- FMA
- The Fabricator
- FABTECH
- Canadian Metalworking
Our Publications
Categories
- Additive Manufacturing
- Aluminum Welding
- Arc Welding
- Assembly and Joining
- Automation and Robotics
- Bending and Forming
- Consumables
- Cutting and Weld Prep
- Electric Vehicles
- En Español
- Finishing
- Hydroforming
- Laser Cutting
- Laser Welding
- Machining
- Manufacturing Software
- Materials Handling
- Metals/Materials
- Oxyfuel Cutting
- Plasma Cutting
- Power Tools
- Punching and Other Holemaking
- Roll Forming
- Safety
- Sawing
- Shearing
- Shop Management
- Testing and Measuring
- Tube and Pipe Fabrication
- Tube and Pipe Production
- Waterjet Cutting
Industry Directory
Webcasts
Podcasts
FAB 40
Advertise
Subscribe
Account Login
Search
Think about postprocessing when designing 3D-printed parts
- By Kip Hanson
- February 12, 2019
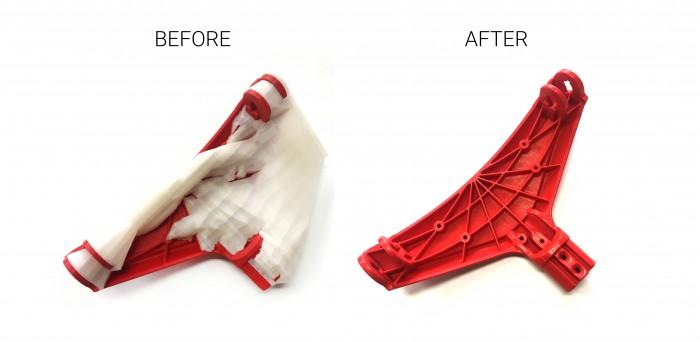
A before-and-after postprocessing view of a typical 3D-printed part, in this case, a vacuum cleaner component.
Few would argue that cost-effective and efficient postprocessing of 3D-printed parts is a necessary aspect of the industry’s continued growth. Yet it’s important to recognize that postprocessing is far more effective if it’s considered early in the design process—not treated as an afterthought.
“Think about a typical 3D-printed metal part,” said Rösler Metal Finishing USA’s Bernie Kerschbaum. “Instead of using several thick, solid posts to support the part during the build, a designer can make life easier for everyone if a series of needle-like supports were used, which are much easier to remove. Similar arguments can be made on the polymer side, where a designer might adjust the support’s material density or structure directly adjacent to the workpiece. Both approaches can significantly reduce the amount of postprocessing.”
The best product designers are the ones who understand the complete manufacturing process and don’t simply focus on form, fit, and function, Kerschbaum noted. For instance, blind holes or holes smaller than the preferred abrasive media do not allow that media to flow through the workpiece, virtually guaranteeing additional finishing steps. How the part is actually built may also affect postprocessing—improper orientation within the build chamber may mean additional supports are needed. It can also increase the amount of stair-stepping that occurs or create irregularly shaped holes that now need machining.
Ironically, a design that optimizes postprocessing—by allowing the part to simply be dumped into a vibratory finishing machine, for example—may also help streamline the build process itself, as it may now be possible to use thicker layers and let an optimized finishing process “clean up the mess,” so to speak.
“Simple changes in part design can make a huge difference,” said Andy Kottage of PostProcess Technologies. “If someone adds a big blob of support material to one section of the part, postprocessing cycle times might go up, while detergent or abrasive life can go down. That’s why additive part manufacturers, in particular, should work closely with their equipment suppliers to balance the postprocessing time with the build time as best they can, and to make sure that the part can be finished effectively. This is especially true on larger part quantities, where hand-finishing becomes impractical.”
About the Author
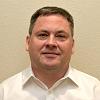
Kip Hanson
About the Publication
- Podcasting
- Podcast:
- The Fabricator Podcast
- Published:
- 04/16/2024
- Running Time:
- 63:29
In this episode of The Fabricator Podcast, Caleb Chamberlain, co-founder and CEO of OSH Cut, discusses his company’s...
- Trending Articles
- Industry Events
16th Annual Safety Conference
- April 30 - May 1, 2024
- Elgin,
Pipe and Tube Conference
- May 21 - 22, 2024
- Omaha, NE
World-Class Roll Forming Workshop
- June 5 - 6, 2024
- Louisville, KY
Advanced Laser Application Workshop
- June 25 - 27, 2024
- Novi, MI