Editor-in-Chief
- FMA
- The Fabricator
- FABTECH
- Canadian Metalworking
Our Publications
Categories
- Additive Manufacturing
- Aluminum Welding
- Arc Welding
- Assembly and Joining
- Automation and Robotics
- Bending and Forming
- Consumables
- Cutting and Weld Prep
- Electric Vehicles
- En Español
- Finishing
- Hydroforming
- Laser Cutting
- Laser Welding
- Machining
- Manufacturing Software
- Materials Handling
- Metals/Materials
- Oxyfuel Cutting
- Plasma Cutting
- Power Tools
- Punching and Other Holemaking
- Roll Forming
- Safety
- Sawing
- Shearing
- Shop Management
- Testing and Measuring
- Tube and Pipe Fabrication
- Tube and Pipe Production
- Waterjet Cutting
Industry Directory
Webcasts
Podcasts
FAB 40
Advertise
Subscribe
Account Login
Search
Additive manufacturing isn’t just for billion-dollar organizations
Latest issue of The Additive Report highlights companies that have adopted AM technology—and discovered 3D printing's ‘empowering’ effects
- By Don Nelson
- January 22, 2019
Every few months or so I read about a university, government agency, or manufacturing company that’s opening a research center devoted to advanced technologies. These organizations tend to be large and well-funded.
GE, for example, invested approximately $1.5 billion in its Global Research Center, stocking it with advanced-technology equipment. Chicago’s Digital Manufacturing and Design Innovation Institute was launched with a $70 million grant from the Department of Defense and $250 million in funding from the private sector. And in December, Ford Motor Co. rolled out its latest model—a $45 million research center devoted to cutting-edge technologies like 3D printing.
A company looking to successfully adopt additive manufacturing (AM) or other advanced process doesn’t need to be a multibillion-dollar multinational. Nor does it need to open a research center.
The key to success, writes a columnist in the February 2019 issue of The Additive Report, is “being receptive to trying the technology.”
A key editorial mission of The Additive Report is to tell the stories of manufacturing companies whose roots lie in earlier-generation technologies but are receptive to trying next-gen processes like AM.
One such company profiled in February is Boyce Technologies, a manufacturer of security and communications equipment. The company primarily fabricates and CNC-machines its products. It began experimenting with AM a couple of years ago.
Boyce 3D-prints prototypes, but mostly uses the technology for production work. It found that certain parts—the housings for LED strips, for example—are better when additively manufactured than when machined. With the company’s traditional production method, LED strips would need to be inserted into a block of machined ABS plastic. 3D printing allows Boyce to design a series of profiles that hold the strips and let the antenna equipment be embedded in the part. (Click here to read the report.)
Another company highlighted in the February Additive Report is VIBA, a French motorcycle builder. It’s selling a redesigned, modernized version of Honda’s iconic Monkey motorbike from the 1960s.
VIBA’s take on the limited-edition two-wheeler features several 3D-printed components. These include the upper handlebar riser, luggage rack, mudguard/headlight, and fuel tank.
The aluminum tank best illustrates AM’s benefits. It features an internal honeycomb structure that prevents fuel from sloshing around during acceleration, braking, and turning, which enhances stability. And because the tank was printed as one piece, it has no welding seams, giving it a super-sleek profile. (Click here to read the report.)
Another advantage AM delivers is that it’s a “hands-off” operation, according to an engineer at Intralox LLC USA, a New Orleans manufacturer of conveyors. He said it’s inefficient to produce one part on a machining center because of the setup time involved.
“3D printing really has minimal setup,” he said in article in the February issue. “And it’s a hands-off process. Someone who’s not an expert machinist, like me … can walk up to the machine and hit go. It’s pretty empowering.”
About the Author
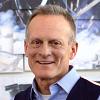
Don Nelson
2135 Point Blvd.
Elgin, IL 60123
(815)-227-8248
About the Publication
- Podcasting
- Podcast:
- The Fabricator Podcast
- Published:
- 04/16/2024
- Running Time:
- 63:29
In this episode of The Fabricator Podcast, Caleb Chamberlain, co-founder and CEO of OSH Cut, discusses his company’s...
- Trending Articles
- Industry Events
16th Annual Safety Conference
- April 30 - May 1, 2024
- Elgin,
Pipe and Tube Conference
- May 21 - 22, 2024
- Omaha, NE
World-Class Roll Forming Workshop
- June 5 - 6, 2024
- Louisville, KY
Advanced Laser Application Workshop
- June 25 - 27, 2024
- Novi, MI