- FMA
- The Fabricator
- FABTECH
- Canadian Metalworking
Our Publications
Categories
- Additive Manufacturing
- Aluminum Welding
- Arc Welding
- Assembly and Joining
- Automation and Robotics
- Bending and Forming
- Consumables
- Cutting and Weld Prep
- Electric Vehicles
- En Español
- Finishing
- Hydroforming
- Laser Cutting
- Laser Welding
- Machining
- Manufacturing Software
- Materials Handling
- Metals/Materials
- Oxyfuel Cutting
- Plasma Cutting
- Power Tools
- Punching and Other Holemaking
- Roll Forming
- Safety
- Sawing
- Shearing
- Shop Management
- Testing and Measuring
- Tube and Pipe Fabrication
- Tube and Pipe Production
- Waterjet Cutting
Industry Directory
Webcasts
Podcasts
FAB 40
Advertise
Subscribe
Account Login
Search
OK, Boomer, time to 3D-scan and -print the future
Additive manufacturing equipment is facilitating the reverse-engineering of parts
- By Kip Hanson
- February 28, 2020
OK, I admit it. I’m a boomer. That means I grew up with a black-and-white TV, no internet, and gas-guzzling cars with V-8 engines and no seat belts.
So it should come as no surprise that, despite my daily scribblings about advanced manufacturing technology, I still have frequent gee-whiz moments when learning about the latest gadget or doohickey (yes, those are boomer terms).
One such moment occurred a couple weeks ago. While writing an article on the growth of reverse-engineering equipment and software, I had a chance to speak with several industry experts, and it struck me during one of these conversations that I wouldn’t be writing about this topic were it not for 3D printing. That’s because, as with so many other developments over the past decade, reverse engineering has been made easier and far more capable thanks to additive manufacturing.
The result? There’s a lot more reverse engineering going on these days.
Consider this: For around $5,000, an entrepreneur can purchase a handheld structured light or laser-line scanner, point it at practically any object, and within minutes have a digital copy of said object suitable for 3D printing. This file then can be sent to any of the hundreds of online service bureaus, and a day or two later, the aspiring (reverse) engineer will have an accurate replica of the desired object in his or her hands. And for another $5,000 or so, he or she could buy a 3D printer and simply print it themselves.
This lowers the bar significantly for anyone wishing to replicate and, hopefully, improve upon anything that fits within a 3D printer. If I were so inclined, I might have my family dress up as Game of Thrones characters, scan them, scale the resulting files to game-piece size, and 3D-print a chess set containing highly detailed copies of Ned Stark, Daenerys Targaryen, Ygritte, and the rest of the cast. (The dragons might be difficult.)
If I then chose to mass-produce my “A Song of Ice and Fire” chess set, I could just as easily create a series of 3D-printed injection molds.
More pragmatic uses include custom prostheses and orthotics, aftermarket auto parts, replacements for damaged machine or aircraft components, jewelry, and other consumer goods. In the past, these objects were re-created via traditional methods such as plaster casting or by taking painstaking measurements on a CMM (coordinate measuring machine). Now, it’s simply point, shoot, print.
All of this was explained to me during my discussions with the people who sell 3D scanning equipment and modeling software, after which I asked the question, “How long until I can 3D-model an object with my smart phone?”
The answer was an uncomfortable pause, followed by “It’s coming, Boomer.”
About the Author
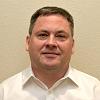
Kip Hanson
About the Publication
- Podcasting
- Podcast:
- The Fabricator Podcast
- Published:
- 04/16/2024
- Running Time:
- 63:29
In this episode of The Fabricator Podcast, Caleb Chamberlain, co-founder and CEO of OSH Cut, discusses his company’s...
- Trending Articles
- Industry Events
16th Annual Safety Conference
- April 30 - May 1, 2024
- Elgin,
Pipe and Tube Conference
- May 21 - 22, 2024
- Omaha, NE
World-Class Roll Forming Workshop
- June 5 - 6, 2024
- Louisville, KY
Advanced Laser Application Workshop
- June 25 - 27, 2024
- Novi, MI