- FMA
- The Fabricator
- FABTECH
- Canadian Metalworking
Our Publications
Categories
- Additive Manufacturing
- Aluminum Welding
- Arc Welding
- Assembly and Joining
- Automation and Robotics
- Bending and Forming
- Consumables
- Cutting and Weld Prep
- Electric Vehicles
- En Español
- Finishing
- Hydroforming
- Laser Cutting
- Laser Welding
- Machining
- Manufacturing Software
- Materials Handling
- Metals/Materials
- Oxyfuel Cutting
- Plasma Cutting
- Power Tools
- Punching and Other Holemaking
- Roll Forming
- Safety
- Sawing
- Shearing
- Shop Management
- Testing and Measuring
- Tube and Pipe Fabrication
- Tube and Pipe Production
- Waterjet Cutting
Industry Directory
Webcasts
Podcasts
FAB 40
Advertise
Subscribe
Account Login
Search
Engine-maker changes from casting to additively manufacturing turbine parts
- May 13, 2021
- News Release
- Additive Manufacturing
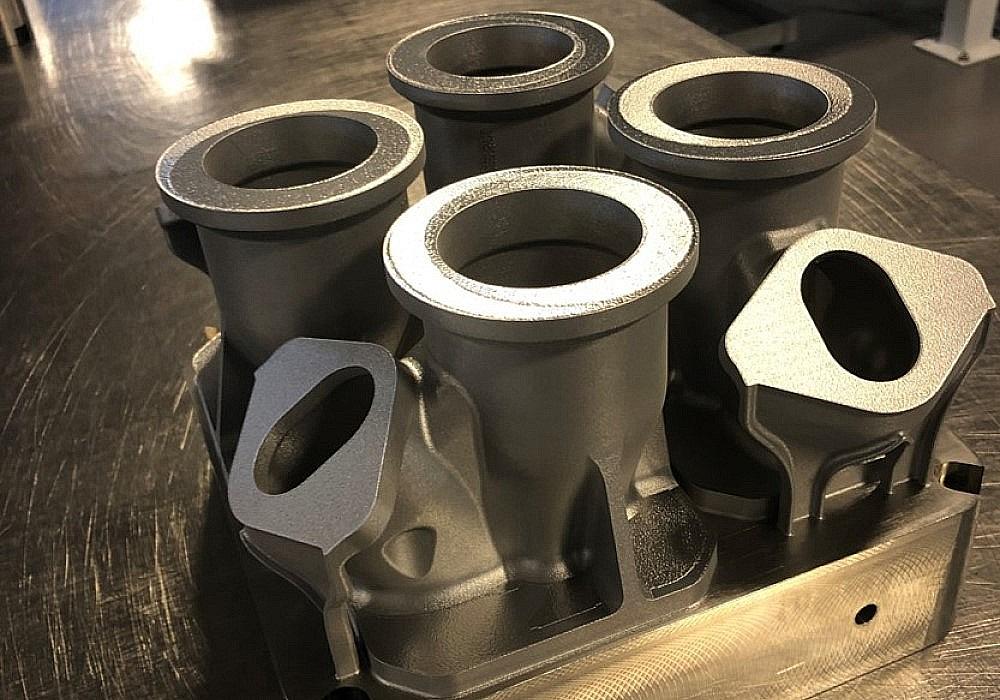
GE Aviation found it cost less to 3D-print four bleed-air turbine parts than cast them. Images: GE Aviation
GE Aviation has switched from investment casting four parts for land/marine turbines to 3D-printing them. The company based its decision on the lower costs additive manufacturing provides and that AM shortens time to market.
GE Aviation collaborated with fellow division and metal 3D printer builder GE Additive to study the feasibility of switching to AM. The aerospace engineering team expects the four 3D-printed parts to cost up to 35% less than cast versions.
Equally important, says the company, is it took only 10 months from identifying target parts to 3D-printing final prototypes. Ordinarily, developing and casting an aerospace or land/marine turbine part takes 12 to 18 months or longer.
GE Aviation’s AM leader, Eric Gatlin, said, “This is the first time we’ve done a part-for-part replacement, and it was cheaper doing it with additive than casting.” To ensure the cost-competitiveness of 3D printing, GE had four outside vendors quote on casting the parts. “We still came in lower with additive manufacturing,” he said.
GE Aviation was an early adopter of additively manufacturing parts for engines. Its 3D-printed fuel nozzle tip for the LEAP engine, for example, consolidated 20 different parts—and the steps needed to machine and assemble them—into a single structure. And for the company’s new turboprop engine, 855 parts were combined into just 10 3D-printed components. In both cases, the manufacturer realized significant assembly-cost savings.
The Chosen Four
The process of selecting the four cast parts to 3D-print began in early 2020 with GE Aviation’s annual audit of castings.
“We are always looking to pull costs out of existing products,” Gatlin said, “so we cast a wide net that included hundreds of castings we buy. Then we ask, ‘Are we getting more competitive?’ ‘Are there things we couldn’t do a year ago that are now technically feasible?’”
The vetting process considered both new and old products and a variety of factors, such as the capabilities of GE Aviation’s 3D printers, part size, shape, and part features. The engineers asked whether the parts used well-characterized materials they had worked with on those machines before. They also took into account the ease of postprocessing steps like machining, used to eliminate surface imperfections, and brazing to add fittings to a part.
By February 2020,the GE Aviation team had identified 180 cast parts for which they thought 3D printing could potentially save money. To make sure, a team of GE Aviation and GE Additive engineers, each using their own organizational production and financial models, split into small groups to calculate the ROI on printing each part.
The audit looked at both low-volume replacement parts and production-volume parts for new programs, like the LM9000 engine.
Then COVID-19 swept the globe.
Production During the Pandemic
At GE Aviation’s additive production facility in Auburn, Ala., where parts for engines are made, the pandemic presented an opportunity for the team to focus on projects like the casting-to-printing one. Unexpectedly, team members had machine and postprocessing time available to start making parts.
“We’re a production shop and would not see a project like this until after GE Aviation’s Additive Technology Center had developed the process for low-rate production,” said Jeff Eschenbach, a senior project manager and project lead at the Auburn facility. “What was different about this project is that we took this on from the very beginning. It created an opportunity for the engineers on-site to get involved.”
The formation of the team kicked everything into high gear. Dozens of parts had passed the initial screening. Additional analysis whittled down the number to nine. They included parts on other marine-industrial gas turbine engines, regional jet turbofans, and some military programs.
The parts were all made of either CoCr, an alloy of cobalt and chrome widely used for hot-turbine parts, or Ti-64, a stiff, lightweight titanium-aluminum-vanadium alloy used for structural parts. The engineers only looked at parts that could fit inside GE Additive’s DMLM (direct metal laser melting) Concept Laser M2 machine.
The team further reduced the number of parts by prioritizing them based on engineering resources and the importance of cost savings to the engine program. The team settled on four parts—adapter caps for the LM9000’s bleed-air system—which became the focus of the program at Auburn.
All four parts are about 3.5 in. dia. by about 6 in. tall and made of CoCr.
From a manufacturing standpoint, the parts share a base geometry and have similar features. Team members assumed the M2 could print three parts; they redesigned the build plate layout to accommodate four. This immediately boosted productivity, because it takes about the same amount of time to print four parts as it does three.
Driving Down Costs
The project was a success, the company reports. It marked the first time GE Aviation had shifted production from investment casting to AM based strictly on cost. “The parts were one-to-one replacements, without any redesign or parts consolidation to improve their economics,” Gatlin said.
“The thing that stuck out to me,” Eschenbach said, “was that we could take an existing casting design, replicate it quickly on our printers, and within weeks of starting on the project [have] final parts that were the same quality as their cast counterparts. This project serves as a template for future work.”
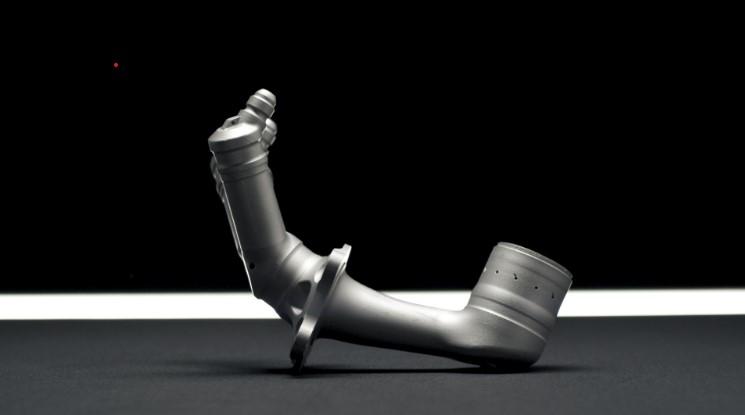
GE Aviation was an early adopter of 3D-printed engine components. Shown is a fuel nozzle tip for its LEAP engine.
GE estimates that dozens, and eventually hundreds and thousands, of parts throughout all its product lines could be 3D-printed.
This report was excerpted from a paper GE published. Click here to read the entire paper.
- Podcasting
- Podcast:
- The Fabricator Podcast
- Published:
- 04/16/2024
- Running Time:
- 63:29
In this episode of The Fabricator Podcast, Caleb Chamberlain, co-founder and CEO of OSH Cut, discusses his company’s...
- Trending Articles
- Industry Events
16th Annual Safety Conference
- April 30 - May 1, 2024
- Elgin,
Pipe and Tube Conference
- May 21 - 22, 2024
- Omaha, NE
World-Class Roll Forming Workshop
- June 5 - 6, 2024
- Louisville, KY
Advanced Laser Application Workshop
- June 25 - 27, 2024
- Novi, MI