Editor-in-Chief
- FMA
- The Fabricator
- FABTECH
- Canadian Metalworking
Our Publications
Categories
- Additive Manufacturing
- Aluminum Welding
- Arc Welding
- Assembly and Joining
- Automation and Robotics
- Bending and Forming
- Consumables
- Cutting and Weld Prep
- Electric Vehicles
- En Español
- Finishing
- Hydroforming
- Laser Cutting
- Laser Welding
- Machining
- Manufacturing Software
- Materials Handling
- Metals/Materials
- Oxyfuel Cutting
- Plasma Cutting
- Power Tools
- Punching and Other Holemaking
- Roll Forming
- Safety
- Sawing
- Shearing
- Shop Management
- Testing and Measuring
- Tube and Pipe Fabrication
- Tube and Pipe Production
- Waterjet Cutting
Industry Directory
Webcasts
Podcasts
FAB 40
Advertise
Subscribe
Account Login
Search
Additive-manufactured press brake tools get users forming fast
Wilson Tool’s Bryan Rogers says 3D-printed press brake tooling can be made in days—not weeks like with steel
- By Don Nelson
- December 16, 2019
- Article
- Additive Manufacturing
Bryan Rogers explained during a video interview at FABTECH 2019 how Wilson Tool’s unique Bend3D program is designed to get press brake operators up and forming fast.
A user of the service receives an aluminum holder that’s fitted with additively manufactured polymer inserts robust enough to form metal. The inserts are used during the initial stages of a job, Rogers said. “They (users) can get their qualification done, get their customer approval—and the lead time is shorter than for steel tooling.” A polymer insert takes five to 10 days to turn around compared to four to eight weeks for steel, he said.
During this preproduction phase, steel tooling can be produced that fits into the same holder used for the polymer inserts.
Rogers also said that since May, Wilson has been conducting internal tests to determine if metal powders are suitable for 3D-printing metal tooling.
About the Author
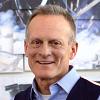
Don Nelson
2135 Point Blvd.
Elgin, IL 60123
(815)-227-8248
About the Publication
Related Companies
- Podcasting
- Podcast:
- The Fabricator Podcast
- Published:
- 04/16/2024
- Running Time:
- 63:29
In this episode of The Fabricator Podcast, Caleb Chamberlain, co-founder and CEO of OSH Cut, discusses his company’s...
- Trending Articles
- Industry Events
16th Annual Safety Conference
- April 30 - May 1, 2024
- Elgin,
Pipe and Tube Conference
- May 21 - 22, 2024
- Omaha, NE
World-Class Roll Forming Workshop
- June 5 - 6, 2024
- Louisville, KY
Advanced Laser Application Workshop
- June 25 - 27, 2024
- Novi, MI