- FMA
- The Fabricator
- FABTECH
- Canadian Metalworking
Categories
- Additive Manufacturing
- Aluminum Welding
- Arc Welding
- Assembly and Joining
- Automation and Robotics
- Bending and Forming
- Consumables
- Cutting and Weld Prep
- Electric Vehicles
- En Español
- Finishing
- Hydroforming
- Laser Cutting
- Laser Welding
- Machining
- Manufacturing Software
- Materials Handling
- Metals/Materials
- Oxyfuel Cutting
- Plasma Cutting
- Power Tools
- Punching and Other Holemaking
- Roll Forming
- Safety
- Sawing
- Shearing
- Shop Management
- Testing and Measuring
- Tube and Pipe Fabrication
- Tube and Pipe Production
- Waterjet Cutting
Industry Directory
Webcasts
Podcasts
FAB 40
Advertise
Subscribe
Account Login
Search
Back to school with robotic welding
Northwest Iowa CC finds a niche with robotics training
- By Amanda Carlson
- July 6, 2009
- Article
- Automation and Robotics
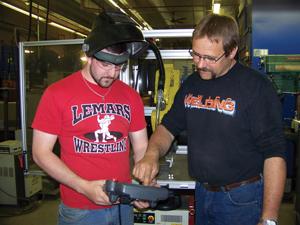
Neighboring industries have turned to automated welding to deal with the welder shortage. NWICC responded by integrating robotics training into its curriculum.
When your philosophy is lead, follow, or get out of the way, you'd better be prepared to back up that statement with more than just words.
That philosophy is the driving force behind the welding program at Northwest Iowa Community College (NWICC). At first glance, NWICC's weld program, located in Sheldon, Iowa, may seem like any other community college's. Enrollment is small but growing, and students are of all types: traditional students pursuing a welding diploma, students working toward a particular certification (structural pipe using mild steel, stainless steel, and aluminum), high school students getting a jump on their weld education requirements, and displaced workers from surrounding factories seeking a career change.
"We have small numbers, which is a benefit because we can spend a lot of one-on-one time with them. It's growing. I'm noticing a lot of interest for college students as well as high school students," said Robert Hoting, welding instructor and a graduate of the NWICC welding program.
But when industries in the area turned their focus on robotic welding, the instructors, administration, and advisory committee responded.
"A lot of the industry in our area is focusing on robotics due to the fact that welders have been in demand, and it's been tougher to fill those positions compared to a few years back. In order to fill some of those positions, especially on the repetitive parts, industry has turned toward robotics as that fill-in," Hoting explained
"We want to be the leaders. We want to come up with out-of-the-box ideas to keep the program moving forward."
Leading the Way
Nine years ago NWICC purchased a used robotic welding system and began training students on robotic programming. The program's advisory committee, made up of industry professionals from the area, believed robotics training was vital to the students' curriculum, given that many shops had automated welding operations in-house. NWICC's administration agreed.
NWICC purchased the robot to give students a little hands-on experience with programming, with the intention of teaching them the basic concepts of XYZ coordinates, moving the robot to the starting point, storing points, and then telling it how to move from point A to point B.
"Do we want it to go in a straight line, in a circular motion, or in a weave pattern? We were at least teaching them the concepts of points and space," Hoting said.
The robot was a nice addition to the program, but it didn't come without its own set of challenges. They were using the original software, which dated back to 1993, and Hoting likened it to using a computer from 1993 in 2008. Therefore, programming the robot to perform certain weld patterns could at times take up to two days. Also, the robot offered only short-circuit or spray-transfer gas metal arc welding modes, which limited what students could do with it.
What concerned Hoting the most was that he was teaching his students to operate a robot and use software that was both antiquated and not widely used by area industry. Since most of the companies employing automated welding were using a different brand of robot than what he had at the school, Hoting worried that the skills he was teaching would be more difficult to transfer on the job.
With that in mind, Hoting and NWICC decided it was time to upgrade their robotic welding equipment.
"Our old robot was still usable, but it's just outdated."
The ideal robotic cell would have to fit into the school's criteria of price, mobility, and usability. To find one that fit those criteria and was the same brand that neighboring employers used would be a bonus. What they found was the robotic welding education cell, offered in conjunction by The Lincoln Electric Co. and FANUC Robotics.
"We chose the robotic education cell because of its price, its mobility, and because it matches up with the robotics used in local industry."
The robotic welding education cell has a FANUC ARC Mate® 50iC/5L robotic arm with Arc Tool software in conjunction with a Lincoln Electric Power Wave® 355M and AutoDrive™ 4R90 wire feed welding package. The unit measures 81 in. tall, 27 in. wide, and 65 in. long and is designed to fit through a standard doorway. It is lightweight and sits on casters, making it portable for classroom-to-classroom demonstrations.
Programming Potential
The system was delivered to the school in October 2008 and was up and running shortly thereafter. Armed with material from a three-day robotics training course at Lincoln Electric, Cleveland, Hoting implemented a curriculum along with a few of his own touches.
Nine months after integrating the new robotic cell into his welding curriculum, Hoting and his staff seem to uncover new potential uses for the new robotic cell every day.
"We're updated now. The software is a Windows®-based system. Everything is based out of the teach pendant. You can develop your program off the teach pendant right where you're standing.
"It's so much easier to work with and change variables. If we wanted to change voltages or processes—for instance, from short-circuit to pulsed—all we have to do is go through the menu, pick it, and go."
Not only are they using it as a regular part of their diploma curriculum, but it also presents itself as a recruiting tool. The unit's portability allows them to load the robot on a trailer, take it to an area high school, and set up demonstrations with the industrial technology classes.
"For several students it's definitely a determining factor. When you look at one program versus another, a lot of times they'll look at equipment.
"One high school student was very interested. He brought his mom to show her the robot. I had him program how to weld a circle and he picked up on it within 15 minutes."
Hoting hopes that the robot will also attract local industries to send workers in need of robotic training to the school. Already active in industry training initiatives stemming from particular welding processes, Hoting hopes to add robotics programming to the list.
"I already do a lot of individualized industry training. Hopefully, this robotic system will open the door for some more of that type of training."
For now Hoting keeps his students—and the robot—pretty busy. They create a program that writes out the NWICC logo (see Figure 1); they make simple T-welds; and they weld pipe to plate, teaching the robot circular motion. Hoting also teaches the students how to build jigs for repetitive parts.
"Say there's a plate and a pipe that's 10 ft. tall. You have to program that robotic arm to reach around the pipe and weld around it without bumping the arm against the pipe. That takes a little planning, especially in this small robotic cell" (see Figure 2).
As for the critics who think automated welding is taking away jobs from manual welders, Hoting said this: "A common fear associated with robotic welding is that it's going to take away jobs. That's not the case. Sometimes your best welder is your best robotic programmer. They can see things happening in the weld that someone with less skill cannot."
About the Author
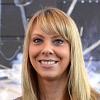
Amanda Carlson
2135 Point Blvd
Elgin, IL 60123
815-227-8260
Amanda Carlson was named as the editor for The WELDER in January 2017. She is responsible for coordinating and writing or editing all of the magazine’s editorial content. Before joining The WELDER, Amanda was a news editor for two years, coordinating and editing all product and industry news items for several publications and thefabricator.com.
About the Publication
subscribe now
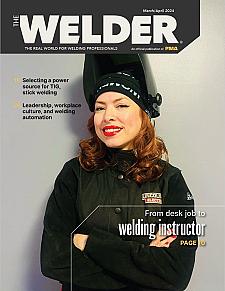
The Welder, formerly known as Practical Welding Today, is a showcase of the real people who make the products we use and work with every day. This magazine has served the welding community in North America well for more than 20 years.
start your free subscription- Stay connected from anywhere
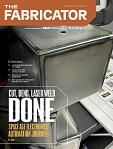
Easily access valuable industry resources now with full access to the digital edition of The Fabricator.
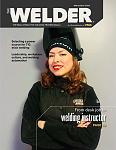
Easily access valuable industry resources now with full access to the digital edition of The Welder.
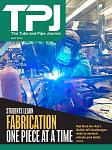
Easily access valuable industry resources now with full access to the digital edition of The Tube and Pipe Journal.
- Podcasting
- Podcast:
- The Fabricator Podcast
- Published:
- 04/16/2024
- Running Time:
- 63:29
In this episode of The Fabricator Podcast, Caleb Chamberlain, co-founder and CEO of OSH Cut, discusses his company’s...
- Industry Events
16th Annual Safety Conference
- April 30 - May 1, 2024
- Elgin,
Pipe and Tube Conference
- May 21 - 22, 2024
- Omaha, NE
World-Class Roll Forming Workshop
- June 5 - 6, 2024
- Louisville, KY
Advanced Laser Application Workshop
- June 25 - 27, 2024
- Novi, MI