- FMA
- The Fabricator
- FABTECH
- Canadian Metalworking
Our Publications
Categories
- Additive Manufacturing
- Aluminum Welding
- Arc Welding
- Assembly and Joining
- Automation and Robotics
- Bending and Forming
- Consumables
- Cutting and Weld Prep
- Electric Vehicles
- En Español
- Finishing
- Hydroforming
- Laser Cutting
- Laser Welding
- Machining
- Manufacturing Software
- Materials Handling
- Metals/Materials
- Oxyfuel Cutting
- Plasma Cutting
- Power Tools
- Punching and Other Holemaking
- Roll Forming
- Safety
- Sawing
- Shearing
- Shop Management
- Testing and Measuring
- Tube and Pipe Fabrication
- Tube and Pipe Production
- Waterjet Cutting
Industry Directory
Webcasts
Podcasts
FAB 40
Advertise
Subscribe
Account Login
Search
NIST researcher wins ‘Oscar’ for developing process that halts microcracking of 3D-printed parts
- November 24, 2021
- News Release
- Additive Manufacturing
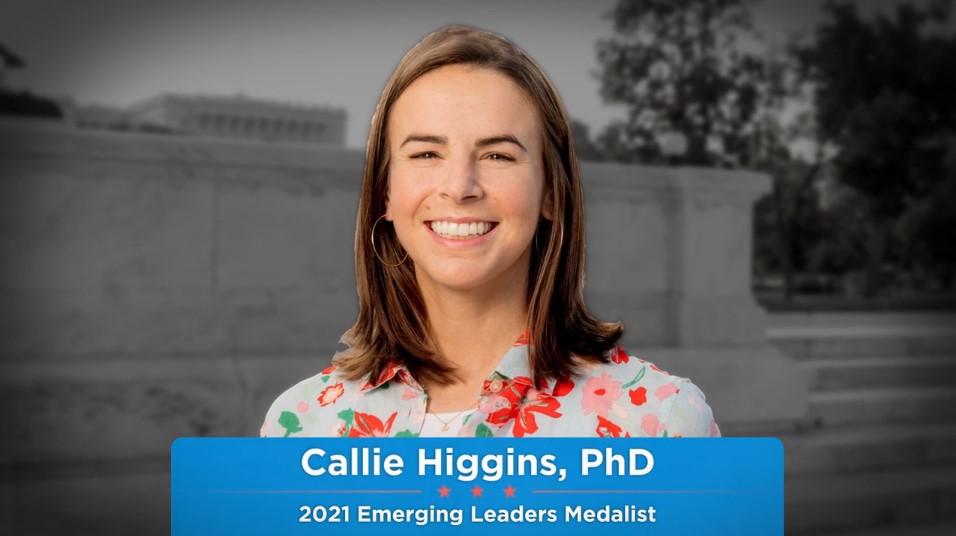
NIST materials research engineer Callie Higgins won a Samuel J. Heyman Service to America Medal for devising a system that improves how light turns liquid plastics into solid materials. The award was presented in October at the John F. Kennedy Center for the Performing Arts. Partnership for Public Service
A materials research engineer at the National Institute of Standards and Technology, Callie I. Higgins, has won the Samuel J. Heyman Service to America Medal in the Emerging Leaders category.
Higgins was one of seven medal winners chosen to receive an award from among 29 finalists. The awards—often called the “Oscars of public service”—are given by the Partnership for Public Service, whose founding chairman was Samuel J. Heyman. Medalists are chosen based on their leadership and innovation, as well as the impact of their work on the health, safety, and prosperity of the country.
“At 31, Higgins and her colleagues invented a groundbreaking technology to detect and remedy microscopic flaws that threaten the safety and reliability of 3D-printed products, potentially revolutionizing the medical, plastics, coatings, optics, and additive manufacturing fields,” the award citation reads.
The in-person awards ceremony was held Oct. 28 at the John F. Kennedy Center for the Performing Arts in Washington, D.C. In a video, actor Rose Byrne shared details about Higgins’ accomplishment.
Curing Liquids
Higgins conducts research to improve a 3D printing technique that uses light to cure liquid plastics, transforming them into solid materials. She is particularly interested in its potential use in regenerative medicine and the on-demand, custom, large-scale manufacturing of plastics, coatings, and optical components.
“The technology has the potential to enable the production of patient-specific artificial organs,” Higgins said. “I want to do everything I can to ensure this becomes a reality.”
Higgins and her colleagues developed a technique that enables scientists and engineers to detect, remedy, and even reverse-engineer microscopic manufacturing flaws that develop during the 3D printing process. The team’s novel microscopy method measures, at the submicron scale, how and where a material’s properties change in real time as curing progresses.
The discovery by Higgins and her colleagues centered on a sophisticated modification of an atomic force microscope. The modification helped revolutionize the way parts made of polymer materials, such as plastics, could be understood and characterized.
Before Higgins’ work, product evaluation was limited to the millimeter scale. Her technique enables products to be evaluated at the submicron scale, allowing microscopic flaws to be seen at all relevant stages of the manufacturing process.
“This science will revolutionize regenerative medicine,” said Scott Turner, the director of advanced research and development at 3D Systems. His company, he said, is planning to use the technology to create 3D-printed lungs, one of the hardest organs to produce.
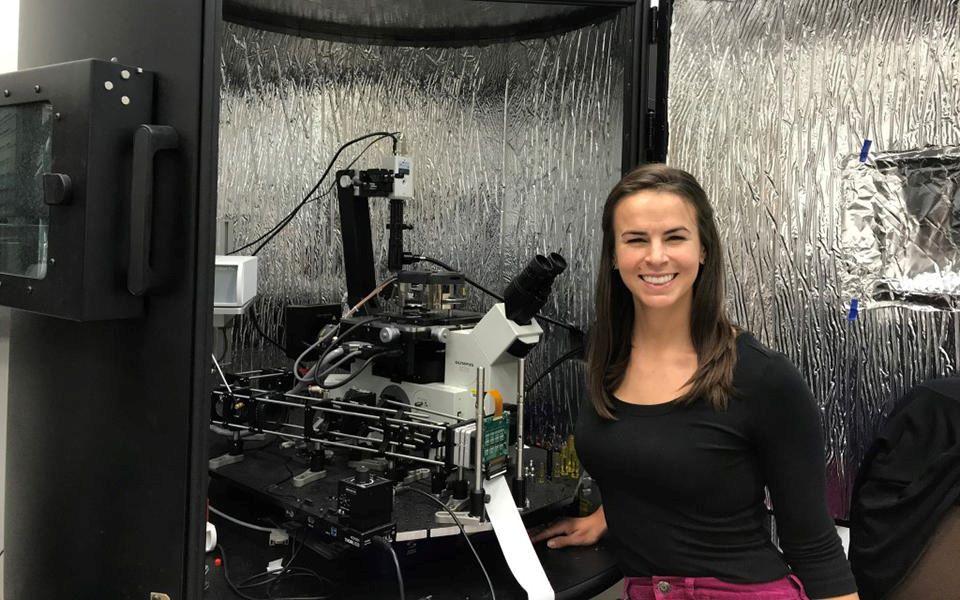
The instrument Callie Higgins and her colleagues developed combines an atomic force microscope (top) with a digital light processing 3D printer (bottom and left). NIST
“Callie’s work is the kind of underlying science that will guide us through the future of tissue engineering with photopolymers,” Turner said.
Other Applications
Higgins’ work could have an impact on fields beyond health care, including plastics, coatings, optics, and other areas of additive manufacturing.
“Ford Motor Co. has been very assertive in talking with Callie about pursuing the technology because they want to create engine components that will perform the way they need them to but at a much lighter weight,” said Robert Keller, a NIST supervisory materials research engineer.
Higgins said she is excited about the ripple effect of her scientific work.
“Through NIST, I get the opportunity to impact an entire industry, not just one company,” she said. “We are here to drive innovation throughout in the United States, and if we are not serving the people, we aren’t serving our mission.”
Jason Killgore, a project leader in NIST’s Applied Chemicals and Materials Division, noted that Higgins “has been able to connect with industry stakeholders in a way that’s never been seen before.”
“Instead of conducting science in a vacuum and hoping that the industry appreciates what we do down the road, she is actively making sure that we’re doing the right science on a day-to-day basis,” Killgore said.
“This field has the potential to impact so much of our daily lives, if we can bring the right minds together to solve these pressing challenges in the printing process,” Higgins said. “Through the additive manufacturing network of stakeholders I have developed, I am finally in a position where I can effect change.”
The information in this report comes from news items published by NIST and the Partnership for Public Service.
- Podcasting
- Podcast:
- The Fabricator Podcast
- Published:
- 04/16/2024
- Running Time:
- 63:29
In this episode of The Fabricator Podcast, Caleb Chamberlain, co-founder and CEO of OSH Cut, discusses his company’s...
- Trending Articles
- Industry Events
16th Annual Safety Conference
- April 30 - May 1, 2024
- Elgin,
Pipe and Tube Conference
- May 21 - 22, 2024
- Omaha, NE
World-Class Roll Forming Workshop
- June 5 - 6, 2024
- Louisville, KY
Advanced Laser Application Workshop
- June 25 - 27, 2024
- Novi, MI