Global Product Manager
- FMA
- The Fabricator
- FABTECH
- Canadian Metalworking
Categories
- Additive Manufacturing
- Aluminum Welding
- Arc Welding
- Assembly and Joining
- Automation and Robotics
- Bending and Forming
- Consumables
- Cutting and Weld Prep
- Electric Vehicles
- En Español
- Finishing
- Hydroforming
- Laser Cutting
- Laser Welding
- Machining
- Manufacturing Software
- Materials Handling
- Metals/Materials
- Oxyfuel Cutting
- Plasma Cutting
- Power Tools
- Punching and Other Holemaking
- Roll Forming
- Safety
- Sawing
- Shearing
- Shop Management
- Testing and Measuring
- Tube and Pipe Fabrication
- Tube and Pipe Production
- Waterjet Cutting
Industry Directory
Webcasts
Podcasts
FAB 40
Advertise
Subscribe
Account Login
Search
Keys to selecting a compact inverter power source
Understanding TIG welding arc starts, current control, and gas flow control
- By Mike Sammons
- March 27, 2024
- Article
- Arc Welding
Some TIG torches feature a button for 2T/4T (on/off) control and a rotary thumb wheel to adjust amperage.
Do you want a gas tungsten arc welding (GTAW, or TIG) machine that can also perform shielded metal arc welding (SMAW, or stick), or can you get by with a stick machine that also works for occasional TIG welding? Many compact inverter-based welding power sources offer outputs for both processes, so the choice isn’t always clear. For welders who want to focus on TIG welding, the difference in arc starts, current control, and gas flow control capabilities are especially important (see Figure 1).
TIG Arc Starts
There are three different TIG arc starting methods: scratch start, lift TIG, and high-frequency (HF) noncontact arc start. Stick welding machines with direct current (DC) TIG capabilities use scratch start or lift TIG technology (as do many multiprocess welding machines) because they are simpler and keep power sources more affordable.
Scratch start is sometimes referred to as live TIG because the tungsten becomes electrically live (hot) when the operator turns on the power source. (As with stick welding, be careful of causing an unintended arc if the tungsten accidentally contacts the workpiece). To strike an arc, lightly scratch the tungsten on the material and lift it up 1/16 to 1/8 in. The motion is similar to striking a match or starting a stick electrode.
The drawback to this method is that small tungsten fragments can break off. If these fragments become included in the weld, they can create a hard spot that could lead to cracking. As a result, this method does not comply with welding codes and procedures for critical applications. Even if compliance is not an issue, consider grinding out arc starts to remove potential inclusions. One trick to avoid inclusions is to start and establish the arc on a piece of scrap metal adjacent to the weld and transfer it to the workpiece.
With lift TIG, the tungsten remains electrically cold until the operator initiates current flow, such as with a foot pedal or button on the TIG torch. Lift TIG creates positive arc starts that work well for many applications. Since there is no friction between the tungsten and the workpiece, there is little risk of contaminating the base material. However, because the tungsten does touch the workpiece, lift TIG does not comply with codes and welding procedure specifications that specify noncontact arc starts.
Some users get frustrated with this method, typically as a result of using a scratch start technique. To start the arc with lift TIG, follow this sequence:
- Lightly touch the torch to the workpiece and hold it there. The machine needs to sense the dead short.
- With the tungsten touching the workpiece, press the foot pedal or torch control.
- Lift the tungsten about 1/8 in. The welding machine will detect the voltage change and initiate current flow.
- Hold the tungsten in place until the arc becomes established. To keep the tungsten steady, rest the cup on the workpiece and rock the tungsten.
(Watch as lift TIG is demonstrated.)
To minimize the risk of tungsten inclusion, welding codes (ASME Section IX, API, AWS) and procedures specify a noncontact arc start method, notably for applications related to processing piping, pressure vessels, power generation, aerospace, structural steel, nonferrous metals, and delicate joints.
To create noncontact arc starts, TIG welding machines incorporate a circuit that provides pulses of HF voltage (but very low amperage) superimposed on the welding circuit. The HF ionizes the shielding gas and creates a path for the welding current to follow. With an inverter power source, HF is not necessary to maintain the arc in either DC or alternating current (AC)/DC welding, so the HF circuit shuts off after establishing the arc.
Incorporating HF arc starting circuitry does add significant cost to a welding machine. However, it is the price of admission for making code-quality TIG welds on ferrous materials, and it is required for AC TIG welding on nonferrous materials.
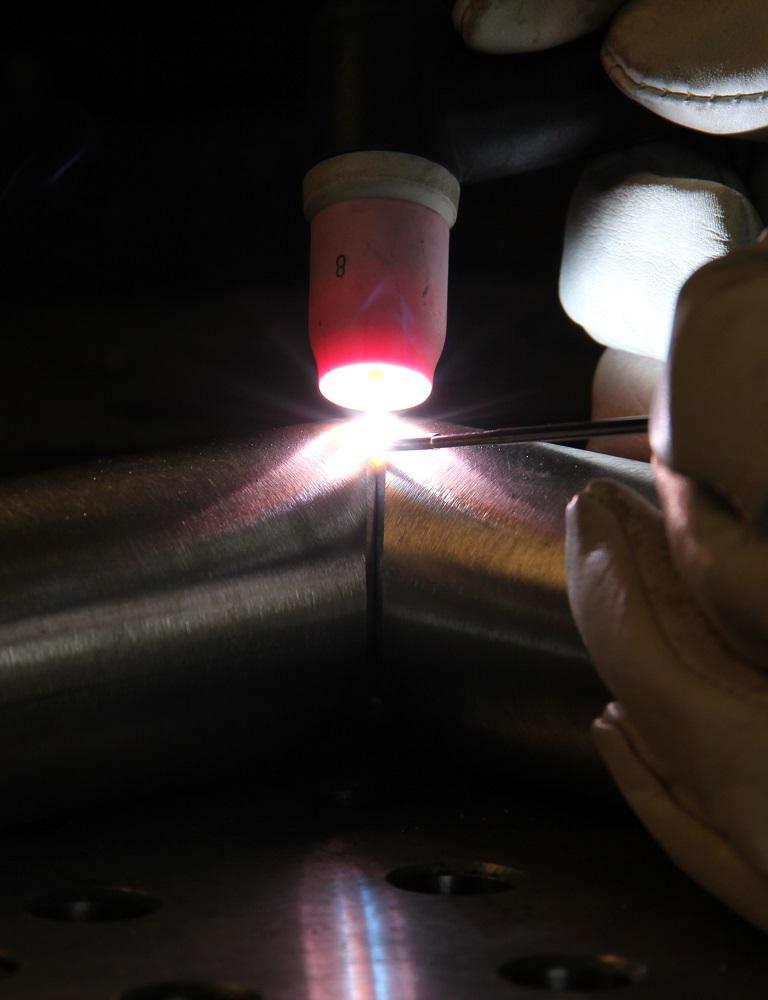
TIG functions such as adjustable upslope enable the operator to get settled and ensure the arc and filler wire are positioned correctly at the start of the weld.
Overall, most welders would prefer to use HF arc start because it is easy, precise, and clean. The only drawback is that HF voltage can interfere with electronics such as computers and CNCs (which is why following good earth-grounding procedures is important). To accommodate this situation, all professional-grade TIG inverters provide options for both lift TIG and HF arc starts. (Watch as TIG arc start options are demonstrated).
Current Control
A basic stick/TIG welding machine may not be able to remotely start the arc and control the welding current; however, all TIG machines will have a connection on the front panel for a remote control. For some welders, the ability to use a foot pedal to adjust current is a must-have function for controlling the weld puddle, especially for aluminum.
For ferrous metals, many welders are content with TIG machines that feature weld sequence controls triggered at the torch. Also known as “upslope” and “downslope,” these functions ramp the current up and down at the beginning and end of the weld. For example, users can set:
- Arc start current, set as percentage of the weld current, from 10% to 100%.
- Upslope time of 0 to 10 seconds.
- Downslope time of 0 to 10 seconds.
- End current, also set as a percentage of the weld current, from 10% to 100%.
Slope control mimics the function of a foot pedal and can be handy when welding in awkward positions that make use of a foot control impractical. Upslope enables the operator to get settled and ensure the arc and filler wire are positioned correctly at the start of the weld. Downslope allows the weld to cool gradually to help prevent crater cracking.
How slope control works depends on another setting, called 2T or 4T trigger control (the T stands for touch, as in the number of times the operator needs to touch the control during the weld sequence).
In 2T mode, the two-touch function is as follows:
- Press the torch button to start the upslope function; hold it to maintain the set welding current.
- Release the button to start the downslope sequence and terminate the arc.
In 4T mode, the four-touch function is as follows:
- Press and hold the trigger to weld at starting amperage.
- Release to start the upslope and weld at the amperage set on the front panel.
- Press the trigger again to start the downslope to the end current.
- Release the trigger to terminate the arc.
When a weld sequence is not set, 4T operates as a trigger-hold function, allowing the operator to weld without continuously holding down the torch button: Press and release the button to weld continuously with less hand strain; press and release the button again to terminate the arc.
Gas Flow Control
To keep stick/TIG welding machines more affordable, many manufacturers omit a shielding gas inlet port and solenoid valve. In this scenario, the torch gas line connects directly to the outlet of a flowmeter, and operators manually control gas flow with a valve on the torch. At some point, everyone forgets to turn the valve on (which will contaminate the base metal and tungsten) or close the valve (which wastes gas).
A power source intended primarily for TIG welding should feature a gas inlet port, a solenoid valve activated by remote, the current control, and controls to adjust gas pre- and postflow time. The general rule of thumb for postflow time is one second for every 10 amps of welding current. Extended postflow time is especially important when welding stainless steel and chrome-moly steel, as they are more prone to warping, oxidation, and hydrogen embrittlement, respectively.
Final Thoughts
Other key differentiators between TIG power sources and stick/TIG power sources include outputs for pulsed DC TIG and AC TIG for aluminum and nonferrous metals. Finally, note that today’s professional-grade inverter power sources offer equally excellent TIG and stick arc characteristics. Older-style conventional welding machines were literally wired to favor one process or the other, but that is no longer true with many inverters. The good news is that if you want a full-featured TIG machine, you can essentially obtain premium stick performance for free.
About the Author
About the Publication
Related Companies
subscribe now
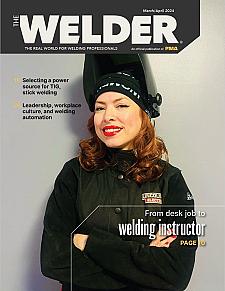
The Welder, formerly known as Practical Welding Today, is a showcase of the real people who make the products we use and work with every day. This magazine has served the welding community in North America well for more than 20 years.
start your free subscription- Stay connected from anywhere
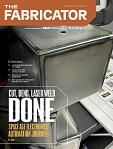
Easily access valuable industry resources now with full access to the digital edition of The Fabricator.
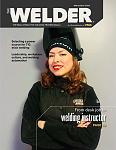
Easily access valuable industry resources now with full access to the digital edition of The Welder.
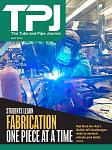
Easily access valuable industry resources now with full access to the digital edition of The Tube and Pipe Journal.
- Podcasting
- Podcast:
- The Fabricator Podcast
- Published:
- 04/16/2024
- Running Time:
- 63:29
In this episode of The Fabricator Podcast, Caleb Chamberlain, co-founder and CEO of OSH Cut, discusses his company’s...
- Trending Articles
Sheffield Forgemasters makes global leap in welding technology
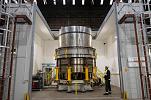
ESAB unveils Texas facility renovation
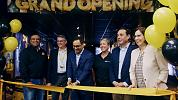
Engine-driven welding machines include integrated air compressors
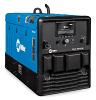
The impact of sine and square waves in aluminum AC welding, Part I
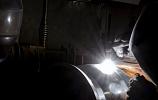
How welders can stay safe during grinding
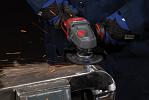
- Industry Events
16th Annual Safety Conference
- April 30 - May 1, 2024
- Elgin,
Pipe and Tube Conference
- May 21 - 22, 2024
- Omaha, NE
World-Class Roll Forming Workshop
- June 5 - 6, 2024
- Louisville, KY
Advanced Laser Application Workshop
- June 25 - 27, 2024
- Novi, MI