- FMA
- The Fabricator
- FABTECH
- Canadian Metalworking
Our Publications
Categories
- Additive Manufacturing
- Aluminum Welding
- Arc Welding
- Assembly and Joining
- Automation and Robotics
- Bending and Forming
- Consumables
- Cutting and Weld Prep
- Electric Vehicles
- En Español
- Finishing
- Hydroforming
- Laser Cutting
- Laser Welding
- Machining
- Manufacturing Software
- Materials Handling
- Metals/Materials
- Oxyfuel Cutting
- Plasma Cutting
- Power Tools
- Punching and Other Holemaking
- Roll Forming
- Safety
- Sawing
- Shearing
- Shop Management
- Testing and Measuring
- Tube and Pipe Fabrication
- Tube and Pipe Production
- Waterjet Cutting
Industry Directory
Webcasts
Podcasts
FAB 40
Advertise
Subscribe
Account Login
Search
Footwear manufacturer transitions to 3D-printing PPE
Superfeet and its partners produce tens of thousands of PAPR hoods for health care workers
- By Kip Hanson
- May 4, 2020
- Article
- Additive Manufacturing
I’d love to write an entire article about one of the coolest AM organizations I’ve come across: Superfeet Worldwide Inc. But as with everyone else on Planet Earth, what I want must temporarily take a backseat to COVID-19.
Eric Hayes can relate. Hayes, the chief marketing officer at Superfeet, Ferndale, Wash., would rather be promoting his employer’s custom footwear line, spawned five years ago through the company’s sister company and 3D printing arm, Flowbuilt Manufacturing.
Flowbuilt has partnered with HP Inc. and is using three of that company’s Multi Jet Fusion (MJF) printers and Fitstation platform “to democratize personalization by making 3D scanning and gait analysis solutions available in stores around the world.” Flowbuilt uses the data from Fitstation scans to craft 3D-printed insoles and footwear tuned to each individual foot.
As I said, it’s a cool company. But after chatting with Hayes I learned there’s something even cooler than 3D-printing bespoke shoe insoles: using that same technology to save lives.
“Superfeet has a culture of giving,” he said. “When we started hearing about the health care crisis and resultant PPE shortages, some of our team reached out to others in the community to see how we might use our manufacturing capabilities to help. They told us the hospitals were in desperate need of a special hood known as a PAPR,” short for powered air-purifying respirator.
That conversation took place on a Thursday. By Tuesday of the following week, Hayes said, the company had delivered two functioning prototypes to the local hospital for evaluation. Two days after that the manufacturer was moving into production.
Superfeet had help. Another Washington-based company—Pioneer Aerofab, a manufacturer of airplane interiors—joined in to supply the fabric portion of the hood. And HP put Superfeet in touch with another member of the MJF manufacturing network, JawsTec Inc., American Falls, Idaho, which used its bank of printers to produce additional PAPR components.
The multistate, multicompany team quickly ramped up to 10,000 units a week, well on its way to the initial goal of 30,000 PAPRs. The team exceeded its goal in April, when it sent 42,000 PAPR hoods to hospitals.
“That’s the power of having a team of engineers equipped with 3D printers at your disposal, in that you can react very quickly, moving from prototype to full-scale production in days rather than months,” Hayes said. “It’s a great example of the new paradigm in manufacturing, as well as all that’s possible when people get together to address a common need.”
Other profiles in our COVID-19 Coverage:
• Idaho 3D printing farm Slant 3D
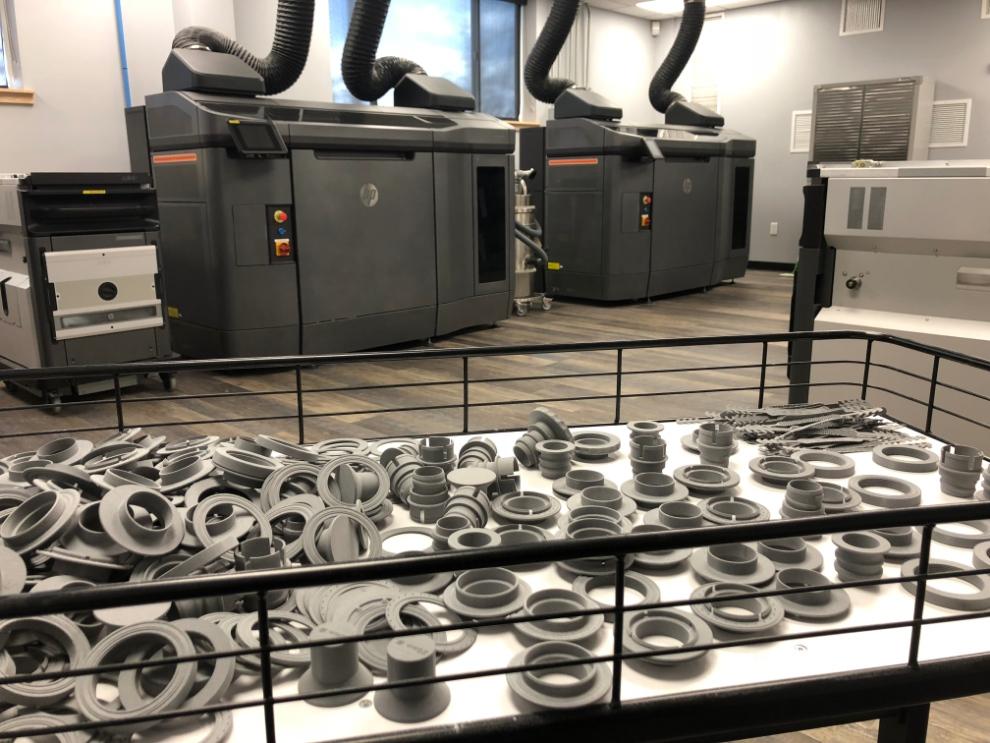
Some of the components Superfeet 3D-printed for the 42,000 PAPR hoods it produced in April with its partners. Superfeet
• Owner of Innovative Technical Resource Group
• Two Canadian 3D printing companies, VanDerZwaag Machining & Development and InkSmith
About the Author
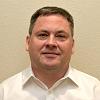
Kip Hanson
About the Publication
- Podcasting
- Podcast:
- The Fabricator Podcast
- Published:
- 04/16/2024
- Running Time:
- 63:29
In this episode of The Fabricator Podcast, Caleb Chamberlain, co-founder and CEO of OSH Cut, discusses his company’s...
- Trending Articles
- Industry Events
16th Annual Safety Conference
- April 30 - May 1, 2024
- Elgin,
Pipe and Tube Conference
- May 21 - 22, 2024
- Omaha, NE
World-Class Roll Forming Workshop
- June 5 - 6, 2024
- Louisville, KY
Advanced Laser Application Workshop
- June 25 - 27, 2024
- Novi, MI