- FMA
- The Fabricator
- FABTECH
- Canadian Metalworking
Our Publications
Categories
- Additive Manufacturing
- Aluminum Welding
- Arc Welding
- Assembly and Joining
- Automation and Robotics
- Bending and Forming
- Consumables
- Cutting and Weld Prep
- Electric Vehicles
- En Español
- Finishing
- Hydroforming
- Laser Cutting
- Laser Welding
- Machining
- Manufacturing Software
- Materials Handling
- Metals/Materials
- Oxyfuel Cutting
- Plasma Cutting
- Power Tools
- Punching and Other Holemaking
- Roll Forming
- Safety
- Sawing
- Shearing
- Shop Management
- Testing and Measuring
- Tube and Pipe Fabrication
- Tube and Pipe Production
- Waterjet Cutting
Industry Directory
Webcasts
Podcasts
FAB 40
Advertise
Subscribe
Account Login
Search
Defense Department awards Desktop Metal $2.45 million to develop AM process for cobalt-free tungsten carbide
- October 23, 2020
- News Release
- Additive Manufacturing
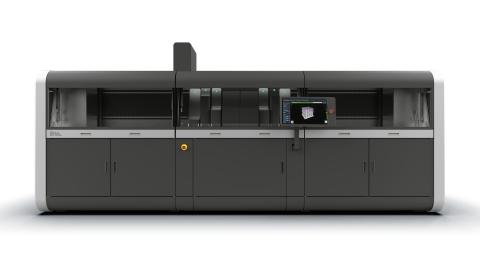
Desktop Metal’s Production System will be used to 3D-print cobalt-free tungsten-carbide parts for the Army project. Desktop Metal
Investigators at the U.S. Army Research Laboratory (ARL) have developed a cobalt-free binder for cemented tungsten carbide. The binder is expected to promote sustainable manufacturing by providing an environmentally friendly method to mass-produce metals, alloys, cermets, and composite parts for both commercial and Department of Defense applications.
The DoD has provided 3D printer manufacturer Desktop Metal $2.45 million in funding to develop a cost-effective, high-volume additive manufacturing process capable of building complex net- or near-net-shape parts from the new hardmetal.
Desktop Metal will use its Production System, featuring the company’s proprietary Single Pass Jetting (SPJ) technology, to mass-manufacture parts.
The goals and requirements of the three-year project include:
• Develop a feedstock and binder system for cobalt-free hardmetals.
• Use the Desktop Metal SPJ process to print at least 200,000 parts in one day with a single machine.
• Deliver a cost analysis for scaling up the SPJ technology to successfully manufacture at least 500,000 prototype pieces.
“We believe combining this novel material with Desktop Metal’s Single Pass Jetting technology will have major applications not only in the defense sector but also in the commercial sector,” said ARL Materials Engineer Dr. Nicholas Ku. “Further, we believe this combined method will dramatically improve sustainability, reduce the use of a conflict mineral, and provide an environmentally friendly process to mass-produce parts with superior properties.”
The project was awarded to Desktop Metal by the U.S. Army Contracting Command on behalf of the National Center for Manufacturing Sciences Advanced Manufacturing, Materials & Processes Consortium.
- Podcasting
- Podcast:
- The Fabricator Podcast
- Published:
- 04/16/2024
- Running Time:
- 63:29
In this episode of The Fabricator Podcast, Caleb Chamberlain, co-founder and CEO of OSH Cut, discusses his company’s...
- Trending Articles
- Industry Events
16th Annual Safety Conference
- April 30 - May 1, 2024
- Elgin,
Pipe and Tube Conference
- May 21 - 22, 2024
- Omaha, NE
World-Class Roll Forming Workshop
- June 5 - 6, 2024
- Louisville, KY
Advanced Laser Application Workshop
- June 25 - 27, 2024
- Novi, MI