The 7018 electrodes are easy to use and contain a thick flux with high powder content. They produce a smooth, quiet arc with minimal spatter and medium arc penetration. Many welders use 7018 electrodes to weld thick metals such as structural steel. They also produce strong welds with high impact properties (even in cold weather) and can be used on carbon steel, high-carbon, low-alloy, high-strength steel base metals (see Figure 2).
The 7024 electrodes contain a high amount of iron powder content that helps increase deposition rates and are often used for high-speed horizontal or flat fillet welds. These electrodes perform well on steel plate that is at least 1/4 inch thick. They also can be used on metals thicker than 1/2 in.
- What is the best way to choose a SMAW electrode?
Select an electrode that matches the base metal strength properties and composition. For example, when working on mild steel, generally any E60 or E70 electrode will work.
Next, match the electrode type to your welding position and consider your available power source. Remember, certain electrodes can be used only with DC or AC, while others can be used with either.
Assess the joint design and fit-up that you need and select an electrode that will provide the best penetration characteristics (digging, medium, or light). If you're working on a joint with tight fit-up or one that is not beveled, E6010 or E6011 will provide digging arcs to ensure sufficient penetration. For thin materials or joints with wide root openings, select an electrode with a light or soft arc, such as an E6013.
To avoid weld cracking on thick, heavy material or complicated joint designs, select an electrode with maximum ductility. Also consider the service condition the component will encounter and the specifications it must meet. Will it be used in a low-temperature, high-temperature, or shock-loading environment? For these applications, a low-hydrogen E7018 electrode works well.
You should also consider the production efficiency. When working in the flat position, electrodes with a high-iron powder content, as such E7014 or E7024, offer higher deposition rates. For critical applications, always check the welding specification and procedures for the electrode type.
- What function does the flux surrounding a SMAW electrode serve?
All SMAW electrodes comprise a wire surrounded by a coating called flux, which serves several important purposes. It is actually the flux, or the covering, on the electrode that dictates where and how an electrode can be used.
When you strike an arc, the flux burns and produces a series of complex chemical reactions. As the flux ingredients burn in the welding arc, they release shielding gas to protect the molten weld pool from atmospheric impurities. When the weld pool cools, the flux forms slag to protect the weld metal from oxidation and prevent porosity in the weld bead.
Flux also contains ionizing elements that make the arc more stable (especially when welding with an AC power source), along with alloys that give the weld its ductility and tensile strength. Some electrodes use flux with a higher concentration of iron powder to help increase deposition rates, while others contain added deoxidizers that act as cleaning agents and have the ability to penetrate corroded or dirty workpieces or mill scale.
- When is a high-deposition SMAW electrode appropriate?
High-deposition electrodes can help complete a job faster, but they are not without limitations. The additional iron powder in these electrodes makes the weld pool much more fluid, meaning that they can't be used for out-of-position welding.
They also cannot be used for critical or code-required applications, such as pressure vessel or boiler fabrication, where weld beads are subject to high stresses.
High-deposition electrodes, however, are an excellent choice for noncritical applications such as welding a simple liquid storage tank or two pieces of nonstructural metal.
- What is the proper way to store and redry SMAW electrodes?
A heated, low-humidity environment is the best storage place for SMAW electrodes. For example, many mild steel, low-hydrogen 7018 electrodes need to be stored at a temperature between 250 and 300 degrees.
Generally, electrodes' reconditioning temperatures are higher than the storage temperature to help eliminate excess moisture. The reconditioning environment for low-hydrogen 7018 electrodes should be from 500 to 800 degrees F for one to two hours.
Some electrodes, like 6011, only need to be stored dry at room temperature, which is defined as a humidity level not exceeding 70 percent and a temperature between 40 and 120 degrees F.
For specific storage and reconditioning times and temperatures, always refer to the manufacturer's recommendations.
About the Author
Mike Crawford
101 Trade Square
Troy, OH 45373
937-332-4000
About the Publication
subscribe now
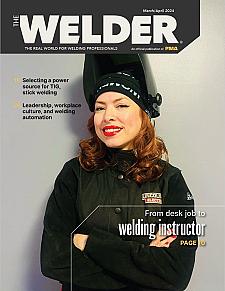
The Welder, formerly known as Practical Welding Today, is a showcase of the real people who make the products we use and work with every day. This magazine has served the welding community in North America well for more than 20 years.
start your free subscription- Stay connected from anywhere
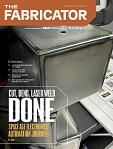
Easily access valuable industry resources now with full access to the digital edition of The Fabricator.
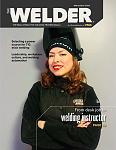
Easily access valuable industry resources now with full access to the digital edition of The Welder.
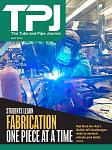
Easily access valuable industry resources now with full access to the digital edition of The Tube and Pipe Journal.
- Podcasting
- Podcast:
- The Fabricator Podcast
- Published:
- 04/30/2024
- Running Time:
- 53:00
Seth Feldman of Iowa-based Wertzbaugher Services joins The Fabricator Podcast to offer his take as a Gen Zer...
- Trending Articles
Aluminum MIG wires offer smooth feeding, reduced tangling
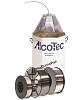
The role of flux in submerged arc welding performance
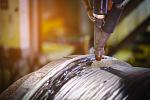
Three ESAB welding machines win Red Dot Awards for product design
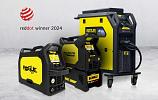
Power source added to cobot welding system for simplified automation
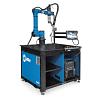
Connecticut students compete in Maritime Welding Competition
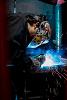
- Industry Events
Pipe and Tube Conference
- May 21 - 22, 2024
- Omaha, NE
World-Class Roll Forming Workshop
- June 5 - 6, 2024
- Louisville, KY
Advanced Laser Application Workshop
- June 25 - 27, 2024
- Novi, MI
Precision Press Brake Certificate Course
- July 31 - August 1, 2024
- Elgin,