Editor-in-Chief
- FMA
- The Fabricator
- FABTECH
- Canadian Metalworking
Our Publications
Categories
- Additive Manufacturing
- Aluminum Welding
- Arc Welding
- Assembly and Joining
- Automation and Robotics
- Bending and Forming
- Consumables
- Cutting and Weld Prep
- Electric Vehicles
- En Español
- Finishing
- Hydroforming
- Laser Cutting
- Laser Welding
- Machining
- Manufacturing Software
- Materials Handling
- Metals/Materials
- Oxyfuel Cutting
- Plasma Cutting
- Power Tools
- Punching and Other Holemaking
- Roll Forming
- Safety
- Sawing
- Shearing
- Shop Management
- Testing and Measuring
- Tube and Pipe Fabrication
- Tube and Pipe Production
- Waterjet Cutting
Industry Directory
Webcasts
Podcasts
FAB 40
Advertise
Subscribe
Account Login
Search
Waiting for 3D printing’s time to come
After being around 30 years, additive manufacturing accounts for a tiny portion of the global manufacturing economy. What will it take to change that?
- By Don Nelson
- July 24, 2019
My view of 3D printing’s place in manufacturing has changed numerous times since I first witnessed an SLA apparatus in action 30 years ago.
Watching the small, curious machine methodically build a part one shiny resin layer at a time was mesmerizing—and disconcerting. The demonstration convinced me that additive manufacturing (AM) would soon replace milling, turning, and all the other subtractive machining processes I had reported on throughout my career. No machining. No job.
AM’s threat to machining, however, proved nonexistent throughout the 1990s and into the early 2010s. Sure, 3D printers built excellent plastic prototypes—but not much else. I stopped thinking about them.
Then along came MakerBot. The company sold a small 3D printer for the consumer market for less than $1,000. Some 3,500 of the devices were sold between 2009 and 2011. By the time Stratasys acquired the company in 2013 for more than $400 million, MakerBot had sold an estimated 22,00 units.
Other 3D printers for consumers soon flooded the market, as the idea of additively manufacturing household items and virtually “anything you need” captured the public’s imagination.
I thought proliferation of the technology at the grass-roots level would speed its acceptance within manufacturing. Nope. Consumers quickly discovered that 3D printing was slow, limited in terms of usable materials, and couldn’t match the quality of parts produced by conventional methods like machining and molding.
I first viewed AM as a legitimate disruptive technology in 2015, when GE Aviation began 3D-printing fuel nozzle tips for the LEAP engine at its Auburn, Ala., facility. The plant printed its 30,000th nozzle last October.
If GE were willing to install a 3D-printed part in an airplane engine, I reasoned, the technology must have evolved significantly in the past couple years. I also consider GE’s vast commitment of resources—financial, technical, and personnel—as the main reason AM is poised to take a much bigger bite of the $12 trillion global manufacturing economy in the coming years. AM currently accounts for roughly $10 billion.
So how will AM increase its share of the manufacturing economy? The consensus is that suppliers need to build printers that are designed to operate at production volumes, develop a much wider range of cheaper materials, and introduce more AM-specific software.
It’s also necessary to do a better job educating AM users, according to consultant John Barnes. “About 1 percent of manufacturers know what to do with AM,” he said. “The other 99 percent … are still trying to figure out how to integrate it into their operations.”
Another strategy is to foment an AM “revolution.” Brian Neff, founder of 3D metal parts manufacturer Sintavia, said during a speech at the grand opening of the company’s facility in May that a revolution is coming.
Speaking of his competitors in the aerospace and defense industry—metal forging and casting companies—Neff said: “We are going to displace these industries. Not because a government official dictated it. Not because anyone is doing a special favor for us. Not even because we have a mandate from God. … We are going to displace these traditional … manufacturers because of the free market.
“We are less expensive, we are faster, and we are more efficient. And the byproduct of this superiority of process is to consign this dirty type of manufacturing and these polluters to the dustbin of history. The OEM customers want it, the technology supports it, and the competition fears it.
“That is what I call a revolution,” said Neff.
Sometimes it takes a revolution. An industrial revolution.
About the Author
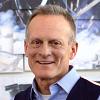
Don Nelson
2135 Point Blvd.
Elgin, IL 60123
(815)-227-8248
About the Publication
- Podcasting
- Podcast:
- The Fabricator Podcast
- Published:
- 04/16/2024
- Running Time:
- 63:29
In this episode of The Fabricator Podcast, Caleb Chamberlain, co-founder and CEO of OSH Cut, discusses his company’s...
- Trending Articles
- Industry Events
16th Annual Safety Conference
- April 30 - May 1, 2024
- Elgin,
Pipe and Tube Conference
- May 21 - 22, 2024
- Omaha, NE
World-Class Roll Forming Workshop
- June 5 - 6, 2024
- Louisville, KY
Advanced Laser Application Workshop
- June 25 - 27, 2024
- Novi, MI