- FMA
- The Fabricator
- FABTECH
- Canadian Metalworking
Our Publications
Categories
- Additive Manufacturing
- Aluminum Welding
- Arc Welding
- Assembly and Joining
- Automation and Robotics
- Bending and Forming
- Consumables
- Cutting and Weld Prep
- Electric Vehicles
- En Español
- Finishing
- Hydroforming
- Laser Cutting
- Laser Welding
- Machining
- Manufacturing Software
- Materials Handling
- Metals/Materials
- Oxyfuel Cutting
- Plasma Cutting
- Power Tools
- Punching and Other Holemaking
- Roll Forming
- Safety
- Sawing
- Shearing
- Shop Management
- Testing and Measuring
- Tube and Pipe Fabrication
- Tube and Pipe Production
- Waterjet Cutting
Industry Directory
Webcasts
Podcasts
FAB 40
Advertise
Subscribe
Account Login
Search
Testing and Measuring - Page 2
-
- From The Fabricator
Digital caliper has 800-mm measuring range, integrated wireless connectivity
- Oct 10, 2023
- Product Release
Mahr Inc. has introduced the MarCal 18 EWR(i) digital caliper with a measuring range of 800 mm to handle larger components.
-
- From The Fabricator
Industrial-grade widefield stereo microscope offers distortion-free vision
- Sep 27, 2023
- Product Release
Titan Tool Supply Inc. has introduced the model FX-3 industrial-grade widefield stereo microscope for remote visual inspection tasks.
-
- From The Fabricator
Sensor provides optical seam tracking for arc and laser welding
- Sep 11, 2023
- Product Release
Scansonic has introduced the TH6D-Advanced optical seam sensor, offering 25- μm resolution and scalable pattern recognition algorithms.
Setting up for tube inspection success
- By Lincoln Brunner
- Sep 9, 2023
- Article
Mundo-Tech has taken the product of a team brainstorming session, 3D-printed fixtures, and turned it into an offshoot business that is now presenting a whole new world of possibilities.
Inspection increases accuracy, speed of tube production
- By Patrick Bauer
- Sep 7, 2023
- Article
For Yoshimura R&D, reducing setup time is critically important. The company has found one way to do that is reducing inspection time.
-
- From The Fabricator
Analyzer checks composition of 15 different two-gas mixtures
- Aug 24, 2023
- Product Release
The MFA 10.0 multigas analyzer from Witt can quickly check the composition of 15 different two-gas mixtures of argon, helium, CO2, methane, oxygen, nitrogen, and hydrogen.
-
- From The Fabricator
Blum-Novotest expands into new North American headquarters
- Aug 23, 2023
- News Release
Blum-Novotest Inc., a provider of measurement and testing technology, has moved into a new North American headquarters in Erlanger, Ky.
-
- From The Fabricator
Starrett names strategic accounts manager for industrial products
- Aug 23, 2023
- News Release
The L.S. Starrett Co. has appointed Seth Downing as strategic accounts manager North America, industrial products.
-
- From The Fabricator
Force/torque sensors now compatible with FANUC robots
- Aug 22, 2023
- Product Release
ATI Industrial Automation has announced the compatibility of its Multi-Axis Force/Torque (F/T) sensors with FANUC’s robots and Force Control software.
-
- From The Fabricator
Evident appoints new CEO and COO
- Aug 15, 2023
- News Release
Evident Corp., a manufacturer of inspection and testing equipment for maintenance, manufacturing, and environmental applications, has appointed William Wesley “Wes” Pringle as CEO and Hiroyuki Yoshimoto as president/COO.
Inspection system measures tube position and temperature during production
- Aug 9, 2023
- Product Release
Xiris Automation has introduced its Pre-Weld Inspection System for HF tube mills.
-
- From The Fabricator
Photon Automation expands operations with laser applications lab in Michigan
- Jul 13, 2023
- News Release
Greenfield, Ind.-based Photon Automation Inc., a provider of automated laser technology, has opened a laser applications laboratory in Farmington Hills, Mich.
-
- From The Welder
Miller’s Insight Centerpoint application measures welding data from Deltaweld power sources
- Jul 10, 2023
- Product Release
Miller Electric Mfg. LLC has announced that Deltaweld 350 and 500 power sources are now available with the Insight Centerpoint weld information application.
-
- From The Fabricator
Verisurf introduces ultrasonic thickness inspection with Renishaw probe
- Jul 7, 2023
- Product Release
Verisurf Software Inc. has announced support for the Renishaw RUP1 (REVO ultrasonic probe) in the upcoming Verisurf 2024 software release.
-
- From The Fabricator
Spectrolab S LAS02 stationary analyzer delivers high-end metal analysis
- Jun 29, 2023
- Product Release
Spectro Analytical Instruments has introduced the Spectrolab S LAS02 arc/spark OES metal analyzer for process control and research applications.
subscribe now
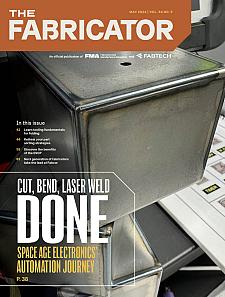
The Fabricator is North America's leading magazine for the metal forming and fabricating industry. The magazine delivers the news, technical articles, and case histories that enable fabricators to do their jobs more efficiently. The Fabricator has served the industry since 1970.
start your free subscription- Podcasting
- Podcast:
- The Fabricator Podcast
- Published:
- 04/16/2024
- Running Time:
- 63:29
In this episode of The Fabricator Podcast, Caleb Chamberlain, co-founder and CEO of OSH Cut, discusses his company’s...
- Trending Articles
Capturing, recording equipment inspection data for FMEA
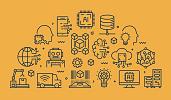
Tips for creating sheet metal tubes with perforations
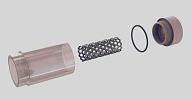
Are two heads better than one in fiber laser cutting?
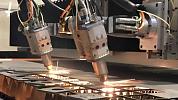
Supporting the metal fabricating industry through FMA
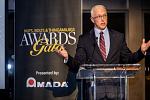
Zekelman Industries to invest $120 million in Arkansas expansion
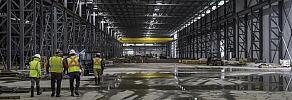
- Industry Events
16th Annual Safety Conference
- April 30 - May 1, 2024
- Elgin,
Pipe and Tube Conference
- May 21 - 22, 2024
- Omaha, NE
World-Class Roll Forming Workshop
- June 5 - 6, 2024
- Louisville, KY
Advanced Laser Application Workshop
- June 25 - 27, 2024
- Novi, MI
- Upcoming Webcasts
Navigating Change: The Manufacturer’s Guide to Change Management with ERP Implementation
- May 16, 2024
- Sponsored
- Presented By: ECI Software Solutions, M1