- FMA
- The Fabricator
- FABTECH
- Canadian Metalworking
Our Publications
Categories
- Additive Manufacturing
- Aluminum Welding
- Arc Welding
- Assembly and Joining
- Automation and Robotics
- Bending and Forming
- Consumables
- Cutting and Weld Prep
- Electric Vehicles
- En Español
- Finishing
- Hydroforming
- Laser Cutting
- Laser Welding
- Machining
- Manufacturing Software
- Materials Handling
- Metals/Materials
- Oxyfuel Cutting
- Plasma Cutting
- Power Tools
- Punching and Other Holemaking
- Roll Forming
- Safety
- Sawing
- Shearing
- Shop Management
- Testing and Measuring
- Tube and Pipe Fabrication
- Tube and Pipe Production
- Waterjet Cutting
Industry Directory
Webcasts
Podcasts
FAB 40
Advertise
Subscribe
Account Login
Search
Swedish researchers and materials manufacturer demonstrate advancement in 3D-printed copper parts
- March 18, 2021
- News Release
- Additive Manufacturing
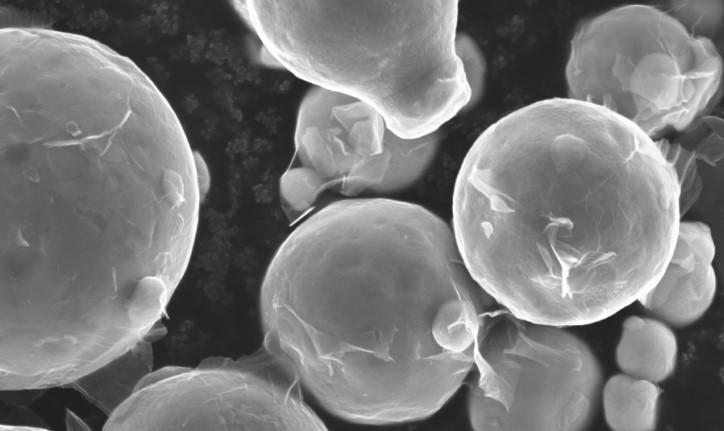
Uppsala University used a patented Graphmatech technology to enhance copper used to 3D-print parts. Images: Simon Tidén, Uppsala University
Metal additive manufacturing has grown significantly the past few years because of the technology’s ability to produce customized and complex designs on demand, as well as offering more-sustainable manufacturing with reduced waste and lower material requirements.
Pure copper and some other metals, however, have proven challenging to print because of their high reflectivity. At the wavelengths commonly used in laser powder bed fusion—the dominant technology in metal AM—only a small part of the energy is absorbed by the material, resulting in low-density parts.
Researchers at Sweden’s Uppsala University have collaborated with graphene materials company Graphmatech AB to demonstrate a way to significantly lower the reflectivity of copper powder, which would allow the printing of denser parts.
“By modifying the surface of the copper powder using Graphmatech’s patented graphene technology, we successfully reduced the reflectance by up to 67%,” said the Swedish company’s CEO, Dr. Mamoun Taher. The graphene survived the printing process to positively impact the density of the printed copper-graphene parts, significantly reducing their porosity.
“This 3D-printable hybrid material has the potential to add value in a range of sectors, such as e-mobility, electronics, and defense,” added Taher.The research is being undertaken by Prof. Ulf Jansson’s research group at the Uppsala University Ångström Laboratory with PhD candidate Simon Tidén.
- Podcasting
- Podcast:
- The Fabricator Podcast
- Published:
- 04/16/2024
- Running Time:
- 63:29
In this episode of The Fabricator Podcast, Caleb Chamberlain, co-founder and CEO of OSH Cut, discusses his company’s...
- Trending Articles
- Industry Events
16th Annual Safety Conference
- April 30 - May 1, 2024
- Elgin,
Pipe and Tube Conference
- May 21 - 22, 2024
- Omaha, NE
World-Class Roll Forming Workshop
- June 5 - 6, 2024
- Louisville, KY
Advanced Laser Application Workshop
- June 25 - 27, 2024
- Novi, MI