- FMA
- The Fabricator
- FABTECH
- Canadian Metalworking
Categories
- Additive Manufacturing
- Aluminum Welding
- Arc Welding
- Assembly and Joining
- Automation and Robotics
- Bending and Forming
- Consumables
- Cutting and Weld Prep
- Electric Vehicles
- En Español
- Finishing
- Hydroforming
- Laser Cutting
- Laser Welding
- Machining
- Manufacturing Software
- Materials Handling
- Metals/Materials
- Oxyfuel Cutting
- Plasma Cutting
- Power Tools
- Punching and Other Holemaking
- Roll Forming
- Safety
- Sawing
- Shearing
- Shop Management
- Testing and Measuring
- Tube and Pipe Fabrication
- Tube and Pipe Production
- Waterjet Cutting
Industry Directory
Webcasts
Podcasts
FAB 40
Advertise
Subscribe
Account Login
Search
In the COVID-19 era, flexibility is key for welders and other metal fabricators
- By Amanda Carlson
- May 27, 2020
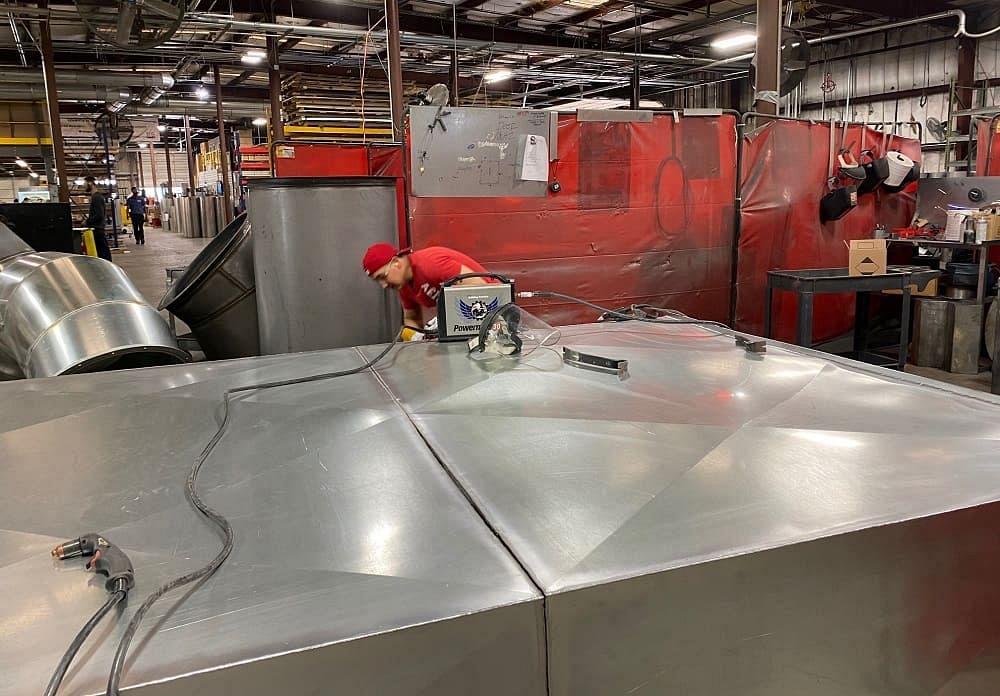
In March, US Duct received a call from a contractor in need of a certain HVAC component to complete a ventilation project at UNC Rex Hospital in Raleigh, N.C. By lunchtime the next day the company had designed, fabricated, revised, and shipped the component – a turnaround of slightly more than 24 hours. Image provided by US Duct
In the short time COVID-19 has been a part of our daily existence, it has taught us a lifetime’s worth of lessons.
First, it’s taught us to manage our frustration with our fellow man. Yes, I’m talking about the hoarding. Hoarding of toilet paper, paper towels, ramen noodles, meat, and cleaning products. I mean, does anyone really need eight containers of Clorox wipes? Come on. As Frank Costanza, played by the late Jerry Stiller on “Seinfeld,” used to say, “Serenity Now!”
We’ve all had to learn to deal with disappointment. I feel particularly sad for the high school seniors; the ones who had sports or activities canceled this spring, who didn’t get to go to prom, say goodbye to classmates and teachers, and who won’t get to don that gap and gown and walk in a real graduation ceremony. These milestones are a rite of passage that allows them to properly close the door on one life chapter before walking through the next.
But mostly it’s taught, or at least reminded, us of the importance of being flexible, and boy have we been flexible. From household budgets and at-home learning to working from home or not working at all, flexibility has been the name of the game.
And it hasn’t been an easy or painless game. Being flexible doesn’t feel very good when doing so means you have to postpone something you’ve worked really hard to put together.
In early March I read a story online about a brand-new welding and fabrication business in southwest Indiana and I thought they’d be a great fit for this issue.
The company comprises a husband-wife duo and the husband’s friend and former co-worker. Together they started a business to specialize in fabricating custom truck equipment and accessories as well as custom welding and fabrication projects. On March 2 they opened a 3,000-sq.-ft. facility, and based on that article, they were chomping at the bit to get to work.
I reached out to them shortly after the article was published to express my interest in featuring them in the May/June issue of The WELDER, setting up an in-person interview, which they agreed to. Well, due to COVID-19, many states in the Great Lakes region were told to shelter in place, scrapping our plans for an in-person interview. We decided to speak over the phone, but I was having trouble nailing down a date.
It turns out two of the company’s three employees had to step away temporarily to find other work because of slow business, so time was tight. Certainly, this was not the way they envisioned the startup of their dream, but in these situations, practicality wins. I hope I can catch up with them later this year.
While this is an example of the difficulties small businesses like this one face, there are also positive stories of fabricators coming together to fast-track an important project, like the one US Duct, Kernersville, N.C., completed for a nearby hospital.
You can see other examples of fabricators’ flexibility and adaptability on thefabricator.com. There is a reason that metal fabrication is designated as an essential business, and the stories featured there are evidence of that.
subscribe now
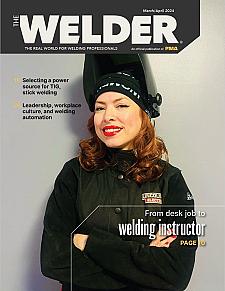
The Welder, formerly known as Practical Welding Today, is a showcase of the real people who make the products we use and work with every day. This magazine has served the welding community in North America well for more than 20 years.
start your free subscriptionAbout the Author
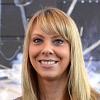
Amanda Carlson
2135 Point Blvd
Elgin, IL 60123
815-227-8260
Amanda Carlson was named as the editor for The WELDER in January 2017. She is responsible for coordinating and writing or editing all of the magazine’s editorial content. Before joining The WELDER, Amanda was a news editor for two years, coordinating and editing all product and industry news items for several publications and thefabricator.com.
About the Publication
- Stay connected from anywhere
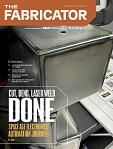
Easily access valuable industry resources now with full access to the digital edition of The Fabricator.
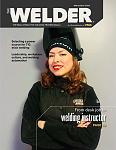
Easily access valuable industry resources now with full access to the digital edition of The Welder.
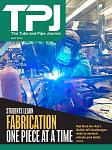
Easily access valuable industry resources now with full access to the digital edition of The Tube and Pipe Journal.
- Podcasting
- Podcast:
- The Fabricator Podcast
- Published:
- 04/16/2024
- Running Time:
- 63:29
In this episode of The Fabricator Podcast, Caleb Chamberlain, co-founder and CEO of OSH Cut, discusses his company’s...
- Industry Events
16th Annual Safety Conference
- April 30 - May 1, 2024
- Elgin,
Pipe and Tube Conference
- May 21 - 22, 2024
- Omaha, NE
World-Class Roll Forming Workshop
- June 5 - 6, 2024
- Louisville, KY
Advanced Laser Application Workshop
- June 25 - 27, 2024
- Novi, MI