- FMA
- The Fabricator
- FABTECH
- Canadian Metalworking
Our Publications
Categories
- Additive Manufacturing
- Aluminum Welding
- Arc Welding
- Assembly and Joining
- Automation and Robotics
- Bending and Forming
- Consumables
- Cutting and Weld Prep
- Electric Vehicles
- En Español
- Finishing
- Hydroforming
- Laser Cutting
- Laser Welding
- Machining
- Manufacturing Software
- Materials Handling
- Metals/Materials
- Oxyfuel Cutting
- Plasma Cutting
- Power Tools
- Punching and Other Holemaking
- Roll Forming
- Safety
- Sawing
- Shearing
- Shop Management
- Testing and Measuring
- Tube and Pipe Fabrication
- Tube and Pipe Production
- Waterjet Cutting
Industry Directory
Webcasts
Podcasts
FAB 40
Advertise
Subscribe
Account Login
Search
Response to fake news about additive manufacturing, Part 2
Blogger Kip Hanson continues his measured rant about a magazine article that throws shade at 3D printing
- By Kip Hanson
- October 21, 2019
Where was I? Oh, yeah, that article comparing additive to subtractive manufacturing, the one that edged into fake news territory.
The author, “Dave,” continued by saying that some 3D printers, especially those with lasers onboard, are expensive. That’s a big 10-4, but so are multitasking lathes, 5-axis machining centers, punch/laser combo machines—all of which, 3D printers included, bring us one step closer to machine builder Mazak’s “Done in One” manufacturing concept.
Like everything in life, the more you put in the more you get out.
I really take exception to Dave’s contention that mold and die makers are unlikely to see any degree of success with 3D printing. Not true. I’ve spoken with numerous manufacturing companies that use 3D-printed molds or mold inserts to reduce plastic injection cycle times, including a well-known OEM that is currently saving more than $1 million annually on a single part program.
Feel free to Google “conformal cooling channels” if you need additional examples. And when you’re done, Google “Wilson Tool additive” to see what this leader in press brake tooling thinks about 3D printing and its ability to significantly reduce lead times on custom orders.
Dave did raise a valid point about a 3D printer’s need for periodic alignment. I’m not sure about the need to relevel the equipment, but, yes, routine maintenance is definitely a must with any CNC machine tool, especially where high-powered lasers are present.
Dave also took a shot at 3D printing’s Achilles’ heel—support materials—and the fact that overhangs and shallow angles require some sort of scaffolding to keep them from sagging (with polymers) or lifting (in the case of metals). It’s a bummer, to be sure, but at least one 3D printer manufacturer—Velo3D—is now advertising “support-free” metal printing, and where one industry pioneer leads others are sure to follow.
The article’s remaining points are also valid, although none are additive manufacturing deal-breakers. It’s true that managing the software can get “confusing” and users must “educate” themselves about the process and technology, although they apply equally well to other aspects of manufacturing. No one ever said 3D printing would eliminate DFM (design for manufacturing) and other best practices, especially when you consider that manufacturers today enjoy Jackson Pollock-like design freedom rather than the paint-by-numbers restrictions of yesteryear.
And, yes, additive is a time-consuming process and parts can warp or distort after production. Again, certain aspects of 3D printing are a real bummer, especially if it means scrapping a part that you just spent two days and thousands of dollars producing. It happens. The potential for failure, though, doesn’t mean the technology should be avoided but understood and conquered, just as shop people have been doing for centuries.
My advice to Dave is to rejoice in the fact that manufacturers now have a shiny new tool in their toolbox. It isn’t perfect. It’s often quite expensive. It certainly can’t do everything, and it does take some knowledge and skill to use. But try to imagine manufacturing life without it. ’Nuff said.
About the Author
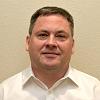
Kip Hanson
About the Publication
- Podcasting
- Podcast:
- The Fabricator Podcast
- Published:
- 04/16/2024
- Running Time:
- 63:29
In this episode of The Fabricator Podcast, Caleb Chamberlain, co-founder and CEO of OSH Cut, discusses his company’s...
- Trending Articles
- Industry Events
16th Annual Safety Conference
- April 30 - May 1, 2024
- Elgin,
Pipe and Tube Conference
- May 21 - 22, 2024
- Omaha, NE
World-Class Roll Forming Workshop
- June 5 - 6, 2024
- Louisville, KY
Advanced Laser Application Workshop
- June 25 - 27, 2024
- Novi, MI