- FMA
- The Fabricator
- FABTECH
- Canadian Metalworking
Our Publications
Categories
- Additive Manufacturing
- Aluminum Welding
- Arc Welding
- Assembly and Joining
- Automation and Robotics
- Bending and Forming
- Consumables
- Cutting and Weld Prep
- Electric Vehicles
- En Español
- Finishing
- Hydroforming
- Laser Cutting
- Laser Welding
- Machining
- Manufacturing Software
- Materials Handling
- Metals/Materials
- Oxyfuel Cutting
- Plasma Cutting
- Power Tools
- Punching and Other Holemaking
- Roll Forming
- Safety
- Sawing
- Shearing
- Shop Management
- Testing and Measuring
- Tube and Pipe Fabrication
- Tube and Pipe Production
- Waterjet Cutting
Industry Directory
Webcasts
Podcasts
FAB 40
Advertise
Subscribe
Account Login
Search
Fabrication, additive manufacturing companies produce part for 787 airliner
- December 26, 2018
- News Release
- Additive Manufacturing
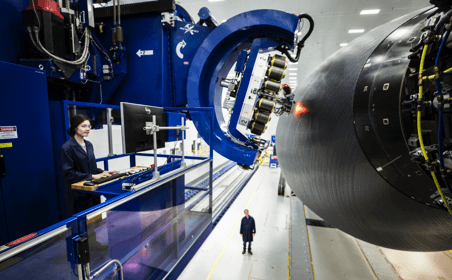
Spirit AeroSystems and Norsk Titanium collaborated on a 3D-printed, titanium structural component for the fuselage of a Boeing 787 Dreamliner.
Spirit AeroSystems, which produces Boeing 787 fuselages and other structures, received its first additively manufactured, titanium structural component from Norsk Titanium U.S. Inc. (NTi).
The part, a back-up fitting for an access door latch in the forward fuselage of the 787 Dreamliner, has been machined and finished at Spirit's Wichita, Kan., facility.
NTi, headquartered in Norway with a Plattsburgh, N.Y., office, is an FAA-approved, OEM-qualified supplier of additive-manufactured, structural titanium components. NTi’s proprietary Rapid Plasma Deposition™ (RPD) process has been in serial production of Boeing 787 titanium components since April, 2017.
"Integrating additive manufacturing capability into our production system to build end-use titanium parts expands Spirit's fabrication capabilities and puts us at the forefront of advanced manufacturing," said Kevin Matthies, Spirit AeroSystems senior vice president of Global Fabrication. "With our Norsk collaboration, Spirit is bringing the power and benefits of additive manufacturing in support of our customers."
With RPD, titanium wire is melted in an inert, argon-gas environment and precisely, rapidly built up in layers to a near-net-shape part. The result is significantly less machining compared to conventional manufacturing methods, said NTi. Reduced machining lessens tooling and energy usage, which are significant cost drivers for titanium parts.
Once the AM phase of production is completed, Spirit final-machines and -finishes, inspects, and installs the part.
- Podcasting
- Podcast:
- The Fabricator Podcast
- Published:
- 04/16/2024
- Running Time:
- 63:29
In this episode of The Fabricator Podcast, Caleb Chamberlain, co-founder and CEO of OSH Cut, discusses his company’s...
- Trending Articles
- Industry Events
16th Annual Safety Conference
- April 30 - May 1, 2024
- Elgin,
Pipe and Tube Conference
- May 21 - 22, 2024
- Omaha, NE
World-Class Roll Forming Workshop
- June 5 - 6, 2024
- Louisville, KY
Advanced Laser Application Workshop
- June 25 - 27, 2024
- Novi, MI