- FMA
- The Fabricator
- FABTECH
- Canadian Metalworking
Categories
- Additive Manufacturing
- Aluminum Welding
- Arc Welding
- Assembly and Joining
- Automation and Robotics
- Bending and Forming
- Consumables
- Cutting and Weld Prep
- Electric Vehicles
- En Español
- Finishing
- Hydroforming
- Laser Cutting
- Laser Welding
- Machining
- Manufacturing Software
- Materials Handling
- Metals/Materials
- Oxyfuel Cutting
- Plasma Cutting
- Power Tools
- Punching and Other Holemaking
- Roll Forming
- Safety
- Sawing
- Shearing
- Shop Management
- Testing and Measuring
- Tube and Pipe Fabrication
- Tube and Pipe Production
- Waterjet Cutting
Industry Directory
Webcasts
Podcasts
FAB 40
Advertise
Subscribe
Account Login
Search
Setting standards for beverage production
On-site orbital welding helps build showcase brewery
- By Ken Grossman and Todd Barnum
- February 28, 2002
- Article
- Tube and Pipe Fabrication
![]() |
When Sierra Nevada planned for a major brewery expansion at its Chico, Calif., brewery in 1997, it decided to employ the newest generation of sanitary automatic valving in the filtration and yeast-handling areas. Because Sierra would install sanitary valving, it looked for a welding technology that could match the same high standards as the valving itself. After investigating all the alternatives, the company chose to use orbital gas tungsten arc welding (GTAW) wherever possible.
In addition to making high-quality welds, orbital welding helps to achieve consistent, repeatable welds on the inside diameter (ID) and outside diameter (OD). It also produces an aesthetically pleasing appearance.
Quality Under Control
The quality of tubing systems in the food and beverage industries is not as critical as in pharmaceutical and biochemical plants, but its importance is significant.
In breweries, the contamination threat to consumer health is minor, though the monetary loss from ruined product can be substantial.
The brewing process requires various temperatures—higher in some areas, lower in others. In high-temperature areas, bacterial growth is of less concern. Therefore, it is not unusual for different areas of a brewery to have different quality control standards.
Unlike dairies and processors of other perishable foods that must safeguard against pathogenic growth, breweries must safeguard against wild yeast and bacteria. Brewers want their specific strain of yeast to be the only strain in the product. Bacteria aren't necessarily harmful—some are responsible for making foods such as yogurt—but they can impart unusual and unexpected flavors in beer.
Irregularities in tubing systems, especially in weld joints, can lead to corrosion and biofouling, resulting in contamination or complete destruction of the product.
Clean welds on the inner surfaces help to prevent crevices in which contaminating particles can lodge or harmful bacteria can grow. Eliminating crevices supports efficient and trouble-free cleaning-in-place (CIP) procedures.
Expansion at Sierra Nevada
The foundation for today's showcase facility was laid in 1988 when Sierra moved from the original brewery to its current location. The welding task was large enough to justify hiring a full-time certified welder to assist with most of the original fabrication at the new location.
One fermentation area had an automated valving system with double-seat valve technology. When the company began planning the expansion, it decided to employ sanitary and labor-saving double-seat valving in the filtration and yeast-handling areas too.
The company also gained some experience with automation.
A Little More About a Little Weld Bead
Welding offers the potential for an aesthetically pleasing outer surface; however, the welding operation has a profound effect on the inner surface condition and requires careful consideration. Reducing surface roughness minimizes the time needed to purge a line to suitable purity levels. The greater the surface roughness, the greater the potential for moisture and particle contamination.Furthermore, mechanical fittings are sites for contamination, because gaps or crevices often appear in the vicinity of overlapping joints.
The area affected by welding is relatively small. A weld bead width typically is 3 millimeters, compared to typical tube lengths of 6 meters; the weld surface therefore comprises approximately 0.05 percent of the total area. Nevertheless, inappropriate welding conditions lead to unacceptable levels of contamination in an otherwise clean system.
In a showcase brewery, both the external and internal quality and consistency of the weld surfaces are equally important. Properly purged, automated, full-penetration welding—effecting external and internal welds simultaneously—made sense. Automated GTAW fusion welding precludes many welding problems and produces not only an aesthetically pleasing external weld but also a smooth internal finish that offers the least opportunity to harbor contaminants or harmful bacteria.
Orbital welding meets these criteria. Furthermore, tubes, fittings, and elbows do not require special preparation. Equally important, many costly errors associated with manual welding can be prevented with automated welding.
Designed for CIP
The heart of the new Sierra Nevada facility is a kit for a brew house, designed and mostly fabricated in Germany by the Huppmann Company. During the expansion, a planning committee comprised representatives from Sierra Nevada; a process engineer from Huppmann; and an engineer from Barnum Mechanical, a Newcastle, Calif., engineering firm. The engineer from Barnum Mechanical was appointed project manager.
The Barnum team worked closely with Sierra, developing the construction plan and coordinating crews of all the contractors on the construction team. In addition to assembling and installing the prefabricated systems at the brew house, Barnum engineers and construction crew designed and installed all the systems to support the brew house. This included the brewery's CIP systems, its yeast rooms, fermentation rooms, and bright beer filtration systems.
All of the systems at the brewery were designed for CIP. It has several independent CIP systems, each dedicated to a particular area of the plant—brew house, fermentation area, yeast area, the tubing between filtered beer and packaging lines, and the filtered beer.
The tubing system was designed for the most efficient CIP technology and sterilizing-in-place processes. The brewery uses a couple of cleaning methods, but wherever possible, heat is used. Water is circulated at a minimum of 180 degrees, typically for 60 minutes, to make sure the whole system has been heated to and held at that temperature. In areas that can't be heated practically, a hydrogen peroxide-based sanitizer is used at the end of the cleaning process.
Build-in-place Versus Prefabricating
Years ago contractors would order equipment such as tanks, pumps, valves, and tubing, go to a plant, and build it in place. Today that route is considered to be too expensive, especially where production is already ongoing, so as much as possible is prefabricated.
In its shops, Barnum combines a variety of stainless steel flow components, pumps, valves, and heat exchangers according to customer specifications, and then it prefabricates pasteurization systems, batching systems, syrup recovery systems, and CIP systems. These are mounted to a frame and controls are added, wired, and checked. Then it's mounted onto a skid, shipped, and installed in a plant.
Barnum Mechanical uses orbital welding to prefabricate the skidded systems. Its software tools and engineering team evolve each year as the company's experience grows. The company augments that experience with two orbital fusion welding systems from Astro Arc Polysoude. With power supply operating currents varying from 60 to 80 amps, these GTAW welding units typically required less than four minutes per weld on 4-in. tubing.
Orbital Welding On-site
The installation phase involves making many connections between tanks and flow panels, plus integrating new components into the existing process system. In addition, many of the control systems require connections. This involves cutting into existing production systems and adding valving without affecting production.
Plant operators don't see fabricators use a lot of in-plant orbital welding in this business because moisture and food particles, inherent in food and beverage processing facilities, can be detrimental to the orbital welding process.
However, the plant at Sierra Nevada was new, so the conditions were favorable for orbital welding.
Over the course of the four-month period in which the brewing equipment was installed, Barnum's construction crew performed thousands of welds, installing several miles of tube ranging from 1 to 4 inches in diameter with wall thicknesses from 0.065 in. to 0.083 in. Each orbital welding machine made approximately 95 welds per day during the installation. That process was expedited by the programs stored in the automatic welding machine's memory, which facilitated changing weld heads.
For the brewery project, each weld was inspected visually. Barnum also provided sample welds to help ensure quality would be maintained at various positions throughout the installation. Most of the welds merely required cleaning and the application of a Scotch-Brite® finish.
Ken Grossman is president of Sierra Nevada Brewing Co., 1075 E. 20th St., Chico, CA 95928, phone 530-345-2739, fax 530-893-1275, e-mail ken@sierranevada.com, Web site www.sierranevada.com. Since 1981 Sierra Nevada has brewed a variety of ales and lagers that are available throughout the U.S.
Tom Barnum is president of Barnum Mechanical Inc., 9244 Old State Highway 113, Newcastle, CA 95658, phone 916-652-7223, fax 916-652-5147, e-mail tom@barnummech.com, Web site www.barnummech.com. Barnum Mechanical is a design-and-build engineering house that serves companies in the beverage industry across the western U.S.
About the Publication
subscribe now
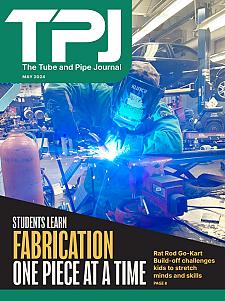
The Tube and Pipe Journal became the first magazine dedicated to serving the metal tube and pipe industry in 1990. Today, it remains the only North American publication devoted to this industry, and it has become the most trusted source of information for tube and pipe professionals.
start your free subscription- Stay connected from anywhere
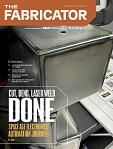
Easily access valuable industry resources now with full access to the digital edition of The Fabricator.
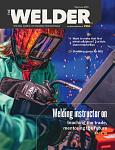
Easily access valuable industry resources now with full access to the digital edition of The Welder.
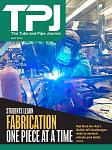
Easily access valuable industry resources now with full access to the digital edition of The Tube and Pipe Journal.
- Podcasting
- Podcast:
- The Fabricator Podcast
- Published:
- 05/07/2024
- Running Time:
- 67:38
Patrick Brunken, VP of Addison Machine Engineering, joins The Fabricator Podcast to talk about the tube and pipe...
- Trending Articles
Making the move from hard automation to robotic welding
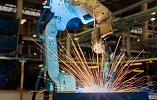
Zekelman Industries to invest $120 million in Arkansas expansion
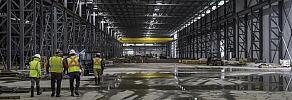
HGG Profiling Equipment names area sales manager
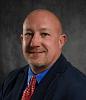
Miscellaneous metals fabricator increases productivity and opportunity with plasma cutting
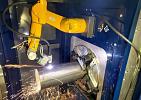
Students learn fabrication one piece at a time
- Industry Events
Laser Welding Certificate Course
- May 7 - August 6, 2024
- Farmington Hills, IL
World-Class Roll Forming Workshop
- June 5 - 6, 2024
- Louisville, KY
Advanced Laser Application Workshop
- June 25 - 27, 2024
- Novi, MI
Precision Press Brake Certificate Course
- July 31 - August 1, 2024
- Elgin,