- FMA
- The Fabricator
- FABTECH
- Canadian Metalworking
Categories
- Additive Manufacturing
- Aluminum Welding
- Arc Welding
- Assembly and Joining
- Automation and Robotics
- Bending and Forming
- Consumables
- Cutting and Weld Prep
- Electric Vehicles
- En Español
- Finishing
- Hydroforming
- Laser Cutting
- Laser Welding
- Machining
- Manufacturing Software
- Materials Handling
- Metals/Materials
- Oxyfuel Cutting
- Plasma Cutting
- Power Tools
- Punching and Other Holemaking
- Roll Forming
- Safety
- Sawing
- Shearing
- Shop Management
- Testing and Measuring
- Tube and Pipe Fabrication
- Tube and Pipe Production
- Waterjet Cutting
Industry Directory
Webcasts
Podcasts
FAB 40
Advertise
Subscribe
Account Login
Search
Z4® welding/grinding respirator combines safety, convenience, and comfort
Lightweight helmet with respirator suitable for grinding, welding
- By Amanda Carlson
- May 20, 2019
- Article
- Safety
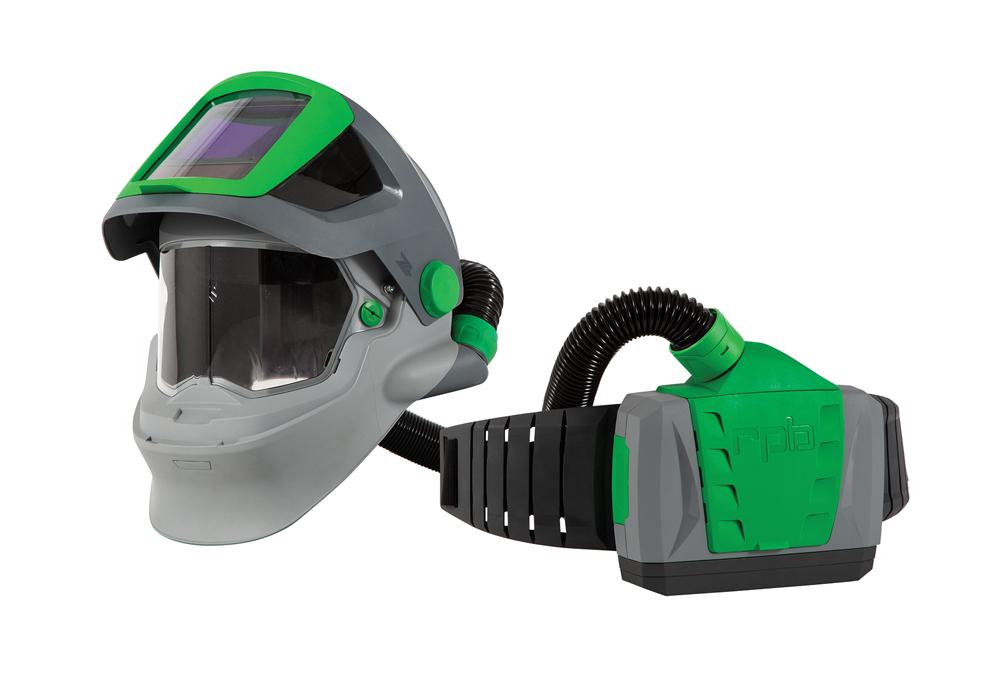
The welding/grinding respirator has an ANSI Z87+ approved grinding visor beneath a flip-up welding visor, which can be lifted quickly when necessary. The RPB Vision-Link™ offers 650 lumens and can be attached to the Z4 at any time, without modifications to the respirator.
Safety is essential in any work environment, but it’s paramount in metal fabrication. Unfortunately, safety sometimes can be uncomfortable or seem inconvenient.
In the world of welding and grinding, occasionally welders choose the convenience of no PPE during spot welding or quick grinding jobs. Other times welders don’t wear the proper PPE because it is heavy and uncomfortable. For this reason, RPB® Safety LLC, Royal Oak, Mich., has developed the Z4® welding/grinding respirator in hopes it will help convince welders that safety, convenience, and comfort can be one in the same.
The welding/grinding respirator combines the light-duty safety requirements of a grinding shield with the heavy-duty protection necessary for welding. One of the marquis features of the welding/grinding respirator is its overall weight of 1.77 lbs., which the company reports is 23 percent lighter than similar PPE.
Sam Kelly, engineering manager at RPB Safety, said the Z4 addresses a need to provide end users with a light and ergonomic helmet that provides protection for the user’s eyes and lungs. But most notably, the all-in-one respirator eliminates the need for separate PPE, ensuring users are protected at all times.
“More often than not, we came across welders wearing two head tops—a grinding shield and a welding helmet. We found they were constantly switching between the two, and in most cases, the grinding visor was not a respirator. The other point was the risk of the end user doing a quick grind job between welds without wearing any protection,” Kelly explained.
Lose the Weight, Configurate
The welding/grinding respirator evenly distributes weight to the sides of the head, eliminating top-heavy pressure points around the forehead and temples. This, in turn, helps to alleviate strain on the neck and upper back. The emphasis on weight distribution is the result of feedback the company learned through observing and talking with metalworkers out in the field.
“We worked very closely with manufacturing plants during our initial research and development stages. During each visit we observed and discussed end users’ likes and dislikes around their current head tops. We realized a lot of the feedback came down to comfort and weight distribution, so we put a lot of emphasis on that during development,” Kelly said.
For individualized comfort, users can configure certain aspects of the welding/grinding respirator to fit their preferences. One of the customizable elements is the adjustable, padded head suspension, which provides six points of adjustment to ensure the helmet fits securely. The optional side padding helps to distribute weight evenly for increased comfort and stability.
Another customizable element is the adjustable airflow, a dual-air distribution system that delivers 75 percent of the air through a swivel outlet, allowing users to direct the flow as they choose. The remaining 25 percent of the air is directed to the lens automatically to prevent fogging.
“We have heard that people in hot environments keep the head tops on even while they’re not working because the airflow in the helmet keeps them cool,” Kelly added.
The welding/grinding respirator has an ANSI Z87+ approved grinding visor beneath a flip-up welding visor, which can be lifted quickly when necessary. The RPB Vision-Link™ offers 650 lumens and can be attached to the Z4 at any time, without modifications to the respirator. The idea for this was generated from users who struggled to work in dimly lit environments, Kelly said.
Comfort is the name of the game, and it was the main design intention behind all features of the welding/grinding respirator.
RPB Safety LLC, www.rpbsafety.com
About the Author
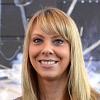
Amanda Carlson
2135 Point Blvd
Elgin, IL 60123
815-227-8260
Amanda Carlson was named as the editor for The WELDER in January 2017. She is responsible for coordinating and writing or editing all of the magazine’s editorial content. Before joining The WELDER, Amanda was a news editor for two years, coordinating and editing all product and industry news items for several publications and thefabricator.com.
About the Publication
subscribe now
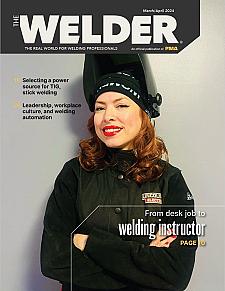
The Welder, formerly known as Practical Welding Today, is a showcase of the real people who make the products we use and work with every day. This magazine has served the welding community in North America well for more than 20 years.
start your free subscription- Stay connected from anywhere
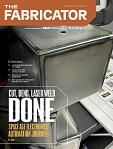
Easily access valuable industry resources now with full access to the digital edition of The Fabricator.
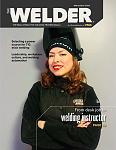
Easily access valuable industry resources now with full access to the digital edition of The Welder.
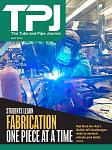
Easily access valuable industry resources now with full access to the digital edition of The Tube and Pipe Journal.
- Podcasting
- Podcast:
- The Fabricator Podcast
- Published:
- 04/30/2024
- Running Time:
- 53:00
Seth Feldman of Iowa-based Wertzbaugher Services joins The Fabricator Podcast to offer his take as a Gen Zer...
- Industry Events
Pipe and Tube Conference
- May 21 - 22, 2024
- Omaha, NE
World-Class Roll Forming Workshop
- June 5 - 6, 2024
- Louisville, KY
Advanced Laser Application Workshop
- June 25 - 27, 2024
- Novi, MI