- FMA
- The Fabricator
- FABTECH
- Canadian Metalworking
Categories
- Additive Manufacturing
- Aluminum Welding
- Arc Welding
- Assembly and Joining
- Automation and Robotics
- Bending and Forming
- Consumables
- Cutting and Weld Prep
- Electric Vehicles
- En Español
- Finishing
- Hydroforming
- Laser Cutting
- Laser Welding
- Machining
- Manufacturing Software
- Materials Handling
- Metals/Materials
- Oxyfuel Cutting
- Plasma Cutting
- Power Tools
- Punching and Other Holemaking
- Roll Forming
- Safety
- Sawing
- Shearing
- Shop Management
- Testing and Measuring
- Tube and Pipe Fabrication
- Tube and Pipe Production
- Waterjet Cutting
Industry Directory
Webcasts
Podcasts
FAB 40
Advertise
Subscribe
Account Login
Search
Tank fabrication goes vertical
Vessel and tank shell production success hinges on process expertise and good welding
- By Amanda Carlson and Rhonda Zatezalo
- August 12, 2020
- Article
- Shop Management
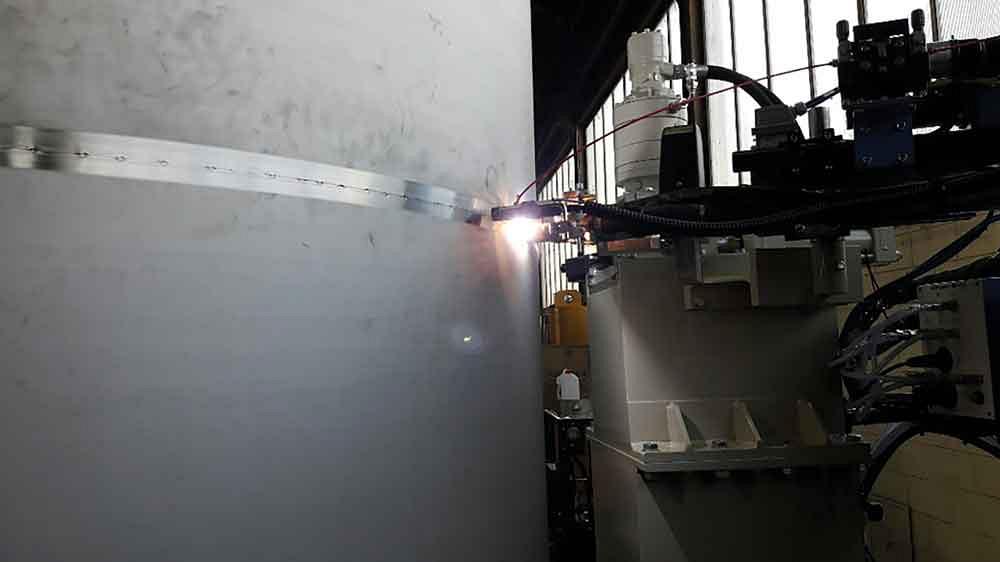
The IMCAR Station 1 for tank and vessel shell production is the first step in the vertical fabrication process. Image provided by Fabrication Solutions and Technologies (FST)
Keeping up with current fabrication technology is both a passion and career for Jeremiah Weekley. As president of Longview, Texas-based Fabrication Solutions and Technologies (FST), Weekley not only has to understand the dynamic nature of the industry, he also has to help customers understand and envision fabrication methods that are somewhat outside the box by North American standards.
FST offers systems for tank and vessel manufacturing in industries such as food and beverage, dairy, pharmaceutical, renewable energy, oil and gas, and aerospace. Its turnkey options provide all the components necessary for tank and vessel production. To sell customers on fabrication methods and equipment that are technologically progressive requires extensive knowledge of the process as well as equipment partners who can remove the uncertainty surrounding a new process with training and expertise.
A Different Way to Manufacture Tanks
Weekley has a comprehensive background in the realm of steel fabricating equipment. He worked his way up from an entry-level position at a company that sold imported steel fabricating equipment and into directing sales, marketing, logistics, and ordering inventory. From there he joined a startup company that manufactured API tank and code vessels in the Texas Permian Basin and then moved on to another company that manufactured engineered-to-order high-pressure vessels for natural gas, primarily midstream.
“I was able to spend nearly five years on the manufacturing side and learn all the things I thought I knew about manufacturing from my years of selling equipment and solutions. I got to see things from the client’s eyes and be far more involved in the manufacturing side, which laid a good foundation for me at FST when we launched,” Weekley said.
Weekley also had experience representing equipment manufactured by IMCAR Bending & Welding Technologies, a fabricator of tank production systems based in Italy. So when IMCAR approached him about possibly starting a business to represent its equipment full-time in the states, it seemed like a good fit.
“IMCAR knew that in order to capture the North American market, it needed a more direct sales and service approach, since they’re in Europe. They asked me if I would be interested in heading up this type of business with them in the states, and five years later here we are,” Weekley explained.
FST has standard lines of fabricating equipment, but Weekley said it specializes in premium equipment lines that offer a technological advantage that isn’t readily available from North American manufacturers.
“IMCAR is the manufacturer of these tank production systems that we’ve become synonymous with. We’ve done a lot of these systems in food and beverage production, API tank production, and we also have some clients in private space exploration. We’ve found that it can build a really good rocket.”
Horizonal Versus Vertical Tank Fabrication
Here in the U.S., it is somewhat the norm for tanks to be fabricated horizontally. The equipment that IMCAR manufactures, however, is set up to fabricate tanks vertically. Over time some companies have realized the efficiency advantages gained with vertical production, but by and large because of facilities’ typical height, more businesses here employ horizontal tank fabrication.
“The definite disadvantage when you’re in a market that traditionally produces tanks horizontally is the overall hook height, which would be your under-crane height. If your building was built to manufacture tanks horizontally, the building would be long and not so tall. When you’re fabricating a tank vertically, you don’t need a long building, but you do need a tall one. So sometimes the biggest disadvantage to vertical tank fabrication is the existing infrastructure. However, if you do have the building for it, the advantages of vertical tank production are numerous and far outweigh horizontal production,” Weekley said.
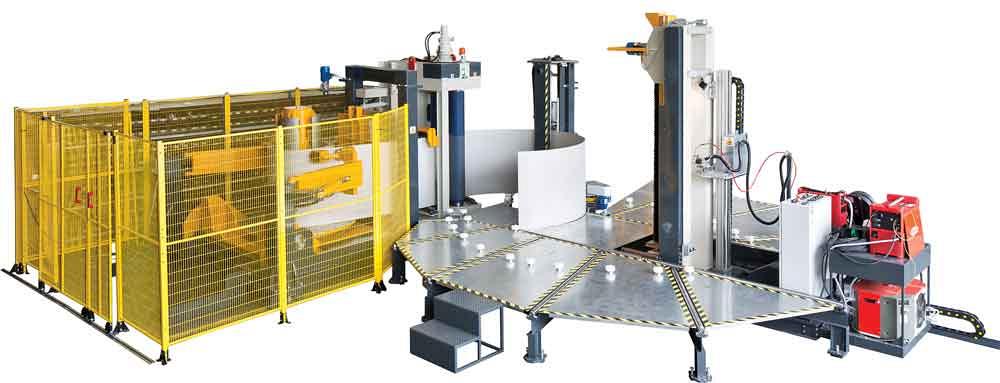
Station 2 employs the Fronius plasma TIG system that produces clean welds quickly. Image provided by Fronius
First, vertical tank fabrication doesn’t need as much space on the shop floor as horizontal fabrication does. Second, the tank shell does not require support rings to hold the shape. When that is in a horizontal position, on the other hand, measures must be taken to eliminate egg-shaping and the barrel effect that can produce misshaped vessels.
“Those measures include personnel having to go inside the tank to grind or weld the seam, polish, or back-weld. When you build it vertically with the proper welding method, you eliminate the need to go inside or to have to support that tank section,” Weekley said.
Last and most important, Weekley said fabricating a tank vertically offers a weld inch-per-minute efficiency of more than 5- to-1, and even greater if you include the ability to grind and polish weld seams.
Choosing a Welding Partner
Many variables go into creating a solid weld. FST knew from the beginning this was a challenge it had to solve to be successful in its chosen niche.
“We knew that if we didn't choose a welding partner that had the expertise, the technology, the support, and training that our clients needed, it would be disastrous. In fact, it had been done previously in the market to a certain degree. And every time, almost without fail, it was the source of contention and problems. We set out to solve that problem, and we did, through a collaboration with Fronius,” Weekley said.
By choosing to partner exclusively with Fronius for welding, the FST team gets occasional resistance from those companies unfamiliar with the brand. A lot of the welding industry is beholden to name recognition, and it’s natural to be skeptical of an unknown product.
When asked how they hurdle that obstacle, Weekley said, “Generally we're able to reduce that reluctance fairly quickly with demonstrations. Seeing the Fronius technology at work alleviates those concerns.”
For carbon steel applications, FST uses a Fronius dual-MIG system for simultaneous internal and external welding.
“We don’t do that because it’s needed to achieve full penetration, we do it because it allows a less skilled operator to perform the weld and still provide high-level results at an optimum speed,” Weekley said.
For stainless steel applications, FST paired its vertical systems with a Fronius plasma welding package. Though the plasma TIG welding process is not as well-known or highly used here as it is in Europe, it offers a fast, clean weld. The unfamiliarity that many fabricators have with plasma welding can make it a tough sell.
“A lot of times customers are more familiar with performing a MIG root with a TIG cap. But when we explain that they can do a full-penetration weld at a respectable speed with impeccable quality that’s easy to clean, it seems to sell itself when we demo it. We’ve found that it’s not as complicated as people would like to believe; it’s all about how we equip the customer, and from that standpoint, we work as a team with Fronius to ensure our customers are well-trained.”
During installation, not only are FST representatives there to train customers on systems setup and operation, a Fronius representative also is present to answer any and all welding questions.
“Our guys are also trained at Fronius, so everyone involved has a level of familiarity that benefits the client. Once they see what plasma welding is capable of doing, it opens a lot of eyes.”
Faster Results
Based on averages reported by FST’s customers, using the horizontal tank fabrication method (pre-FST) customers expected a range of 0.41 to 1.01 IPM of vessel production, depending on the method used. After these customers installed the vertical FST system, the rate of production jumped to a range of 3.8 to 4.01 IPM. It’s almost four to five times faster than horizontal production. Some clients have reported increases of more than 8 times faster than their previous method.
“We actually allow our clients to work from coil or plate. When you work from coil, you're able to produce, depending on your diameters, many, many tank sections from one coil as opposed to a truckload of plate steel coming in. Two employees spend half a day unloading that truck, only to pick it back up, put it in a plate roll, roll it, support it, and then move it down the line to fit it up. You have to keep it in round and out of the egg-shape situation.
“So you have to have support rings. We eliminate all that. Our people with a coil of steel can roll, cut, and plasma-weld a vertical seam and remove a completed tank section in less than 30 minutes. And traditionally you'd have guys working well over an hour to have that same shell. Not only that, but our shell is much more precise when it's in round form, it doesn't have the unbent straights that happen from traditional plate rolling. So what happens is when you start with a better tank shell, obviously the rest of your process is going to go smoother. So then when we stack those sections on one another, they are much easier to align, it welds much better, and we also have the added benefit of being able to grind or polish that seam with our system instead of a man walking inside of a horizontal tank section to do the same job.”
But none of that would matter without a sound, fast, and efficient welding system.
“It all hinges on the welding. In our world 80% of the project is our equipment, but if the 20% that includes the welding doesn’t go well, that’s all that matters.”
By partnering with hand-picked companies and working with expert consultants across the industry, the small team at FST can offer options that customers may not even be aware of. This is core to where Weekley says the company is headed.
“The future of FST is more client-centric and ensures we are staying on the cutting edge of technology. We have a few opportunities now to work with some clients to experiment with new methods and technologies of fully automating their facilities. We’re excited about this direction. I believe this will be a focus for FST teams in the future because the technology is evolving so rapidly.”
About the Authors
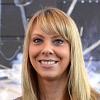
Amanda Carlson
2135 Point Blvd
Elgin, IL 60123
815-227-8260
Amanda Carlson was named as the editor for The WELDER in January 2017. She is responsible for coordinating and writing or editing all of the magazine’s editorial content. Before joining The WELDER, Amanda was a news editor for two years, coordinating and editing all product and industry news items for several publications and thefabricator.com.
Rhonda Zatezalo
Contributing Writer
248-783-6085
About the Publication
Related Companies
subscribe now
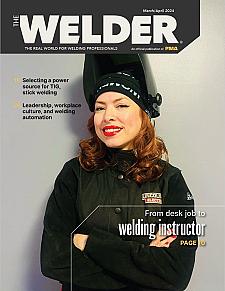
The Welder, formerly known as Practical Welding Today, is a showcase of the real people who make the products we use and work with every day. This magazine has served the welding community in North America well for more than 20 years.
start your free subscription- Stay connected from anywhere
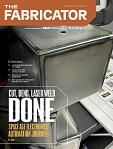
Easily access valuable industry resources now with full access to the digital edition of The Fabricator.
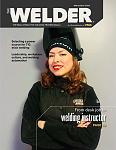
Easily access valuable industry resources now with full access to the digital edition of The Welder.
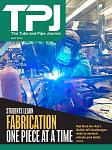
Easily access valuable industry resources now with full access to the digital edition of The Tube and Pipe Journal.
- Podcasting
- Podcast:
- The Fabricator Podcast
- Published:
- 04/30/2024
- Running Time:
- 53:00
Seth Feldman of Iowa-based Wertzbaugher Services joins The Fabricator Podcast to offer his take as a Gen Zer...
- Industry Events
16th Annual Safety Conference
- April 30 - May 1, 2024
- Elgin,
Pipe and Tube Conference
- May 21 - 22, 2024
- Omaha, NE
World-Class Roll Forming Workshop
- June 5 - 6, 2024
- Louisville, KY
Advanced Laser Application Workshop
- June 25 - 27, 2024
- Novi, MI