- FMA
- The Fabricator
- FABTECH
- Canadian Metalworking
Our Publications
Categories
- Additive Manufacturing
- Aluminum Welding
- Arc Welding
- Assembly and Joining
- Automation and Robotics
- Bending and Forming
- Consumables
- Cutting and Weld Prep
- Electric Vehicles
- En Español
- Finishing
- Hydroforming
- Laser Cutting
- Laser Welding
- Machining
- Manufacturing Software
- Materials Handling
- Metals/Materials
- Oxyfuel Cutting
- Plasma Cutting
- Power Tools
- Punching and Other Holemaking
- Roll Forming
- Safety
- Sawing
- Shearing
- Shop Management
- Testing and Measuring
- Tube and Pipe Fabrication
- Tube and Pipe Production
- Waterjet Cutting
Industry Directory
Webcasts
Podcasts
FAB 40
Advertise
Subscribe
Account Login
Search
Hardfacing: a new take on a very old technique
The first additive process was, arguably, hardfacing
- By Kip Hanson
- UPDATED February 18, 2020
- February 18, 2020
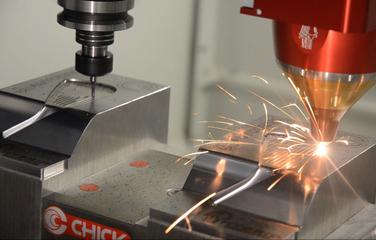
Cladding heads affix to machines tools, turning them into additive/subtractive systems. Hybrid Manufacturing Technologies
I’m an old machinist, one who always assumed that a company I’ve known my entire adult life—Kennametal—was responsible for the development of hardfacing. Never heard of it? It’s the application of a wear-resistant alloy to a softer substrate, usually by welding. However, as you’ll see, there are newer, far more capable methods of hardfacing on the rise.
One of the most common hardfacing alloys is Stellite, a material that Kennametal trademarked years ago. Kennametal didn’t invent Stellite. Elwood Haynes did. He also invented another tough-to-machine metal: Hastelloy. I won’t go into the history of the Haynes Stellite Co., except to say that at one point Kennametal acquired the Stellite part of the business and the rest went on to become Haynes International.
So who invented hardfacing? More importantly, what does any of this have to do with additive manufacturing? Bear with me.
After some Saturday morning Googling, I’ve learned it was the Stoody brothers of Whittier, Calif., who developed the weld overlay process we now call hardfacing. That was in 1921, and the material they developed for their newfangled but-soon-to-be-very-important technology? Stoodite, of course.
Now to the second question. With the possible exception of 3D photosculptures (for which Francois Willeme was granted a patent in 1864), hardfacing was the first instance of AM—although I might be the first person to ever give the Stoody boys, Winston and Shelley, credit for it.
Today, traditional hardfacing is still performed—albeit in a more automated fashion—but it has also morphed into something else entirely. It’s called direct energy deposition (DED), and it might soon be coming to a machine shop near you. Simply put, it works by applying metal powder (or wire feedstock) onto a workpiece while simultaneously hitting it with a laser beam. As beam, powder, and workpiece meet, layer upon layer of material is deposited, allowing the machine operator to repair damaged turbine blades and propellers, for example, or even build up entire workpieces from scratch.
Machine builders Okuma, DMG Mori, Mazak, and others have mounted these DED devices—also known as direct metal deposition or laser metal fusion or sometimes just “cladding heads”—onto their CNC lathes and machining centers. Brilliant!
Imagine the possibilities. Not only can these done-in-one, do-it-all multitasking centers mill, turn, and drill practically anything, but they can now actually add metal to a workpiece. No more complaints about secondary finishing operations or 3D printing’s relatively low accuracy, because parts can be machined to whatever tolerances are needed during the printing process.
If I’d had one of these machines on a big Inconel job back in 1983, my boss wouldn’t have needed to write me up. I could have just fixed those parts on the fly and no one would have been the wiser. As I said, brilliant!
About the Author
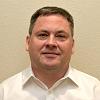
Kip Hanson
About the Publication
- Podcasting
- Podcast:
- The Fabricator Podcast
- Published:
- 04/16/2024
- Running Time:
- 63:29
In this episode of The Fabricator Podcast, Caleb Chamberlain, co-founder and CEO of OSH Cut, discusses his company’s...
- Trending Articles
- Industry Events
16th Annual Safety Conference
- April 30 - May 1, 2024
- Elgin,
Pipe and Tube Conference
- May 21 - 22, 2024
- Omaha, NE
World-Class Roll Forming Workshop
- June 5 - 6, 2024
- Louisville, KY
Advanced Laser Application Workshop
- June 25 - 27, 2024
- Novi, MI