- FMA
- The Fabricator
- FABTECH
- Canadian Metalworking
Categories
- Additive Manufacturing
- Aluminum Welding
- Arc Welding
- Assembly and Joining
- Automation and Robotics
- Bending and Forming
- Consumables
- Cutting and Weld Prep
- Electric Vehicles
- En Español
- Finishing
- Hydroforming
- Laser Cutting
- Laser Welding
- Machining
- Manufacturing Software
- Materials Handling
- Metals/Materials
- Oxyfuel Cutting
- Plasma Cutting
- Power Tools
- Punching and Other Holemaking
- Roll Forming
- Safety
- Sawing
- Shearing
- Shop Management
- Testing and Measuring
- Tube and Pipe Fabrication
- Tube and Pipe Production
- Waterjet Cutting
Industry Directory
Webcasts
Podcasts
FAB 40
Advertise
Subscribe
Account Login
Search
Safeguarding against robotic welding hazards
Ensuring worker protection in a robotic weld setting
- By Mike Carlson
- February 10, 2009
- Article
- Safety
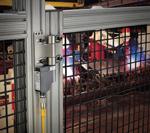
Figure 2 Interlock switches monitor the position of a guard or gate, controlling access to a hazardous area and shutting down or preventing machines from starting when the guard or gate is open.
Robotic welding allows for high throughput and overall production efficiency as well as improved worker safety. Yet without the proper safeguarding devices, robotic welding setups can produce hazards that pose a threat to operators.
Safeguarding refers to the aspects of machine safety that focus on protecting people who operate or come into contact with dangerous machines in the industrial environment. Safeguarding devices are systems that detect or prevent inadvertent or intentional access to a hazard. These devices work automatically to protect workers against identified hazards, including those found at the point of machine operation, power transmission, and other places moving parts are found.
Safety light screens, safety interlock switches, and two-hand controls are three types of safeguarding devices that can be used as part of a comprehensive safety system for robotic welding applications. Additional safety devices such as automatic weld screens and high-volume ventilation systems can also minimize exposure to other hazards in the welding environment.
Light Screens
A light screen is an optoelectronic device used to protect welders from a machine hazard. The basic elements of a safety light screen, or safety light curtain, are an LED emitter array and corresponding phototransistor receiver. They produce a "screen of light" with a specified resolution that detects intrusions into the sensing field (see Figure 1). When an opaque object—such as an arm or hand—is detected, it generates a stop signal to the machine control. This sensing field is installed between the hazard and personnel, at a distance from the hazard such that an individual cannot access the hazard.
Safety light screens offer reliability and tolerance to failures, preventing potentially costly and dangerous safety failures. They are suitable for use in applications in which the operator requires frequent access to a hazard and the hazardous machine motion can be stopped relatively quickly. Light screens are available in numerous designs to meet a variety of requirements. While some robotic setups require just a single curtain to send a stop signal to the machine control, light curtains also can be cascaded together to form an L- or U-shaped configuration that can guard multiple sides of a machine or provide area guarding within manufacturing cells.
These devices can be further configured for a specific application. For example, blanking involves desensitizing the light screen sensing field to ignore some objects but respond to other objects of a defined size. Muting can be used for automatic, temporary suspension of a light curtain to allow material feeding. Many light curtains feature an automatic reset, which is useful for reaching only through the sensing field. A manual reset is typically used when the operator passes through and becomes clear of the sensing field.
Interlock Switches
Safety interlock switches monitor the position of a guard or gate, and they are used to shut off power, control personnel access, and prevent the machine from starting when the guard is open (see Figure 2). While hard guarding includes fixed and adjustable guards, safety interlock switches can be used with interlocked guards.
A fixed guard is a simple, permanent type of machine guarding used as a barrier around a machine hazard to prevent access or to contain a hazard. However, this type of guard doesn't move and may need to be disassembled to allow access for maintenance. An adjustable guard, on the other hand, is adjustable to accommodate various jobs or tooling setups. Since it needs to be adjusted for each job, adjustable guards tend to require additional personnel training and supervision. Interlocking guards (such as doors, gates, and covers) can be moved and often are used when frequent access within the guard is needed. Guards that can be moved or removed generally need to be interlocked, preventing an accident from occurring if someone tries to access a guarded area.
A movable interlocked guard is recommended if operators need intermittent to frequent access to a hazardous area. If the guard is moved or opened, the interlock switches prevent cycle initiation or send a stop signal to the machine control. By locking the guard closed or in position, some interlock switches can also prevent access to the machine until it comes to a safe stop, maximizing safety by further protecting operators from potential injuries.
Interlock switches or devices are interfaced with a control system to monitor the position of the guard, preventing the guarded machine from operating unless the guard is closed and stopping the hazard if the guard is open. Interlock switches options are electromechanical, magnetic, RF tag, and optical, depending on the application. Optical-based interlock switches, for example, are good for ignoring EMI/RFI interference resulting from welding fields, making them suitable for many robotic welding applications.
Two-hand Control Systems
Two-hand control systems—comprised of two actuating buttons (or hand controls) and a safety module—are used to activate a machine and prevent false or unintended cycles (see Figure 3). When both buttons are concurrently actuated within a second, via mechanically based buttons or ergonomically designed buttons, a signal is sent to initiate and control a machine cycle.
Along with preventing unintentional machine actuation, two-hand controls can function as a safeguarding device by physically engaging both of an operator's hands, keeping them out of harm's way when a machine is operating. If an operator releases one or both actuating buttons, the safety module (or other logic device) immediately stops the machine cycle.
Safety Controllers
Safety PLCs and buses often are used to control disparate safety devices, but these methods can be costly and often more involved than what is actually required. Another option is a safety controller that can reduce the time and complexity of interfacing multiple safety-related devices by incorporating them into one device (see Figure 4). These safety controllers are available with flexible capabilities, such as muting and bypassing. They also can provide diagnostics to automatically detect faulty devices or wiring configuration errors, maintaining a comprehensive safety system for applications such as robotic welding.
While a complete safety system—often consisting of multiple safety devices—is essential in ensuring workers' safety and production efficiency, the designer and user should be aware that the system can become complex and difficult to manage. However, many safety solutions, as well as information and assistance, are available to aid in providing a safe working environment.
About the Author
Mike Carlson
9714 Tenth Ave. N.
Minneapolis, MN 55441
763-544-3164
About the Publication
subscribe now
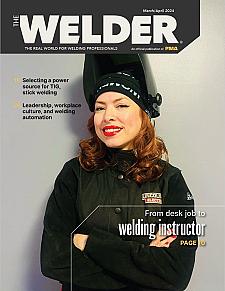
The Welder, formerly known as Practical Welding Today, is a showcase of the real people who make the products we use and work with every day. This magazine has served the welding community in North America well for more than 20 years.
start your free subscription- Stay connected from anywhere
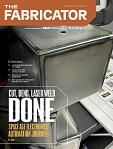
Easily access valuable industry resources now with full access to the digital edition of The Fabricator.
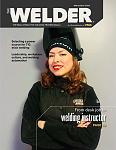
Easily access valuable industry resources now with full access to the digital edition of The Welder.
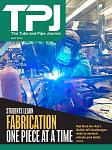
Easily access valuable industry resources now with full access to the digital edition of The Tube and Pipe Journal.
- Podcasting
- Podcast:
- The Fabricator Podcast
- Published:
- 04/16/2024
- Running Time:
- 63:29
In this episode of The Fabricator Podcast, Caleb Chamberlain, co-founder and CEO of OSH Cut, discusses his company’s...
- Industry Events
16th Annual Safety Conference
- April 30 - May 1, 2024
- Elgin,
Pipe and Tube Conference
- May 21 - 22, 2024
- Omaha, NE
World-Class Roll Forming Workshop
- June 5 - 6, 2024
- Louisville, KY
Advanced Laser Application Workshop
- June 25 - 27, 2024
- Novi, MI