Editor-in-Chief
- FMA
- The Fabricator
- FABTECH
- Canadian Metalworking
Our Publications
Categories
- Additive Manufacturing
- Aluminum Welding
- Arc Welding
- Assembly and Joining
- Automation and Robotics
- Bending and Forming
- Consumables
- Cutting and Weld Prep
- Electric Vehicles
- En Español
- Finishing
- Hydroforming
- Laser Cutting
- Laser Welding
- Machining
- Manufacturing Software
- Materials Handling
- Metals/Materials
- Oxyfuel Cutting
- Plasma Cutting
- Power Tools
- Punching and Other Holemaking
- Roll Forming
- Safety
- Sawing
- Shearing
- Shop Management
- Testing and Measuring
- Tube and Pipe Fabrication
- Tube and Pipe Production
- Waterjet Cutting
Industry Directory
Webcasts
Podcasts
FAB 40
Advertise
Subscribe
Account Login
Search
Steel used to make bunker-busting bombs adapted by Army for 3D printing
Using additive manufacturing technologies to build replacement parts on the battlefield could ‘revolutionize logistics’
- By Don Nelson
- March 5, 2019
- Article
- Additive Manufacturing
A low-alloy-steel powder with high toughness could one day allow soldiers in the field to 3D-print ultrastrong replacement parts. The powder is estimated to be about 50 percent stronger than commercially available feedstocks.
“I think it’s going to really revolutionize logistics,” said Dr. Brandon McWilliams, a materials manufacturing scientist at the U.S. Army Combat Capabilities Development Command’s Army Research Laboratory, Aberdeen Proving Ground, Md.
“Instead of worrying about carrying a whole truckload—or convoy-loads—of spares, you can potentially make anything you need,” he said, “as long as you have raw materials and a printer.”
The Army based the powder on the AF96 alloy the U.S. Air Force developed for making bunker bombs. The Army uses the alloy in powder bed fusion printers.
“We’re able to print up parts with internal structures that they would not necessarily be able to create with that much dimensional accuracy when they try to machine a part,” said Dr. Andelle Kudzal, a materials engineer on McWilliams’ team.
McWilliams noted that quickly printed, reliable 3D metal parts are still a long way off. The team has printed and delivered a usable empeller fan for the M1 Abrams tank, but the part isn’t qualified yet.
McWilliams said, “We still need to be able to answer, ‘Does this perform as good as the OEM part? Does this perform better?’”
McWilliams noted that there is resistance in some quarters to 3D-printed parts. “Some people think you can’t get good properties out of printed metal parts. We’re demonstrating that you can.”
About the Author
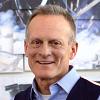
Don Nelson
2135 Point Blvd.
Elgin, IL 60123
(815)-227-8248
About the Publication
- Podcasting
- Podcast:
- The Fabricator Podcast
- Published:
- 04/16/2024
- Running Time:
- 63:29
In this episode of The Fabricator Podcast, Caleb Chamberlain, co-founder and CEO of OSH Cut, discusses his company’s...
- Trending Articles
- Industry Events
16th Annual Safety Conference
- April 30 - May 1, 2024
- Elgin,
Pipe and Tube Conference
- May 21 - 22, 2024
- Omaha, NE
World-Class Roll Forming Workshop
- June 5 - 6, 2024
- Louisville, KY
Advanced Laser Application Workshop
- June 25 - 27, 2024
- Novi, MI