Senior Editor
- FMA
- The Fabricator
- FABTECH
- Canadian Metalworking
Our Publications
Categories
- Additive Manufacturing
- Aluminum Welding
- Arc Welding
- Assembly and Joining
- Automation and Robotics
- Bending and Forming
- Consumables
- Cutting and Weld Prep
- Electric Vehicles
- En Español
- Finishing
- Hydroforming
- Laser Cutting
- Laser Welding
- Machining
- Manufacturing Software
- Materials Handling
- Metals/Materials
- Oxyfuel Cutting
- Plasma Cutting
- Power Tools
- Punching and Other Holemaking
- Roll Forming
- Safety
- Sawing
- Shearing
- Shop Management
- Testing and Measuring
- Tube and Pipe Fabrication
- Tube and Pipe Production
- Waterjet Cutting
Industry Directory
Webcasts
Podcasts
FAB 40
Advertise
Subscribe
Account Login
Search
A metal AM expert dishes on powder and system improvements
Manufacturers eyeing adoption of metal AM should start with basics like what AM can and can't do
- By Tim Heston
- February 1, 2019
Metal 3D printing crosses markets. And those in machining, fabrication, and other areas of conventional manufacturing have been paying attention.
A high-end, previously machined part could be totally redesigned to take advantage of all that additive manufacturing (AM) has to offer, complete with impossible-to-drill internal contours and impossible-to-mill contours. In this sense, metal additive complements machining.
On the other hand, metal 3D printing fuses metal particles together; it is essentially welding and, therefore, potentially in the wheelhouse of a high-end specialty fabricator. If a specialty fabricator—like those serving industries such as aerospace, medical, and defense—is eyeing metal AM, it should start with the basics: what these technologies are, what they can and can’t do, and what’s hype and what’s not.
I recently interviewed a member of TRUMPF Inc.’s additive manufacturing team—Franziska Maschowski, business development manager for TruPrint products. I asked her what’s needed to build good parts and how advancements in lasers have improved metal 3D printing.
“You need three factors to produce a good part,” Maschowski said. “You need a good machine, you need good process parameters, and you need good powders.”
Modern powders are specifically designed for metal AM. They exhibit properties like “feasibility” traits (analogous to weldability) that make them perfectly suited for a certain process or additive application. This includes materials with low levels of carbon—different from, say, tool steel alloys used for decades in the mold and die industry. A material chemistry that’s very machinable may not be feasible for a metal additive process.
Laser advancements have also pushed metal AM forward, Maschowski said. “We now have smaller focal diameters that result in better surface roughness and finer details, and you can build parts with higher dimensional accuracy.” Despite improvements in 3D printing capabilities, the process is not the best way to produce big parts. The reasons are the relatively high cost of powder and the lengthy build cycle.
But what about printing a number of small parts on a 3D printer with a large bed? This, Maschowski said, probably wouldn’t be a good approach either. Using a single laser to print a large bed of tiny parts still would take a long time and require a lot of powder. And if the parts were being built with a certified manufacturing process, there may be limits to how that powder can be reused.
A multilaser system would be plausible, but instead of powering one giant system, Maschowski suggested running several smaller, right-sized machines that could produce small parts on demand.
About the Author
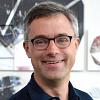
Tim Heston
2135 Point Blvd
Elgin, IL 60123
815-381-1314
Tim Heston, The Fabricator's senior editor, has covered the metal fabrication industry since 1998, starting his career at the American Welding Society's Welding Journal. Since then he has covered the full range of metal fabrication processes, from stamping, bending, and cutting to grinding and polishing. He joined The Fabricator's staff in October 2007.
About the Publication
- Podcasting
- Podcast:
- The Fabricator Podcast
- Published:
- 04/16/2024
- Running Time:
- 63:29
In this episode of The Fabricator Podcast, Caleb Chamberlain, co-founder and CEO of OSH Cut, discusses his company’s...
- Trending Articles
- Industry Events
16th Annual Safety Conference
- April 30 - May 1, 2024
- Elgin,
Pipe and Tube Conference
- May 21 - 22, 2024
- Omaha, NE
World-Class Roll Forming Workshop
- June 5 - 6, 2024
- Louisville, KY
Advanced Laser Application Workshop
- June 25 - 27, 2024
- Novi, MI