- FMA
- The Fabricator
- FABTECH
- Canadian Metalworking
Our Publications
Categories
- Additive Manufacturing
- Aluminum Welding
- Arc Welding
- Assembly and Joining
- Automation and Robotics
- Bending and Forming
- Consumables
- Cutting and Weld Prep
- Electric Vehicles
- En Español
- Finishing
- Hydroforming
- Laser Cutting
- Laser Welding
- Machining
- Manufacturing Software
- Materials Handling
- Metals/Materials
- Oxyfuel Cutting
- Plasma Cutting
- Power Tools
- Punching and Other Holemaking
- Roll Forming
- Safety
- Sawing
- Shearing
- Shop Management
- Testing and Measuring
- Tube and Pipe Fabrication
- Tube and Pipe Production
- Waterjet Cutting
Industry Directory
Webcasts
Podcasts
FAB 40
Advertise
Subscribe
Account Login
Search
Additive lightens the load for aero-parts manufacturer
3D printing helps aerospace parts manufacturer produce lighter, more complex parts faster
- By Eric Lundin
- November 15, 2019
- Article
- Additive Manufacturing
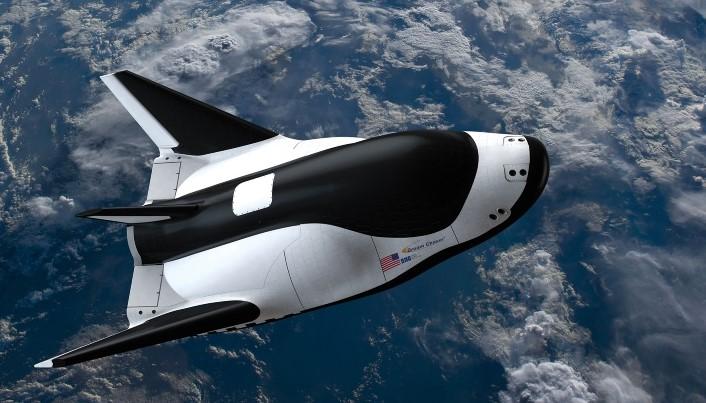
Keystone manufactures components for advanced space vehicles like the Dream Chaser cargo system, built to support the International Space Station. Sierra Nevada Corp.
A granddaddy in the world of manufacturing, machining has long been the key to making intricate, high-tolerance parts. This process is so ubiquitous that, to some laymen, machining is manufacturing. Although a capable and versatile process, a downside to machining is that much of the original material ends up as waste. In some cases, machining removes more than half of the original material, generating more waste than part by volume.
Rather than starting with a billet, casting, or forging and machining it to final form, the additive process builds parts layer by layer, depositing material and using heat to fuse it. The result is much less waste.
Also, whenever a machined part calls for complex or intricate features, the designer has to keep in mind the limitations of the machine tool and often has to make a compromise here or there. Additive manufacturing (AM) allows much more latitude in feature design.
Keystone Engineering Co., Long Beach, Calif., a manufacturer of space-flight systems and vehicles, has found that AM can help it make some components more efficiently than with conventional manufacturing processes while meeting crucial strength and weight targets. (Note: Keystone changed its name to NuSpace Inc. after this story was filed.—Ed.)Ready for Launch
“It’s all about the fuel,” said Wayne Tuttle, director of weld technology and mission assurance for Keystone. Founded in 1907, the company has focused on components for transportation systems from the outset. It transitioned from automotive and rail to aircraft and aerospace, keeping up with progress as technologies changed over the decades.
These days Keystone uses its portfolio of capabilities to make components for the latest space vehicles and systems, including high-altitude, long-endurance UAVs (unmanned aerial vehicles); the Dream Chaser cargo system, which will supply the International Space Station; the SM-3, Delta II, and Delta III rocket systems; and the 702HP, StarII, 601HP, GPS, and GPM Dawn communication satellites.
In all of Keystone’s modern endeavors, fuel-carrying capacity is critical. In anything that lifts off the Earth’s surface, the maximum weight, and therefore the maximum amount of fuel, is limited.
About 95 percent of the onboard fuel in a typical communications satellite launch is allocated to the rocket that lifts the satellite into space and puts it on a trajectory that gets it into the proper orbit.
Satellites run on solar power, so barring a component failure, their communication capability is essentially unlimited. If a satellite were to achieve a perfect orbit, in theory it would last for several decades.
However, a perfect orbit isn’t achievable; satellites drift over time. This is where the other 5 percent of the fuel comes into play. When a satellite wanders from its intended orbit, controllers fire onboard rockets to adjust the satellite’s position. Therefore, the practical limit for a satellite’s service life is related to the amount of fuel it carries when it is launched.
Tuttle and the Keystone team are driven by one main task: Reduce the weight of the components on the satellite. Every ounce they remove means an additional ounce of fuel, which extends the satellite’s service life.
Forging Ahead in Spinning
One manufactured part of particular interest at Keystone is the hemispherical component that caps a fuel tank.
“We make a cap that is 0.030-inch thick,” Tuttle said. Operators start with a forging 2.5-in. thick and machine it down to the final hemispherical shape and thickness, meaning that far more material gets machined away than gets used for the part. The waste amounts to hundreds of pounds of material per cap.
After machining the cap, Keystone adds features to it by welding or additional machining—attaching a retaining ring, creating a port, installing a locating pin or a valve, or adding any other attributes the manufacturer specifies for that tank cap. The company looked for a better way, and it found one in hot spinning. Using a forming tool to force a rotating sheet of material to conform to a hemispherical die is much faster than machining, and although a cap made this way requires a little machining, it wastes just a few dozen pounds per cap.
The company’s engineers wondered if they could find a better way to make features for the cap, striving to make parts in the precise shapes and sizes they needed rather than buy off-the-shelf components made by conventional methods.
They found a way with AM.
Longtime welding equipment and services provider Liburdi has been expanding its product offerings and has been developing AM systems.
Choosing an AM Process
AM isn’t a single process; it’s a field that comprises numerous processes, feedstocks, and power sources. Metal AM processes usually are divided into two main categories, which are powder bed fusion (PBF) and direct energy deposition (DED).
PBF applies heat selectively, fusing regions of a previously laid layer of powder, whereas DED fuses materials as they are deposited, explained J.J. Sixsmith, welding manager at Liburdi Automation Inc., a member of the Liburdi Group of Companies.
“PBF is well-suited to intricate parts, but part orientation is fixed, and the working envelope is limited to approximately 10 by 10 by 12 in.,” said Nejib Chekir, a member of Liburdi Group’s AM research team.
“DED is well-suited to making symmetric parts, making repairs, and adding features to existing parts, and it doesn’t have dimensional limits,” he added. The last two criteria are critical to Keystone’s customers’ applications.
Commonly used heat sources are power supplies designed for gas tungsten arc welding (GTAW), plasma welding, electron beam welding, and laser welding. They vary in heat input, heat-affected zones (HAZs), and cooling rates.
GTAW and plasma tend to provide the most heat; laser provides the most focused and smallest heat input, smallest HAZ, and fastest cooling rate. The electron beam process requires a vacuum chamber and thus is more cumbersome. It’s also slower because of the time needed to evacuate the chamber.
The feedstocks used are powder metal and wire. Powder offers the largest variety of alloys, and various powders can be mixed to create new blends. Drawbacks include the substantial care necessary in handling and storing them, because powders are prone to picking up impurities, including oxygen, and they are affected by humidity, both of which contribute to porosity and incomplete fusion.
Wire isn’t available in as many alloys as powder. When using wire, a manufacturer is limited to the commercially available alloys, and wires can’t be mixed to create new additive materials. Also, although wire is in a solid form and therefore less likely to develop voids, this doesn’t rule out porosity. Wire can be plagued by porosity if the parts and the wire are not properly cleaned and surface oxides are not removed just before the process.
For all that, wire has several advantages. It allows instantaneous changes in part volume by increasing or decreasing the feed rate or by switching wire diameter. Also, the wire addition process allows more freedom of movement in that it is fed directly into the melt pool.
A key differentiator is product consistency. Powder consistency varies, whereas the chemistry of wire products is consistent from one batch to the next.
Pulling It All Together
The variations in AM processes, their capabilities, and their limitations can seem extensive, but matching the process to the application isn’t insurmountable.
“The key is to adequately describe the problem you’re trying to solve,” Tuttle said. For fastening features to fuel tank caps, Keystone found that its problem was dimensions that exceeded the working envelope of PBF, which guided the company to DED.
The next choice was the material. Tuttle favors wire for its consistency.
“With wire, we know exactly what we’re going to get,” Tuttle said. “Consistency in chemistry and consistency in results.”
Next was the power source. Keystone didn’t get the complete fusion it needed from a laser, so it tried electron beam welding. More heat, dispersed more thoroughly throughout the part, worked like a charm.
The 3D printing process has another advantage for hemispherical caps. The conventional process involved welding hardware to the caps, which required a relatively thick substrate. AM uses less heat and directs it to the target area in a more focused manner than welding, so it works well to add features to relatively thinner substrates, Tuttle said.
The process developed by Liburdi meets all of Keystone’s criteria, and Keystone has leveraged the technology and applied for a patent on one of its components.
About the Author
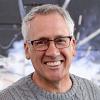
Eric Lundin
2135 Point Blvd
Elgin, IL 60123
815-227-8262
Eric Lundin worked on The Tube & Pipe Journal from 2000 to 2022.
About the Publication
- Podcasting
- Podcast:
- The Fabricator Podcast
- Published:
- 04/16/2024
- Running Time:
- 63:29
In this episode of The Fabricator Podcast, Caleb Chamberlain, co-founder and CEO of OSH Cut, discusses his company’s...
- Trending Articles
- Industry Events
16th Annual Safety Conference
- April 30 - May 1, 2024
- Elgin,
Pipe and Tube Conference
- May 21 - 22, 2024
- Omaha, NE
World-Class Roll Forming Workshop
- June 5 - 6, 2024
- Louisville, KY
Advanced Laser Application Workshop
- June 25 - 27, 2024
- Novi, MI