Contributing Writer
- FMA
- The Fabricator
- FABTECH
- Canadian Metalworking
Categories
- Additive Manufacturing
- Aluminum Welding
- Arc Welding
- Assembly and Joining
- Automation and Robotics
- Bending and Forming
- Consumables
- Cutting and Weld Prep
- Electric Vehicles
- En Español
- Finishing
- Hydroforming
- Laser Cutting
- Laser Welding
- Machining
- Manufacturing Software
- Materials Handling
- Metals/Materials
- Oxyfuel Cutting
- Plasma Cutting
- Power Tools
- Punching and Other Holemaking
- Roll Forming
- Safety
- Sawing
- Shearing
- Shop Management
- Testing and Measuring
- Tube and Pipe Fabrication
- Tube and Pipe Production
- Waterjet Cutting
Industry Directory
Webcasts
Podcasts
FAB 40
Advertise
Subscribe
Account Login
Search
Using existing tooling for new product applications
Evaluating the tooling's capabilities and limitations
- By David Jenkins Jr.
- November 29, 2001
- Article
- Tube and Pipe Production
![]() |
Figure 1: This design is typical for the last fin pass for low-carbon steel using high-frequency welding. |
"In turbulent times, one must be innovative or be rendered defenseless." Peter Drucker said these words when addressing the Steel Service Center Institute several years ago, and they are still appropriate for today's climate in the tube, pipe, and roll form producing industries.
Many producers diversify their product lines during the slow part of the business cycle to maintain or improve market share. Manufacturing staffs are told to enhance the product offering at the lowest cost possible, but this creates potential for disappointing performance when production reality does not meet expectations.
One method of avoiding setbacks when planning to produce a new tubular or roll formed product is to review the new application with your tooling supplier before pilot production. Working together can help to reduce or eliminate any potential surprises associated with producing the new product.
Material
A common phrase used in tube and pipe production is, "We already make this size — it's just a material change." With the advanced alloys available today, problems may arise from not researching the new material's strength characteristics. Changing the material without changing the roll tooling may lead to problems related to springback or underforming.
![]() |
Figure 2: This design is similar to that shown in Figure 1, except that it includes a fin blade to maintain an open V angle for welding coated materials. |
Higher-strength material may require more forming passes; the addition of a finishing pass; or exchanging the position of an overform roll pass with that of a less severe forming pass. Additional passes may be necessary to lock in the final shape. In tube and pipe production, a change in the forming progression may be necessary to ensure proper presentation to the weld box.
Changing to galvanized, aluminized, or prepainted material necessitates modifications to the forming of the product if the existing tooling previously had been used to process plain stock. Designed relief in roll form tooling prevents peeling of coatings. The producer may opt to flash-chrome the tooling or use carbide rolls to alleviate galling or pickup on prepainted material.
In tube and pipe welding, changing the fin blade thickness or adding an edge conditioning unit helps to prevent weld impurities from prearcing, which can result in the low-melt-temperature coatings burning off in the welding process.
Figure 1shows a typical last fin pass design for low-carbon steel using high-frequency welding. Figure 2 shows the same pass with a fin blade designed to maintain an open V angle when welding coated materials.
Production Speed
In competitive markets, each company's survival depends on achieving a comparative advantage over its competitors. Comparative advantage in the tube, pipe, and roll forming industries generally lies in two areas: efficiency or production speed, or both. However, upgrading existing equipment or purchasing new equipment to enhance efficiency or production speed while ignoring tooling design can delay project start-up and product shipments.
![]() |
Figure 3: The difference in speed between outer diameter and the root diameter is in direct proportion to the RPM of the roll. This graph shows the speed difference on roll tooling with an 8.187-in. outer diameter and a 6-in. root diameter. The difference in speed is a leading cause of marking and pickup. |
Producers factor in anticipated production speeds — based on the projected line or welding speed — when quoting. Using roll tooling that was not designed for the new speeds can lead to cosmetic imperfections from roll marks or galling.
The most common cause of roll marks is the difference in surface speeds from the tooling root diameter to the last point of contact on the outer periphery of the roll. This difference in surface speeds increases proportionally as the production speed increases.
For example, consider the production of a 2.5-in.-dia. tube made with tooling with a 6-in. root diameter. The last point of contact between the tube and the surface of the roll is at the minor relief angle in the tooling, which measures 8.187 in. in diameter.
At the 6-in. root diameter, the surface speed of the roll is 1.57 ft. per rotation, and the 8.187-in. outer diameter has a surface speed of 2.14 ft. per rotation:
Root diameter: 6 in. p/12 in. per ft. = 1.57 ft.
Diameter at minor relief angle: 8.187 in. p/12 in. per ft. = 2.14 ft.
At 100 RPM, the outer diameter at the minor relief angle is traveling 57 FPM faster than the root diameter:
(100 RPM 2.14 ft.) – (100 RPM 1.57 ft.) = 57 FPM
The difference is directly proportional to the production speed. See Figure 3.
Modifying clearances or changing to a floating flange design — a type of roll tooling that allows the tooling flanges to spin independently of the driven center section — can address the cosmetic issues.
Specialty Tube Shapes
When exploring the possibilities of manufacturing special tube shapes — square, rectangular, and other nonround shapes — many novice producers make a direct comparison to round tube. Typically, many believe that as long as the outside periphery of the specialty shape is the same as the largest round tube their equipment can produce, the special shape can be formed.
However, the requirements of the shaped product (for example, corner radii versus material gauge) dictate the tooling design, and the tooling needs adequate force to form the tube.
This force is not the horsepower rating of the motor, but the torque the motor produces at the line speed. New direct-current and variable-speed alternating-current motors can reach full torque at 20 percent of the rated RPM values.
Older motors have a limited range of RPM in which full torque is achieved. Manufacturers may have to modify the drivetrain by changing sheave sizes, worm gear ratios, or even adding a transmission to transmit the torque to the tooling to form the shaped part properly.
One Size Does Not Fit All
Customer demands for new tube, pipe, and roll formed products are ever-changing. Incorporating new materials, increasing production speed, and developing new shapes introduce variables that producers must understand to successfully — and profitably — supply new products. Many components, such as entry tables, mills, and weld boxes, may well serve a variety of products. However, roll tooling is designed for one particular product and has limited application leeway.
About the Author
About the Publication
subscribe now
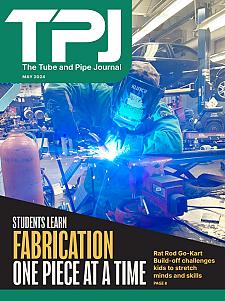
The Tube and Pipe Journal became the first magazine dedicated to serving the metal tube and pipe industry in 1990. Today, it remains the only North American publication devoted to this industry, and it has become the most trusted source of information for tube and pipe professionals.
start your free subscription- Stay connected from anywhere
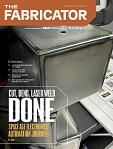
Easily access valuable industry resources now with full access to the digital edition of The Fabricator.
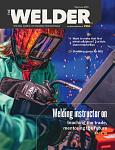
Easily access valuable industry resources now with full access to the digital edition of The Welder.
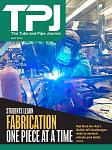
Easily access valuable industry resources now with full access to the digital edition of The Tube and Pipe Journal.
- Podcasting
- Podcast:
- The Fabricator Podcast
- Published:
- 05/07/2024
- Running Time:
- 67:38
Patrick Brunken, VP of Addison Machine Engineering, joins The Fabricator Podcast to talk about the tube and pipe...
- Trending Articles
Making the move from hard automation to robotic welding
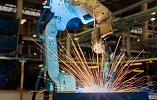
Zekelman Industries to invest $120 million in Arkansas expansion
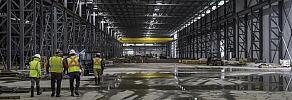
Brushless copper tubing cutter adjusts to ODs up to 2-1/8 in.
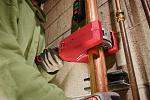
HGG Profiling Equipment names area sales manager
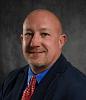
Miscellaneous metals fabricator increases productivity and opportunity with plasma cutting
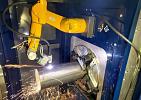
- Industry Events
Laser Welding Certificate Course
- May 7 - August 6, 2024
- Farmington Hills, IL
World-Class Roll Forming Workshop
- June 5 - 6, 2024
- Louisville, KY
Advanced Laser Application Workshop
- June 25 - 27, 2024
- Novi, MI
Precision Press Brake Certificate Course
- July 31 - August 1, 2024
- Elgin,